The Advantages of WAAM 3D Printing Technology
Table of Contents
Imagine a 3D printer that can create colossal metal structures, churning out components the size of a car or even a small building. This isn’t science fiction; it’s the reality of WAAM 3D printing technology. Buckle up, because we’re about to delve into the fascinating world of WAAM , exploring its benefits, the metals it can print with, and how it’s revolutionizing manufacturing.
What is WAAM 3D Printing?
WAAM , or Wire Arc Additive Manufacturing, is a metal 3D printing process that works like a high-tech welding robot. Instead of laying down plastic filament, WAAM 3D uses a continuous wire as feedstock. An electric arc melts the wire, and a robotic arm meticulously deposits the molten metal layer by layer, building the desired 3D object.
Think of it like building a metal sculpture with a sophisticated hot glue gun. But unlike traditional welding, WAAM offers precise control over the deposition process, enabling the creation of complex geometries.
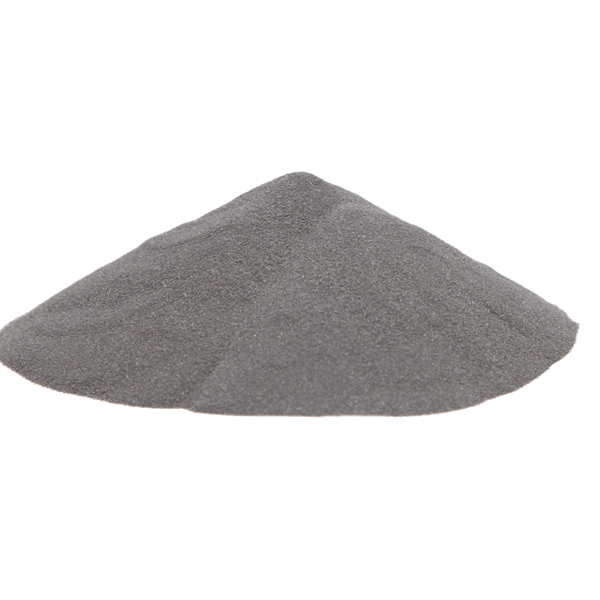
The Allure of Large-Scale Metal Printing
While traditional 3D printing excels at creating intricate plastic parts, it often struggles with large-scale metal components. But WAAM breaks these limitations. Here’s why manufacturers are buzzing about its potential:
- Big is Beautiful: WAAM ‘s biggest strength lies in its ability to print massive metal structures. Unlike other metal 3D printing technologies restricted by build chamber size, WAAM utilizes a robotic arm, offering virtually unlimited build volume. This opens doors to printing giant parts like ship hulls, bridge components, or even rocket engine casings.
- Speed Demon: Compared to traditional manufacturing methods like casting or forging, WAAM boasts impressive printing speeds. Imagine creating a large metal component in a matter of hours instead of days or weeks. This translates to faster turnaround times and reduced production costs.
- Material Magic: WAAM is compatible with a wide range of metal alloys, including steel, titanium, aluminum, and nickel alloys. This versatility allows manufacturers to choose the most suitable material for the application’s specific needs, be it strength, corrosion resistance, or weight considerations.
- Waste Not, Want Not: WAAM is a material-efficient process. Unlike subtractive manufacturing techniques like machining, which generate significant scrap, WAAM deposits material only where it’s needed. This translates to cost savings and a more environmentally friendly production process.
Metals that Make WAAM Mighty
The success of WAAM hinges on the variety of metals it can effectively print with. Here’s a closer look at some of the most commonly used metal powders in WAAM :
Metal Alloy | Composition | Properties | Applications |
---|---|---|---|
AISI 1045 Steel | 0.42% Carbon, 0.6% Manganese, Iron (Base) | High strength, good ductility, machinable | Gears, shafts, structural components |
AISI 316L Stainless Steel | 16-18% Chromium, 10-14% Nickel, 2% Molybdenum, Iron (Base) | Excellent corrosion resistance, good strength | Chemical processing equipment, marine applications, food & beverage equipment |
Inconel 625 | 20% Chromium, 9% Nickel, 3% Molybdenum, Iron (Base) | High-temperature strength, excellent corrosion resistance | Gas turbine components, rocket engine parts, heat exchangers |
Titanium Grade 2 | 99.2% Titanium | High strength-to-weight ratio, good biocompatibility | Aircraft parts, medical implants, sporting goods |
Aluminum 6061 | 95.8% Aluminum, 0.6% Magnesium, 0.35% Silicon, Iron (Impurity) | Good machinability, lightweight, corrosion resistant | Automotive parts, building components, electrical enclosures |
Maraging Steel 1.2362 | 18% Nickel, 12.5% Molybdenum, 3% Cobalt, Iron (Base) | Ultra-high strength, good toughness | Aerospace components, tooling, high-performance firearms |
Nickel Alloy 718 | 55% Nickel, 18% Chromium, 8.5% Molybdenum, Iron (Base) | High strength, excellent creep resistance at elevated temperatures | Turbine disks, pressure vessels, fasteners |
Copper | 99.9% Copper | High electrical conductivity, good thermal conductivity | Electrical conductors, heat sinks, |
Hastelloy C-276 | 57% Nickel, 16% Molybdenum, 15% Chromium, Iron (Base) | Exceptional corrosion resistance to a wide range of chemicals | Chemical processing equipment, pollution control systems, nuclear waste containment |
Inconel 718Plus | Similar to Inconel 718 with improved printability | High strength, good creep resistance, excellent printability for complex geometries | Turbine blades, heat exchangers, demanding aerospace parts |
Aluminum Si7Mg0.3 | Aluminum alloy with 7% Silicon and 0.3% Magnesium | Excellent castability, good weldability, suitable for large WAAM prints | Automotive components, building facades, large structural components |
Beyond the Material Magic: A Look at WAAM ‘s Applications
The ability to print large, complex metal structures with a wide range of materials opens doors to a vast array of applications across various industries. Here are some exciting ways WAAM is transforming manufacturing:
- Aerospace: WAAM ‘s ability to print lightweight, high-strength components like aircraft wing components, fuselage parts, and landing gear is revolutionizing aerospace manufacturing. This technology allows for complex geometries and customization, potentially leading to lighter and more efficient aircraft.
- Construction: Imagine printing entire building components or even bridges on-site. WAAM’s potential for large-scale metal printing has the construction industry buzzing. This technology could significantly reduce construction times and costs, while also enabling the creation of innovative architectural designs.
- Shipbuilding: WAAM can be used to print massive ship hulls, propeller shafts, and other critical components. This not only reduces fabrication times but also allows for the creation of complex, lightweight structures for improved fuel efficiency.
- Oil & Gas: WAAM is well-suited for printing high-pressure pipelines, pressure vessels, and other equipment used in the oil and gas industry. The ability to print these components on-site, closer to drilling locations, can offer significant logistical advantages.
- Medical Implants: WAAM has the potential to revolutionize custom prosthetics and orthopedic implants. By printing implants using biocompatible titanium alloys, WAAM can create patient-specific implants that perfectly match individual anatomies, leading to improved functionality and patient outcomes.
The Cost Equation: WAAM – Investment versus Benefit
While WAAM offers a plethora of advantages, it’s important to consider the cost aspect. Here’s a breakdown of some factors to consider:
- Equipment Cost: WAAM printers are complex machines, and the initial investment can be significant. However, as the technology matures and adoption increases, the cost is expected to decrease.
- Material Cost: Metal powders used in WAAM can be expensive compared to plastics used in traditional 3D printing. However, the minimal material waste associated with WAAM helps offset some of these costs.
- Operational Costs: The energy consumption of WAAM printers can be high due to the arc welding process involved. However, the reduced labor costs and faster production times can help balance this factor.
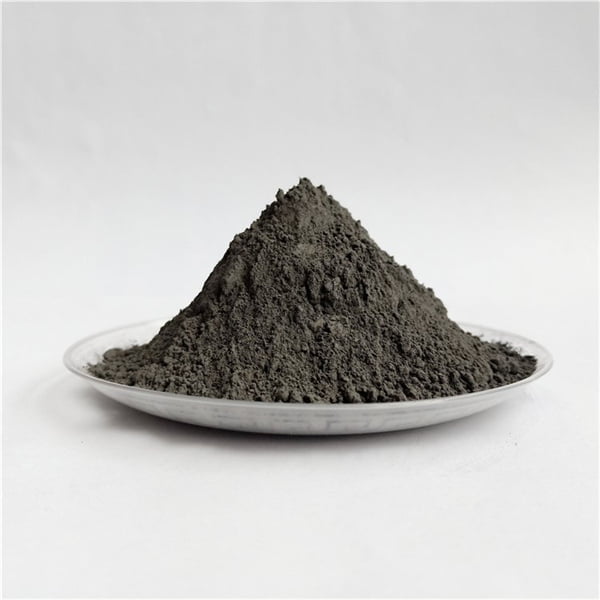
The Future of WAAM : A Brighter, Bigger Picture
WAAM technology is still in its early stages, but its potential is undeniable. As research and development continue, we can expect advancements in several areas:
- Print Speed and Efficiency: Optimizing the deposition process and automating certain aspects of WAAM can further increase printing speeds and production efficiency.
- Multi-Material Printing: The ability to print with multiple metal alloys within the same build would open doors to creating components with graded properties, tailored for specific applications.
- Standardization and Regulations: Developing standardized printing parameters and material qualifications for WAAM will be crucial for wider adoption across different industries.
FAQ
Question | Answer |
---|---|
What are the limitations of WAAM3D printing? | While WAAM3D boasts significant advantages, it’s not without limitations. Compared to some powder-bed fusion 3D printing technologies, WAAM3D printed parts may have slightly lower surface finish and dimensional accuracy. Additionally, the high temperatures involved in the process can introduce residual stresses within the printed part, potentially affecting its mechanical properties. However, with proper heat management techniques and post-processing methods, these limitations can be mitigated. |
Is WAAM3D suitable for small, intricate parts? | WAAM3D excels at large-scale metal printing. For small, intricate parts with high precision requirements, other 3D printing technologies like Selective Laser Melting (SLM) might be better suited. |
How safe is WAAM3D printing? | WAAM3D printing involves arc welding, which necessitates following safety protocols like wearing proper personal protective equipment (PPE) and ensuring adequate ventilation in the printing environment. |
What are the environmental benefits of WAAM3D printing? | Compared to traditional subtractive manufacturing techniques, WAAM3D offers significant environmental advantages. The minimal material waste associated with WAAM3D reduces overall resource consumption and environmental impact. Additionally, the potential for on-site printing in certain applications can minimize transportation needs, further contributing to a greener footprint. |
Conclusion
WAAM3D represents a significant leap forward in the realm of metal additive manufacturing. Its ability to print large, complex metal structures with a wide range of materials opens doors to exciting possibilities across various industries. While there are limitations to address and advancements on the horizon, WAAM3D undoubtedly holds the potential to revolutionize how we design, build, and create with metal. As the technology matures and costs become more favorable, WAAM3D is poised to become a game-changer in the world of metal fabrication.
Share On
MET3DP Technology Co., LTD is a leading provider of additive manufacturing solutions headquartered in Qingdao, China. Our company specializes in 3D printing equipment and high-performance metal powders for industrial applications.
Inquiry to get best price and customized Solution for your business!
Related Articles
About Met3DP
Recent Update
Our Product
CONTACT US
Any questions? Send us message now! We’ll serve your request with a whole team after receiving your message.
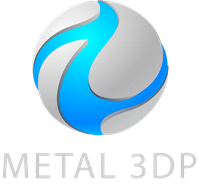
Metal Powders for 3D Printing and Additive Manufacturing