The working steps of WAAM
Table of Contents
Imagine building complex metal structures layer by layer, like a culinary master crafting a magnificent cake. That’s the essence of Wire Arc Additive Manufacturing (WAAM), a revolutionary 3D printing technology that’s transforming the way we create metal parts.
This comprehensive guide will delve into the captivating world of WAAM, taking you on a journey from design conception to the final printed masterpiece. We’ll dissect the process step-by-step, explore the fascinating world of WAAM-compatible metal wires, and answer all your burning questions in a clear and engaging way. So, buckle up and get ready to be amazed!
Understanding the WAAM Workflow
Firstly, a 3D model needs to be prepared, which will serve as a guide for the WAAM process. This model is typically created using Computer-Aided Design (CAD) software. Imagine it as the blueprint for your metal masterpiece. Here, meticulous attention to detail is crucial, as any imperfections in the model will translate into the final printed part.
Next comes the selection of the metal wire, the building block of your creation. WAAM boasts a diverse selection of metal wires, each offering unique properties. We’ll delve deeper into this fascinating world in the next section.
With the 3D model and metal wire chosen, the WAAM system takes center stage. This system comprises a robotic arm, a wire feeder, and a welding torch. The robotic arm, with pinpoint precision, maneuvers the wire feeder and welding torch, meticulously following the pre-programmed path dictated by the 3D model.
The welding torch does the heavy lifting, literally. It unleashes a focused arc of energy that melts the metal wire, transforming it into a molten pool. This molten metal is then deposited layer by layer, gradually building up the desired shape.
Think of WAAM like a sophisticated metal welder on steroids. While traditional welding joins existing pieces of metal, WAAM creates entirely new structures from scratch.
As each layer is deposited, the previous layer cools and solidifies, creating a strong bond. This meticulous layer-by-layer approach allows for the fabrication of intricate geometries that would be impossible with traditional manufacturing techniques.
Finally, once the printing process is complete, the part may undergo post-processing. This might involve heat treatment to relieve residual stress, machining to achieve precise tolerances, or surface finishing for aesthetic appeal.
Now that you’ve grasped the fundamental steps of WAAM, let’s explore the diverse range of metal wires that breathe life into this technology.
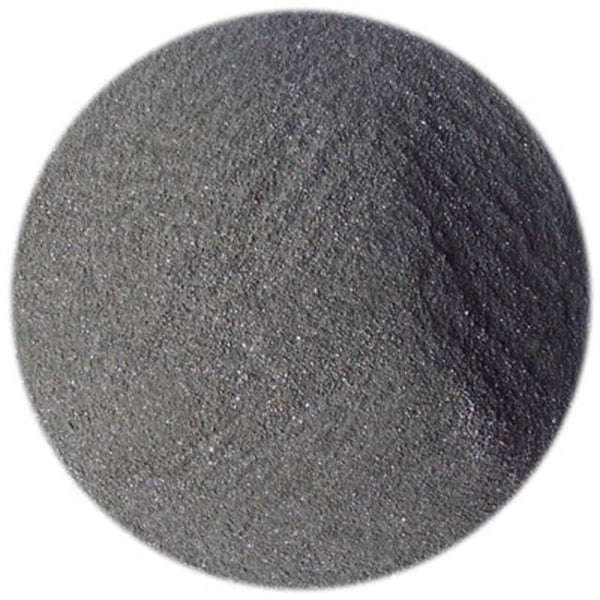
the World of WAAM-Compatible Metal Wires
The choice of metal wire in WAAM significantly impacts the final product’s properties. Just like choosing the right ingredients for a recipe, selecting the appropriate wire ensures your printed part possesses the desired strength, ductility, and corrosion resistance. Here’s a glimpse into some of the most commonly used metal wires in WAAM:
Metal Wire | Composition | Properties | Applications |
---|---|---|---|
Low-Carbon Steel (AISI 1025, 1045) | Primarily iron with low carbon content | Excellent weldability, good strength, and affordability | Structural components, general-purpose parts, machine bases |
High-Strength Low-Alloy (HSLA) Steel | Iron with additional elements like vanadium and niobium | Higher strength compared to low-carbon steel, good toughness | Heavy machinery components, bridges, pressure vessels |
Stainless Steel (AISI 304, 316) | Iron alloyed with chromium and nickel | Excellent corrosion resistance, good strength, biocompatible grades available | Food processing equipment, medical implants, chemical processing tanks |
Aluminum (AA 5356, 6061) | Lightweight, good corrosion resistance, high electrical conductivity | Aerospace components, automotive parts, heat exchangers | |
Titanium (Ti-6Al-4V) | High strength-to-weight ratio, excellent corrosion resistance | Aerospace parts, biomedical implants, marine applications | |
Nickel Alloys (Inconel 625, Inconel 718) | Nickel alloyed with chromium, molybdenum, and other elements | Exceptional high-temperature performance, excellent corrosion resistance | Gas turbine components, rocket engine parts, heat exchangers |
Copper | Excellent electrical conductivity and thermal conductivity | Electrical conductors, heat sinks, brazing applications | |
Cobalt-Chrome (CoCr) | High wear resistance, biocompatible grades available | Medical implants, orthopedic devices, cutting |
The table above provides a starting point, but the world of WAAM-compatible metal wires extends far beyond these entries. Here are some additional noteworthy options:
- Tool Steels: These include grades like AISI H13 and D2, renowned for their exceptional wear resistance and ability to retain hardness at elevated temperatures. Applications include cutting tools, molds, and dies.
- Magnesium Alloys: The lightest structural metal on the planet, magnesium offers significant weight savings in applications like aerospace and automotive components. However, its susceptibility to corrosion necessitates careful selection and post-processing techniques.
- Refractory Alloys: These high-melting-point metals, like tantalum and molybdenum, excel in environments with extreme heat. They find use in furnace components, rocket engine nozzles, and other high-temperature applications.
Beyond the base metal, some WAAM wires incorporate additional elements to enhance specific properties. For instance, certain steel wires might be infused with copper to improve electrical conductivity or with nickel to bolster corrosion resistance. This versatility allows engineers to tailor the material to the specific demands of the application.
Here’s a crucial point to remember: not all metal wires are created equal for WAAM. Certain factors influence a wire’s suitability for this process:
- Weldability: The wire needs to melt smoothly and form a strong bond with the underlying layer.
- Feedability: The wire diameter and surface characteristics should ensure smooth and uninterrupted feeding through the wire feeder.
- Spatter: Excessive spatter, molten metal droplets ejected during welding, can compromise the dimensional accuracy and surface finish of the printed part.
Metal wire manufacturers play a critical role in developing WAAM-compatible wires. They meticulously control the composition, microstructure, and surface properties to optimize these factors for the WAAM process.
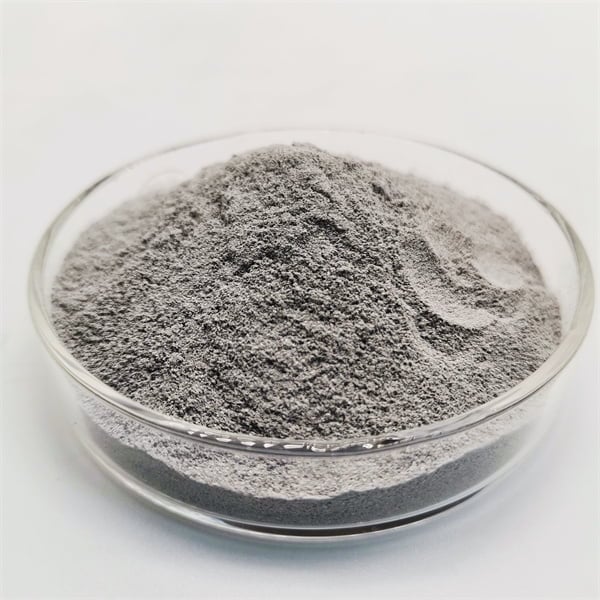
The Benefits and Considerations of WAAM
Now that you’re familiar with the WAAM workflow and the fascinating world of metal wires, let’s delve into the advantages and considerations associated with this technology.
Advantages of WAAM:
- Design Freedom: WAAM allows for the fabrication of complex geometries that are impossible with traditional techniques like casting or machining. This opens doors for innovative designs and lightweight structures.
- Material Versatility: The wide range of WAAM-compatible metal wires enables the creation of parts with diverse properties, catering to various applications.
- Large Build Volume: WAAM systems can handle large work envelopes, making them suitable for building sizable structures. This is particularly advantageous in industries like shipbuilding and construction.
- Reduced Lead Time: Compared to traditional manufacturing methods, WAAM can significantly shorten lead times, especially for complex parts.
- Near-Net-Shape Manufacturing: WAAM produces parts with minimal material waste, offering environmental and cost benefits.
Considerations for WAAM:
- Surface Finish: While WAAM can produce good quality surfaces, they might require additional post-processing for applications demanding a superior finish.
- Residual Stress: The layer-by-layer deposition process can introduce residual stress into the part. Heat treatment can help mitigate this concern.
- Porosity: Minimizing porosity, small air pockets trapped within the metal, is crucial for achieving optimal mechanical properties. Careful process control is essential.
- Cost: The initial investment cost for WAAM systems can be higher compared to some traditional techniques. However, the benefits in design freedom, lead time, and material utilization can offset these costs in the long run.
FAQ
Here are some frequently asked questions regarding WAAM, presented in a clear and concise table format:
Question | Answer |
---|---|
What are the limitations of WAAM? | As discussed, surface finish, residual stress, and porosity are aspects to consider. Additionally, WAAM build speeds might be slower compared to some other additive manufacturing techniques. |
What industries are adopting WAAM? | WAAM is finding applications in various sectors, including aerospace, automotive, shipbuilding, construction, and oil & gas. |
What are the future prospects of WAAM? | WAAM technology is continuously evolving. Advancements in wire development, process control, and automation are expected to further enhance its capabilities and broaden its adoption across various industries. |
We hope this comprehensive guide has equipped you with a solid understanding of WAAM, its working principles, the world of WAAM-compatible metal wires, and the key considerations associated with this transformative technology. As WAAM continues to evolve, it holds immense potential to revolutionize how we design, engineer, and manufacture metal parts.
Share On
MET3DP Technology Co., LTD is a leading provider of additive manufacturing solutions headquartered in Qingdao, China. Our company specializes in 3D printing equipment and high-performance metal powders for industrial applications.
Inquiry to get best price and customized Solution for your business!
Related Articles
About Met3DP
Recent Update
Our Product
CONTACT US
Any questions? Send us message now! We’ll serve your request with a whole team after receiving your message.