Durable Valve Bodies via Metal AM for Marine Use
Table of Contents
Durable Valve Bodies via Metal AM for Marine Use
The maritime industry operates in some of the planet’s most demanding conditions. Constant exposure to corrosive saltwater, extreme temperatures, high pressures, and significant mechanical stress places immense strain on every component. Among the most critical elements ensuring operational safety and efficiency are valve bodies. These essential components regulate fluid flow in vital systems, from ballast water management and engine cooling to desalination plants and hydraulic controls. Traditionally manufactured through casting or forging, valve bodies face challenges related to long lead times, design constraints, and material limitations, especially when dealing with complex geometries or specialized alloys required for harsh marine environments. However, the advent of metal additive manufacturing (AM), commonly known as metal 3D printing, is revolutionizing how these critical parts are produced, offering unprecedented advantages in design freedom, material performance, and supply chain agility for marine engineering solutions.
Introduction: Enhancing Marine Operations with AM Valve Bodies
Valve bodies are the foundational casing for valves, containing the internal components (like gates, globes, balls, or plugs) that control the flow of liquids or gases. In marine applications, their integrity is paramount. A failure can lead to system shutdowns, costly repairs, environmental damage, or even catastrophic safety incidents. The materials used must withstand severe corrosion from seawater, often exacerbated by pollutants, varying temperatures, and microbial activity. Furthermore, the internal pressures and stresses demand high mechanical strength and durability.
Traditional manufacturing methods like sand casting, investment casting, or forging have served the industry for decades. While effective for mass production of standard designs, they often involve:
- Long Lead Times: Tooling creation (molds, dies) can take weeks or months, delaying production, especially for custom or low-volume parts.
- Design Limitations: Certain complex internal geometries, optimized flow paths, or integrated features are difficult or impossible to achieve cost-effectively with subtractive or formative methods.
- Material Waste: Machining processes can generate significant scrap material, increasing costs and environmental impact.
- Supply Chain Complexities: Sourcing specialized castings or forgings, particularly for obsolete or legacy systems, can be challenging and expensive, impacting maintenance and repair schedules for vessel operators and marine service providers.
Metal additive manufacturing offers a transformative alternative. By building parts layer by layer directly from digital models using high-performance metal powders, metal 3D printing provides solutions to many of these traditional pain points. This technology enables the production of highly complex, optimized, and durable valve bodies specifically tailored for the unforgiving conditions of marine and offshore environments. Companies like Met3dp, leveraging decades of collective expertise in metal AM, are at forefront of this shift, providing not only advanced printing equipment but also specialized metal powders crucial for marine applications. Based in Qingdao, China, Met3dp utilizes industry-leading technologies to deliver comprehensive AM solutions, empowering the maritime sector to enhance operational reliability and efficiency through next-generation manufacturing.
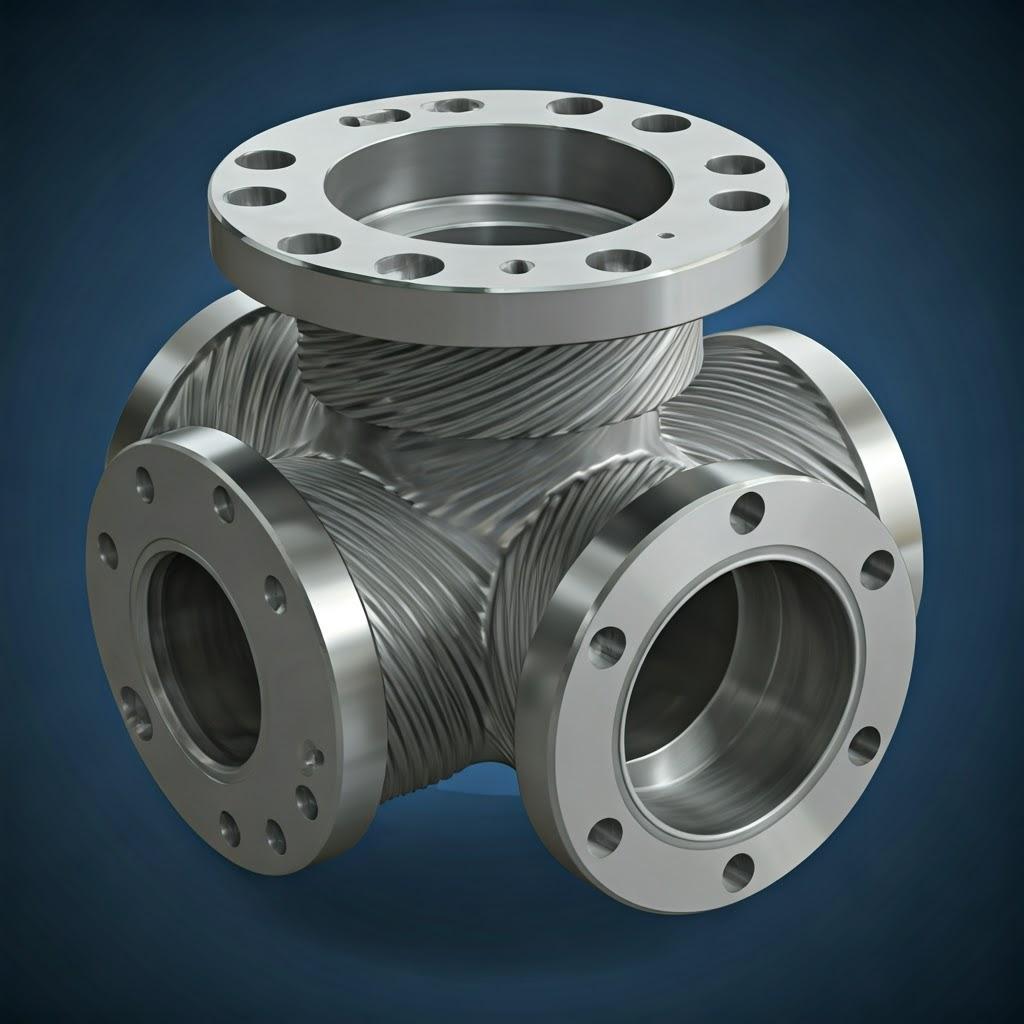
Marine Valve Body Applications: Where Durability Meets Demand
The scope of valve body applications within the marine industry is vast, reflecting the complexity of modern vessels and offshore structures. Metal AM is proving particularly valuable where performance, reliability, and tailored solutions are critical. Key application areas include:
- Shipbuilding and Vessel Operations:
- Ballast Water Management Systems (BWMS): Require valves resistant to varying water qualities and treatment chemicals (e.g., chlorine, ozone). AM allows for optimized flow paths and integration of sensors within compact designs. Materials like super duplex stainless steels (like 254SMO) or nickel-copper alloys offer superior corrosion resistance.
- Seawater Cooling Systems: Essential for engines and auxiliary machinery. Valve bodies must handle continuous seawater flow, demanding high resistance to general corrosion, pitting, and crevice corrosion. CuNi alloys (like CuNi30Mn1Fe) are often preferred for their excellent biofouling resistance and seawater corrosion performance.
- Fuel and Lubrication Systems: Require valves compatible with various fuel types and oils, often under pressure. Stainless steels like 316L provide a good balance of corrosion resistance and strength.
- Firefighting Systems: Demand high reliability and resistance to stagnant seawater corrosion. AM enables robust designs potentially integrating monitoring features.
- Hydraulic Systems: Operating cranes, winches, and steering gear involves high pressures. AM can produce valve bodies from high-strength alloys with complex internal channels optimized for hydraulic fluid flow.
- Offshore Oil and Gas Platforms:
- Production and Process Systems: Handling crude oil, natural gas, and produced water requires materials resistant to harsh chemicals (H2S, CO2) and high pressures/temperatures. Specialized alloys printable via AM offer tailored solutions.
- Subsea Equipment: Valves deployed deep underwater face extreme pressures, low temperatures, and galvanic corrosion risks. AM enables the creation of highly reliable, compact valve bodies from exotic alloys designed for longevity in inaccessible locations. Procurement managers for offshore projects value the ability to source robust, custom components.
- Utility Systems: Similar to shipboard systems (cooling, firewater), but often on a larger scale and subject to stringent offshore regulations.
- Desalination Plants (Ship-Based and Land-Based Marine Adjacent):
- Reverse Osmosis (RO) Systems: High-pressure seawater requires extremely corrosion-resistant materials to prevent premature failure. Super austenitic or duplex stainless steels (like 254SMO) are critical, and AM facilitates complex manifold and valve body designs to optimize flow and minimize pressure drops. Wholesale buyers for desalination projects look for reliable suppliers of these critical components.
- Naval Applications:
- Military vessels demand high shock resistance, low magnetic permeability (in some cases), and extreme reliability. AM offers pathways to produce specialized valve bodies meeting stringent naval specifications, often requiring difficult-to-machine materials.
Table: Key Marine Application Areas for AM Valve Bodies
Application Area | Key Systems Requiring Durable Valves | Critical Requirements | Potential AM Benefits | Target Audience Considerations |
---|---|---|---|---|
Shipbuilding/Operations | Ballast Water, Seawater Cooling, Fuel, Fire | Corrosion Resistance (Seawater, Chemicals), Reliability | Optimized Flow, Compact Design, Material Choice | Vessel Operators, Shipyards, Marine Suppliers |
Offshore Oil & Gas | Production, Subsea Control, Utility Systems | High Pressure, Chemical Resistance, Extreme Temps | Complex Geometries, High-Strength Alloys, Reliability | Platform Operators, EPC Contractors, Subsea Eng. |
Desalination | Reverse Osmosis, Pre-treatment | Extreme Corrosion Resistance (Brine), High Pressure | Optimized Manifolds, Super Duplex/Austenitic Steels | Plant Designers, Water Treatment Suppliers |
Naval Vessels | All Critical Fluid Systems | Shock Resistance, Specific Signatures, High Reliability | Specialized Alloys, Custom Designs, On-Demand Spares | Naval Procurement, Defense Contractors |
Export to Sheets
The ability to use metal 3D printing allows engineers and procurement managers to source valve bodies optimized for specific challenges within each application, moving beyond the limitations of standard, off-the-shelf components. This is particularly crucial for upgrades, retrofits, or situations demanding unique performance characteristics.
Why Metal 3D Printing for Marine Valve Bodies? Advantages Over Traditional Methods
The adoption of metal AM for producing marine valve bodies isn’t just a novel approach; it offers tangible, compelling advantages over conventional manufacturing techniques like casting and forging, addressing key industry needs for performance, speed, and customization. These benefits resonate strongly with engineers seeking better designs and procurement managers looking for reliable, efficient sourcing solutions.
- Unparalleled Design Freedom:
- Complex Internal Geometries: AM excels at creating intricate internal channels, flow paths, and chambers that are difficult or impossible to achieve with casting (requiring complex cores) or machining (due to tool access limitations). This allows for hydrodynamically optimized designs that reduce pressure drop, minimize turbulence, prevent cavitation, and improve overall valve efficiency.
- Topology Optimization: Engineers can use software tools to optimize the valve body’s structure, placing material only where it’s needed to withstand specific loads and pressures. This leads to significantly lighter components without sacrificing strength, a critical factor in weight-sensitive marine applications.
- Part Consolidation: Multiple components previously assembled together (e.g., a valve body and adjacent fittings or sensor mounts) can potentially be consolidated into a single printed part. This reduces assembly time, eliminates potential leak points at joints, and simplifies inventory management.
- Integrated Features: Cooling channels, sensor ports, or mounting features can be directly integrated into the valve body design during the printing process.
- Accelerated Lead Times and On-Demand Production:
- No Tooling Required: Metal AM bypasses the time-consuming and costly step of creating molds or dies. Production can begin almost immediately after the digital design is finalized. This drastically reduces lead times, especially for prototypes, custom designs, or low-volume production runs.
- Rapid Prototyping: Engineers can quickly iterate on designs, printing and testing prototypes in a fraction of the time required for traditional methods. This speeds up the development cycle for new valve technologies.
- Spare Parts On-Demand: For aging vessels or equipment with obsolete parts, metal AM offers a powerful solution. Instead of searching for rare original castings or undertaking expensive reverse engineering and re-tooling, a digital scan of an existing part can be used to print a replacement on-demand. This minimizes downtime and extends the operational life of critical assets. Marine service providers and ship operators benefit immensely from this capability.
- Material Efficiency and Waste Reduction:
- Additive vs. Subtractive: AM builds parts layer by layer, using only the material necessary for the component itself (plus support structures, which are often recyclable). This contrasts sharply with subtractive machining, where a significant portion of the initial material block becomes waste chips. While powder handling requires care, the overall material utilization is generally much higher.
- Optimized Material Use: Topology optimization inherently leads to using less material for the same or better performance, contributing to cost savings and sustainability.
- Enhanced Material Properties and Selection:
- Specialized Alloys: Metal AM can effectively process a wide range of high-performance alloys crucial for marine environments, including stainless steels (316L), nickel-based alloys, copper-nickel alloys (CuNi30Mn1Fe), and super austenitic/duplex stainless steels (254SMO). Some alloys that are notoriously difficult to cast or machine can be processed more readily with AM. Met3dp, for instance, manufactures a diverse portfolio of high-quality metal powders specifically optimized for AM processes like Selective Electron Beam Melting (SEBM) and Laser Powder Bed Fusion (LPBF), ensuring optimal material properties.
- Fine-Grained Microstructures: Depending on the AM process and parameters, the rapid solidification during printing can result in fine-grained microstructures, potentially leading to improved mechanical properties like strength and fatigue resistance compared to coarse-grained castings.
- Tailored Corrosion Resistance: The ability to precisely control the build process and select optimal alloys like 254SMO allows for valve bodies with exceptional resistance to pitting, crevice corrosion, and general corrosion in aggressive chloride-rich environments like seawater.
- Supply Chain Resilience and Digital Inventory:
- Decentralized Manufacturing: Parts can potentially be printed closer to the point of need, reducing shipping costs and dependencies on long, complex global supply chains.
- Digital Warehouse: Instead of stocking physical inventory of numerous valve body variants, companies can maintain a digital library of part designs. Components can be printed as needed, reducing warehousing costs and obsolescence risks. Procurement managers gain flexibility in sourcing critical components.
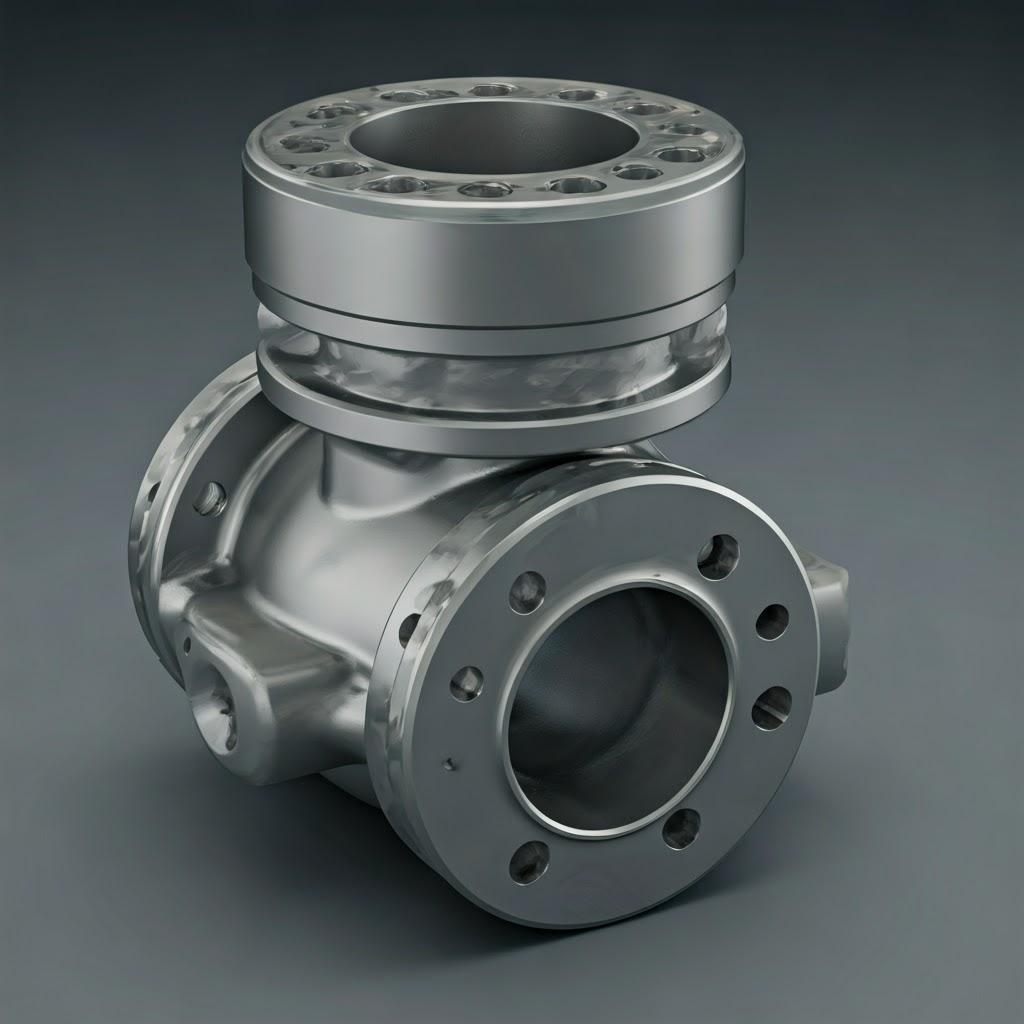
Table: Metal AM vs. Traditional Manufacturing for Marine Valve Bodies
Feature | Metal Additive Manufacturing (AM) | Traditional (Casting/Forging/Machining) | Advantage for Marine AM |
---|---|---|---|
Design Freedom | High (Complex internal channels, topology opt.) | Moderate to Low (Limited by tooling/machining) | Optimized performance, weight reduction |
Lead Time | Short (Days/Weeks – no tooling) | Long (Weeks/Months – tooling required) | Faster prototyping, on-demand spares |
Tooling Cost | None | High (Molds, dies) | Cost-effective for low/medium volume |
Material Waste | Low (Additive process, powder recycling) | High (Machining scrap, casting runners/risers) | Cost savings, sustainability |
Part Consolidation | High potential | Low potential | Reduced assembly, fewer leak points |
Material Selection | Wide range, including difficult-to-machine alloys | Established for common alloys, some limitations | Access to optimal high-performance materials |
Minimum Order Qty | Low (Economical for single parts or small batches) | High (Often required to amortize tooling costs) | Flexibility for custom parts & spares |
Inventory | Digital Warehouse potential | Requires Physical Stocking | Reduced warehousing costs, less obsolescence |
Export to Sheets
While traditional methods remain suitable for high-volume production of standard parts, metal AM provides compelling technical and logistical advantages for marine valve bodies requiring complex designs, specialized materials, rapid availability, or improved performance characteristics. Partnering with an experienced AM provider like Met3dp ensures access to the necessary technology, materials, and expertise to leverage these benefits effectively.
Selecting the Right Alloys: 316L, CuNi30Mn1Fe, 254SMO for Marine Environments
The choice of material is arguably the most critical factor determining the success and longevity of a valve body in marine service. The relentless corrosive attack of seawater, combined with operational stresses, demands materials with specific properties. Metal additive manufacturing offers the flexibility to work with advanced alloys perfectly suited for these challenges. Among the most relevant and recommended powders for marine valve bodies are 316L Stainless Steel, CuNi30Mn1Fe (Copper-Nickel), and 254SMO (Super Austenitic Stainless Steel). Understanding their unique characteristics is key for engineers designing components and procurement specialists sourcing reliable parts.
- 316L Stainless Steel (Austenitic Stainless Steel):
- Composition: Primarily Iron, with significant Chromium (16-18%), Nickel (10-14%), Molybdenum (2-3%), and low Carbon (<0.03%).
- Key Properties:
- Good General Corrosion Resistance: The chromium forms a passive oxide layer protecting against general corrosion. Molybdenum enhances resistance to pitting and crevice corrosion, particularly in chloride environments (like seawater, though less resistant than specialized alloys).
- Excellent Formability and Weldability: Relatively easy to work with, both in traditional manufacturing and AM.
- Good Strength and Ductility: Offers a solid combination of mechanical properties suitable for moderate pressure applications.
- Hygienic Properties: Often used in applications where cleanliness is important.
- Cost-Effective: Generally less expensive than more specialized nickel or copper-based alloys.
- Marine Applications: Suitable for less critical systems, freshwater circuits onboard, structural components, fuel/oil systems, or environments with lower chloride concentrations or less aggressive conditions. Often specified by marine component suppliers for standard applications.
- AM Considerations: Widely available as AM powder, well-characterized printing parameters. Good printability leading to dense parts. Post-processing like heat treatment (stress relief) may be beneficial.
- CuNi30Mn1Fe (Copper-Nickel Alloy, often C71500):
- Composition: Primarily Copper, with Nickel (approx. 30%), Manganese (approx. 1%), and Iron (approx. 1%).
- Key Properties:
- Excellent Seawater Corrosion Resistance: Highly resistant to uniform corrosion and stress corrosion cracking in seawater. The presence of iron and manganese enhances resistance to erosion corrosion caused by high flow rates.
- Superior Biofouling Resistance: Copper ions leaching from the surface naturally inhibit the settlement and growth of marine organisms (algae, barnacles), which is a major advantage for keeping seawater systems clean and efficient.
- Good Strength and Ductability: Offers robust mechanical properties suitable for pressure systems.
- Good Thermal Conductivity: Relevant for heat exchanger components sometimes integrated with valve systems.
- Marine Applications: Ideal for seawater cooling pipes, heat exchangers, condensers, firewater systems, and valve bodies directly handling raw seawater, especially where biofouling is a concern. A preferred choice for many naval and commercial marine piping systems.
- AM Considerations: Can be processed via AM, though requires careful parameter optimization due to copper’s high thermal conductivity and reflectivity (especially for laser-based systems). Powder quality is crucial. Post-processing often includes stress relief annealing.
- 254SMO (Super Austenitic Stainless Steel, e.g., UNS S31254):
- Composition: High levels of Chromium (approx. 20%), Nickel (approx. 18%), Molybdenum (approx. 6%), Nitrogen (approx. 0.2%), and low Carbon.
- Key Properties:
- Exceptional Pitting and Crevice Corrosion Resistance: The high Molybdenum, Chromium, and Nitrogen content provides outstanding resistance in aggressive chloride environments like warm seawater, brackish water, and desalination brine. Its Pitting Resistance Equivalent Number (PREN) is typically >42.5, significantly higher than 316L (PREN ≈ 25).
- High Strength: Stronger than standard austenitic steels like 316L.
- Good Ductility and Toughness: Retains good mechanical properties even at low temperatures.
- Good Weldability: Can be welded using appropriate techniques.
- Marine Applications: High-performance choice for critical applications involving aggressive seawater, chlorinated seawater (e.g., after BWMS treatment), desalination plant components (high-pressure side), offshore platform process systems handling corrosive fluids, and subsea equipment. Specified when 316L is insufficient. Wholesale distributors often stock components made from this grade for demanding projects.
- AM Considerations: Successfully processed via AM, yields high-density parts with properties comparable to wrought material. Requires optimized parameters and potentially specific heat treatments (solution annealing) to ensure optimal corrosion resistance and mechanical properties. Powder producers like Met3dp focus on providing high-quality, gas-atomized 254SMO powders with controlled chemistry and particle size distribution, crucial for achieving reliable printing results. Their advanced powder making system, employing technologies like gas atomization with unique nozzle designs, ensures high sphericity and flowability, critical for consistent layer deposition in powder bed fusion processes.
Table: Comparison of Recommended Alloys for Marine AM Valve Bodies
Property | 316L Stainless Steel | CuNi30Mn1Fe | 254SMO Super Austenitic SS | Significance for Marine Valves |
---|---|---|---|---|
Primary Elements | Fe, Cr, Ni, Mo | Cu, Ni, Mn, Fe | Fe, Cr, Ni, Mo, N | Determines fundamental characteristics |
General Corrosion (SW) | Good | Excellent | Excellent | Resistance to overall metal loss |
Pitting/Crevice Corr. (SW) | Moderate | Good | Exceptional | Resistance to localized attack in seawater |
Biofouling Resistance | Low | Excellent | Low | Prevents marine growth blockage/inefficiency |
Strength | Good | Good | High | Ability to withstand pressure/stress |
PREN (Typical) | ~25 | N/A (Different mechanism) | >42.5 | Indicator of pitting resistance in chlorides |
Cost | Lower | Higher | Highest | Material expense contribution |
Primary Use Case | General purpose, less harsh | Seawater handling, biofouling | Aggressive seawater, desalination | Application-specific suitability |
AM Powder Availability | High | Moderate | Moderate to High | Ease of sourcing for printing |
Export to Sheets
Selecting the optimal material requires a thorough analysis of the specific operating environment (temperature, pressure, flow rate, water chemistry, presence of pollutants, biofouling risk) and the performance requirements of the valve body. Consulting with material experts and experienced AM service providers like Met3dp, who possess deep knowledge of both the materials and the printing processes, is crucial for making the right choice and ensuring the long-term reliability of critical marine components. Met3dp’s commitment to producing high-quality metal powders, including innovative alloys tailored for demanding sectors, positions them as a valuable partner for marine engineering challenges.
Design for Additive Manufacturing (DfAM): Optimizing Valve Bodies for Printing
Simply replicating a traditionally designed valve body using metal additive manufacturing often fails to unlock the technology’s full potential and can even introduce new challenges. To truly leverage the benefits of AM – enhanced performance, reduced weight, faster production – engineers must embrace Design for Additive Manufacturing (DfAM) principles. DfAM involves rethinking the component’s design from the ground up, considering the unique capabilities and constraints of the chosen AM process (like Laser Powder Bed Fusion – LPBF or Selective Electron Beam Melting – SEBM). Optimizing valve bodies for AM specifically for marine applications requires careful attention to several key areas:
- Topology Optimization and Lattice Structures:
- Goal: Reduce weight and material usage while maintaining or increasing structural integrity under pressure and operational loads.
- How: Use specialized software to analyze load paths and remove material from non-critical areas. Replace solid sections with internal lattice structures where appropriate.
- Marine Benefit: Lighter components reduce overall vessel weight, improving fuel efficiency or allowing for increased payload. Reduced material usage lowers costs, especially with expensive marine-grade alloys. Efficient load-bearing structures ensure reliability under demanding sea conditions.
- Internal Channel and Flow Path Optimization:
- Goal: Improve fluid dynamics, reduce pressure drop, minimize turbulence, and prevent erosion or cavitation.
- How: AM allows for smooth, curved internal channels and complex manifold designs impossible with drilling or casting. Flow simulations can guide the design of optimal pathways. Self-supporting channel shapes (e.g., teardrop or diamond cross-sections) can minimize the need for internal supports that are difficult to remove.
- Marine Benefit: Enhanced valve efficiency contributes to better system performance (e.g., cooling, ballast management). Reduced erosion extends the valve body’s service life in abrasive or high-velocity fluid conditions.
- Support Structure Minimization and Optimization:
- Goal: Reduce printing time, material waste, and post-processing effort associated with removing support structures.
- How: Orient the part strategically on the build plate. Design features with self-supporting angles (typically >45 degrees from the horizontal). Use easily removable support structures where unavoidable, particularly avoiding them on critical internal or sealing surfaces. Integrate features that serve as inherent support.
- Marine Benefit: Faster production cycles, lower manufacturing costs, and reduced risk of damaging the part during support removal. Ensures internal passages remain unobstructed.
- Wall Thickness and Feature Size Considerations:
- Goal: Ensure structural integrity, printability, and proper heat dissipation during the build process.
- How: Adhere to minimum printable wall thicknesses and feature sizes specific to the AM machine and material (e.g., typically >0.4-0.5 mm for LPBF). Maintain consistent wall thickness where possible to avoid thermal stress concentration. Thicken areas subject to high stress or pressure.
- Marine Benefit: Prevents print failures, ensures the valve body can withstand operating pressures, and improves overall part quality and consistency.
- Part Consolidation and Feature Integration:
- Goal: Reduce assembly complexity, potential leak points, and overall part count.
- How: Redesign adjacent components (flanges, sensor ports, mounting brackets) to be printed as a single, monolithic valve body unit. Integrate internal features like flow straighteners or mixing chambers.
- Marine Benefit: Simplifies procurement and inventory for marine suppliers and end-users. Increases system reliability by eliminating joints and seals. Reduces overall system weight and footprint.
- Designing for Post-Processing:
- Goal: Ensure critical surfaces can be easily accessed for required finishing operations.
- How: Add extra material (machining stock) to surfaces requiring tight tolerances or specific finishes (e.g., sealing faces, flange connections). Ensure internal channels are accessible for cleaning, inspection, and potential polishing.
- Marine Benefit: Guarantees the valve body meets functional requirements for sealing, connection, and flow after all manufacturing steps are completed.
Table: Key DfAM Considerations for Marine Valve Bodies
DfAM Principle | Objective | AM-Enabled Technique | Benefit for Marine Valve Body |
---|---|---|---|
Weight Reduction | Minimize mass, save material | Topology Optimization, Lattice Structures | Fuel efficiency, lower cost (high-value alloys) |
Flow Efficiency | Reduce pressure drop, minimize turbulence | Smooth/Curved Internal Channels, Optimized Paths | Better system performance, reduced erosion |
Printability | Minimize supports, ensure build success | Part Orientation, Self-Supporting Angles | Faster printing, lower cost, easier finishing |
Structural Integrity | Withstand pressure & loads | Minimum Wall Thickness Rules, Feature Sizing | Reliability, safety, longevity |
System Simplification | Reduce part count, assembly, leak points | Part Consolidation, Integrated Features | Easier procurement, higher reliability |
Functionality | Meet performance specs post-printing | Designing for Post-Processing (Machining Stock) | Guarantees fit, sealing, and function |
Export to Sheets
Applying DfAM effectively requires expertise not just in design principles but also in the specific nuances of different metal AM printing methods. Collaborating with an experienced AM service provider like Met3dp, who understands the interplay between design, materials (like their high-quality 316L, CuNi alloys, and super austenitic powders), and machine capabilities (including their industry-leading print volume and accuracy), is crucial for developing truly optimized marine valve bodies. Their engineering teams can assist customers in adapting or redesigning components to maximize the advantages offered by additive manufacturing.
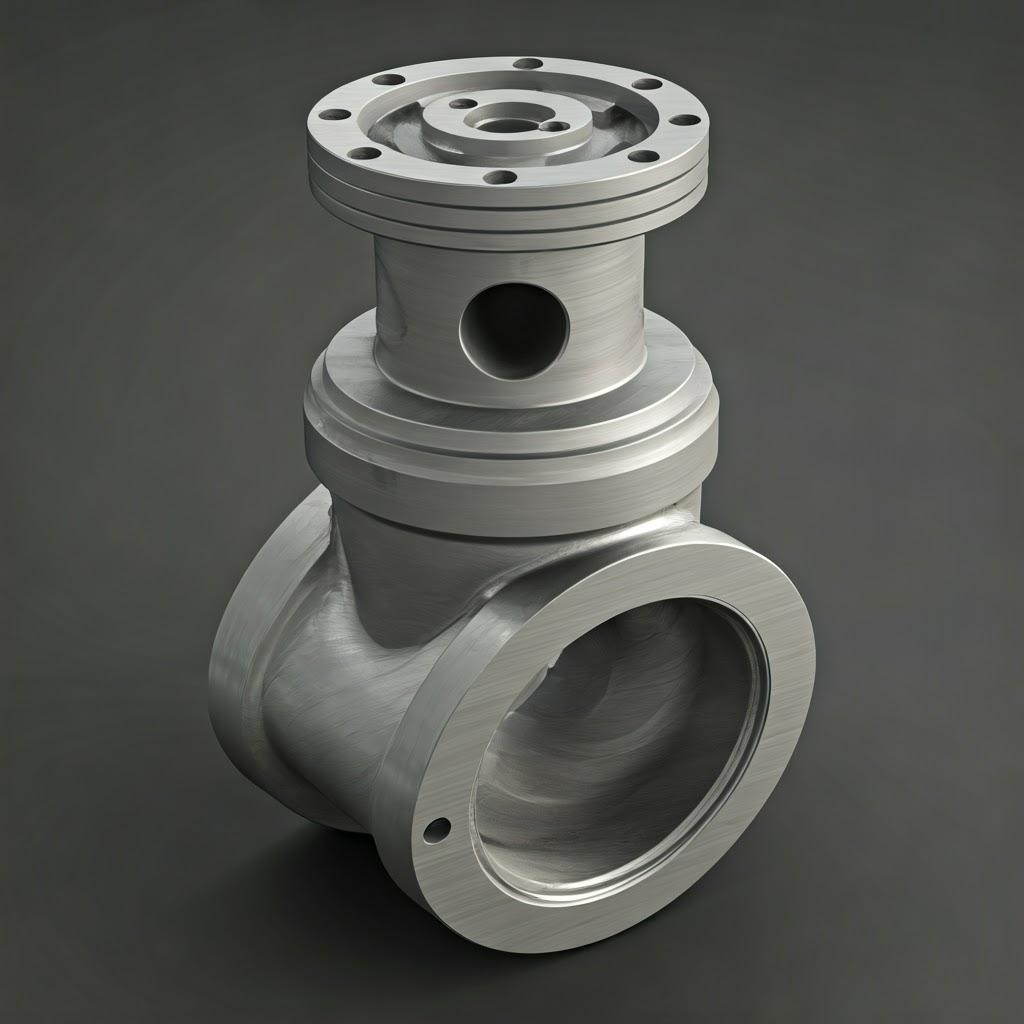
Precision Matters: Tolerances, Surface Finish, and Dimensional Accuracy in AM Valve Bodies
While metal AM offers significant design freedom, understanding the achievable levels of precision – tolerances, surface finish, and dimensional accuracy – is critical for functional components like valve bodies, especially for sealing surfaces and mating interfaces. Engineers and procurement managers must have realistic expectations about the as-printed state and factor in post-processing requirements.
- Dimensional Accuracy:
- Definition: How closely the final printed part conforms to the dimensions specified in the CAD model.
- Typical Values: For powder bed fusion processes (LPBF, SEBM), typical dimensional accuracy is often in the range of ±0.1 mm to ±0.2 mm or ±0.1% to ±0.2% of the dimension, whichever is greater. However, this can vary significantly based on:
- Part size and geometry (larger parts may exhibit more distortion)
- Material properties (thermal expansion, shrinkage)
- Machine calibration and condition
- Build parameters (layer thickness, energy input)
- Thermal stresses during the build and cool-down phases
- Marine Relevance: Critical for ensuring proper fit with mating pipes (flanges), actuators, and internal valve components. While general body dimensions might be acceptable as-printed, critical interfaces often require tighter control.
- Surface Finish (Roughness):
- Definition: The measure of the fine-scale irregularities on a surface, often expressed as Ra (average roughness).
- Typical As-Printed Values:
- Top Surfaces: Generally smoother, potentially Ra 5-15 µm.
- Vertical Walls: Moderate roughness, often Ra 8-20 µm, influenced by layer lines.
- Down-Facing/Supported Surfaces: Typically the roughest, potentially Ra 15-30 µm or more, due to support contact points or the nature of powder fusion on down-facing slopes.
- Internal Channels: Roughness depends heavily on orientation, diameter, and whether supports were needed. Can be challenging to achieve smooth finishes without post-processing.
- Factors Influencing Roughness: Powder particle size distribution (finer powders can yield smoother finishes), layer thickness (thinner layers generally improve finish), laser/beam parameters, and part orientation.
- Marine Relevance: Crucial for sealing surfaces (gasket faces, valve seats) where a smooth finish (often requiring Ra < 1.6 µm or better) is necessary to prevent leaks. Rough internal surfaces can increase friction losses, potentially trap contaminants, and even affect corrosion resistance in some cases.
- Tolerances:
- Definition: The permissible range of variation for a specific dimension.
- Achievability: While general dimensional accuracy might be ±0.1-0.2 mm, achieving tighter tolerances (e.g., ±0.025 mm to ±0.05 mm) on specific features (like seal grooves, bearing bores, flange faces) typically requires post-machining.
- DfAM Consideration: Designs must account for this by adding machining stock (e.g., 0.5 mm to 1.5 mm) to critical surfaces in the AM design file.
- Marine Relevance: Essential for interchangeability of parts, proper sealing under pressure, and correct assembly with other system components. Procurement specifications often mandate specific tolerances for critical features.
Table: Typical Precision Parameters in Metal AM (Powder Bed Fusion)
Parameter | Typical As-Printed Range | Influencing Factors | Post-Processing Potential | Relevance to Marine Valves |
---|---|---|---|---|
Dimensional Accuracy | ±0.1 to ±0.2 mm / ±0.1-0.2% | Part Size, Material, Machine, Parameters, Thermal Stress | Machining for high accuracy | Fit with pipes, actuators, internal components |
Surface Finish (Ra) | 5 µm – 30+ µm | Surface Orientation, Layer Height, Powder Size, Supports | Machining, Polishing, Blasting | Sealing surfaces, flow efficiency, corrosion |
Tolerances | Limited as-printed | (Same as Accuracy) | CNC Machining required for tight Tol. | Interchangeability, sealing, assembly |
Export to Sheets
It’s important to note that providers like Met3dp, with their focus on industry-leading accuracy and reliability, invest heavily in machine calibration, process control, and quality assurance measures to achieve the best possible precision in the as-printed state. However, for the demanding requirements of many marine valve applications, a combination of precise AM printing followed by targeted post-machining is often the most effective strategy to meet all dimensional and surface finish specifications. Clear communication between the design engineers, procurement team, and the AM service provider regarding critical dimensions and tolerances is essential.
Post-Processing Pathways: Finishing Touches for Optimal Performance
An as-printed metal AM part is rarely ready for immediate deployment, especially for critical applications like marine valve bodies. Post-processing steps are almost always necessary to relieve internal stresses, remove support structures, achieve required tolerances and surface finishes, and ensure the material possesses the desired mechanical and corrosion properties. Understanding these common pathways is crucial for planning production timelines and costs.
- Stress Relief / Heat Treatment:
- Purpose: To relieve internal stresses built up during the rapid heating and cooling cycles of the AM process. This prevents distortion or cracking later and stabilizes the part’s dimensions. Also used to achieve specific metallurgical phases and properties (e.g., strength, ductility, corrosion resistance).
- Methods:
- Stress Relief: Heating the part to a moderate temperature (below transformation points) and holding it, followed by slow cooling. Common for many alloys.
- Annealing/Solution Annealing: Heating to higher temperatures to dissolve precipitates, homogenize the microstructure, and improve ductility or corrosion resistance (e.g., crucial for optimizing 254SMO’s corrosion performance). Requires specific temperature profiles and cooling rates (e.g., water quenching).
- Aging/Precipitation Hardening: Used for specific alloys (not typically the primary marine ones discussed, but relevant for others) to increase strength.
- Considerations: Must be performed in controlled atmosphere furnaces (vacuum or inert gas) to prevent oxidation, especially for reactive alloys. Heat treatment parameters are alloy-specific and critical for performance.
- Support Structure Removal:
- Purpose: To remove the temporary structures used to anchor the part to the build plate and support overhanging features during printing.
- Methods: Can range from manual break-off (for easily accessible, lightly sintered supports) to cutting, grinding, or CNC machining. Wire EDM is sometimes used for intricate or hard-to-reach supports. Access to internal channel supports can be particularly challenging.
- Considerations: Must be done carefully to avoid damaging the part surface. DfAM plays a huge role in minimizing the need for difficult support removal.
- CNC Machining:
- Purpose: To achieve tight dimensional tolerances, specific geometric features (like O-ring grooves or threaded holes), and smooth surface finishes on critical areas.
- Applications for Valve Bodies: Machining flange faces for flatness and finish, boring internal diameters for valve seats or pistons, machining sealing surfaces, threading connection ports.
- Considerations: Requires accurate fixturing of the potentially complex AM part. Sufficient machining stock must be included in the DfAM stage.
- Surface Finishing:
- Purpose: To improve surface smoothness (reduce Ra), remove minor imperfections, enhance aesthetics, or prepare the surface for coating.
- Methods:
- Abrasive Blasting (Sandblasting, Bead Blasting): Provides a uniform matte finish, removes loose powder particles.
- Tumbling/Vibratory Finishing: Uses media to smooth surfaces and edges, suitable for batches of smaller parts.
- Polishing: Mechanical or electro-polishing to achieve very smooth, mirror-like finishes, sometimes required for specific flow paths or sealing areas.
- Micro-machining/Abrasive Flow Machining (AFM): Can be used to improve the finish of internal channels.
- Considerations: Choice depends on the required Ra value, geometry accessibility, and cost.
- Cleaning and Inspection:
- Purpose: Remove any remaining loose powder, machining fluids, or contaminants. Verify dimensional accuracy, surface integrity, and check for defects.
- Methods: Ultrasonic cleaning, visual inspection, Coordinate Measuring Machine (CMM) checks, Non-Destructive Testing (NDT) like X-ray or CT scanning (especially for critical pressure-containing parts to check for internal porosity).
- Considerations: Essential quality assurance steps before deployment.
Table: Common Post-Processing Steps for AM Marine Valve Bodies
Post-Processing Step | Purpose | Common Methods | Key Considerations |
---|---|---|---|
Heat Treatment | Relieve stress, optimize material properties (corrosion, strength) | Stress Relief, Annealing, Solution Annealing | Alloy-specific parameters, controlled atmosphere |
Support Removal | Detach part from build plate, remove overhang supports | Manual Break-off, Machining, Grinding, Wire EDM | Access (esp. internal), avoid part damage |
CNC Machining | Achieve tight tolerances, critical surface finishes, features | Milling, Turning, Drilling, Tapping | Fixturing, machining stock allowance (DfAM) |
Surface Finishing | Improve smoothness (Ra), aesthetics, prepare for coating | Blasting, Tumbling, Polishing, AFM | Required Ra, accessibility, cost |
Cleaning & Inspection | Remove contaminants, verify dimensions, check for defects | Ultrasonic Cleaning, CMM, Visual, NDT (X-ray) | Final QA, ensuring fitness for service |
Export to Sheets
The extent and sequence of post-processing depend heavily on the valve body’s design complexity, material choice, and application requirements. Procurement managers should factor these steps into overall lead time and cost calculations when sourcing AM components. Working with a full-service provider like Met3dp, who can manage or coordinate these necessary post-processing steps, ensures a streamlined workflow and guarantees the final part meets all specifications.
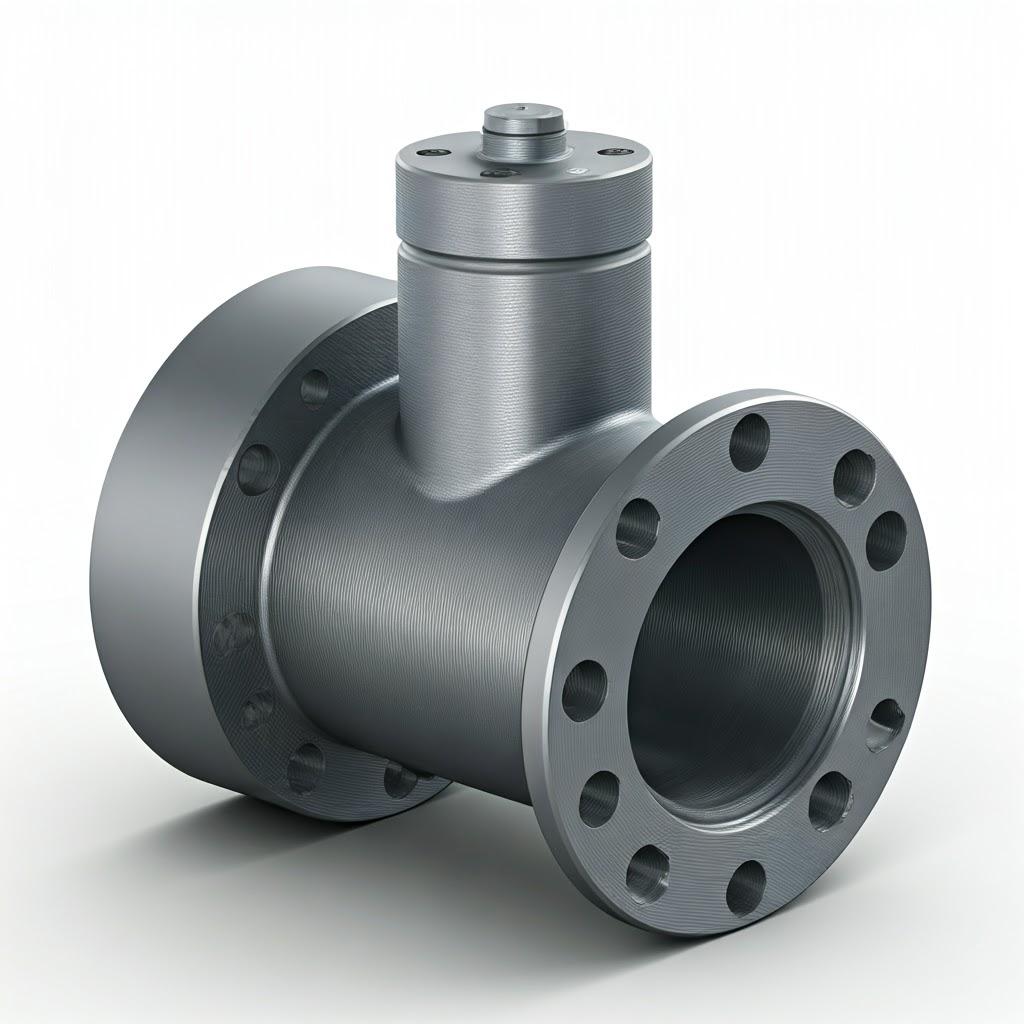
Navigating Challenges in AM Valve Body Production: Solutions and Best Practices
While metal additive manufacturing offers significant advantages for producing marine valve bodies, it’s not without its potential challenges. Recognizing these hurdles and implementing best practices is essential for ensuring consistent quality, reliability, and performance. Experienced AM providers have developed strategies to mitigate these common issues.
- Residual Stress and Warping:
- Challenge: The rapid heating/cooling cycles can induce internal stresses, potentially causing the part to warp during or after the build, or even crack. This is more pronounced in large parts or complex geometries.
- Solutions:
- Optimized Build Strategy: Careful selection of scan patterns, layer times, and thermal management during the build.
- Robust Support Structures: Well-designed supports help anchor the part and manage heat dissipation.
- Appropriate Heat Treatment: Post-build stress relief cycles are crucial for stabilizing the part.
- Simulation: Thermal simulation tools can predict stress accumulation and inform design/build strategy adjustments.
- Porosity:
- Challenge: Small voids or pores can form within the printed material due to incomplete fusion between powder particles, trapped gas, or keyholing phenomena (vapor depression instability). Porosity can compromise mechanical strength, fatigue life, and pressure integrity – critical for valve bodies.
- Solutions:
- Optimized Print Parameters: Fine-tuning laser/electron beam power, scan speed, layer thickness, and focus for the specific material to achieve >99.5% density (often >99.9% is achievable).
- High-Quality Powder: Using powders with controlled particle size distribution, morphology (high sphericity), and low gas content, like those produced by Met3dp using advanced gas atomization and PREP technologies. Consistent powder quality is paramount.
- Process Monitoring: In-situ monitoring systems can detect potential anomalies during the build.
- Hot Isostatic Pressing (HIP): A post-processing step involving high temperature and pressure to close internal voids. Often required for critical aerospace or subsea components, adds cost and time but guarantees maximum density.
- Support Removal Difficulties:
- Challenge: Supports in complex internal channels or hard-to-reach areas can be very difficult or impossible to remove completely, potentially obstructing flow or acting as initiation sites for corrosion.
- Solutions:
- DfAM Focus: Designing self-supporting internal channels and minimizing the need for internal supports is the best approach.
- Optimized Support Design: Using support structures designed for easier removal (e.g., specific geometries, lower density supports).
- Advanced Removal Techniques: Considering chemical etching (for specific material combinations) or Abrasive Flow Machining (AFM) for internal channel finishing, although these add complexity.
- Inspection: Borescope inspection or CT scanning to verify complete removal from critical passages.
- Achieving Tolerances and Surface Finish:
- Challenge: As discussed previously, as-printed parts rarely meet the tight tolerances and smooth surface finishes required for sealing faces or dynamic components without secondary machining.
- Solutions:
- Integrated Workflow: Planning for post-machining from the DfAM stage by including machining stock.
- Precise Post-Processing: Utilizing high-precision CNC machining and appropriate surface finishing techniques.
- Metrology: Rigorous CMM inspection to verify final dimensions and tolerances.
- Material Property Validation and Consistency:
- Challenge: Ensuring that the mechanical properties (strength, ductility, hardness) and corrosion resistance of the AM part consistently meet the specifications for the chosen alloy and application requirements. Properties can be influenced by build parameters, orientation, and heat treatment.
- Solutions:
- Standardized Procedures: Following established ASTM or ISO standards for AM processes and testing.
- Parameter Development: Thorough validation of printing parameters for each specific alloy.
- Witness Coupons: Printing test coupons alongside the main part for destructive testing (tensile tests, hardness, microstructure analysis).
- Material Certification: Using certified powders and providing material test reports (MTRs) with delivered parts. Companies like Met3dp emphasize material quality and provide comprehensive solutions including application development services.
- Quality Assurance and Certification:
- Challenge: Demonstrating consistent quality and process control, especially for critical marine applications often requiring class society approvals (e.g., DNV, ABS, Lloyd’s Register).
- Solutions:
- Robust Quality Management System (QMS): Implementing ISO 9001 or industry-specific standards (e.g., AS9100 for aerospace which shares some rigor).
- Traceability: Maintaining full traceability of powder batches, machine parameters, and post-processing steps for each part.
- Non-Destructive Testing (NDT): Employing methods like CT scanning, X-ray, or dye penetrant inspection to verify integrity.
- Collaboration with Classification Societies: Working proactively with marine classification societies to qualify materials, processes, and components for specific applications.
Navigating these challenges requires a combination of advanced technology, material science expertise, rigorous process control, and a strong focus on quality assurance. Partnering with a knowledgeable and experienced metal AM provider is the most effective way for marine engineers and procurement managers to mitigate risks and successfully implement AM for demanding valve body applications. Met3dp’s commitment to reliability, accuracy, and comprehensive solutions, backed by their advanced powder manufacturing and printing capabilities, positions them well to address these industry challenges.
Choosing Your Partner: Selecting a Metal AM Service Provider for Marine Components
The success of implementing metal additive manufacturing for critical marine components like valve bodies hinges significantly on selecting the right manufacturing partner. Not all AM service providers possess the specific expertise, equipment, materials knowledge, and quality systems required for the demanding maritime environment. Engineers and procurement managers sourcing these components should evaluate potential partners based on a rigorous set of criteria:
- Marine Alloy Expertise:
- Requirement: Demonstrated experience and validated processes for printing marine-grade alloys like 316L, Copper-Nickel (CuNi30Mn1Fe), Super Austenitic/Duplex Stainless Steels (254SMO, Duplex), and potentially Nickel alloys or Titanium for specialized applications.
- Evaluation: Ask for case studies, material datasheets for AM parts, and evidence of successful prints with relevant materials. Verify their understanding of the unique challenges each alloy presents during printing and post-processing (e.g., thermal properties of CuNi, heat treatment for 254SMO).
- Quality Management System (QMS) and Certifications:
- Requirement: A robust QMS, ideally certified to ISO 9001 or a comparable standard. For certain critical applications, experience working towards or achieving certifications relevant to marine or offshore industries (e.g., familiarity with requirements from DNV, ABS, Lloyd’s Register) is a significant advantage.
- Evaluation: Request QMS certification details. Inquire about their experience with classification society requirements and their process for part qualification if needed. Look for evidence of strong process control and documentation practices.
- Technological Capability and Capacity:
- Requirement: Access to appropriate AM technologies (e.g., LPBF, SEBM) suitable for the chosen materials and part complexity. Sufficient build volume for the required valve body sizes and capacity to meet project timelines. State-of-the-art equipment ensures higher accuracy and reliability.
- Evaluation: Understand their machine park, build envelope sizes, and typical lead times. Assess their maintenance and calibration procedures. Met3dp, for example, prides itself on printers delivering industry-leading print volume, accuracy, and reliability.
- Material Quality and Traceability:
- Requirement: Use of high-quality, certified metal powders specifically designed for AM, with controlled chemistry and particle characteristics. Full traceability from raw powder batch to finished part is essential.
- Evaluation: Inquire about their powder sourcing and quality control procedures. Do they manufacture their own powders, like Met3dp with its advanced gas atomization and PREP systems, ensuring tight control over quality? Ask for material test reports (MTRs) and traceability documentation procedures.
- Design for Additive Manufacturing (DfAM) Support:
- Requirement: Engineering expertise to assist customers in optimizing designs for AM, minimizing supports, reducing weight, and leveraging the unique advantages of the technology.
- Evaluation: Discuss their DfAM capabilities and willingness to collaborate on design optimization. Review examples of how they have helped other clients improve their components through DfAM.
- Post-Processing Capabilities:
- Requirement: Ability to perform or manage necessary post-processing steps including heat treatment (in controlled atmospheres), support removal, precision CNC machining, surface finishing, and cleaning to meet all specifications.
- Evaluation: Assess their in-house capabilities versus their network of trusted subcontractors. Ensure they can deliver a finished part meeting all dimensional, surface, and material property requirements.
- Inspection and Testing:
- Requirement: Comprehensive inspection capabilities, including dimensional metrology (CMM), surface roughness testing, and Non-Destructive Testing (NDT) methods like X-ray, CT scanning, or dye penetrant testing to ensure part integrity, especially for pressure-bearing components.
- Evaluation: Understand their standard QA/QC procedures and available NDT methods. Confirm their ability to provide necessary inspection reports and certifications.
- Track Record and Reputation:
- Requirement: A proven history of successfully delivering high-quality metal AM parts for demanding industries (marine, aerospace, medical, oil & gas). Positive customer references and case studies.
- Evaluation: Ask for relevant project examples and references. Check their industry standing and client feedback. Exploring a potential partner’s background, like learning more about Met3dp, can provide insight into their experience, values, and commitment to innovation and quality.
Table: Key Criteria for Selecting a Marine Metal AM Partner
Criteria | Why It Matters for Marine Valve Bodies | Evaluation Points |
---|---|---|
Marine Alloy Expertise | Ensures correct processing for corrosion & mechanical needs | Experience with 316L, CuNi, 254SMO; datasheets, case studies |
QMS & Certifications | Guarantees consistent quality & process control | ISO 9001; familiarity with DNV/ABS; QA procedures |
Technology & Capacity | Determines feasibility, accuracy, speed, part size limits | Machine type (LPBF/SEBM), build volume, calibration, lead times |
Material Quality | Directly impacts final part properties & reliability | Powder source (in-house like Met3dp?), QC, traceability, MTRs |
DfAM Support | Optimizes design for performance, cost, printability | Engineering resources, collaborative approach, optimization examples |
Post-Processing | Ensures finished part meets all functional requirements | In-house vs. managed services (heat treat, machining, finishing) |
Inspection & Testing | Verifies integrity, dimensions, absence of defects | CMM, NDT capabilities (X-ray/CT), reporting |
Track Record | Demonstrates reliability & experience in demanding sectors | Marine/offshore projects, client references, industry reputation |
Export to Sheets
Choosing a partner isn’t just about finding a supplier; it’s about establishing a collaborative relationship with an expert who understands the unique demands of the marine industry. A provider like Met3dp, offering comprehensive solutions spanning printers, advanced metal powders, and application development services, embodies the type of partnership needed to successfully leverage AM for critical components.
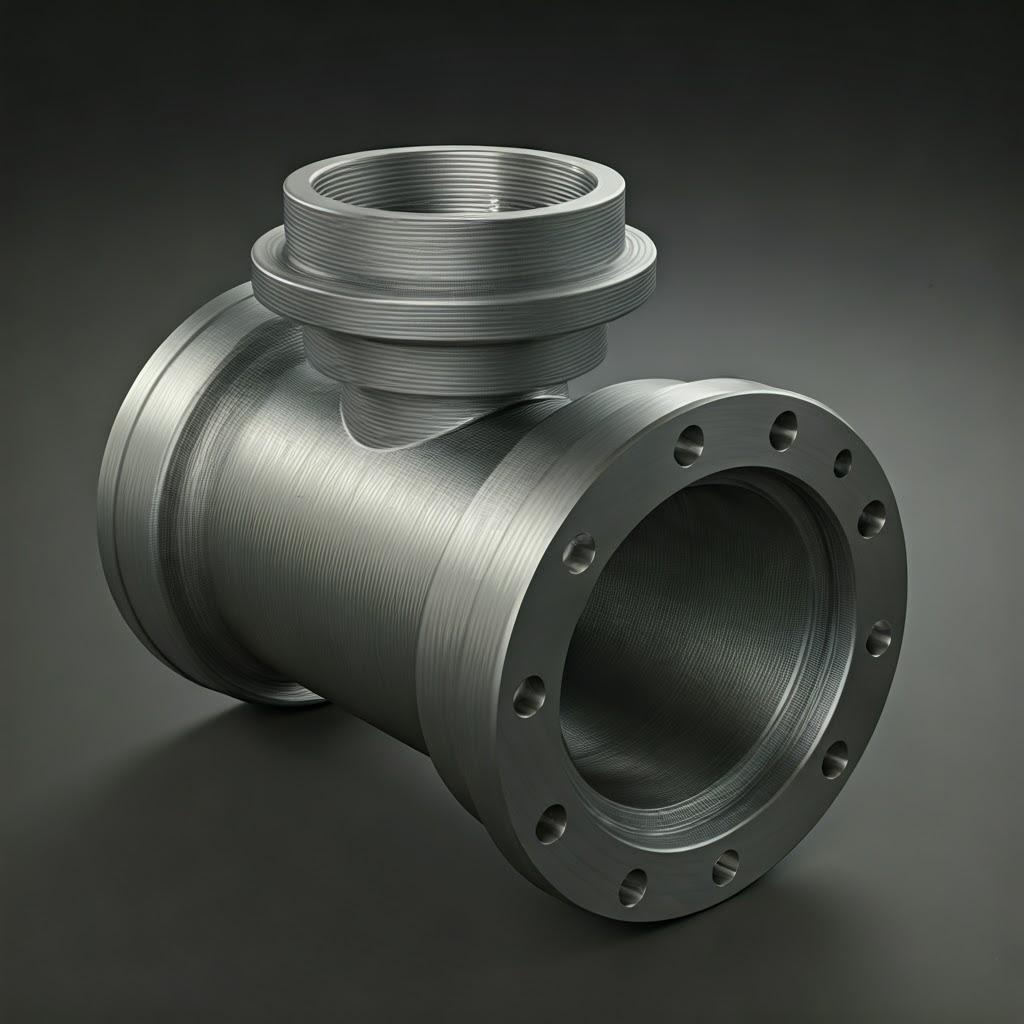
Understanding Costs and Lead Times for AM Marine Valve Bodies
One of the primary considerations for procurement managers and engineers evaluating manufacturing methods is the associated cost and lead time. Metal additive manufacturing presents a different paradigm compared to traditional casting or forging, particularly impacting these two factors.
Cost Factors in Metal AM Valve Bodies:
The cost of producing a valve body via metal AM is influenced by several interconnected variables:
- Material Type and Volume: High-performance marine alloys like 254SMO or CuNi30Mn1Fe are inherently more expensive than standard 316L stainless steel. The sheer volume of material used in the part (after DfAM optimization) is a primary cost driver. Powder quality and sourcing also play a role.
- Part Complexity and Size: While AM handles complexity well, highly intricate designs may require more support structures and longer print times. Larger parts occupy more machine time and use more material, increasing costs. The overall dimensions impact how many parts can fit in a single build.
- Build Time: Determined by the part volume, layer height, and scanning parameters. Longer build times mean higher machine operating costs allocated to the part.
- Support Structures: The volume of material used for supports and the time/effort required for their removal add to the cost. Effective DfAM aims to minimize this.
- Post-Processing Requirements: Each step adds cost:
- Heat Treatment: Furnace time, energy, controlled atmosphere usage.
- Machining: Setup time, machine time, complexity of features.
- Surface Finishing: Labor, consumables, specialized equipment (e.g., polishing, AFM).
- Non-Destructive Testing (NDT): Methods like CT scanning add significant cost but may be required for critical components to ensure internal integrity.
- Quantity: While AM avoids tooling costs, there are still setup costs per build. Unit costs tend to decrease slightly with larger batch sizes, but the effect is less dramatic than with traditional mass production methods where tooling amortization dominates low-volume costs.
- Quality Assurance & Documentation: Rigorous inspection and detailed documentation packages add overhead but are necessary for critical applications.
Lead Times for AM vs. Traditional Methods:
This is often where AM demonstrates a compelling advantage, especially for certain scenarios:
- Prototyping: AM: Days to 1-2 weeks. Traditional (casting/forging): Weeks to months (dominated by tooling creation).
- Low-Volume Production / Custom Parts: AM: Typically 1-4 weeks (depending on complexity, post-processing, queue times). Traditional: Months (tooling lead time is the main bottleneck).
- Spare Parts (On-Demand): AM: Can be produced in 1-3 weeks from a digital file, crucial for minimizing downtime (MRO – Maintenance, Repair, Operations). Traditional: Can take months if tooling needs recreating or the part is obsolete; minimum order quantities may apply.
- High-Volume Production: Traditional casting/forging often becomes more cost-effective per part and can achieve faster per-part production rates after the initial tooling phase. AM lead times are less sensitive to volume but are limited by machine capacity.
Table: Cost & Lead Time Considerations – AM vs. Traditional
Factor | Metal Additive Manufacturing | Traditional (Casting/Forging + Machining) | Key Takeaway for Marine Valves |
---|---|---|---|
Tooling Cost | None | High (Molds, Dies) | AM cost-effective for low volume, prototypes, spares |
Unit Cost (Low Vol) | Potentially lower (no tooling amortization) | High (dominated by tooling cost) | AM advantage for custom/urgent needs |
Unit Cost (High Vol) | Higher (machine time, material focus) | Lower (mass production efficiencies) | Traditional often better for mass-produced std parts |
Material Cost | Significant driver (optimization is key) | Significant driver | High-performance alloys costly in both methods |
Complexity Cost | Moderate impact (handled well by process) | High impact (complex tooling, machining) | AM enables complex designs economically |
Lead Time (Proto) | Very Fast (Days/Weeks) | Slow (Weeks/Months) | AM ideal for rapid iteration |
Lead Time (Prod) | Fast for Low Vol (Weeks) | Slow initial (Months), then faster per part | AM superior for urgent, low-volume, spare parts |
Waste | Lower (additive process) | Higher (machining, runners/risers) | AM generally more material-efficient |
Export to Sheets
In summary, while the per-part cost for a simple, high-volume valve body might be lower with traditional casting, metal AM offers significant cost and lead time advantages for complex designs, specialized materials, prototypes, low-to-medium volume production runs, and crucially, the rapid production of spare parts for marine assets. Obtaining a specific quote from an AM provider like Met3dp, based on a detailed CAD model and specifications, is the best way to assess the cost and timeline for a particular marine valve body project.
Frequently Asked Questions (FAQ) about Metal AM Valve Bodies for Marine Use
Here are answers to some common questions engineers and procurement specialists have about using metal 3D printing for marine valve bodies:
- Q1: What kind of pressure ratings can metal AM valve bodies handle?
- A: The pressure rating of an AM valve body is primarily determined by its design (wall thickness, geometry), the chosen material’s strength (yield and tensile strength at operating temperature), and the quality of the manufacturing process (ensuring full density and absence of critical defects). When designed, printed, and post-processed correctly (potentially including HIP for critical applications), metal AM valve bodies made from alloys like 316L, 254SMO, or high-strength steels can achieve pressure ratings comparable or even superior to their traditionally manufactured counterparts meeting relevant ASME or ISO standards. The key is proper engineering validation, potentially supported by burst testing and finite element analysis (FEA), specific to the final product.
- Q2: Are metal 3D printed valve bodies certified or approved by marine classification societies (like DNV, ABS)?
- A: Certification is typically application-specific and involves qualifying the entire process: the material, the AM machine, the printing parameters, post-processing steps, and the specific component design. While classification societies are increasingly developing guidelines and frameworks for additive manufacturing, obtaining class approval for a critical valve body often requires a dedicated qualification program undertaken collaboratively by the end-user, the AM service provider, and the classification society. Experienced providers like Met3dp understand these requirements and can support customers through the necessary testing, documentation, and qualification processes required to gain certification for specific marine applications. It’s not automatic; it requires deliberate effort.
- Q3: How does the cost of a metal AM valve body compare directly to a cast or forged equivalent?
- A: It depends heavily on the specifics. For a standard, simple valve body produced in high volumes, traditional casting is often cheaper per part due to economies of scale after amortizing tooling costs. However, metal AM becomes highly competitive or even more cost-effective when:
- Tooling costs are prohibitive (low volume, prototypes).
- The design is complex (difficult/expensive to cast or machine).
- Lead time is critical (AM avoids tooling delays).
- Specialized alloys are required that are difficult to cast/forge.
- On-demand spare parts are needed (eliminating inventory and long waits for obsolete parts).
- DfAM allows for significant weight reduction or part consolidation, providing system-level savings. Therefore, a direct cost comparison needs to consider volume, complexity, material, lead time sensitivity, and the total cost of ownership, including potential downtime savings with AM spares.
- A: It depends heavily on the specifics. For a standard, simple valve body produced in high volumes, traditional casting is often cheaper per part due to economies of scale after amortizing tooling costs. However, metal AM becomes highly competitive or even more cost-effective when:
Conclusion: Setting Sail with Advanced Valve Body Manufacturing
The marine environment demands components that offer uncompromising reliability, corrosion resistance, and performance. Valve bodies, as critical flow control elements, are central to the safe and efficient operation of vessels and offshore structures. While traditional manufacturing methods have long served the industry, metal additive manufacturing presents a powerful, modern alternative, offering transformative benefits tailored to the challenges of the maritime world.
From enabling highly optimized, complex designs that enhance flow efficiency and reduce weight, to utilizing advanced corrosion-resistant alloys like 316L, CuNi30Mn1Fe, and 254SMO, metal AM pushes the boundaries of what’s possible. The ability to rapidly prototype, produce custom components on demand, and drastically shorten lead times for critical spare parts provides unparalleled agility for marine engineers, operators, and procurement teams. By embracing DfAM principles and understanding the nuances of post-processing and quality assurance, the potential challenges of AM can be effectively navigated, resulting in components that meet or exceed the performance of traditional counterparts.
Choosing the right partner is paramount to harnessing these advantages. Look for providers with proven expertise in marine alloys, robust quality systems, advanced technological capabilities, and a collaborative approach. Companies like Met3dp, headquartered in Qingdao, China, exemplify this commitment. With decades of collective expertise, industry-leading SEBM printers and gas atomization powder production, a wide portfolio of high-performance metal powders, and comprehensive solutions spanning equipment, materials, and application development, Met3dp is enabling next-generation manufacturing across demanding sectors.
As the maritime industry continues to evolve, embracing digital manufacturing technologies like metal AM will be key to enhancing efficiency, reliability, and sustainability. For valve bodies and countless other critical components, additive manufacturing is not just a future possibility – it’s a present-day solution offering significant competitive advantages. Explore how these capabilities can power your organization’s additive manufacturing goals by visiting Met3dp online.
Share On
MET3DP Technology Co., LTD is a leading provider of additive manufacturing solutions headquartered in Qingdao, China. Our company specializes in 3D printing equipment and high-performance metal powders for industrial applications.
Inquiry to get best price and customized Solution for your business!
Related Articles
About Met3DP
Recent Update
Our Product
CONTACT US
Any questions? Send us message now! We’ll serve your request with a whole team after receiving your message.
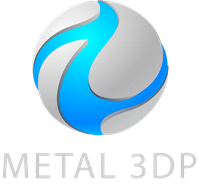
Metal Powders for 3D Printing and Additive Manufacturing