Workpiece Repair: The Ultimate Guide
Table of Contents
Workpiece repair is a critical aspect of manufacturing and maintenance industries. From machinery components to structural parts, the need to restore worn or damaged workpieces is paramount. This guide delves into the intricate world of workpiece repair, highlighting the importance, methods, materials, and technical specifics involved. Whether you’re a seasoned professional or a curious novice, this comprehensive article will provide valuable insights into workpiece repair.
Overview of Workpiece Repair
Workpiece repair involves restoring the functionality and integrity of a component that has been worn out or damaged. This process is essential in extending the lifespan of machinery, reducing downtime, and saving costs associated with complete replacements.
Key Details of Workpiece Repair:
- Definition: The process of restoring damaged or worn components to their original specifications.
- Purpose: Extend machinery life, reduce costs, minimize downtime.
- Methods: Welding, metal powder spraying, machining, coating.
- Materials Used: Metal powders, welding rods, coatings.
- Applications: Automotive, aerospace, manufacturing, construction.
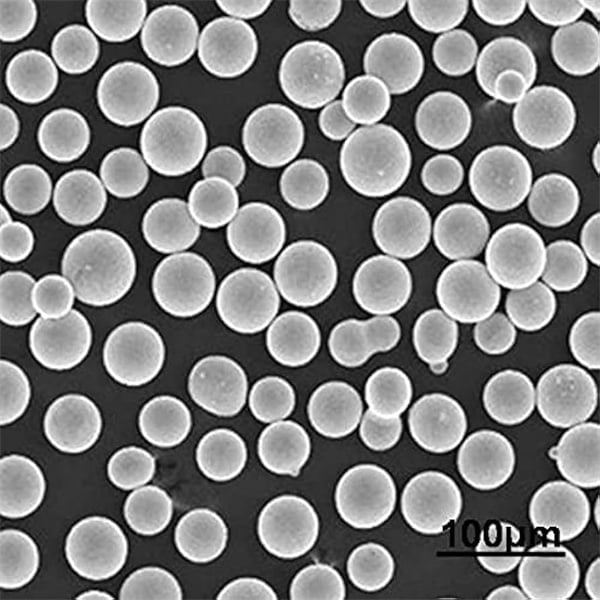
Types of Metal Powders for Workpiece Repair
Metal powders play a crucial role in workpiece repair. Different types offer varying properties suited for specific applications. Here are some of the most commonly used metal powders:
Metal Powder Model | Composition | Properties | Applications |
---|---|---|---|
Inconel 625 | Nickel-based | High corrosion resistance, excellent mechanical properties | Aerospace, marine |
Cobalt 6B | Cobalt-based | Superior wear and galling resistance | Valve seats, pump components |
Stellite 21 | Cobalt-based | High resistance to thermal and mechanical shock | Gas turbine blades, engine valves |
WC-Co | Tungsten carbide-cobalt | Exceptional hardness and wear resistance | Cutting tools, mining equipment |
Hastelloy C276 | Nickel-molybdenum-chromium | Outstanding resistance to pitting and stress corrosion | Chemical processing, pollution control |
NiCr 80/20 | Nickel-chromium | High temperature and oxidation resistance | Heating elements, gas turbines |
316L Stainless Steel | Iron-chromium-nickel-molybdenum | Excellent corrosion resistance, good mechanical properties | Medical devices, food processing |
420 Stainless Steel | Iron-chromium | High hardness, good wear resistance | Cutting tools, surgical instruments |
AlSi10Mg | Aluminum-silicon-magnesium | Lightweight, good thermal conductivity | Automotive, aerospace |
Ti6Al4V | Titanium-aluminum-vanadium | High strength-to-weight ratio, excellent corrosion resistance | Aerospace, biomedical implants |
Applications of Workpiece Repair
The applications of workpiece repair span various industries, each with unique requirements and standards.
Industry Applications:
Industry | Common Applications |
---|---|
Automotive | Engine components, transmission parts |
Aerospace | Turbine blades, structural components |
Manufacturing | Machine tools, molds, dies |
Construction | Heavy machinery parts, tools |
Marine | Propellers, shafts, hull components |
Oil and Gas | Drilling equipment, valves, pumps |
Methods of Workpiece Repair
Different methods are employed to repair workpieces, depending on the material, damage, and application.
Common Repair Methods:
- Welding: Fusing materials together using heat.
- Metal Powder Spraying: Applying metal powder to a surface and fusing it using heat.
- Machining: Removing damaged material and reshaping the part.
- Coating: Applying protective layers to surfaces to restore functionality.
Comparing Methods:
Method | Advantages | Disadvantages |
---|---|---|
Welding | Strong, permanent repair | Requires skilled labor, heat can alter properties |
Metal Powder Spraying | Versatile, precise | Expensive, equipment-intensive |
Machining | Precise, controlled | Material removal, can be time-consuming |
Coating | Protective, can enhance properties | May not restore structural integrity |
Specifications, Sizes, Grades, and Standards
Understanding the specifications, sizes, grades, and standards is crucial for selecting the right materials and methods for workpiece repair.
Specifications and Standards:
Material | Grade | Standard |
---|---|---|
Inconel 625 | UNS N06625 | ASTM B446 |
Cobalt 6B | AMS 5894 | ASTM F75 |
Stellite 21 | AMS 5385 | ASTM F75 |
WC-Co | Various | ISO 4288 |
Hastelloy C276 | UNS N10276 | ASTM B575 |
NiCr 80/20 | Various | ISO 1173 |
316L Stainless Steel | UNS S31603 | ASTM A240 |
420 Stainless Steel | UNS S42000 | ASTM A276 |
AlSi10Mg | Various | ISO 209 |
Ti6Al4V | UNS R56400 | ASTM B348 |
Suppliers and Pricing Details
When selecting materials for workpiece repair, it’s essential to consider the suppliers and pricing details to ensure cost-effectiveness and availability.
Suppliers and Pricing:
Supplier | Material | Pricing (per kg) | Notes |
---|---|---|---|
Praxair | Inconel 625 | $120 | Bulk discounts available |
Höganäs | Cobalt 6B | $150 | High-quality grades |
Kennametal | Stellite 21 | $200 | Consistent supply |
Sandvik | WC-Co | $250 | Custom blends available |
Haynes International | Hastelloy C276 | $180 | Wide range of sizes |
Oerlikon Metco | NiCr 80/20 | $100 | Good availability |
Carpenter Technology | 316L Stainless Steel | $90 | Reliable supplier |
Allegheny Technologies | 420 Stainless Steel | $70 | Competitive pricing |
ECKA Granules | AlSi10Mg | $50 | Lightweight materials |
Timet | Ti6Al4V | $300 | Premium quality |
Comparing Pros and Cons
Choosing the right method and material for workpiece repair involves weighing the pros and cons of each option.
Advantages and Limitations:
Material | Advantages | Limitations |
---|---|---|
Inconel 625 | High strength, corrosion resistance | Expensive, difficult to machine |
Cobalt 6B | Excellent wear resistance | High cost |
Stellite 21 | High thermal stability | Brittle, expensive |
WC-Co | Extreme hardness | Difficult to shape |
Hastelloy C276 | Superior corrosion resistance | High cost |
NiCr 80/20 | Good high-temperature properties | Oxidation at high temperatures |
316L Stainless Steel | Good overall properties | Lower hardness |
420 Stainless Steel | High hardness | Prone to corrosion |
AlSi10Mg | Lightweight, good thermal properties | Lower strength |
Ti6Al4V | High strength-to-weight ratio | Very expensive |
Technical Insights
Parameters, Thresholds, and Ranges:
Material | Parameter | Value | Notes |
---|---|---|---|
Inconel 625 | Melting Point | 1290-1350°C | High temperature resistance |
Cobalt 6B | Hardness | 45-55 HRC | Wear resistant |
Stellite 21 | Thermal Conductivity | 14 W/m·K | Good thermal properties |
WC-Co | Hardness | 90-92 HRA | Extremely hard |
Hastelloy C276 | Tensile Strength | 690 MPa | Strong under stress |
NiCr 80/20 | Electrical Resistivity | 1.09 µΩ·m | Conductive |
316L Stainless Steel | Density | 8.0 g/cm³ | Durable |
420 Stainless Steel | Hardness | 50 HRC | High hardness |
AlSi10Mg | Density | 2.68 g/cm³ | Lightweight |
Ti6Al4V | Tensile Strength | 895 MPa | High strength |
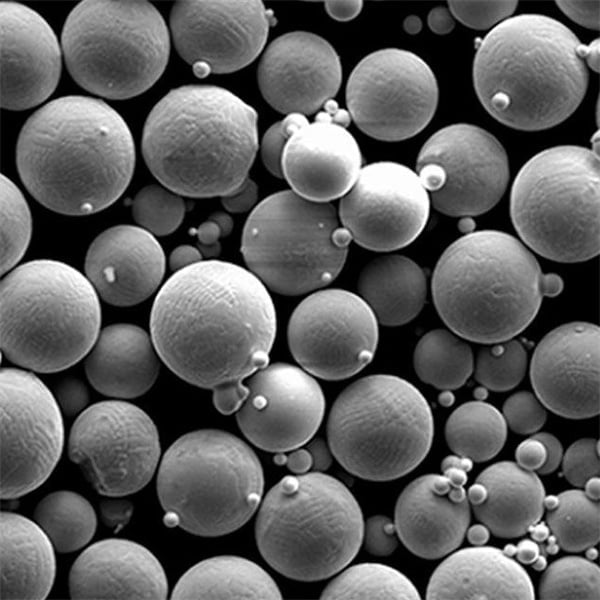
FAQ
Question | Answer |
---|---|
What is workpiece repair? | Workpiece repair is the process of restoring a damaged or worn component to its original specifications. |
Why is workpiece repair important? | It extends the lifespan of machinery, reduces downtime, and saves costs. |
What are common methods of workpiece repair? | Common methods include welding, metal powder spraying, machining, and coating. |
Which industries benefit from workpiece repair? | Automotive, aerospace, manufacturing, construction, marine, and oil and gas industries. |
What materials are used in workpiece repair? | Common materials include Inconel 625, Cobalt 6B, Stellite 21, WC-Co, Hastelloy C276, and various stainless steels. |
How do I choose the right material for repair? | Consider the application’s requirements, including strength, corrosion resistance, and cost. |
What are the advantages of using metal powders? | Metal powders offer precise application, versatility, and the ability to tailor properties. |
Are there any limitations to workpiece repair? | Some limitations include the need for skilled labor, potential changes in material properties, and cost. |
Share On
MET3DP Technology Co., LTD is a leading provider of additive manufacturing solutions headquartered in Qingdao, China. Our company specializes in 3D printing equipment and high-performance metal powders for industrial applications.
Inquiry to get best price and customized Solution for your business!
Related Articles
About Met3DP
Recent Update
Our Product
CONTACT US
Any questions? Send us message now! We’ll serve your request with a whole team after receiving your message.
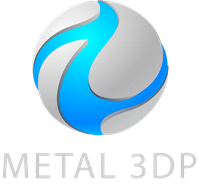
Metal Powders for 3D Printing and Additive Manufacturing