Understanding Powder Atomization Equipment
Table of Contents
Powder atomization is a mechanical process used to produce fine powders from molten metal. It involves breaking up a molten metal stream into fine droplets which solidify into powder particles. Atomization produces spherical metallic powders with controlled particle size distribution. This overview examines the key aspects of powder atomization equipment.
Powder Atomization Equipment Types
There are several main types of atomization equipment used in industrial powder production:
Equipment | Description |
---|---|
Gas atomization | Molten metal stream atomized by high pressure inert gas jets |
Water atomization | Molten metal stream broken up by high pressure water jets |
Centrifugal atomization | Molten metal poured or driven off edge of spinning disc |
Ultrasonic atomization | High frequency vibrations applied to molten stream |
Plasma atomization | Plasma arc melts and atomizes metal into fine droplets |
Gas atomization and water atomization are the most common industrial methods. Centrifugal, ultrasonic and plasma atomization have more specialized applications. The choice depends on factors like material being atomized, powder specifications required, production rate and cost.
Atomization Process Characteristics
Key characteristics of the powder atomization process using different methods:
Characteristic | Typical Range |
---|---|
Gas pressure | 2-8 MPa |
Water pressure | 10-150 MPa |
Gas flow rate | 0.5-3 m3/min/mm2 |
Disc diameter | 100-1000 mm |
Disc speed | 10000-50000 rpm |
Frequency | 20-60 kHz |
Plasma power | 30-80 kW |
Higher gas and water pressures produce finer powder particles. Faster disc speeds and higher frequencies also create finer powders. The ranges reflect industrial practice for common metals like steel, aluminum, copper alloys.
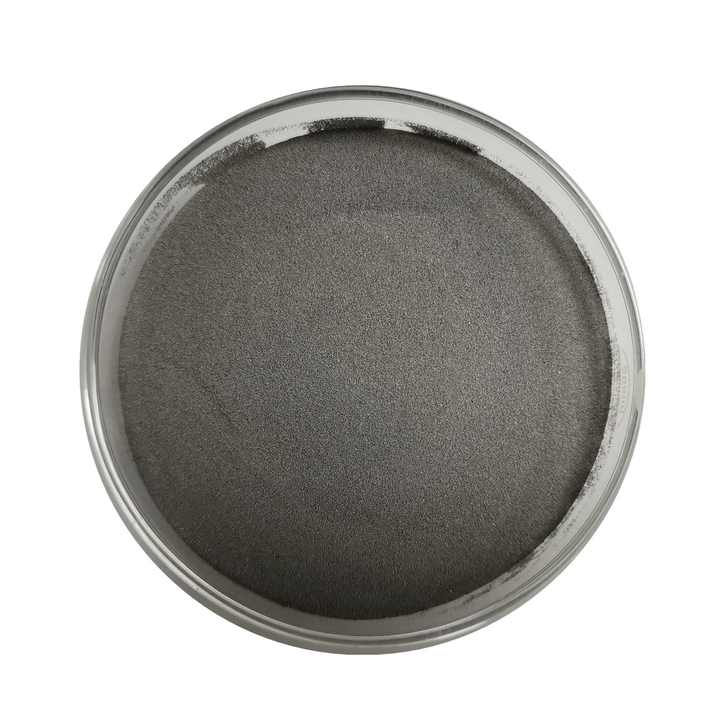
Powder Particle Size Control
Particle size distribution is a critical quality metric for atomized powders. The main factors controlling powder particle size are:
- Atomizing fluid pressure – higher pressure creates finer particles
- Atomizing fluid flow rate – higher flow gives finer particles
- Molten metal flow rate – lower metal flow yields finer powder
- Atomizing nozzle design – nozzle geometry affects droplet size
- Disc/nozzle relative velocity – faster relative motion makes smaller droplets
- Material properties – viscosity, surface tension affect fragmentation
Careful control of these parameters allows production of powder with target particle size distribution. For example, gas atomized steel powder with D50 of 10-100 microns.
Applications of Atomized Metal Powders
Atomized powders find uses in many industries and applications:
Industry | Applications |
---|---|
Powder metallurgy | Press and sinter components, MIM feedstock |
Metal additive manufacturing | Binder jet printing, DED feedstock |
Thermal spray coatings | Wire-arc, plasma, flame spray coatings |
Welding | Flux cored arc welding filler |
Brazing | Braze pastes and preforms |
Electronics | Conductive pastes and inks |
Automotive | Friction materials, powder forging |
Spherical atomized powders provide excellent flowability and mixing needed for many powder processing methods. Tight control of powder size distribution optimizes performance.
Powder Atomization System Design
Key elements in designing an atomization system are:
- Metal delivery – Tundish, pouring vat, induction guide or rotating electrode
- Atomizer – Nozzle design, number of nozzles, nozzle placement
- Atomizing medium – Gas control manifold, water pumps and plumbing
- Powder collection – Cyclone separators, bag house filters, scrubbers
- System controls – Pressure, temperature and flow sensors and control loops
Additional considerations are containment, safety interlocks, powder handling and storage. Systems can be custom engineered to produce most metal alloys.
Specifications for Atomization Equipment
Typical specifications for industrial gas and water atomization systems:
Parameter | Typical Ranges |
---|---|
Production capacity | 10-5000 kg/h |
Atomizing gas pressure | 2-8 MPa |
Atomizing gas flow | 0.5-3 Nm3/mm2 |
Water pressure | 10-150 MPa |
Nozzle size | 2-8 mm ID |
Nozzle type | Straight bore, convergent-divergent |
Cyclone efficiency | >95% at 10 μm |
Baghouse efficiency | >99.9% at 1 μm |
Capacity, pressure, and nozzle details depend on alloy, desired particle sizes and production rates. System is custom designed for specific application.
Installation and Operation
Important considerations for installing and operating powder atomization equipment:
- Proper foundations and supports for dynamic equipment
- Vibration isolation to minimize transfer to structures
- Robust interlocks on gas, water, electrical systems
- Monitoring and control instrumentation for process variables
- Containment of overspray and dust in work zones
- Fume and dust extraction equipment operation
- Safety protocols for molten metal handling and spray
- Calibration and maintenance of gas/water systems
- Shutdown and cleanout procedures to prevent buildup
Startups should follow carefully developed procedures. Staff training is critical to safely operate and maintain the system.
Maintenance Requirements
Routine maintenance is needed for optimal uptime and powder quality:
- Inspect atomizing nozzles – replace worn or damaged nozzles
- Check spin plates on centrifugal atomizers – resurface or replace
- Clean powder collection cyclones and bag house filters
- Verify calibration of pressure, flow and temperature sensors
- Check operation of emergency stop valves and interlocks
- Monitor atomizing gas purity – moisture can cause oxidation
- Clean feed lines and tundish to avoid metal buildup
- Lubricate and inspect spin drive motor and bearings
Establish maintenance schedule and procedures based on hours of operation and criticality.
Choosing an Atomization Equipment Supplier
Key factors in selecting an atomization system supplier:
- Experience with specific alloy being atomized
- Capability to engineer full system
- Range of available nozzle designs and atomizer configurations
- Flexibility to meet capacity and particle size needs
- Installation, training, and aftersales support offered
- Local presence or partnerships in target market
- Compliance with applicable codes and standards
- References and case studies for similar projects
- Pricing and delivery timeline
Evaluate suppliers based on technical expertise, not just equipment cost. An experienced partner helps ensure success.
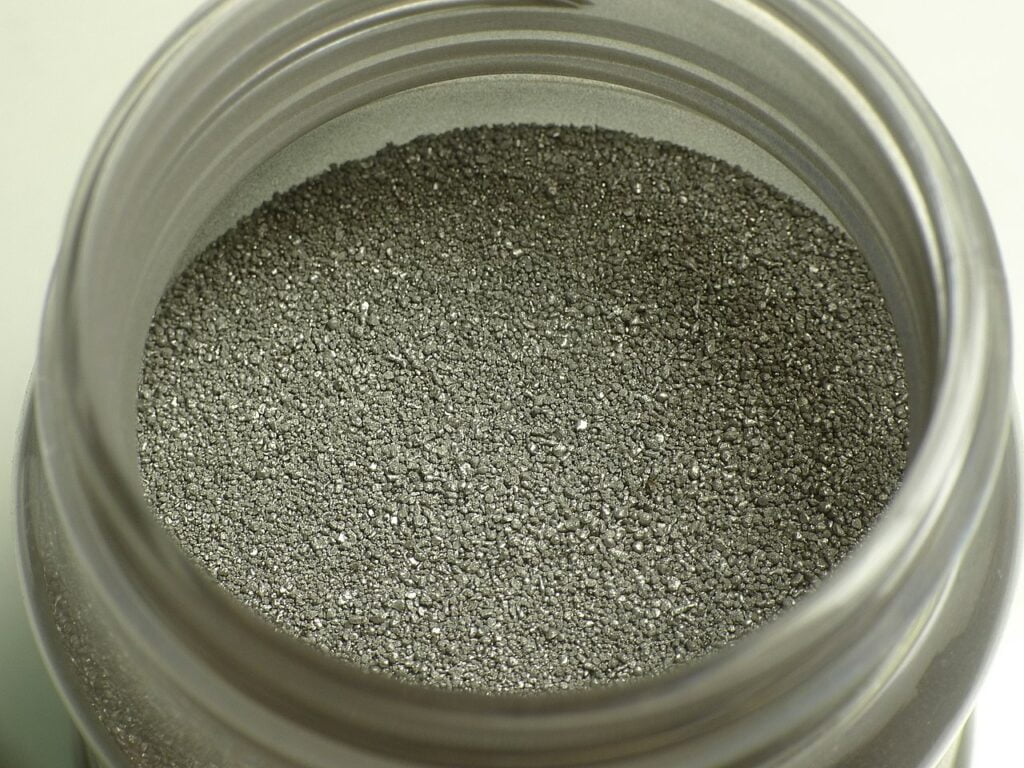
Cost Analysis of Atomization Systems
Atomization equipment has high capital cost but can produce powder at competitive pricing:
System | Capital Cost Range | Powder Price Range |
---|---|---|
Gas atomization | $500,000 – $5,000,000 | $5-50/kg |
Water atomization | $200,000 – $2,000,000 | $2-20/kg |
Centrifugal atomization | $50,000 – $500,000 | $10-100/kg |
Ultrasonic atomization | $100,000 – $1,000,000 | $50-500/kg |
Plasma atomization | $200,000 – $2,000,000 | $20-200/kg |
Costs driven by capacity, materials of construction, controls. Fine powders command premium pricing. Require high production volume to justify capital investment.
Pros and Cons of Powder Atomization Methods
Comparison of advantages and limitations of different atomization techniques:
Method | Advantages | Disadvantages |
---|---|---|
Gas atomization | Narrowest particle distribution, inert atmosphere | High capital cost, high gas consumption |
Water atomization | Lower equipment cost, small particle sizes | Oxidation possible, drying required |
Centrifugal atomization | Simple design, easy scale up | Broad particle distribution, irregular shapes |
Ultrasonic atomization | No fluids required, low maintenance | Limited alloys and production rate |
Plasma atomization | Very fine particles from pure metal | High energy use, low powder output |
Select method based on priority factors like particle size, atmosphere, cost, alloy compatibility. No single best option for all scenarios.
Key Takeaways on Powder Atomization Technology
- Wide range of equipment options to produce fine metal powders from molten alloys
- Gas and water atomization most common; specialized techniques available
- Control of fluid and metal flow dynamics governs final particle sizes
- Spherical powders with optimized particle distribution enable advanced applications
- Significant capital investment required but powder pricing can support it
- Partnering with experienced supplier critical for successful atomization project
Careful process development and engineering produces powder with characteristics to match application needs.
Powder Atomization Equipment FAQ
Q: What metals and alloys can be atomized into powder?
A: Most standard steels, aluminum alloys, copper alloys, nickel superalloys can be atomized. Refractory metals like tungsten and tantalum are also possible. Limitations are related to melting point, reactivity, and viscosity.
Q: What are typical gas atomization pressures and flow rates?
A: Gas pressures range from 2-8 MPa for air or inert gases like nitrogen and argon. Flow rates vary from 0.5-3 Nm3/min/mm2 of nozzle opening area, depending on pressure and particle size targets.
Q: How small can particles be made through atomization?
A: Gas and water atomization can produce powders down to 5-10 microns. Specialized techniques like ultrasonic or plasma can generate submicron particles. Smaller sizes have much lower production rates.
Q: How consistent is the particle size distribution?
A: Well engineered atomization systems can achieve CV of 5-10% on normal particle size distribution. Tighter distributions are possible but require extensive process development and control.
Q: How much powder can centrifugal atomization process produce?
A: Centrifugal atomizers are relatively compact and lower cost. Production capacity ranges from 10-100 kg/h, suitable for small volume specialty alloys.
Q: What determines capital cost of an atomization system?
A: Key factors are alloy being processed, particle size and distribution targets, production rate, controls, and material of construction. A 500 kg/h gas atomization system costs around $1-2 million.
Q: What safety precautions are needed for powder atomization?
A: Proper personal protective equipment for handling hot metal and atomized powder is critical. Containment of overspray, proper ventilation, monitoring equipment for gases and dusts, and emergency stop circuits help mitigate risks.
Q: What maintenance is required on atomization equipment?
A: Nozzles, spin plates, and collection cyclones wear over time and need replacement. Hoses, valves, sensors, and pumps must be serviced regularly. Proper start up and shutdown prevents buildup. Training staff on protocols is vital.
Q: How is powder handling and storage managed after atomization?
A: Powder should be quickly transferred from collectors into sealed containers to limit exposure and oxidation. Moisture control is critical. Separate room temperature storage with fire suppression and explosion venting is standard.
Q: What standards apply to atomization system design?
A: There are no universal standards, but applicable pressure vessel codes and material standards dictate design choices. Consult experienced suppliers familiar with local regulations and requirements. Get legal and regulatory council when installing new hazardous systems.
Share On
MET3DP Technology Co., LTD is a leading provider of additive manufacturing solutions headquartered in Qingdao, China. Our company specializes in 3D printing equipment and high-performance metal powders for industrial applications.
Inquiry to get best price and customized Solution for your business!
Related Articles
About Met3DP
Recent Update
Our Product
CONTACT US
Any questions? Send us message now! We’ll serve your request with a whole team after receiving your message.