Wire Arc Additive Manufacturing (WAAM)
Table of Contents
Introduction
Welcome to the world of Wire Arc Additive Manufacturing (WAAM)! This innovative technology is revolutionizing the way we approach manufacturing, particularly in industries where precision and material strength are paramount. From aerospace to automotive, WAAM is making waves. But what exactly is WAAM, and why should you care? Let’s dive in.
Overview of Wire Arc Additive Manufacturing (WAAM)
Wire Arc Additive Manufacturing (WAAM) is an advanced form of additive manufacturing that uses an electric arc to melt wire feedstock, which is then deposited layer by layer to create a three-dimensional object. Unlike traditional manufacturing methods that involve cutting away material, WAAM builds objects from the ground up, reducing waste and allowing for greater design flexibility.
How WAAM Works
At its core, WAAM involves feeding a metal wire into an electric arc, which melts the wire and deposits it onto a substrate. This process is controlled by a computer-aided design (CAD) system, which ensures precision and repeatability. The layers are built up sequentially until the final shape is achieved.
Key Benefits of WAAM
- Material Efficiency: WAAM uses wire feedstock, which is more material-efficient than traditional manufacturing methods that rely on bulk material.
- Design Flexibility: The layer-by-layer approach allows for complex geometries that would be difficult or impossible to achieve with conventional methods.
- Cost-Effective: Reduced material waste and the ability to create near-net-shape parts can lead to significant cost savings.
- Speed: WAAM can produce large components faster than many other additive manufacturing methods.
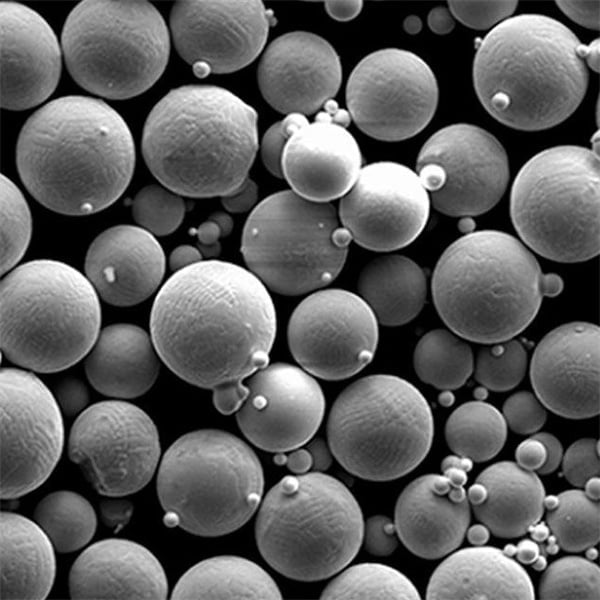
Types of Metal Powders Used in WAAM
One of the critical aspects of WAAM is the selection of metal powders. Different metals have different properties, making them suitable for various applications. Here’s a look at some specific metal powder models used in WAAM:
Metal Powder | Description |
---|---|
Inconel 718 | A nickel-chromium alloy known for its high strength and resistance to corrosion and heat, making it ideal for aerospace applications. |
Ti-6Al-4V | A titanium alloy with excellent strength-to-weight ratio and corrosion resistance, commonly used in aerospace and biomedical industries. |
316L Stainless Steel | Offers good corrosion resistance and mechanical properties, suitable for marine, pharmaceutical, and food processing industries. |
AlSi10Mg | An aluminum alloy known for its good mechanical properties and lightweight nature, often used in automotive and aerospace applications. |
ER70S-6 | A mild steel wire with high tensile strength, frequently used in general manufacturing and construction. |
CuNi2SiCr | A copper alloy with excellent electrical and thermal conductivity, ideal for electrical and electronic applications. |
H13 Tool Steel | A chromium-molybdenum-vanadium alloy known for its high toughness and resistance to thermal fatigue, widely used in tooling and die applications. |
NiCrMo-625 | A nickel-based superalloy with outstanding corrosion resistance and high-temperature strength, suitable for marine and chemical processing industries. |
ER4043 Aluminum | An aluminum-silicon alloy with good fluidity and reduced shrinkage, commonly used in welding and casting applications. |
316L VM | Vacuum melted variant of 316L stainless steel, offering superior cleanliness and uniformity, ideal for medical implants and high-purity applications. |
Applications of Wire Arc Additive Manufacturing (WAAM)
WAAM is finding applications across various industries due to its versatility and efficiency. Here’s a detailed look at where WAAM is making an impact:
Industry | Application |
---|---|
Aerospace | Manufacturing of large structural components, repair of turbine blades, and production of complex geometries. |
Automotive | Creation of lightweight and high-strength parts, prototypes, and custom components. |
Marine | Production of large-scale components, repair of ship parts, and creation of corrosion-resistant parts. |
Oil & Gas | Fabrication of pressure vessels, pipelines, and complex components exposed to harsh environments. |
Medical | Custom implants, surgical tools, and prosthetics with tailored properties. |
Construction | Production of architectural elements, structural components, and customized designs. |
Tooling | Manufacturing of molds, dies, and fixtures with high precision and durability. |
Energy | Production of components for wind turbines, nuclear reactors, and other energy systems. |
Defense | Fabrication of armor, weapon components, and other military hardware. |
Electronics | Creation of components with high electrical and thermal conductivity, such as heat sinks and connectors. |
Specifications, Sizes, Grades, and Standards
WAAM technology can accommodate various specifications, sizes, grades, and standards to meet the diverse needs of different industries. Here’s a breakdown:
Specification | Details |
---|---|
Wire Diameter | Typically ranges from 0.8 mm to 4.0 mm, depending on the material and application. |
Deposition Rate | Varies based on material and process parameters, generally between 1 kg/hr to 10 kg/hr. |
Layer Thickness | Generally between 0.1 mm to 1.0 mm, depending on the required resolution and part complexity. |
Material Grades | Conforms to industry standards such as ASTM, ISO, and AMS specifications. |
Quality Standards | Adheres to standards such as ISO 9001 for quality management and AS9100 for aerospace applications. |
Surface Finish | Typically requires post-processing such as machining or grinding to achieve desired surface finish. |
Dimensional Accuracy | Generally within ±0.5 mm, depending on the process control and material properties. |
Suppliers and Pricing Details
Sourcing the right materials and equipment for WAAM can be crucial. Here are some leading suppliers and indicative pricing details:
Supplier | Material | Price Range (per kg) | Notes |
---|---|---|---|
Hoganas | Metal powders | $50 – $150 | Offers a wide range of metal powders with high purity and consistency. |
Carpenter Technology | Specialty alloys | $70 – $200 | Known for high-performance alloys, suitable for demanding applications. |
Sandvik | Stainless steel powders | $60 – $180 | Provides high-quality stainless steel powders for various industries. |
Oerlikon Metco | Thermal spray materials | $80 – $220 | Specializes in surface solutions and advanced materials. |
Aperam | Nickel alloys | $90 – $250 | Offers a range of nickel-based superalloys with excellent mechanical properties. |
Arcam AB | Titanium powders | $100 – $300 | A leading supplier of titanium powders, ideal for aerospace and medical applications. |
GKN Additive | Custom metal powders | $70 – $210 | Provides tailored metal powder solutions for specific customer requirements. |
Praxair | Industrial gases & powders | $60 – $190 | Supplies metal powders and gases essential for WAAM processes. |
Kennametal | Cobalt alloys | $80 – $230 | Known for high-strength and wear-resistant cobalt-based alloys. |
Ametek | Aluminum alloys | $50 – $160 | Offers a variety of aluminum powders suitable for lightweight and high-strength applications. |
Advantages of Wire Arc Additive Manufacturing (WAAM)
Wire Arc Additive Manufacturing (WAAM) offers numerous advantages over traditional manufacturing methods and even other additive manufacturing techniques. Here are some key benefits:
- Material Efficiency: WAAM uses wire feedstock, which minimizes material waste compared to subtractive methods.
- Cost Savings: Reduced material waste and the ability to produce near-net-shape parts can significantly lower manufacturing costs.
- Design Flexibility: The layer-by-layer construction allows for complex geometries that are difficult or impossible to achieve with traditional methods.
- Speed: WAAM can produce large parts faster than many other additive manufacturing methods, making it suitable for rapid prototyping and production.
- Scalability: WAAM is capable of producing large-scale components, which is beneficial for industries like aerospace and construction.
- Reduced Lead Times: The ability to produce parts on-demand can lead to shorter lead times and quicker turnaround.
- Strength and Durability: WAAM parts often exhibit excellent mechanical properties, making them suitable for demanding applications.
Disadvantages of Wire Arc Additive Manufacturing (WAAM)
While WAAM offers many advantages, it also has some limitations that need to be considered:
- Surface Finish: The as-built surface finish of WAAM parts can be rough and may require post-processing such as machining or grinding.
- Dimensional Accuracy: Achieving high dimensional accuracy can be challenging and often requires careful process control and post-processing.
- Material Limitations: Not all materials are suitable for WAAM, and the choice of feedstock can be limited.
- Heat Input: The high heat input from the electric arc can lead to residual stresses and distortions in the part, which may require stress relief treatments.
- Equipment Costs: The initial investment in WAAM equipment can be high, although it can be offset by the savings in material and production costs over time.
- Process Complexity: The WAAM process involves complex interactions between the wire feed, arc, and substrate, requiring skilled operators and precise control.
Comparison of WAAM with Other Additive Manufacturing Methods
When it comes to additive manufacturing, WAAM is just one of several methods available. Let’s compare WAAM with other popular additive manufacturing techniques:
Parameter | WAAM | SLA (Stereolithography) | SLS (Selective Laser Sintering) | FDM (Fused Deposition Modeling) |
---|---|---|---|---|
Material Efficiency | High (wire feedstock) | Moderate | High | Moderate |
Cost | Moderate to High | High | High | Low to Moderate |
Design Flexibility | High | Very High | High | Moderate |
Speed | High | Moderate | Moderate | Moderate |
Scalability | High | Low | Moderate | Low |
Surface Finish | Moderate to Low (post-processing needed) | High | Moderate | Low |
Dimensional Accuracy | Moderate (post-processing needed) | High | High | Moderate |
Strength and Durability | High | Moderate | High | Low to Moderate |
Pros and Cons of Different Metal Powders in WAAM
Choosing the right metal powder for WAAM is crucial for achieving the desired properties in the final part. Here’s a comparison of some popular metal powders:
Metal Powder | Advantages | Disadvantages |
---|---|---|
Inconel 718 | High strength, excellent corrosion and heat resistance. | High cost, requires careful process control to avoid cracking. |
Ti-6Al-4V | Excellent strength-to-weight ratio, corrosion resistance. | Expensive, sensitive to oxygen contamination. |
316L Stainless Steel | Good corrosion resistance, widely available. | Lower strength compared to other alloys, may require post-processing for improved surface finish. |
AlSi10Mg | Lightweight, good mechanical properties. | Lower strength compared to some other metals, potential for porosity. |
ER70S-6 | High tensile strength, cost-effective. | Susceptible to corrosion, requires protective coatings. |
CuNi2SiCr | Excellent electrical and thermal conductivity. | Limited availability, higher cost. |
H13 Tool Steel | High toughness, thermal fatigue resistance. | Requires heat treatment for optimal properties, potential for distortion during cooling. |
NiCrMo-625 | Outstanding corrosion resistance, high-temperature strength. | Expensive, challenging to process without cracking. |
ER4043 Aluminum | Good fluidity, reduced shrinkage. | Lower strength compared to other aluminum alloys, sensitive to thermal expansion. |
316L VM | Superior cleanliness and uniformity. | Higher cost due to vacuum melting process, may require post-processing for optimal surface finish and properties. |
WAAM: A Technical Perspective
Wire Arc Additive Manufacturing (WAAM) is a fascinating intersection of metallurgy, robotics, and computer science. Let’s explore some technical aspects that make WAAM a cutting-edge technology:
- Metallurgy: The choice of metal powders, understanding their properties, and controlling the microstructure during the WAAM process are crucial for achieving the desired mechanical properties in the final part.
- Robotics: WAAM often involves robotic arms or gantry systems to precisely control the deposition of material, ensuring consistent quality and repeatability.
- Computer-Aided Design (CAD): Advanced CAD software is used to design parts and control the deposition process, allowing for complex geometries and precise control over the final shape.
Case Studies: Success Stories in WAAM
To understand the real-world impact of WAAM, let’s look at some success stories:
- Aerospace Industry: A leading aerospace company used WAAM to manufacture large structural components for aircraft. The ability to produce near-net-shape parts significantly reduced material waste and production time, leading to substantial cost savings.
- Automotive Industry: An automotive manufacturer utilized WAAM to produce lightweight, high-strength components for electric vehicles. The flexibility of WAAM allowed for rapid prototyping and customization, accelerating the development process.
- Medical Industry: A medical device company used WAAM to create custom implants and surgical tools. The ability to tailor the properties of the final part to meet specific requirements improved patient outcomes and satisfaction.
Future Trends in WAAM
As technology continues to advance, the future of WAAM looks promising. Here are some trends to watch:
- Material Development: Continued research into new metal powders and alloys will expand the range of materials available for WAAM, improving properties and performance.
- Process Optimization: Advances in process control, including real-time monitoring and adaptive control systems, will enhance the accuracy and repeatability of WAAM.
- Integration with Other Technologies: Combining WAAM with other additive manufacturing methods and traditional manufacturing processes will lead to hybrid manufacturing solutions, offering even greater flexibility and efficiency.
- Sustainability: WAAM’s material efficiency and potential for on-demand manufacturing align with growing trends toward sustainable and eco-friendly manufacturing practices.
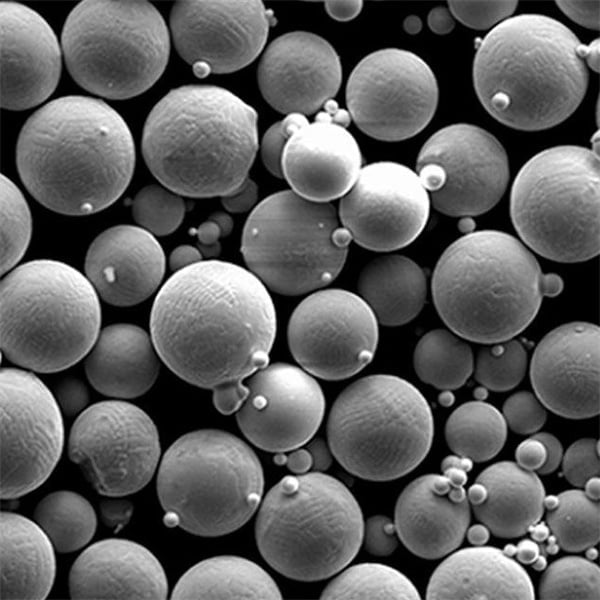
FAQ
Question | Answer |
---|---|
What is WAAM? | WAAM stands for Wire Arc Additive Manufacturing, an advanced manufacturing process that uses an electric arc to melt wire feedstock and build 3D objects. |
How does WAAM differ from other additive manufacturing methods? | WAAM uses wire feedstock and an electric arc, offering high material efficiency, scalability, and the ability to produce large parts quickly. |
What materials can be used in WAAM? | WAAM can use a variety of metal powders, including Inconel, titanium alloys, stainless steel, aluminum alloys, and more. |
What are the advantages of WAAM? | WAAM offers material efficiency, cost savings, design flexibility, speed, scalability, and the ability to produce strong and durable parts. |
What are the disadvantages of WAAM? | WAAM parts may require post-processing for surface finish and dimensional accuracy, and the process can involve high equipment costs and complexity. |
What industries use WAAM? | WAAM is used in aerospace, automotive, marine, oil & gas, medical, construction, tooling, energy, defense, and electronics industries. |
What is the typical wire diameter used in WAAM? | The wire diameter typically ranges from 0.8 mm to 4.0 mm, depending on the material and application. |
What is the deposition rate in WAAM? | The deposition rate varies based on material and process parameters, generally between 1 kg/hr to 10 kg/hr. |
How accurate are WAAM parts? | WAAM parts generally have a dimensional accuracy within ±0.5 mm, but this can vary depending on process control and material properties. |
What post-processing is required for WAAM parts? | WAAM parts may require machining, grinding, heat treatment, or other post-processing techniques to achieve the desired surface finish and properties. |
Conclusion
Wire Arc Additive Manufacturing (WAAM) is a transformative technology that combines the precision of additive manufacturing with the efficiency of wire feedstock. From aerospace to medical implants, WAAM is making an impact across industries, offering unparalleled design flexibility, material efficiency, and cost savings. As technology continues to evolve, the potential for WAAM is boundless, promising a future where complex, high-strength components can be produced quickly and sustainably. Whether you’re an engineer, designer, or manufacturer, understanding WAAM can open up new possibilities and drive innovation in your field.
Share On
MET3DP Technology Co., LTD is a leading provider of additive manufacturing solutions headquartered in Qingdao, China. Our company specializes in 3D printing equipment and high-performance metal powders for industrial applications.
Inquiry to get best price and customized Solution for your business!
Related Articles
About Met3DP
Recent Update
Our Product
CONTACT US
Any questions? Send us message now! We’ll serve your request with a whole team after receiving your message.
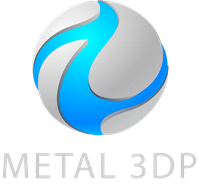
Metal Powders for 3D Printing and Additive Manufacturing