1080 grade metal powders
Table of Contents
The world of manufacturing is undergoing a revolution, with additive manufacturing (AM), also known as 3D printing, taking center stage. This transformative technology allows for the creation of complex, three-dimensional objects directly from digital models. But what fuels this revolution? Enter the unsung heroes: metal powders. Specifically, 1080 grade metal powders offer a potent combination of strength, versatility, and printability, making them ideal for crafting a wide range of structural parts.
Understanding 1080 grade metal powders
1080 refers to the minimum yield strength (in MPa) that these metal powders are guaranteed to achieve after the AM process. Imagine building a bridge – you wouldn’t want the materials to crumble under pressure, right? 1080 grade metal powders ensure your creations possess the muscle needed to handle structural loads. But strength isn’t the whole story. Let’s delve deeper with a detailed table:
Metal Powder | Composition | Key Properties | Characteristics |
---|---|---|---|
17-4 PH Stainless Steel | 17% Cr, 4% Cu, Mo, Nb | High strength, good corrosion resistance, age-hardenable | Excellent for aerospace, automotive, and medical applications |
316L Stainless Steel | 16-18% Cr, 10-14% Ni, 2-3% Mo | Excellent corrosion resistance, biocompatible | Widely used in chemical processing, marine environments, and medical implants |
Inconel 625 | 20% Cr, 25% Ni, 9% Fe, Mo, Nb | Exceptional high-temperature strength, oxidation resistance | Ideal for jet engines, gas turbines, and heat exchangers |
Maraging Steel | 18% Ni, Mo, Co, Ti | Ultra-high strength, good toughness, low distortion | Used in aerospace components, tooling, and weapon systems |
Aluminum Alloy 6061 | 95.5% Al, Mg, Si, Cu | Good strength-to-weight ratio, excellent machinability | Popular choice for automotive parts, electronics enclosures, and building materials |
Aluminum Alloy 7075 | 90% Al, Zn, Mg, Cu | High strength-to-weight ratio, good fatigue resistance | Used in aircraft structures, sporting goods, and high-performance applications |
Titanium Alloy Ti-6Al-4V | 90% Ti, 6% Al, 4% V | Excellent strength-to-weight ratio, good corrosion resistance | Crucial for aerospace components, biomedical implants, and marine applications |
Nickel Alloy 201 | 99% Ni | Highly ductile, good electrical conductivity | Used in electronics components, heat sinks, and chemical processing equipment |
Copper | 99.9% Cu | Excellent electrical conductivity, good thermal conductivity | Ideal for electrical conductors, heat exchangers, and decorative applications |
Inconel 718 | 50% Ni, 18% Cr, Nb, Mo | High strength, good creep resistance at high temperatures | Valuable for aerospace components, gas turbines, and molds |
Understanding the Table:
- Composition: This column lists the primary elements present in each metal powder.
- Key Properties: This section highlights the most important characteristics of each powder, such as strength, corrosion resistance, and printability.
- Characteristics: This column describes some of the typical applications where these powders shine.
Choosing the Right Powder:
Selecting the perfect 1080 grade metal powders depends on your project’s specific needs. Think of it like picking the right tool for the job. For instance, if you’re constructing a lightweight aircraft component, aluminum alloy 7075 might be ideal due to its exceptional strength-to-weight ratio. On the other hand, if you’re building a chemical processing tank that needs to withstand harsh environments, 316L stainless steel would be a better choice due to its superior corrosion resistance.
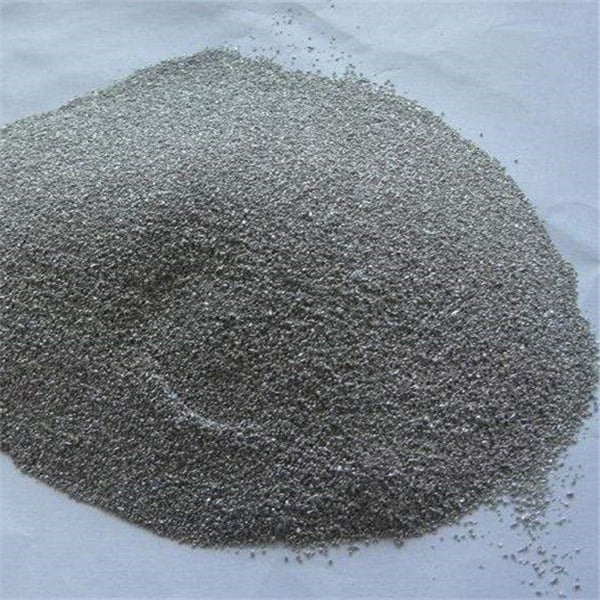
Applications of 1080 grade metal powders
The realm of possibilities for 1080 metal powders is vast. Here’s a glimpse into some of the exciting applications:
Application Area | Specific Examples | Benefits of Using 1080 Powders |
---|---|---|
Aerospace | Lightweight aircraft structures, engine components, landing gear | High strength-to-weight ratio, excellent fatigue resistance, allows for complex geometries |
Automotive | Customizable engine parts, lightweight chassis components, | Design freedom for weight reduction and improved performance, reduced material waste compared to traditional machining |
Medical | Biocompatible implants, custom prosthetics, surgical instruments | Excellent corrosion resistance for biocompatibility, allows for personalized design for improved patient outcomes |
Oil & Gas | Corrosion-resistant pipes, valves, and downhole tools | High strength can withstand extreme pressure environments, improved safety and reliability |
Consumer Products | Sporting goods components, customized bike frames, | Lightweight and strong materials for enhanced performance, potential for on-demand manufacturing and personalization |
Tooling | Complex jigs and fixtures, customized molds for rapid prototyping | High strength for durability, allows for intricate designs that traditional methods struggle with |
Beyond the Applications: The true potential of 1080 powders lies not just in their ability to create individual parts, but in revolutionizing entire manufacturing processes. Imagine a world where complex components are built layer-by-layer, on-demand, with minimal waste. This is the future that 1080 powders are helping to shape.
Advantages and Limitations of 1080 Metal Powders
Every technology has its pros and cons, and 1080 metal powders are no exception. Let’s explore both sides of the coin:
Advantages:
- High Strength: 1080 powders deliver exceptional strength, making them suitable for structural applications. Think of them as the building blocks for robust, reliable parts.
- Design Freedom: Unlike traditional subtractive manufacturing (cutting away material), AM allows for intricate designs and internal features that were previously impossible. Imagine intricate channels within a lightweight part – this becomes a reality with 1080 powders.
- Lightweighting: Several 1080 powders, like aluminum alloys, offer a fantastic strength-to-weight ratio. This translates to lighter components in industries like aerospace and automotive, leading to improved fuel efficiency and performance.
- Reduced Waste: Traditional manufacturing often generates significant scrap material. AM with 1080 powders utilizes only the necessary material, minimizing waste and promoting sustainability.
- Customization: The ability to create parts on-demand with minimal setup time opens doors for customization and rapid prototyping. Imagine creating a custom bike frame that perfectly fits your body – this is a possibility with 1080 powders.
Limitations:
- Cost: Currently, AM with 1080 powders can be more expensive than traditional manufacturing methods for high-volume production. However, as technology advances and adoption increases, costs are expected to decrease.
- Build Speed: While AM offers significant advantages, it can be slower than traditional methods for large-scale production. Think of it like baking a complex cake layer-by-layer versus mass-producing cookies – there’s a trade-off in speed for intricate designs.
- Surface Finish: AM parts can have a slightly rougher surface finish compared to traditionally machined parts. However, post-processing techniques can significantly improve surface quality.
- Material Availability: While the range of 1080 powders is expanding, it’s not as vast as the selection of materials available in traditional manufacturing. This is an evolving landscape, with new options constantly being developed.
Making the Choice:
The decision to use 1080 metal powders hinges on your specific project requirements. For applications that prioritize strength, design freedom, and lightweighting, 1080 powders offer compelling advantages. However, if cost and production speed are paramount, traditional methods might still be the better fit.
Specifications, Sizes, Grades & Standards
Now that you grasp the applications and considerations, let’s delve into the nitty-gritty details:
Metal Powder Specifications:
These specifications define the physical and chemical properties of the powder, ensuring consistent performance during the AM process. Key aspects include:
- Particle Size Distribution: The size and distribution of powder particles significantly impact printability, surface finish, and mechanical properties.
- Chemical Composition: Strict adherence to specific element ratios guarantees the desired properties in the final part.
- Flowability: The powder’s ability to flow freely is crucial for even distribution during the printing process.
Powder Sizes and Grades:
1080 powders come in a range of particle sizes, typically denoted in micrometers (µm). The chosen size influences several factors:
- Printability: Finer powders (less than 50 µm) offer better detail resolution but can be challenging to flow freely. Coarser powders (above 100 µm) flow more easily but might limit the achievable surface finish.
- Mechanical Properties: Particle size can influence the final part’s strength and density. Generally, finer powders can lead to denser parts with slightly improved mechanical properties.
Powder Grades: Similar to other materials, 1080 powders come in various grades designated by industry standards. These grades specify the powder’s composition, cleanliness, and flowability characteristics. Some common standards include:
- ASTM International (ASTM): A prominent organization that sets standards for various materials, including metal powders. For example, ASTM B294 outlines the standard specification for nickel-chromium powders.
- Additive Manufacturing File Format (AMF): This file format, standardized by ASTM, allows for the exchange of 3D printing data, including information about the recommended powder for a specific application.
Understanding Safety: Metal powders can pose health risks if not handled appropriately. Always adhere to safety data sheets (SDS) provided by the powder manufacturer. These sheets outline potential hazards, recommended personal protective equipment (PPE), and proper handling procedures.
Suppliers and Pricing
The world of metal powder suppliers is constantly evolving. Here’s a roadmap to navigate this landscape:
Finding a Reputable Supplier:
- Industry Reputation: Look for suppliers with a proven track record in supplying high-quality 1080 metal powders for AM. Industry certifications and positive customer reviews can be helpful indicators.
- Material Selection: Ensure the supplier offers the specific 1080 powder type (e.g., 17-4 PH stainless steel) required for your project.
- Technical Expertise: A knowledgeable supplier can provide valuable guidance on powder selection, processing parameters, and potential challenges.
Pricing Considerations:
The cost of 1080 metal powders can vary depending on several factors:
- Material Type: Exotic or high-performance alloys like Inconel typically command a higher price compared to more common materials like steel.
- Powder Grade: Powders with tighter specifications or higher purity levels might be more expensive.
- Quantity: Bulk purchases often come with discounted pricing compared to smaller quantities.
Beyond Price: While cost is a crucial consideration, don’t solely focus on the cheapest option. Factors like consistent quality, reliable supply chains, and technical support can significantly impact your project’s success.
Comparing Popular 1080 Metal Powders
To help you navigate the diverse world of 1080 powders, let’s compare some of the most popular options across key parameters:
Metal Powder | Applications | Strengths | Limitations | Price Range (USD/kg) |
---|---|---|---|---|
17-4 PH Stainless Steel | Aerospace, automotive, medical | High strength, good corrosion resistance, age-hardenable | Requires heat treatment for optimal properties | Moderate |
316L Stainless Steel | Chemical processing, marine environments, medical implants | Excellent corrosion resistance, biocompatible | Lower strength compared to some other options | Moderate |
Inconel 625 | Jet engines, gas turbines, heat exchangers | Exceptional high-temperature strength, oxidation resistance | Expensive, higher density leads to heavier parts | High |
Maraging Steel | Aerospace components, tooling, weapon systems | Ultra-high strength, good toughness, low distortion | Requires special handling due to moisture sensitivity | High |
Aluminum Alloy 6061 | Automotive parts, electronics enclosures, building materials | Good strength-to-weight ratio, excellent machinability | Lower strength compared to some steel options | Low |
Please note: Pricing information is indicative and can fluctuate based on market conditions, supplier, and quantity.
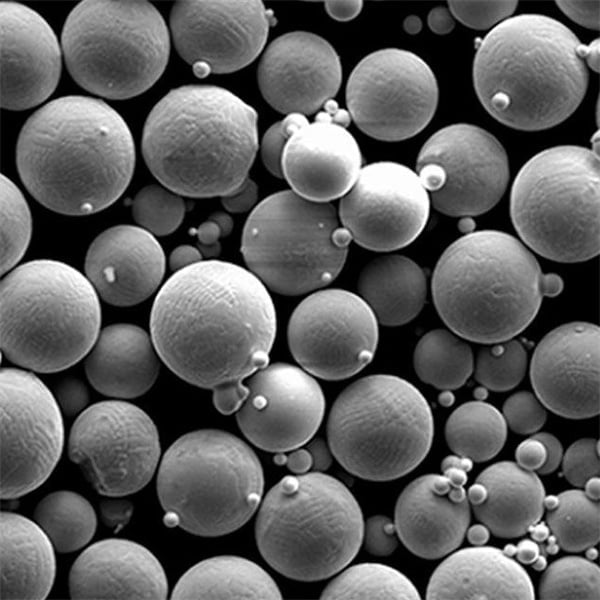
FAQ
Here are some frequently asked questions regarding 1080 metal powders:
Q: Are 1080 metal powders safe to handle?
A: Metal powders can pose health risks if inhaled. Always follow the safety data sheet (SDS) provided by the manufacturer and wear appropriate personal protective equipment (PPE).
Q: What are the environmental benefits of using 1080 metal powders?
A: Compared to traditional manufacturing methods that generate significant scrap material, AM with 1080 powders offers a more sustainable approach. By utilizing only the necessary material layer-by-layer, there’s minimal waste. Additionally, some 1080 powders, like aluminum alloys, can contribute to lighter weight vehicles, leading to reduced fuel consumption and emissions.
Q: What is the future of 1080 metal powders?
A: The future of 1080 metal powders is bright! As research and development continue, we can expect:
- Expansion of Material Selection: The variety of 1080 powders available will continue to grow, offering even more options for specific applications.
- Reduced Costs: With advancements in AM technology and increased powder production, the cost of 1080 powders is expected to decrease, making them more accessible for various industries.
- Improved Printability: Developments in powder characteristics and AM processes will lead to faster printing times and smoother surface finishes for 1080 metal parts.
- On-Demand Manufacturing: The potential for localized, on-demand manufacturing with 1080 powders could revolutionize supply chains and lead to more efficient production models.
Share On
MET3DP Technology Co., LTD is a leading provider of additive manufacturing solutions headquartered in Qingdao, China. Our company specializes in 3D printing equipment and high-performance metal powders for industrial applications.
Inquiry to get best price and customized Solution for your business!
Related Articles
About Met3DP
Recent Update
Our Product
CONTACT US
Any questions? Send us message now! We’ll serve your request with a whole team after receiving your message.
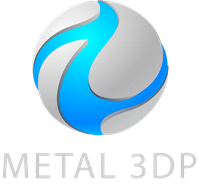
Metal Powders for 3D Printing and Additive Manufacturing