17-4PH stainless steel powder
Table of Contents
Imagine building a component that needs to be incredibly strong, resistant to corrosion, and lightweight all at the same time. Sounds like a tall order, right? Well, for those in the additive manufacturing (AM) world, this dream becomes a reality with the introduction of 17-4PH stainless steel powder specifically designed for Hot Isostatic Pressing (HIP).
This article dives deep into the world of 17-4PH for HIP, exploring its properties, applications, advantages, limitations, and various metal powder options available. We’ll equip you with the knowledge to make informed decisions about incorporating this powerhouse material into your next AM project.
the Secrets of 17-4PH: A Compositional Breakdown
17-4PH stainless steel, also known as UNS S17400, belongs to the precipitation-hardening (PH) family of stainless steels. Here’s a closer look at its key components:
Element | Weight % | Role |
---|---|---|
Chromium (Cr) | 15-17.5 | Enhances corrosion resistance |
Nickel (Ni) | 3.5-5.5 | Improves strength and ductility |
Copper (Cu) | 3-4 | Contributes to precipitation hardening |
Columbium (Cb) (Niobium (Nb)) | 0.4-1.2 | Promotes precipitation hardening |
Silicon (Si) | 1 max | Improves strength and oxidation resistance |
Manganese (Mn) | 1 max | Enhances hardenability |
Carbon (C) | 0.07 max | Crucial for precipitation hardening |
Iron (Fe) | Balance | Base metal |
This unique composition grants 17-4PH exceptional mechanical properties, making it a highly sought-after material for demanding applications.
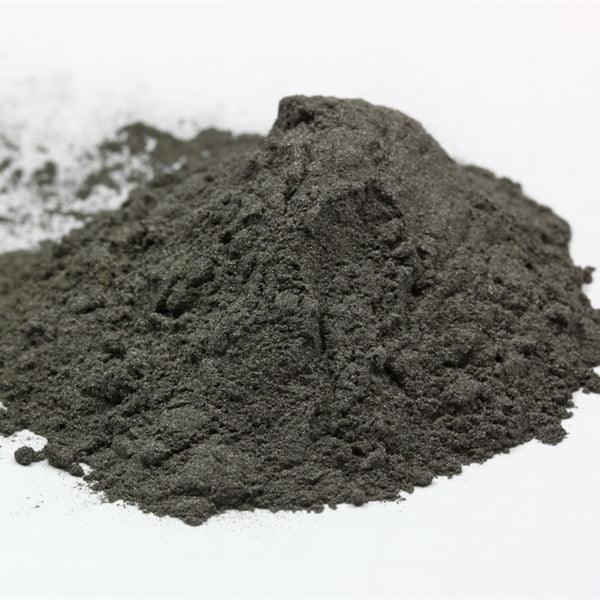
Choosing the Right Fit for Your Project
The beauty of using 17-4PH for HIP lies in the diverse range of metal powder options available. Each powder boasts slightly different characteristics, allowing you to tailor the material to your specific needs. Here’s a breakdown of ten prominent 17-4PH metal powders for HIP:
1. LPW® 17-4 PH Stainless Steel (LPW)
This gas-atomized powder offers excellent flowability and packing density, leading to high-quality builds. It’s a popular choice for aerospace, automotive, and medical applications.
2. EOS StainlessSteel 17-4PH (EOS)
EOS’s offering delivers consistent particle size distribution and spherical morphology, promoting good printability and mechanical properties. It’s well-suited for complex geometries and demanding structural parts.
3. Admatec 17-4PH (Admatec)
This nitrogen-atomized powder boasts high purity and low oxygen content, resulting in improved mechanical performance after HIP. It finds applications in the oil & gas and chemical processing industries.
4. Höganäs AM 17-4PH (Höganäs)
Höganäs’s powder is known for its exceptional flowability and laser absorption characteristics. This translates to efficient printing and consistent builds, making it ideal for high-volume production runs.
5. Carpenter Additive AM 17-4PH (Carpenter)
Carpenter’s metal powder undergoes a unique manufacturing process for enhanced cleanliness and minimal internal defects. This translates to superior mechanical properties for critical aerospace parts.
6. SLM Solutions 17-4PH (SLM Solutions)
This gas-atomized powder features a narrow particle size distribution, enabling precise control over microstructure and final part properties. It’s suitable for applications requiring high dimensional accuracy and strength.
7. Oerlikon AM 17-4PH (Oerlikon)
Oerlikon’s powder is nitrogen-atomized for improved flowability and packing density. It caters to a broad range of industries, including automotive, medical, and aerospace.
8. Element 17-4PH (Element)
This gas-atomized powder prioritizes high sphericity and flowability for optimal printability. It’s a cost-effective option for general-purpose applications in various industries.
9. AP&C 17-4PH (AP&C)
Offering a balance between cost and performance, AP&C’s powder delivers good printability and mechanical properties for less demanding applications.
10. DMG MORI 17-4PH (DMG MORI)
This gas-atomized powder caters specifically to DMG MORI’s Laser Additive Manufacturing systems.
Applications of 17-4PH stainless steel powder
The exceptional properties of 17-4PH for HIP unlock a vast array of applications across various industries. Here are some key areas where this powerful material shines:
- Aerospace: 17-4PH’s high strength-to-weight ratio, excellent corrosion resistance, and fatigue strength make it ideal for aircraft components like landing gear, engine mounts, and structural components. Compared to traditional materials like aluminum or titanium alloys, 17-4PH offers superior mechanical performance while maintaining weight efficiency, a crucial factor in fuel economy and flight range.
- Automotive: The automotive industry leverages 17-4PH for high-performance components like gears, suspension parts, and lightweight brackets. Its ability to withstand wear and tear, along with its strength, makes it a valuable asset in demanding automotive applications. When compared to heavier steel components, 17-4PH offers weight reduction benefits, contributing to improved fuel efficiency and overall vehicle performance.
- Medical: The biocompatible nature of 17-4PH, coupled with its corrosion resistance and strength, makes it suitable for various medical implants. Applications include surgical instruments, prosthetic components, and even spinal implants. Here, 17-4PH stands out compared to traditional materials like stainless steel 316L by offering superior strength-to-weight ratio, allowing for lighter implant designs that improve patient comfort and functionality.
- Oil & Gas: The oil and gas industry relies on 17-4PH for components that need to withstand harsh environments. Its resistance to corrosion and high pressures makes it ideal for downhole tools, valves, and wellhead components. Compared to some nickel-based alloys traditionally used, 17-4PH offers a cost-effective alternative while maintaining the necessary strength and corrosion resistance for these demanding applications.
- Molding & Dies: The high wear resistance and strength of 17-4PH make it a valuable material for mold inserts, tooling fixtures, and dies used in various manufacturing processes. When pitted against tool steels used in traditional applications, 17-4PH offers the potential for lighter mold designs with improved thermal conductivity, leading to faster production cycles.
Beyond these core applications, 17-4PH for HIP finds its way into various other industries, including:
- Defense & Military: Components requiring high strength-to-weight ratio and corrosion resistance.
- Consumer Goods: High-performance sporting goods and luxury watch components.
- Chemical Processing: Components that need to handle corrosive chemicals and high pressures.
The versatility of 17-4PH for HIP makes it a truly transformative material, pushing the boundaries of what’s possible in additive manufacturing.
Power & Perks: Advantages of 17-4PH for HIP
The synergy between 17-4PH and HIP offers a range of advantages that make this combination a frontrunner in AM:
- Exceptional Mechanical Properties: HIPping eliminates internal porosity within the printed part, leading to significant improvements in tensile strength, fatigue strength, and overall mechanical performance compared to non-HIPped parts. This allows for the creation of lightweight components that can withstand demanding loads.
- Enhanced Corrosion Resistance: 17-4PH boasts inherent corrosion resistance due to its chromium content. HIPping further densifies the material, minimizing pathways for corrosion initiation.
- Design Freedom & Complexity: Unlike traditional manufacturing methods, AM allows for the creation of complex geometries with internal channels and intricate features. 17-4PH’s flowability and printability make it ideal for realizing these intricate designs.
- Lightweighting Potential: The high strength-to-weight ratio of 17-4PH allows for significant weight reduction compared to traditional materials. This is particularly beneficial in applications like aerospace and automotive, where every gram saved translates to improved fuel efficiency and performance.
- Material Efficiency: AM minimizes material waste compared to traditional subtractive manufacturing techniques. This, combined with the high density achieved through HIPping, reduces overall material consumption.
Limitations of 17-4PH for HIP
While 17-4PH for HIP boasts an impressive range of benefits, it’s essential to acknowledge its limitations:
- Cost: The cost of 17-4PH metal powder and the HIPping process can be higher compared to some traditional materials and manufacturing techniques. However, the performance benefits and weight reduction potential can often offset the initial cost, especially for high-value applications.
- Part Size Limitations: Current AM build volumes limit the size of components that can be manufactured using 17-4PH. This might pose a challenge for certain large-scale applications.
- Surface Roughness: Additive manufacturing processes can result in a slightly rougher surface finish compared to some traditional techniques like machining. However, post-processing techniques like polishing or blasting can mitigate this issue.
- Material Qualification: For certain critical applications, especially in aerospace and medical sectors, extensive material qualification testing might be required to ensure the performance of 17-4PH parts produced via AM and HIP.
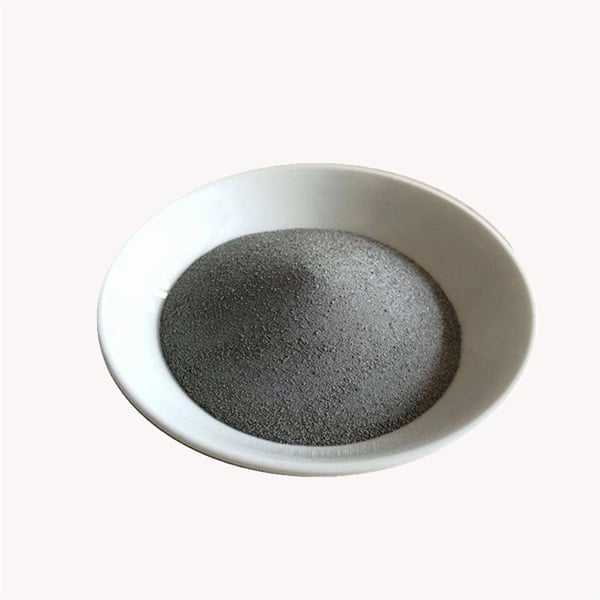
Pros vs. Cons of 17-4PH for HIP
Table: Pros and Cons of 17-4PH for HIP
Feature | Pros | Cons |
---|---|---|
Mechanical Properties | Exceptional strength, fatigue strength, and wear resistance after HIPping | May require additional post-processing for some applications |
Corrosion Resistance | Inherent corrosion resistance, further enhanced by HIPping | Cost of metal powder and HIP process can be higher |
Design Freedom | Allows for complex geometries and lightweighting | Current AM build volumes limit part size for some applications |
Material Efficiency | Minimizes material waste compared to traditional methods | Surface roughness might be higher compared to machining |
Qualification | May require extensive material qualification for critical applications | Offers a balance of performance, design flexibility, and weight savings |
Ultimately, the decision to use 17-4PH for HIP hinges on the specific application requirements and a careful evaluation of pros and cons.
Demystifying the Details: Specifications, Sizes, Grades & Standards
Here’s a breakdown of key specifications, sizes, grades, and relevant standards for 17-4PH metal powder for HIP:
Table: Specifications, Sizes, Grades & Standards for 17-4PH Metal Powder for HIP
Feature | Details |
---|---|
Material Specification | ASTM International ASTM F3055 |
Chemical Composition | Refer to table in “Unveiling the Secrets of 17-4PH” section for breakdown |
Particle Size Distribution | Varies depending on manufacturer, typically ranges from 15-45 microns |
Sphericity | High sphericity is preferred for optimal flowability and printability |
Flowability | Crucial for even powder spreading and layer formation during printing |
Apparent Density | Typically ranges from 4.6 to 5.0 g/cm³ |
Grades | Available in Condition H1150 (solution annealed) and Condition H1025 (aged) |
Standards | May comply with various industry standards like AMS and NADCAP |
Note: This table provides a general overview. Specific details regarding powder specifications and certifications might vary depending on the manufacturer.
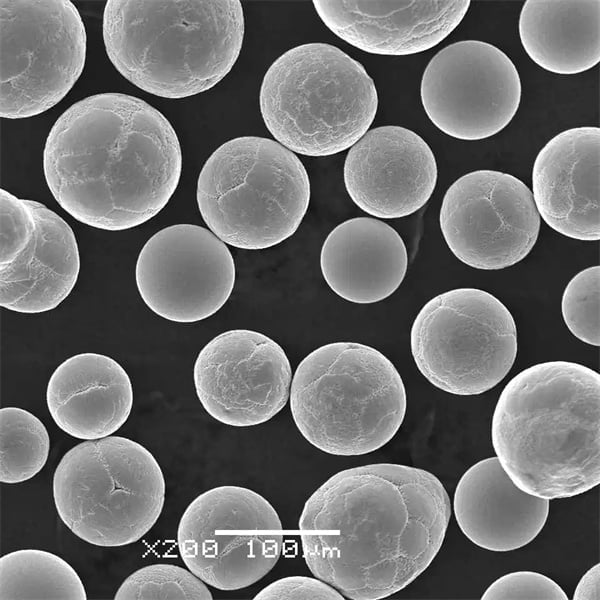
Suppliers & Pricing of 17-4PH Metal Powder for HIP
Several leading metal powder suppliers offer 17-4PH specifically designed for HIP applications. Here are some prominent players (in no particular order):
- LPW
- EOS GmbH
- Admatec GmbH
- Höganäs AB
- Carpenter Additive
- SLM Solutions GmbH
- Oerlikon AM
- Element Materials Technology
- AP&C Copper Additive
- DMG MORI Co., Ltd.
Pricing: The cost of 17-4PH metal powder for HIP can vary depending on the manufacturer, particle size distribution, and order quantity. Generally, expect a higher price point compared to some other metal powders due to the alloying elements and specialized manufacturing processes involved.
It’s important to consult with individual metal powder suppliers for current pricing information and specific quotes.
FAQ
Table: Frequently Asked Questions about 17-4PH for HIP
Question | Answer |
---|---|
What are the benefits of using HIP with 17-4PH? | HIPping eliminates internal porosity, leading to significant improvements in mechanical properties, corrosion resistance, and overall part quality. |
How does 17-4PH for HIP compare to traditional manufacturing methods? | AM with 17-4PH offers design freedom, potential for lightweighting, and reduced material waste compared to subtractive manufacturing techniques. However, cost and part size limitations might need to be considered. |
What are some typical applications for 17-4PH for HIP? | Aerospace, automotive, medical, oil & gas, molding & dies, and various other industries requiring high-performance components. |
What factors should I consider when choosing a metal powder supplier for 17-4PH for HIP? | Consider factors like powder specifications, certifications, pricing, and the supplier’s reputation and experience in the AM |
Share On
MET3DP Technology Co., LTD is a leading provider of additive manufacturing solutions headquartered in Qingdao, China. Our company specializes in 3D printing equipment and high-performance metal powders for industrial applications.
Inquiry to get best price and customized Solution for your business!
Related Articles
About Met3DP
Recent Update
Our Product
CONTACT US
Any questions? Send us message now! We’ll serve your request with a whole team after receiving your message.
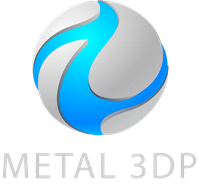
Metal Powders for 3D Printing and Additive Manufacturing