Understanding Electron Beam Selective Melting Equipment
Table of Contents
electron beam selective melting equipment is a cutting-edge technology revolutionizing the manufacturing industry. In this article, we’ll dive deep into the world of EBSM, discussing everything from its basics to the nitty-gritty details of metal powders used, their compositions, characteristics, and applications. Whether you’re a seasoned engineer or a curious enthusiast, this guide is designed to provide comprehensive knowledge while keeping you engaged. So, buckle up and let’s explore the fascinating realm of EBSM!
Overview of Electron Beam Selective Melting (EBSM)
Electron Beam Selective Melting, often referred to as EBSM, is an additive manufacturing technique that uses an electron beam to fuse metal powder layer by layer, creating intricate and high-precision components. Unlike traditional manufacturing methods, EBSM offers unparalleled design flexibility and material efficiency, making it a game-changer in industries such as aerospace, automotive, and medical devices.
What Makes EBSM Unique?
EBSM stands out due to its use of an electron beam instead of a laser, which provides several advantages:
- Higher Energy Efficiency: The electron beam is more energy-efficient compared to lasers.
- Superior Material Properties: The process results in parts with excellent mechanical properties and minimal residual stress.
- Wide Range of Materials: EBSM can work with a variety of metal powders, including those with high melting points.
How Does EBSM Work?
The process begins with a digital 3D model of the component. The model is sliced into thin layers, and each layer’s data is fed to the EBSM machine. The machine spreads a layer of metal powder, and the electron beam selectively melts the powder according to the design. This process is repeated layer by layer until the final part is built.
Types of Metal Powders Used in EBSM
Metal powders are the backbone of the EBSM process. Here, we list and describe specific metal powder models commonly used in EBSM.
1. Titanium Alloy (Ti6Al4V)
- Composition: 90% Titanium, 6% Aluminum, 4% Vanadium
- Properties: High strength-to-weight ratio, excellent corrosion resistance, and biocompatibility.
- Applications: Aerospace components, medical implants, and high-performance automotive parts.
2. Inconel 718
- Composition: 50-55% Nickel, 17-21% Chromium, 4.75-5.5% Niobium, 2.8-3.3% Molybdenum, 0.2-0.8% Aluminum, 0.65-1.15% Titanium
- Properties: Excellent high-temperature strength and resistance to oxidation and corrosion.
- Applications: Turbine blades, aerospace engines, and high-temperature fasteners.
3. Stainless Steel (316L)
- Composition: 16-18% Chromium, 10-14% Nickel, 2-3% Molybdenum
- Properties: Superior corrosion resistance, good mechanical properties, and weldability.
- Applications: Medical instruments, food processing equipment, and chemical processing components.
4. Aluminum Alloy (AlSi10Mg)
- Composition: 89-91% Aluminum, 9-11% Silicon, 0.25-0.45% Magnesium
- Properties: Lightweight, good thermal conductivity, and decent mechanical strength.
- Applications: Lightweight structural components, automotive parts, and heat exchangers.
5. Cobalt-Chromium Alloy (CoCr)
- Composition: 27-30% Chromium, 5-7% Molybdenum, Balance Cobalt
- Properties: High wear resistance, excellent biocompatibility, and strength.
- Applications: Dental implants, orthopedic implants, and aerospace components.
6. Maraging Steel (1.2709)
- Composition: 18% Nickel, 8-12% Cobalt, 4-5% Molybdenum, 0.05-0.15% Titanium
- Properties: High tensile strength, toughness, and ease of heat treatment.
- Applications: Tooling, aerospace structures, and high-performance parts.
7. Hastelloy X
- Composition: 47-53% Nickel, 20.5-23% Chromium, 17-20% Iron, 8-10% Molybdenum
- Properties: Exceptional high-temperature strength and oxidation resistance.
- Applications: Gas turbine engines, chemical processing equipment, and furnace components.
8. Copper Alloy (CuCr1Zr)
- Composition: 99% Copper, 0.1-0.2% Chromium, 0.03-0.08% Zirconium
- Properties: High thermal and electrical conductivity, good strength.
- Applications: Electrical components, heat exchangers, and welding electrodes.
9. Tool Steel (H13)
- Composition: 4.75-5.5% Chromium, 1.2-1.5% Molybdenum, 0.9-1.2% Vanadium, Balance Iron
- Properties: High toughness, resistance to thermal fatigue, and good wear resistance.
- Applications: Molds, dies, and high-temperature tooling.
10. Nickel Alloy (Ni718)
- Composition: 50-55% Nickel, 17-21% Chromium, 4.75-5.5% Niobium, 2.8-3.3% Molybdenum, 0.2-0.8% Aluminum, 0.65-1.15% Titanium
- Properties: Excellent mechanical properties, high-temperature resistance, and good weldability.
- Applications: Aerospace components, gas turbines, and high-stress components.
Characteristics of EBSM Metal Powders
Understanding the characteristics of these metal powders is crucial for selecting the right material for specific applications.
Metal Powder | Density (g/cm³) | Melting Point (°C) | Tensile Strength (MPa) | Yield Strength (MPa) | Elongation (%) | Hardness (HV) |
---|---|---|---|---|---|---|
Ti6Al4V | 4.43 | 1604 | 900-1200 | 830-970 | 10-15 | 350-400 |
Inconel 718 | 8.19 | 1336 | 965 | 720 | 12-15 | 220 |
316L Stainless | 8.00 | 1375 | 485 | 170 | 35 | 150 |
AlSi10Mg | 2.68 | 577 | 250 | 200 | 8-10 | 90 |
CoCr | 8.3 | 1330 | 900 | 450 | 10-15 | 550-650 |
1.2709 Steel | 8.00 | 1413 | 1900-2000 | 1700-1800 | 5-10 | 300-340 |
Hastelloy X | 8.22 | 1354 | 750 | 340 | 30 | 200 |
CuCr1Zr | 8.9 | 1083 | 300 | 80 | 40-50 | 110 |
H13 Steel | 7.8 | 1426 | 1450 | 1150 | 8-10 | 400-450 |
Ni718 | 8.19 | 1336 | 965 | 720 | 12-15 | 220 |
Applications of EBSM Metal Powders
Different metal powders serve various applications depending on their unique properties.
Metal Powder | Industries | Typical Applications |
---|---|---|
Ti6Al4V | Aerospace, Medical | Aircraft components, medical implants |
Inconel 718 | Aerospace, Energy | Turbine blades, high-temperature fasteners |
316L Stainless | Medical, Food Processing | Surgical instruments, food processing equipment |
AlSi10Mg | Automotive, Aerospace | Lightweight structural parts, heat exchangers |
CoCr | Medical, Aerospace | Dental implants, orthopedic devices |
1.2709 Steel | Tooling, Aerospace | Injection molds, aerospace structures |
Hastelloy X | Energy, Chemical Processing | Gas turbines, chemical reactors |
CuCr1Zr | Electrical, Thermal Management | Electrical connectors, heat sinks |
H13 Steel | Tooling, Manufacturing | Die casting molds, extrusion dies |
Ni718 | Aerospace, Power Generation | Jet engine components, power plant turbines |
Grades and Specifications of EBSM Metal Powders
Each metal powder used in EBSM comes in different grades and specifications to meet various industry standards.
Metal Powder | Grade | Standard | Particle Size (μm) | Purity (%) | Manufacturer |
Ti6Al4V | Grade 5 | ASTM F2924, ISO 5832 | 15-45 | 99.9 | AP&C, Arcam |
Inconel 718 | Grade 2 | ASTM B637, AMS 5662 | 15-53 | 99.8 | Carpenter, Praxair |
316L Stainless | Grade 1 | ASTM F138, ISO 5832-1 | 15-45 | 99.9 | Sandvik, GKN |
AlSi10Mg | Grade 2 | EN AC-43000, ISO 3522 | 20-63 | 99.8 | ECKA Granules, LPW |
CoCr | Grade F | ASTM F75, ISO 5832-4 | 10-45 | 99.9 | Carpenter, Sandvik |
1.2709 Steel | Maraging | ASTM A579, AMS 6514 | 15-45 | 99.9 | Höganäs, Carpenter |
Hastelloy X | HX | ASTM B435, AMS 5536 | 15-45 | 99.8 | Praxair, Haynes |
CuCr1Zr | CuCrZr | EN 12420 | 15-63 | 99.8 | Ecka Granules, Oerlikon |
H13 Steel | H13 | ASTM A681, DIN 1.2344 | 15-45 | 99.9 | Höganäs, Carpenter |
Ni718 | 718 | ASTM B637, AMS 5662 | 15-53 | 99.8 | Carpenter, Sandvik |
Suppliers and Pricing Details for EBSM Metal Powders
Knowing where to source metal powders and understanding the pricing can be critical for planning and budgeting.
Supplier | Metal Powders Available | Price Range (USD/kg) | Contact Information |
---|---|---|---|
AP&C | Ti6Al4V, Inconel 718, 316L Stainless | 200-400 | [email protected] |
Carpenter | Inconel 718, CoCr, Maraging Steel, H13 Steel | 250-500 | [email protected] |
Praxair | Inconel 718, Hastelloy X, Ni718 | 300-600 | [email protected] |
Höganäs | Maraging Steel, H13 Steel | 150-350 | [email protected] |
Sandvik | 316L Stainless, CoCr, Ni718 | 200-450 | [email protected] |
ECKA Granules | AlSi10Mg, CuCr1Zr | 150-300 | [email protected] |
GKN | 316L Stainless | 180-400 | [email protected] |
LPW Technology | AlSi10Mg | 180-350 | [email protected] |
Haynes International | Hastelloy X | 350-700 | [email protected] |
Oerlikon | CuCr1Zr | 200-400 | [email protected] |
Advantages and Limitations of EBSM
While EBSM offers numerous benefits, it’s essential to understand its limitations to make informed decisions.
Advantages
Advantage | Description |
---|---|
Design Flexibility | EBSM allows for complex geometries that are difficult or impossible to achieve with traditional manufacturing methods. |
Material Efficiency | The process minimizes waste as only the necessary amount of material is used, reducing overall material costs. |
High-Quality Parts | The resulting parts have excellent mechanical properties, with high strength and durability. |
Short Lead Times | EBSM can significantly reduce the time required to produce parts, from design to final product. |
Reduced Tooling Costs | As no molds or dies are required, EBSM eliminates the need for expensive tooling, making it cost-effective for low to medium volume production. |
Limitations
Limitation | Description |
---|---|
High Initial Investment | The cost of EBSM equipment and setup can be substantial, which might be a barrier for small businesses. |
Material Constraints | Not all metals can be processed using EBSM, limiting the choice of materials compared to traditional methods. |
Surface Finish | Parts produced by EBSM often require post-processing to achieve a smooth surface finish, adding to the production time and cost. |
Build Size Limitation | The build size is restricted by the dimensions of the EBSM machine’s build chamber, which can limit the size of parts that can be manufactured. |
Vacuum Requirement | EBSM requires a vacuum environment, which can complicate the process and increase maintenance requirements compared to other additive manufacturing technologies. |
Detailed Breakdown of EBSM Metal Powders
Here, we delve deeper into the specifics of each metal powder used in EBSM, including their unique features, advantages, and ideal applications.
Titanium Alloy (Ti6Al4V)
Titanium Alloy, specifically Ti6Al4V, is one of the most commonly used metal powders in EBSM due to its remarkable properties. This alloy is celebrated for its high strength-to-weight ratio, making it ideal for aerospace and medical applications where both strength and weight are critical factors. Additionally, its excellent corrosion resistance ensures longevity and durability in harsh environments.
Inconel 718
Inconel 718 is a nickel-based superalloy known for its superior performance at high temperatures. This makes it a preferred choice for aerospace and energy industries. Its resistance to oxidation and corrosion further enhances its suitability for components exposed to extreme conditions. Inconel 718’s robustness ensures that parts can withstand significant mechanical stress without deforming or failing.
316L Stainless Steel
316L Stainless Steel is renowned for its excellent corrosion resistance and mechanical properties. This makes it a versatile choice for a wide range of applications, from medical instruments to food processing equipment. Its ease of welding and forming also contributes to its popularity in various industrial applications.
Aluminum Alloy (AlSi10Mg)
AlSi10Mg is an aluminum alloy that stands out due to its lightweight nature and good thermal conductivity. These properties make it an excellent material for automotive and aerospace applications where reducing weight is crucial without compromising strength. Its decent mechanical properties also make it suitable for producing complex structural components.
Cobalt-Chromium Alloy (CoCr)
Cobalt-Chromium alloys are highly valued in the medical and aerospace industries for their biocompatibility and wear resistance. CoCr alloys are commonly used in dental and orthopedic implants due to their ability to withstand the body’s corrosive environment while maintaining high strength and wear resistance.
Maraging Steel (1.2709)
Maraging Steel, specifically grade 1.2709, is known for its exceptional strength and toughness. This makes it ideal for applications that require high-performance materials, such as tooling and aerospace structures. Its ease of heat treatment allows for precise control over its mechanical properties, making it a highly versatile material.
Hastelloy X
Hastelloy X is a nickel-based superalloy that excels in high-temperature environments. Its ability to maintain strength and resist oxidation at elevated temperatures makes it a go-to material for gas turbines and chemical processing equipment. Its durability and reliability in extreme conditions ensure long-term performance and safety.
Copper Alloy (CuCr1Zr)
Copper alloys like CuCr1Zr are prized for their excellent thermal and electrical conductivity. These properties make them ideal for electrical components and thermal management systems. The addition of chromium and zirconium enhances the alloy’s strength and resistance to softening at elevated temperatures.
Tool Steel (H13)
H13 Tool Steel is a chromium-molybdenum alloy known for its high toughness and resistance to thermal fatigue. These properties make it suitable for die casting molds and extrusion dies. Its durability under high temperatures ensures that tools made from H13 steel can withstand the rigors of repeated use in harsh environments.
Nickel Alloy (Ni718)
Nickel Alloy 718, commonly known as Ni718, is similar to Inconel 718 but specifically tailored for applications requiring excellent mechanical properties and high-temperature resistance. It is widely used in aerospace and power generation industries for components that must endure extreme mechanical stress and thermal conditions.
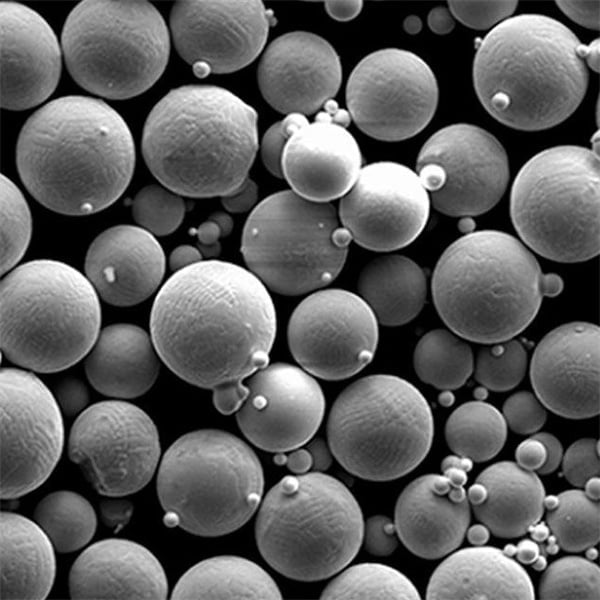
FAQs
What is Electron Beam Selective Melting?
EBSM is an additive manufacturing process that uses an electron beam to selectively melt metal powder, layer by layer, to create complex and high-precision components.
What are the benefits of using EBSM?
EBSM offers numerous benefits, including design flexibility, material efficiency, high-quality parts, short lead times, and reduced tooling costs.
Which industries benefit the most from EBSM?
Industries such as aerospace, medical, automotive, and energy benefit significantly from EBSM due to its ability to produce complex, high-strength components with excellent material properties.
What types of metal powders can be used in EBSM?
EBSM can use a variety of metal powders, including titanium alloys, nickel-based superalloys, stainless steel, aluminum alloys, cobalt-chromium alloys, and more.
What are the limitations of EBSM?
The main limitations of EBSM include high initial investment costs, material constraints, surface finish requirements, build size limitations, and the need for a vacuum environment.
How does EBSM compare to other additive manufacturing methods?
EBSM offers higher energy efficiency, superior material properties, and the ability to work with high-melting-point metals compared to laser-based methods. However, it also requires a vacuum environment and has higher initial setup costs.
Can EBSM be used for mass production?
While EBSM is excellent for prototyping and low to medium volume production, its current limitations in speed and build size make it less suitable for high-volume mass production compared to traditional manufacturing methods.
What post-processing is required for EBSM parts?
EBSM parts often require post-processing such as heat treatment, machining, and surface finishing to achieve the desired mechanical properties and surface quality.
Are there any environmental benefits to using EBSM?
EBSM can be more environmentally friendly than traditional manufacturing methods due to its material efficiency and reduced waste production.
How do I choose the right metal powder for my application?
Choosing the right metal powder depends on the specific requirements of your application, such as mechanical properties, corrosion resistance, thermal conductivity, and biocompatibility. Consulting with material suppliers and industry experts can help you make an informed decision.
By understanding the intricacies of Electron Beam Selective Melting and the various metal powders available, you can harness the full potential of this advanced manufacturing technology to create high-performance, custom-designed components.
Share On
MET3DP Technology Co., LTD is a leading provider of additive manufacturing solutions headquartered in Qingdao, China. Our company specializes in 3D printing equipment and high-performance metal powders for industrial applications.
Inquiry to get best price and customized Solution for your business!
Related Articles
About Met3DP
Recent Update
Our Product
CONTACT US
Any questions? Send us message now! We’ll serve your request with a whole team after receiving your message.
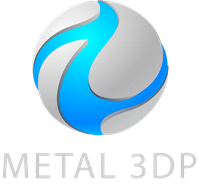
Metal Powders for 3D Printing and Additive Manufacturing