Vacuum Induction Melting
Table of Contents
Overview of Vacuum Induction Melting
Vacuum induction melting (VIM) is a sophisticated and essential process in the metallurgy industry, used primarily to produce high-quality metal alloys. By melting metals under a vacuum, this method minimizes the risk of contamination from gases and impurities, resulting in superior material properties. It’s widely employed in industries where high purity and specific alloy compositions are critical, such as aerospace, medical devices, and high-performance engineering components.
Understanding Vacuum Induction Melting
Vacuum induction melting works by utilizing electromagnetic induction to heat and melt metals in a vacuum-sealed environment. The vacuum conditions reduce the presence of oxygen, nitrogen, and hydrogen, which can cause defects in the final product. This process ensures that the metals produced have excellent mechanical properties, high purity, and controlled compositions.
Key Components and Process
- Induction Furnace: The core of the VIM process, using alternating current to create an electromagnetic field that induces heat in the metal.
- Vacuum Chamber: Encloses the induction furnace, ensuring that melting occurs in a vacuum or inert atmosphere.
- Power Supply: Provides the necessary electrical power for induction heating.
- Cooling System: Maintains appropriate temperatures and prevents overheating.
Benefits of Vacuum Induction Melting
- High Purity: Eliminates contaminants, producing exceptionally pure metals.
- Precise Control: Allows for precise control over alloy compositions.
- Superior Mechanical Properties: Enhances the material’s strength, ductility, and overall performance.
- Versatility: Suitable for a wide range of metals and alloys.
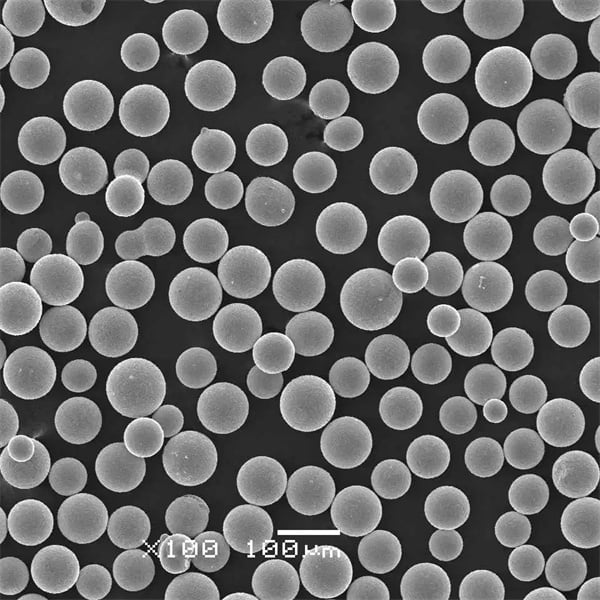
Types of Metal Powders Produced Using Vacuum Induction Melting
Common Metal Powders and Their Uses
Metal Powder | Composition | Properties | Applications |
---|---|---|---|
Nickel Alloy 625 | Ni, Cr, Mo, Nb | High strength, corrosion-resistant | Aerospace, marine, chemical processing |
Titanium Alloy Ti-6Al-4V | Ti, Al, V | High strength-to-weight ratio, biocompatibility | Medical implants, aerospace |
Cobalt-Chromium Alloy | Co, Cr, Mo | Wear-resistant, biocompatible | Dental and orthopedic implants |
Inconel 718 | Ni, Cr, Fe, Nb, Mo | High temperature resistance, strength | Gas turbines, nuclear reactors |
Stainless Steel 316L | Fe, Cr, Ni, Mo | Corrosion-resistant, good weldability | Medical devices, food processing |
Aluminum Alloy 7075 | Al, Zn, Mg, Cu | High strength, lightweight | Aerospace, sporting goods |
Tool Steel H13 | Fe, Cr, Mo, V | High toughness, wear resistance | Die casting, extrusion tools |
Copper Alloy C18200 | Cu, Cr | High conductivity, corrosion resistance | Electrical components, welding electrodes |
Magnesium Alloy AZ91D | Mg, Al, Zn | Lightweight, good castability | Automotive, electronics |
Tantalum | Pure Ta | High melting point, corrosion-resistant | Chemical processing, electronics |
Applications of Vacuum Induction Melting
Vacuum induction melting is utilized across various industries to produce components that require high integrity and specific material properties. Here are some key applications:
Industry | Components Produced |
---|---|
Aerospace | Turbine blades, engine components |
Medical | Implants, surgical instruments |
Automotive | High-performance engine parts |
Electronics | Conductive materials, semiconductor components |
Energy | Turbine components, nuclear reactor parts |
Specifications, Sizes, Grades, and Standards
When dealing with metal powders and components produced via vacuum induction melting, it’s crucial to adhere to specific standards and specifications to ensure quality and performance. Below is an overview of common specifications:
Material | Specifications | Sizes | Grades | Standards |
---|---|---|---|---|
Nickel Alloy 625 | ASTM B446, AMS 5666 | Various sizes | UNS N06625 | ISO 9001, AS9100 |
Titanium Alloy Ti-6Al-4V | ASTM F136, AMS 4911 | Various sizes | Grade 5 | ISO 5832-3, ASTM F136 |
Stainless Steel 316L | ASTM A240, A276 | Various sizes | UNS S31603 | ISO 9001, ASTM A276 |
Inconel 718 | ASTM B637, AMS 5663 | Various sizes | UNS N07718 | ISO 9001, AS9100 |
Tool Steel H13 | ASTM A681, AISI H13 | Various sizes | Grade H13 | ISO 9001, ASTM A681 |
Comparing Pros and Cons of Vacuum Induction Melting
Advantages | Disadvantages |
---|---|
High Purity: Produces metals with fewer impurities and defects. | Cost: High initial setup and operational costs. |
Controlled Atmosphere: Minimizes contamination from gases and other elements. | Complexity: Requires skilled operators and precise control systems. |
Versatility: Can be used for a wide range of metals and alloys. | Scale: Limited batch sizes compared to other methods. |
Enhanced Properties: Improves mechanical properties and performance of metals. | Maintenance: Requires regular maintenance of the vacuum system and induction furnace. |
Major Suppliers and Pricing Details
When sourcing metal powders and components produced through vacuum induction melting, it’s essential to consider suppliers’ reputations, quality standards, and pricing. Here is a summary of some notable suppliers:
Supplier | Location | Products | Pricing (Approx.) |
---|---|---|---|
ATI Metals | USA | Nickel alloys, titanium alloys | $50 – $200/kg |
Carpenter Technology | USA | Specialty alloys, stainless steel | $40 – $180/kg |
Sandvik Materials Technology | Sweden | Stainless steel, high-performance alloys | $30 – $150/kg |
VSMPO-AVISMA | Russia | Titanium alloys | $60 – $220/kg |
H.C. Starck Solutions | Germany | Refractory metals, advanced alloys | $70 – $250/kg |
Advantages and Limitations of Vacuum Induction Melting
Advantages
- Purity and Quality: One of the most significant benefits of VIM is the ability to produce extremely pure metals, essential for high-performance applications.
- Precise Alloy Composition: The process allows for precise control over the alloying elements, ensuring that the final product meets exact specifications.
- Improved Mechanical Properties: Metals produced through VIM often exhibit superior mechanical properties, such as increased strength, toughness, and resistance to fatigue and corrosion.
Limitations
- High Costs: Both the setup and operational costs of vacuum induction melting are high, which can be a barrier for smaller companies or low-volume production.
- Complex Operation: The process requires highly skilled operators and sophisticated control systems to maintain the necessary conditions for quality production.
- Batch Size: The size of batches that can be produced is often smaller compared to other melting processes, which can limit production capacity.
Comparing Vacuum Induction Melting with Other Melting Processes
Parameter | Vacuum Induction Melting | Electric Arc Melting | Air Induction Melting |
---|---|---|---|
Purity | High | Moderate | Low |
Cost | High | Moderate | Low |
Control Over Composition | Excellent | Good | Fair |
Batch Size | Small to Medium | Medium to Large | Large |
Mechanical Properties | Superior | Good | Fair |
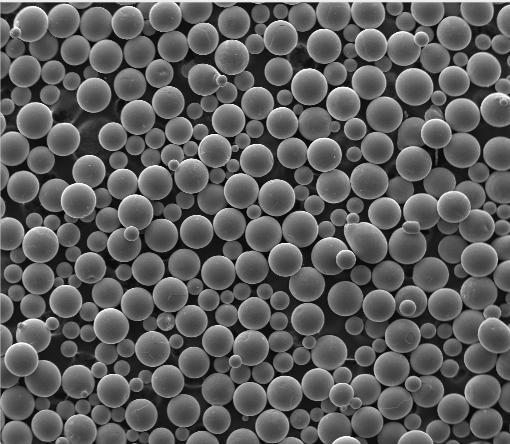
FAQs
Question | Answer |
---|---|
What is Vacuum Induction Melting? | Vacuum induction melting is a process that uses electromagnetic induction to melt metals in a vacuum-sealed environment to produce high-purity alloys. |
Why is a vacuum used in this process? | The vacuum reduces the presence of gases such as oxygen, nitrogen, and hydrogen, which can cause impurities and defects in the metal. |
What types of metals can be melted using VIM? | Various metals including nickel, titanium, cobalt, stainless steel, and more can be melted using VIM. |
What industries commonly use VIM? | Aerospace, medical, automotive, electronics, and energy industries commonly use VIM to produce high-performance components. |
What are the benefits of using VIM over other melting processes? | VIM offers higher purity, better control over alloy composition, and superior mechanical properties compared to other melting processes. |
Are there any limitations to using VIM? | Yes, VIM can be costly and complex, requiring skilled operators and precise control systems. It also typically handles smaller batch sizes. |
Share On
MET3DP Technology Co., LTD is a leading provider of additive manufacturing solutions headquartered in Qingdao, China. Our company specializes in 3D printing equipment and high-performance metal powders for industrial applications.
Inquiry to get best price and customized Solution for your business!
Related Articles
About Met3DP
Recent Update
Our Product
CONTACT US
Any questions? Send us message now! We’ll serve your request with a whole team after receiving your message.
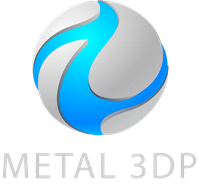
Metal Powders for 3D Printing and Additive Manufacturing