Understanding MIM Technology
Table of Contents
Overview of MIM Technology
Metal injection molding (MIM), also known as powder injection molding (PIM), is an advanced manufacturing process used to produce small, complex metal parts in high volumes.
MIM combines the design flexibility and precision of plastic injection molding with the strength and performance of machined metal parts. It enables the cost-effective production of intricate components with good mechanical properties from advanced metal alloys.
The MIM process starts with a feedstock made of fine metallic powder mixed with a binder material. This feedstock is then injected into a mold using plastic injection molding equipment. The binder holds the metal powder together and imparts flowability for molding.
After molding, the binder is removed from the molded green part through a debinding process. The debound part, called the brown part, is then sintered at high temperatures which fuses the metal particles together into a solid metal part with material properties near that of a wrought part.
MIM is suitable for making small, complex parts using various metals like stainless steel, low alloy steels, tool steels, magnetic alloys, superalloys, titanium alloys and tungsten heavy alloys. It combines the versatility of plastic injection molding with material flexibility of powder metallurgy.
The key benefits of MIM technology include:
- High volume production capability for complex, detailed metal components
- Near-net-shape manufacturing reducing waste and minimizing machining
- Good mechanical properties close to wrought materials
- Wide choice of metals including stainless steel, tool steel, super alloys
- Allows parts consolidation into single components
- Low unit cost due to high volumes
- Consistency and repeatability from automated process
MIM technology is ideal for small, complex parts like medical devices, firearms components, watch components and automotive parts which require precision, strength, economy and mass production scale.
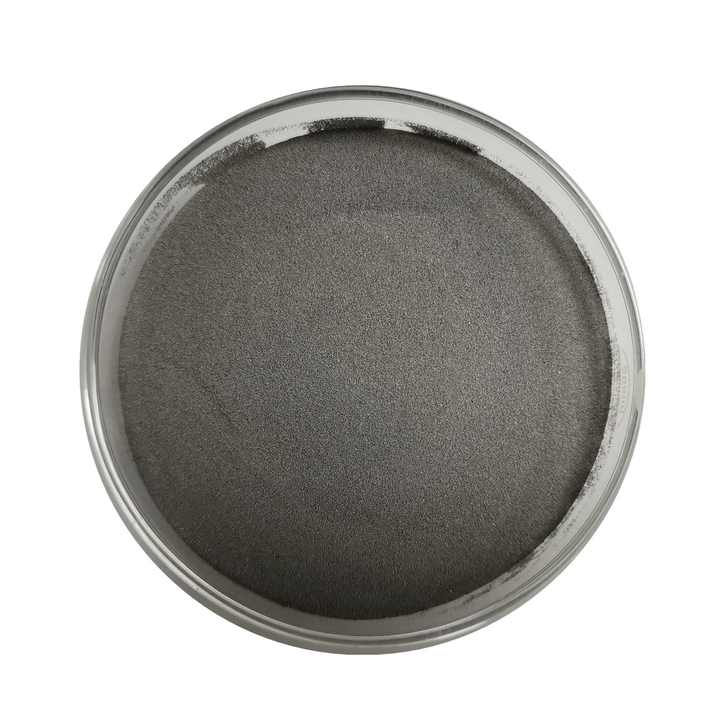
Applications and Uses of MIM Technology
MIM technology is used across various industries to manufacture small, high precision metal parts efficiently in large volumes. Here are some of the key application areas and uses of MIM technology:
Industry | Applications and Uses |
---|---|
Medical and Dentistry | Surgical instruments, dental implants, orthopedic implants, catheter components, needle cannulas, scalpel handles, forceps, clamps, surgical fasteners, reusable surgical instruments |
Firearms and Defense | Triggers, hammers, safeties, ejectors, magazines, spent casings, projectiles, warhead components |
Automotive | Fuel system components, oil pump gears, impellers, valves, turbocharger parts, electronics parts, steering/transmission components |
Aerospace | Turbine blades, impellers, gear teeth, bushings, pump components, engine parts |
Consumer Products | Watch components, jewelry findings, cutlery, scissors, razors, hand tools, zipper parts |
Industrial Hardware | Knobs, fittings, fasteners, sockets, connectors, sprinklers, nozzles |
Electronics | Connectors, switches, micromotors, microgears, screening masks, inductors, magnet rotors |
** Advantages of MIM for Specific Applications**
- Precision: Ideal for miniature parts like medical devices or watch components with intricate geometries.
- Strength: Suitable for components needing high strength like automotive turbochargers and firearm triggers.
- Wear Resistance: MIM parts made from tool steel alloys have excellent wear resistance for long service life.
- Corrosion Resistance: Stainless steel MIM parts withstand corrosion for reusable surgical tools, implants, etc.
- High Hardness: MIM can produce parts with hardness over 40 HRC like cutlery, tooling, dies, etc.
- Electrical Properties: MIM is used to make soft magnetic components like inductors, motor rotors, etc.
- Cost Effective: High volumes reduce part cost substantially compared to machining.
MIM Equipment and Tooling Guides
The main equipment used in the MIM process includes injection molding machines, debinding and sintering furnaces. Here is an overview:
Equipment | Purpose | Considerations |
---|---|---|
Injection Molding Machine | To inject the MIM feedstock into mold cavities under heat and pressure | Mold clamping force, injection rate and pressure capacity, precision and repeatability, controls and automation features. |
Binder Removal Oven | To remove the binder thermally or chemically from molded parts | Temperature range, atmosphere control, loading capacity, uniformity of debinding. |
Sintering Furnace | To densify the debound brown parts by heating to close to melting point | Temperature range, atmosphere control, uniformity of heating, batch capacity, fully automated preferred. |
Molds and tooling | Shaped cavities to form the MIM feedstock into required geometry | Withstand molding pressures and temperatures, precision machined, good surface finish, allows rapid heating/cooling. |
Feedstock Equipment | To mix the metal powder and binder into homogeneous MIM feedstock | Mixers, temperature controllers, pelletizers. |
Secondary Processing | Additional steps like machining, joining, surface treatment | As per part needs like CNC machining, welding, EDM, coating. |
Quality Control | To test feedstock, sintered parts properties | Powder morphology, density, flow rate, viscosity analyzers, mechanical testing equipment. |
Safety Equipment | To handle fine powders safely | Gloves, respirators, dust collection systems. |
Design and Performance Standards
- ISO 21227 – Powders for metal injection molding
- ASTM F2885 – Metal Injection Molding Process
- MPIF 35 – Standards for MIM feedstock
- ASTM E2781 – MIM Tensile Test Specimen Design
- ISO 2740 – Sintered Metal Injection Molding parts
Cost Breakdown
The typical cost distribution in MIM production is:
- Raw Materials (Powder + Binder): 50-60%
- Manufacturing (Molding + Debinding + Sintering): 25-35%
- Secondary Processing: 5-10%
- Quality Control: 2-5%
- Engineering (R&D, Design): 2-5%
Suppliers and Pricing
Here are some leading global suppliers of MIM equipment and their price ranges:
Supplier | Product Category | Price Range |
---|---|---|
ARBURG | Injection molding machines | $100,000 – $500,000 |
Indo-US MIM | MIM feedstock & services | $5 – $50 per Kg |
Elnik | Debinding and sintering furnaces | $50,000 – $1,000,000 |
FineMIM | End-to-end MIM production | $0.5 – $5 per part |
Parmatech | Metal powder Atomization | $250,000 – $1,000,000 |
Meridian Technologies | Tooling and mold design | $5,000 – $100,000 |
Installation, Operation and Maintenance
MIM is an automated process but needs careful installation, operation and maintenance for optimum performance:
Activity | Details |
---|---|
Installation | Precision alignment of injection molding machine and molds. Calibrate temperature controllers. Test run with trial batches. |
Operation | Ensure feedstock quality control as per standards. Achieve process parameters like injection pressure, temperature and speed. |
Maintenance | Schedule preventive maintenance for molding machine barrels, screws, molds. Maintain debinding furnace atmosphere. Calibrate instruments. |
Cleaning | Follow SOPs for machine barrel cleaning after runs. Ensure no powder accumulation in furnace or ducts. Mold cleaning with designed media. |
Safety | Wear personal protective equipment while handling fine powders. Proper disposal of chemical binders. Allow furnace cooling before maintenance. |
Training | Train machine and furnace operators on procedures. Conduct refresher sessions on safety and maintenance. |
Optimization | Adjust process parameters until part quality stabilizes within specifications. Maintain detailed process records. |
Typical Maintenance Activities and Frequency
Activity | Frequency |
---|---|
Injection molding machine nozzle cleaning | After each batch |
Mold polishing | Weekly |
Machine barrel cleaning | Monthly |
Binder removal oven atmosphere check | Monthly |
Sintering furnace thermocouple calibration | 6 months |
Mold flow studies | Annually |
How to Choose an MIM Supplier
Choosing a competent MIM supplier is critical to get good quality parts on time at reasonable cost. Here are important factors to consider:
Factor | Criteria |
---|---|
Technical Capability | Advanced equipment, years of experience, technical expertise |
Material Options | Range of materials like stainless steel, tool steel, tungsten alloys |
Secondary Processing | In-house machining, joining, coating facilities |
Quality Systems | ISO 9001 certification, quality control and inspection procedures |
Production Capacity | High volume production ability for stability |
Lead Time | Fast turnaround time from design to delivery |
Location | Geographic proximity for logistics efficiency |
Cost | Pricing model – per part pricing preferred |
Customer Service | Responsiveness to inquiries, technical support, project management |
Questions to Ask Prospective MIM Suppliers
- What materials and part sizes do you have experience with?
- Do you offer secondary processing like machining or coating?
- What quality certifications and inspection procedures are followed?
- How is handling of sensitive materials like titanium alloys or tungsten carbides done?
- What production volumes can you reliably deliver on a monthly basis?
- How is scrap minimized and yields maximized?
- What is the part-to-part variability in dimensions and properties?
- How will design optimization be done for MIM process?
- What quality reports and control charts will be provided?
Comparing MIM with Other Processes
Comparison between MIM and other metal manufacturing processes:
Process | Advantages | Disadvantages |
---|---|---|
MIM | Complex geometries, mass production, near net shape, wide material choices | Upfront tooling investment, size limitations |
CNC Machining | Material flexibility, fast turnaround of prototypes | Limited complexity, lower volumes |
Metal Casting | Low part cost, high volumes | Shape limitations, lower strength |
Metal Stamping | High speed, high volumes, low costs | Only suits 2D geometries |
3D Printing | Design freedom, fast prototyping | Lower strength, higher cost, limited sizes and materials |
Benefits of MIM over Machining
- Higher material utilization with near net shape
- No expensive machining for complex shapes
- Superior mechanical properties
- Lower tooling costs compared to machining dies
- Automated process enables mass production
- Better surface finishes possible
Advantages of MIM over Metal Casting
- Better dimensional accuracy and surface finish
- Fewer defects like porosity compared to cast parts
- Isotropic properties unlike directional casting
- Low to no flash or opening unlike castings
- No melt-related reactions or compositional changes
- Cores and undercuts possible unlike casting
- Wide material options beyond castable alloys
- Consistency of properties with powder metallurgy
Limitations of MIM versus CNC Machining
- Size limited by injection molding machine capacity
- More upfront time and cost for tooling
- Tight tolerances +/- 0.5% vs. +/- 0.1% for CNC machining
- Geometry limitations vs. unrestricted machining
- Lower maximum hardness achievable compared to machining
- Secondary machining often still needed to achieve tolerances
When Not to Use MIM
- Very large parts beyond MIM equipment capacity
- Parts needing extremely tight tolerances below 0.5%
- Applications requiring surface hardness above 50 HRC
- Products with very low volume requirements
- Components with extreme aspect ratios unsuitable for molding
- When no time for design optimization for MIM process
- Cost-sensitive applications with cheaper manufacturing options
MIM Design and Modeling Considerations
Proper part and feedstock design is crucial for MIM to achieve required properties and performance. Here are key design considerations:
Part Design Stage
- Optimize wall thicknesses for uniform mold filling during injection
- Include generous internal radii and fillets to ease filling
- Avoid severe changes in cross-section along the flow path
- Design proper mold gates and runners for suitable flow patterns
- Add strengthening ribs and gussets to avoid sagging or warpage
- Account for part shrinkage during sintering in initial dimensions
- Develop prototype molds for design validation before full production
Feedstock Development
- Match feedstock viscosity to mold complexity at molding temperatures
- Ensure sufficient powder loading for required sintered density
- Select suitable binder components and powder ratio for mixability
- Optimize powder particle size distribution for powder packing density
- Adjust feedstock formulations for defect-free binder removal
- Validate feedstock properties through mold flow simulations
- Test multiple feedstock iterations to achieve full mold-ability
Simulation and Modeling
- Mold flow modeling to optimize gate locations and runners
- Structural FEA to predict warpage and optimize part geometry
- CFD simulations for uniform binder removal and sintering
- Thermal modeling to minimize residual stresses
- Mechanical modeling to maximize strength and performance
- Process modeling software to study interactions between parameters
- Experimental validation of software predictions through prototype molds
Key Modeling Outputs
- Mold filling time, feedstock viscosity, flow front temperature
- Weld line, air trap and other molding defect predictions
- Spatial binder content, temperature and dissolution gradients
- Sintering rate, density gradients, shrinkage, warpage trends
- Residual stress distribution, hot tear and crack estimates
- Mechanical strength, fatigue life, damage tolerance analysis
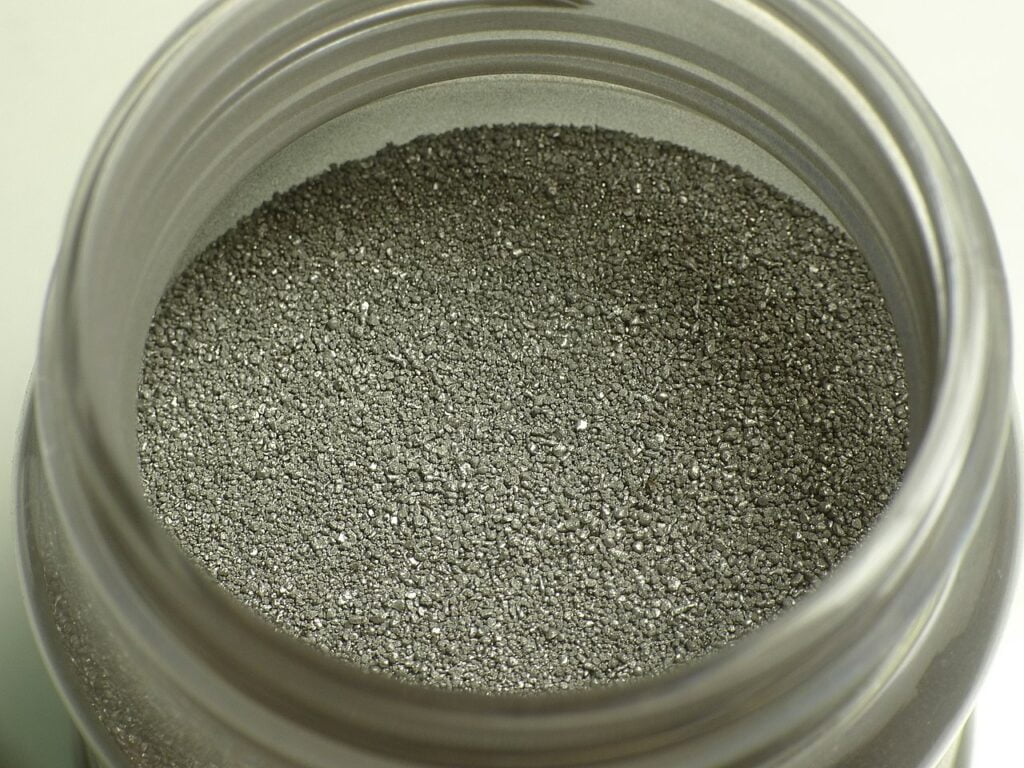
MIM Defects and Mitigation Methods
Defects can arise in MIM parts due to non-optimized feedstock, molding parameters or furnace conditions. Here are common MIM defects and mitigation methods:
Defect | Root Causes | Mitigation Methods |
---|---|---|
Surface defects | Low mold temperature, high friction, binder components | Optimize mold polishing, use mold release agents, lower mold temp gradually |
Weld lines | Undesirable feedstock flow fronts | Optimize gate and runner design through modeling to prevent weld lines |
Warpage | Non-uniform heating in furnace, residual stresses | Structural optimization, pre-sintering stress relief, optimized furnace settings |
Cracks | Rapid sintering, high binder content, steep thermal gradients | Lower heating rate, optimize binder system, structural redesign |
Porosity | Low powder loading in feedstock, poor mixing | Increase powder content in feedstock, improve mixing process |
Dimensional variation | Inconsistent shrinkage, mold wear, density gradients | Statistical process control, mold maintenance, optimize debinding and sintering |
Contamination | Poor handling, furnace atmosphere control | Proper PPE, improve air filters, prevent cross-contamination in furnace batches |
Incomplete filling | High mold temperature, high viscosity | Increase mold and feedstock temperature, use lower viscosity binder |
MIM Industry Data and Trends
MIM Global Market Size
The global MIM market was valued at USD 1.5 billion in 2022 and is projected to reach USD 3.1 billion by 2030, growing at 8.7% CAGR, driven by demand from healthcare, automotive and aerospace sectors.
Industry Growth Drivers
- Lightweighting trends across automotive, aerospace, electronics sectors
- Demand for small, complex metal components in medical devices
- More viable with a wider range of MIM-able materials
- Automation bringing down production costs
- Growth in manufacture of precision components
- Increased adoption in emerging applications like watchmaking
Projected CAGR by Region
- Asia Pacific: 9.3% CAGR
- Europe: 10.2% CAGR
- North America: 7.6% CAGR
- Rest of the World: 7.9% CAGR
Share of MIM Parts by Industry
- Consumer products: 22%
- Automotive: 21%
- Firearms: 15%
- Medical: 14%
- Industrial: 13%
- Aerospace: 8%
- Others: 7%
MIM Technology Development Trends
- New binder systems to reduce defects and enable complex geometries
- Novel feedstock formulations for better powder loading and sintering
- Multi-material MIM combining different powders into one component
- Automation of post-processing like machining, joining, threading etc.
- Hybrid MIM + Additive Manufacturing techniques
- New heating methods like microwave sintering for faster processing
- Integrated simulations combining multiple physics and manufacturing steps
- Increased adoption of quality management systems
Summary
Key takeaways:
- MIM enables high volume production of intricate metal components through combining injection molding and powder metallurgy.
- Suitable for small, complex, high precision parts in medical, firearms, automotive, aerospace, and consumer industries.
- Benefits include near-net shape, wide material choice, good mechanical properties close to wrought materials.
- Involves molding of feedstock, debinding, and sintering steps using specialized equipment.
- Requires expertise in part design, feedstock development, process modeling, defect control, and quality management.
- Projected to grow at 8.7% CAGR globally driven by demand across industries.
- Ongoing technology developments for faster processing, more materials, increased automation and improved part quality.
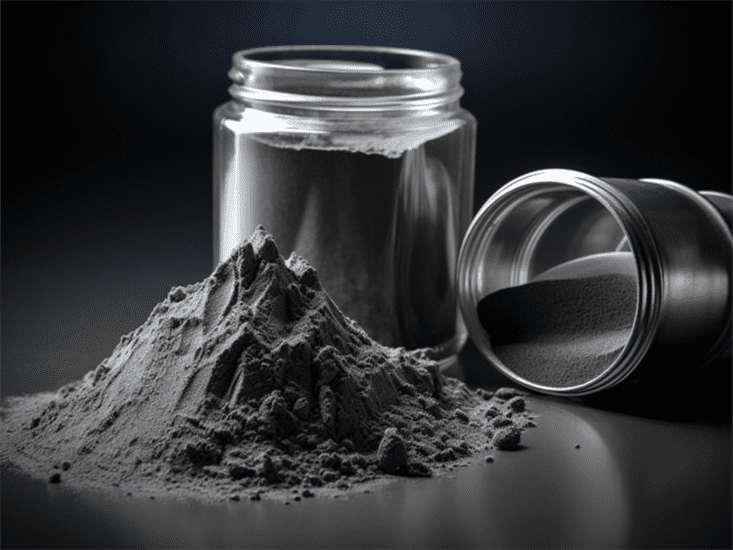
FAQs
Q: What are the key advantages of MIM technology?
A: The main advantages of MIM are:
- Ability to produce small, complex geometries not possible through machining or casting
- Near-net shape manufacturing resulting in
Q: What is the typical tolerance capability of MIM?
A: MIM can generally achieve tolerances of +/- 0.5% although +/- 0.3% is possible for some geometries and machining may be needed for tighter tolerances.
Q: What size of parts can be produced using MIM?
A: MIM can produce parts from 0.1 grams up to around 250 grams in mass. Larger parts are possible but challenging due to limitations in molding machine size.
Q: How does MIM compare to plastic injection molding?
A: While both use injection molding equipment, MIM can produce metal parts whereas plastics have much lower strength. But MIM has lower production rates and higher costs than plastic injection molding.
Q: What heat treatment is used in MIM?
A: The sintering process in MIM involves heating to almost melting point of the metal powder so no further heat treatment is typically needed. Additional heat treatments can be done as required to modify properties.
Q: What materials can be used in MIM?
A: A wide range of materials are MIM-able including stainless steels, tool steels, superalloys, titanium, tungsten heavy alloys, and magnetic alloys among others. New material development is a key research area in MIM.
Q: How does MIM compare to metal 3D printing?
A: MIM can produce higher volumes with better surface finish and mechanical properties. But 3D printing offers greater design freedom and faster time to market for prototypes or custom parts.
Share On
MET3DP Technology Co., LTD is a leading provider of additive manufacturing solutions headquartered in Qingdao, China. Our company specializes in 3D printing equipment and high-performance metal powders for industrial applications.
Inquiry to get best price and customized Solution for your business!
Related Articles
About Met3DP
Recent Update
Our Product
CONTACT US
Any questions? Send us message now! We’ll serve your request with a whole team after receiving your message.