Tungsten Powder
Table of Contents
Imagine a material so dense it could rival a black hole’s core in a thimble. That’s the incredible world of tungsten powder, a fine-grained marvel with properties that push the boundaries of engineering. But beyond its impressive density, tungsten powder boasts a unique blend of characteristics that make it a game-changer in countless industries. Buckle up, because we’re about to delve into the fascinating world of this microscopic metal powerhouse.
An Overview of Tungsten Powder
Tungsten powder, also known as tungsten metal powder, is a finely divided form of the element tungsten (W). It’s manufactured by crushing larger tungsten pieces or using specialized techniques like chemical vapor deposition. The resulting powder consists of microscopic particles with exceptional properties, including:
- High Density: Tungsten is naturally the densest metal on Earth, and its powdered form retains this impressive characteristic. This makes it ideal for applications where weight needs to be minimized while maintaining strength.
- High Melting Point: Tungsten boasts the highest melting point of any metal, exceeding a staggering 3422°C (6192°F). This property makes it perfect for high-temperature environments like rocket engines and furnace linings.
- Excellent Hardness: Tungsten powder particles are incredibly hard, making them ideal for applications requiring abrasion resistance, such as drill bits and cutting tools.
- Good Electrical Conductivity: While not the most conductive metal, tungsten powder offers sufficient conductivity for applications like electrical contacts and electrodes.
These remarkable properties make tungsten powder a highly sought-after material across various industries.
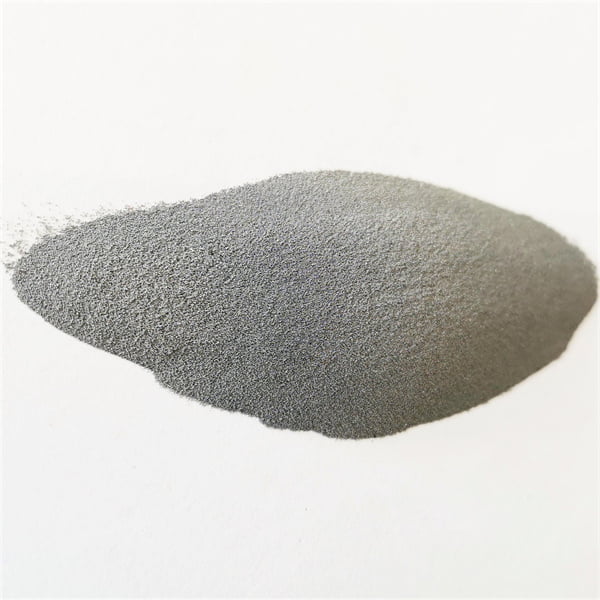
the Diverse Landscape of Tungsten Powders
The world of tungsten powder isn’t a one-size-fits-all affair. Manufacturers offer a variety of models with distinct characteristics to cater to specific needs. Let’s explore some popular options:
1. Spherical Tungsten Powder: As the name suggests, these particles are perfectly round, resembling tiny metal balls. This shape offers several advantages, including:
- Improved Flowability: Spherical particles flow freely, making them ideal for powder metallurgy applications where uniform distribution is crucial.
- High Packing Density: The spherical shape allows for tighter packing, maximizing the amount of tungsten powder in a given space.
- Reduced Wear: The smooth surface minimizes friction during processing, leading to less wear on equipment.
2. Flake Tungsten Powder: Unlike their spherical counterparts, these particles have a plate-like shape. This unique morphology offers benefits like:
- Enhanced Electrical Conductivity: The increased surface area of flake particles improves electrical conductivity, making them suitable for electrical components.
- Superior Lubrication: The plate-like structure allows for better lubrication properties, beneficial for applications like self-lubricating bearings.
3. Angular Tungsten Powder: These irregular-shaped particles possess sharp edges and corners. This characteristic translates to advantages such as:
- Increased Strength: The angular shape creates a stronger inter-particle bond, leading to a more robust material.
- Improved Hardness: The sharp edges enhance the material’s cutting and wear resistance.
4. Carbon-Doped Tungsten Powder: This model incorporates a small amount of carbon into the tungsten powder matrix. The addition of carbon brings several benefits:
- Enhanced Strength: Carbon doping improves the overall strength of the material.
- Increased Creep Resistance: This type of tungsten powder exhibits superior resistance to deformation under high temperature and stress.
5. Nickel-Tungsten (Ni-W) Composite Powder: This model blends tungsten powder with nickel particles. The combination offers advantages like:
- Improved Ductility: The presence of nickel enhances the ductility of the material, making it more formable.
- Tailored Electrical Properties: The ratio of tungsten to nickel can be adjusted to achieve specific electrical properties.
6. Copper-Tungsten (Cu-W) Composite Powder: Similar to Ni-W, this type combines tungsten powder with copper particles. This blend provides benefits such as:
- Enhanced Thermal Conductivity: Copper’s excellent thermal conductivity improves the heat dissipation capabilities of the material.
- Increased Machinability: The presence of copper makes the composite powder easier to machine and shape.
7. Reduced Tungsten Oxide (RTO) Powder: This model undergoes a unique treatment process to minimize the presence of tungsten oxide on the particle surface. The reduction in oxide content offers advantages like:
- Improved Sinterability: Reduced oxide content promotes better bonding between particles during sintering, leading to a stronger final product.
- Enhanced Electrical Conductivity: The reduced oxide layer minimizes electrical resistance.
8. Activated Tungsten Powder: This type of powder undergoes a special activation process to increase its surface area. The increased surface area offers benefits such:
- Enhanced Catalytic Properties: Activated tungsten powder exhibits improved catalytic activity, making it valuable in chemical reactions.
9. Micronized Tungsten Powder: This model refers to tungsten powder with particles finely ground to micron-sized dimensions (one micron is one-millionth of a meter). The microscopic size offers advantages such:
- Improved Sinterability: Micron-sized particles create a larger surface area for bonding, leading to faster and more efficient sintering.
- Enhanced Densification: The small particle size allows for tighter packing, resulting in a denser final product.
10. Atomized Tungsten Powder: This model utilizes a high-temperature, high-pressure gas atomization process to create spherical tungsten powder. Compared to traditionally crushed tungsten powder, atomized variants offer:
- Improved Purity: The gas atomization process minimizes contamination, resulting in a purer tungsten powder.
- Narrower Particle Size Distribution: Atomization produces tungsten powder with a more consistent particle size, leading to more predictable material properties.
Choosing the Right Tungsten Powder: A Matchmaker’s Guide
With such a diverse range of tungsten powder models available, selecting the right one for your specific application is crucial. Consider these factors when making your choice:
- Desired Properties: Identify the key properties you need in the final product, such as high density, superior hardness, or enhanced conductivity.
- Application Requirements: Tailor your choice to the specific application. For instance, spherical tungsten powder might be ideal for powder metallurgy processes requiring good flowability, while angular tungsten powder could be better suited for cutting tools due to its increased strength.
- Processing Methods: Consider the processing methods you’ll be using. For example, micronized tungsten powder might be better suited for processes like sintering, while atomized tungsten powder could offer advantages in applications like thermal spraying.
- Cost Considerations: Different tungsten powder models vary in price. Evaluate your budget and choose the option that offers the best value for your needs.
By understanding the unique properties and applications of various tungsten powder models, you can make an informed decision that optimizes the performance of your final product.
the Applications of Tungsten Powder
The remarkable properties of tungsten powder have translated into a vast array of applications across various industries. Here’s a glimpse into this diverse realm:
Application | Description | Benefits of Using Tungsten Powder |
---|---|---|
Cutting Tools | Drill bits, milling cutters, and other metalworking tools | High hardness and wear resistance for efficient and long-lasting cutting performance. |
Armor-Piercing Projectiles | Bullets and shells designed to penetrate armor | High density for superior penetration power. |
Counterweights | Used for balancing applications in machinery and aerospace | High density allows for a compact counterweight design. |
Electrodes | Used in welding, electric arc furnaces, and other electrical applications | High melting point and good electrical conductivity for reliable performance. |
Electrical Contacts | Used in switches, relays, and other electrical components | High hardness and good electrical conductivity for durable and reliable contacts. |
Heat Sinks | Used in electronics to dissipate heat | High thermal conductivity efficiently draws heat away from sensitive components. |
Nuclear Applications | Used in reactor components and shielding materials | High melting point and density offer excellent resistance to radiation. |
X-ray Imaging | Used as a target material in X-ray tubes | High atomic number effectively converts electron energy into X-rays. |
Catalytic Applications | Used as a catalyst in chemical reactions | Certain tungsten powder models offer enhanced catalytic properties for efficient reactions. |
Composite Materials | Combined with other materials to create composites with unique properties | Tungsten powder can improve the strength, hardness, and density of composite materials. |
This table provides a snapshot of the extensive applications of tungsten powder. From the heavy-duty world of armor-piercing projectiles to the delicate world of X-ray imaging, tungsten powder plays a vital role in countless industries.
the Specifications, Sizes, Grades, and Standards of Tungsten Powder
When selecting tungsten powder, understanding its technical specifications is crucial. Here’s a breakdown of key factors to consider:
Property | Description |
---|---|
Particle Size: Measured in microns (µm) or mesh size (number of openings per linear inch in a sieve). | Affects flowability, packing density, and final product properties. |
Purity: Percentage of tungsten by weight. | Higher purity offers better performance and consistency. |
Apparent Density: The bulk density of the powder. | Affects how much powder can be |
Flowability: How easily the powder flows. | Important for efficient processing in applications like powder metallurgy. |
Chemical Composition: Presence of any impurities or alloying elements. | Can impact the final product’s properties. |
Surface Area: Measured in square meters per gram (m²/g). | Affects properties like reactivity and sintering behavior. |
Particle Size Distribution: This refers to the variation in particle sizes within a tungsten powder sample. It’s typically represented by a graph or chart and is crucial for achieving consistent material properties in the final product.
Grades and Standards: Tungsten powder is available in various grades defined by industry standards like ASTM International (ASTM) or Military (MIL) specifications. These standards outline requirements for properties like chemical composition, particle size distribution, and apparent density. Choosing the appropriate grade ensures the tungsten powder meets the specific needs of your application.
Common Tungsten Powder Sizes
Tungsten powder comes in a wide range of particle sizes, typically ranging from coarse powders with particles exceeding 100 microns to ultra-fine powders with particles less than 1 micron. The choice of size depends on the desired properties and application:
- Coarser powders (100+ microns): Often used in applications like shot blasting and thermal spraying due to their good flowability and splat characteristics.
- Medium-sized powders (10-100 microns): Commonly used in applications like electrical contacts and electrodes due to their balance of flowability and packing density.
- Fine powders (1-10 microns): Often used in powder metallurgy applications due to their high surface area and ability to achieve near-net-shape parts.
- Ultra-fine powders (less than 1 micron): Used in specialized applications like catalysts and X-ray targets due to their extremely high surface area and unique properties.
Advantages and Limitations of Tungsten Powder
Tungsten powder boasts a remarkable range of advantages, making it a highly sought-after material. However, it’s essential to consider its limitations to ensure it’s the right choice for your application.
Advantages of Tungsten Powder:
- Exceptional Density: The highest density of any metal, offering advantages in applications requiring weight minimization and space constraints.
- Superior Melting Point: The highest melting point of any metal, making it ideal for high-temperature environments.
- Excellent Hardness: Highly wear-resistant, perfect for cutting tools and components requiring abrasion resistance.
- Good Electrical Conductivity: While not the most conductive, it offers sufficient conductivity for various electrical applications.
- Versatility: Available in various forms and sizes to cater to diverse applications.
Limitations of Tungsten Powder:
- Brittleness: Tungsten powder can be brittle, especially in its pure form. Alloying with other elements or using specific processing techniques can mitigate this limitation.
- High Cost: Tungsten is a relatively rare metal, and the production process can be energy-intensive, leading to a higher cost compared to some other metal powders.
- Oxidation Sensitivity: Tungsten powder can readily oxidize, especially at high temperatures. Proper storage and handling are crucial to prevent this.
By carefully considering the advantages and limitations of tungsten powder, you can make an informed decision about its suitability for your specific needs.
FAQ
Q: What are some safety precautions to take when handling tungsten powder?
A: Tungsten powder can be slightly irritating to the skin and respiratory system. It’s advisable to wear gloves, safety glasses, and a dust mask when handling tungsten powder.
Q: How is tungsten powder stored?
A: Tungsten powder should be stored in a cool, dry place in sealed containers to prevent moisture absorption and oxidation.
Q: Can tungsten powder be recycled?
A: Yes, tungsten powder can be recycled through various techniques. This makes it a more sustainable material choice in some applications.
Q: What are some alternatives to tungsten powder?
A: Depending on the specific application, alternatives to tungsten powder might include molybdenum powder, tantalum powder, or even certain types of ceramic powders. Each alternative material offers its own unique set of properties and limitations.
Share On
MET3DP Technology Co., LTD is a leading provider of additive manufacturing solutions headquartered in Qingdao, China. Our company specializes in 3D printing equipment and high-performance metal powders for industrial applications.
Inquiry to get best price and customized Solution for your business!
Related Articles
About Met3DP
Recent Update
Our Product
CONTACT US
Any questions? Send us message now! We’ll serve your request with a whole team after receiving your message.
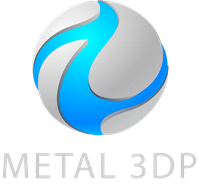
Metal Powders for 3D Printing and Additive Manufacturing