Production of 3D printed metal powder using Electrolysis method
Table of Contents
Imagine sculpting intricate metal objects with the precision of a laser and the versatility of a digital blueprint. This is the magic of 3D printed metal powder, and at the heart of this revolutionary technology lies a crucial ingredient: metal powder. But how do we transform raw materials into these tiny, high-performance particles? Enter the electrolysis method, a process that harnesses the power of electricity to create high-purity metal powders specifically designed for 3D printing.
The Production Process of Electrolytic 3D printed metal powder
The electrolysis method operates on the fundamental principle of separating elements from a compound using an electric current. Here’s a breakdown of the key steps involved:
- Electrolyte Preparation: A specialized solution, called the electrolyte, is prepared. This solution contains dissolved metal ions (positively charged atoms) and usually consists of a metal salt and a conductive agent.
- Electrode Setup: Two electrodes, an anode (positive) and a cathode (negative), are immersed in the electrolyte. The anode is typically made of an inert material like platinum, while the cathode can be the desired metal itself or an inert material coated with the target metal.
- Electric Current Application: When an electric current is applied, the positively charged metal ions in the solution are attracted to the negatively charged cathode. Upon reaching the cathode, they gain electrons and transform back into neutral metal atoms, which deposit on the cathode surface.
- Powder Collection: As the process continues, the metal accumulates on the cathode, forming a dendritic (branching) structure. This structure is then broken down into fine particles using various techniques like mechanical grinding or atomization.
- Purification and Refining: The resulting metal powder may undergo additional purification steps to remove any impurities and achieve the desired level of purity and particle size distribution.
Think of it like this: Imagine a swimming pool filled with tiny, positively charged fish (metal ions) and two floating platforms (electrodes). When you turn on the pool’s filtration system (electric current), the fish are drawn towards the negatively charged platform (cathode). As they reach the platform, they lose their positive charge and take a nap (deposit as metal atoms), eventually forming a clump on the platform’s surface. This clump is then broken down into smaller fish (powder particles) for further processing.
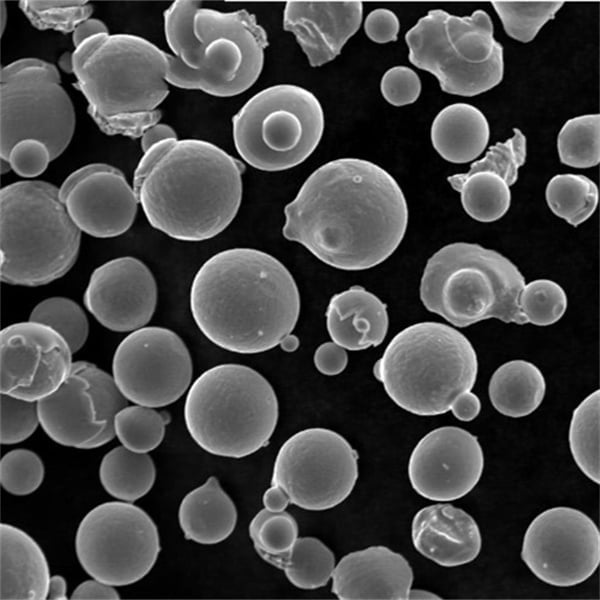
A Gallery of Electrolytic Metal Powders for 3D Printing
While the core principles of the electrolysis method remain consistent, the specific metals and their properties can vary significantly. Here’s a glimpse into some of the most fascinating metal powders crafted through electrolysis, each with unique characteristics:
1. Copper (Cu): Renowned for its exceptional thermal and electrical conductivity, copper powder finds applications in heat sinks, electrical components, and even 3D printed antennas. Its high purity and spherical shape make it a popular choice for various 3D printing techniques.
2. Titanium (Ti): Valued for its lightweight nature, high strength-to-weight ratio, and excellent biocompatibility, titanium powder paves the way for 3D printed prosthetics, implants, and aerospace components. Its resistance to corrosion and high melting point make it ideal for demanding applications.
3. Nickel (Ni): Offering a combination of strength, ductility, and corrosion resistance, nickel powder is used in diverse applications like 3D printed gears, medical devices, and chemical processing equipment. It can also be alloyed with other metals to create unique properties.
4. Stainless Steel (SS): This versatile alloy, typically a combination of iron, chromium, and nickel, boasts excellent corrosion resistance and mechanical properties. Electrolytic stainless steel powder enables the creation of 3D printed parts for food processing equipment, surgical instruments, and automotive components.
5. Aluminum (Al): Lightweight, strong, and readily recyclable, aluminum powder is well-suited for 3D printed aircraft parts, heat exchangers, and consumer electronics. Its high surface area makes it ideal for applications requiring efficient heat dissipation.
6. Cobalt-Chromium (CoCr): This biocompatible alloy exhibits exceptional wear resistance and corrosion resistance, making it a prime candidate for 3D printed dental implants, joint replacements, and surgical tools. Its high strength-to-weight ratio contributes to its suitability for demanding applications.
7. Inconel (Superalloy): Known for its exceptional performance at high temperatures, Inconel powder allows for the creation of 3D printed turbine blades, rocket engine components, and heat exchangers. Its resistance to creep (deformation under stress at high temperatures) makes it invaluable for demanding applications.
8. Tungsten (W): Renowned for its incredibly high melting point and density, tungsten powder is used in 3D printed ammunition components, radiation shielding, and high-temperature tools.
The Advantages of Electrolytic 3D printed metal powder
The electrolysis method offers several compelling advantages for the production of 3D printed metal powder compared to other methods like atomization or gas atomization:
- High Purity: Electrolysis allows for the production of metal powders with exceptionally high purity, often exceeding 99.5%. This purity is crucial for ensuring the desired mechanical properties and performance of the final 3D printed part.
- Fine and Uniform Particle Size: Electrolysis excels in producing fine and uniform particle size distributions. This characteristic is essential for achieving good flowability and packing density of the powder during the 3D printing process, ultimately leading to high-quality printed parts with smooth surface finishes.
- Controllable Particle Morphology: The process parameters in electrolysis, such as electrolyte composition and current density, can be precisely controlled to tailor the morphology (shape) of the powder particles. This level of control allows for the creation of spherical or near-spherical particles, which are ideal for optimal flowability and packing density during 3D printing.
- Environmentally Friendly: Compared to traditional methods like atomization, which can involve high temperatures and hazardous gases, electrolysis offers a more environmentally friendly approach. This is because the process operates at lower temperatures and utilizes water-based electrolytes, reducing the environmental impact.
- Scalability: The electrolysis method can be easily scaled up or down to meet production needs. This scalability makes it suitable for both small-scale research and development applications and large-scale industrial production.
Disadvantages of Preparing 3D Printed Metal Powders by Electrolysis Method
While offering significant advantages, the electrolysis method also comes with some limitations:
- Energy Consumption: The process can be energy-intensive, particularly for metals with high melting points. This can translate to higher production costs compared to some other methods.
- Limited Metal Selection: Currently, the electrolysis method is not suitable for all metals. The process works best for metals with specific electrochemical properties. Research and development are ongoing to expand the range of compatible metals.
- Slower Production Rates: Compared to methods like atomization, electrolysis generally has slower production rates. This can be a limitation for high-volume production applications.
- Process Complexity: Setting up and maintaining an electrolysis system can be more complex compared to some other methods. This complexity requires skilled personnel and specialized equipment, which can increase the overall cost.
Electrolyte Commonly Used for Preparing 3D Printed Metal Powders by Electrolysis Method
The specific electrolyte used in the electrolysis method depends on the desired metal powder. However, some common electrolytes include:
- Metal Salts: These salts, such as copper sulfate (CuSO4) for copper powder or nickel sulfate (NiSO4) for nickel powder, dissolve in water to provide the metal ions for the electrolysis process.
- Conductive Agents: These agents, often acids or bases, increase the conductivity of the electrolyte solution, allowing for efficient flow of the electric current. Examples include sulfuric acid (H2SO4) or hydrochloric acid (HCl).
- Complexing Agents: These chemicals can be added to the electrolyte to improve the stability and control the morphology of the deposited metal particles. They work by selectively binding to specific metal ions, influencing their behavior during the electrolysis process.
It’s important to note that selecting the optimal electrolyte composition requires careful consideration of factors like desired metal, purity requirements, and process efficiency.
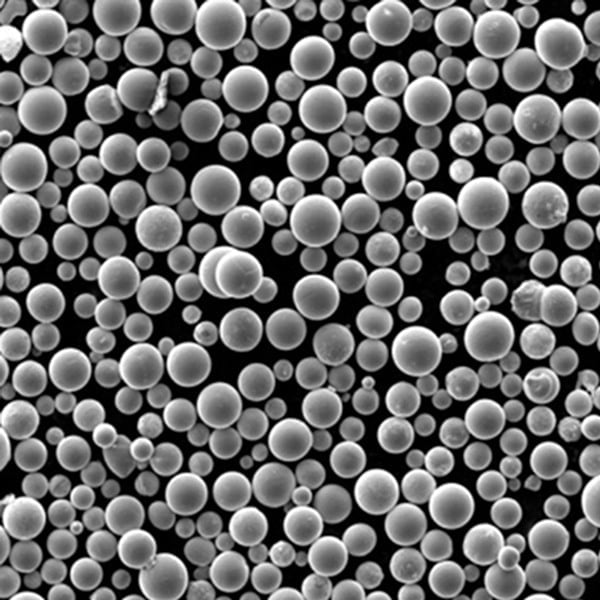
Process Parameters for Preparing 3D Printed Metal Powders Using Electrolysis Method
Several key process parameters significantly impact the quality and characteristics of the produced metal powder in the electrolysis method:
- Current Density: This parameter refers to the amount of current applied per unit area of the cathode. Higher current densities generally lead to faster deposition rates but can also result in larger and less uniform particles.
- Electrolyte Temperature: Maintaining a controlled temperature throughout the process is crucial. Too high temperatures can lead to rapid particle growth and non-uniformity, while excessively low temperatures can hinder the deposition process.
- Electrolyte Composition: As mentioned earlier, the specific composition of the electrolyte, including the type and concentration of metal salts, conductive agents, and complexing agents, significantly influences the particle morphology and purity.
- Agitation: Gentle agitation of the electrolyte solution can help ensure uniform deposition and prevent the formation of agglomerates (clumps) of metal particles.
Optimizing these parameters requires a deep understanding of the interplay between them and the desired characteristics of the final metal powder. This optimization process often involves experimentation and collaboration between engineers and scientists.
The Advantages of Electrolytic 3D Printing Metal Powders
The electrolysis method offers several compelling advantages for the production of 3D printing metal powders compared to other methods like atomization or gas atomization:
- High Purity: Electrolysis allows for the production of metal powders with exceptionally high purity, often exceeding 99.5%. This purity is crucial for ensuring the desired mechanical properties and performance of the final 3D printed part.
- Fine and Uniform Particle Size: Electrolysis excels in producing fine and uniform particle size distributions. This characteristic is essential for achieving good flowability and packing density of the powder during the 3D printing process, ultimately leading to high-quality printed parts with smooth surface finishes.
- Controllable Particle Morphology: The process parameters in electrolysis, such as electrolyte composition and current density, can be precisely controlled to tailor the morphology (shape) of the powder particles. This level of control allows for the creation of spherical or near-spherical particles, which are ideal for optimal flowability and packing density during 3D printing.
- Environmentally Friendly: Compared to traditional methods like atomization, which can involve high temperatures and hazardous gases, electrolysis offers a more environmentally friendly approach. This is because the process operates at lower temperatures and utilizes water-based electrolytes, reducing the environmental impact.
- Scalability: The electrolysis method can be easily scaled up or down to meet production needs. This scalability makes it suitable for both small-scale research and development applications and large-scale industrial production.
Disadvantages of Preparing 3D Printed Metal Powders by Electrolysis Method
While offering significant advantages, the electrolysis method also comes with some limitations:
- Energy Consumption: The process can be energy-intensive, particularly for metals with high melting points. This can translate to higher production costs compared to some other methods.
- Limited Metal Selection: Currently, the electrolysis method is not suitable for all metals. The process works best for metals with specific electrochemical properties. Research and development are ongoing to expand the range of compatible metals.
- Slower Production Rates: Compared to methods like atomization, electrolysis generally has slower production rates. This can be a limitation for high-volume production applications.
- Process Complexity: Setting up and maintaining an electrolysis system can be more complex compared to some other methods. This complexity requires skilled personnel and specialized equipment, which can increase the overall cost.
Electrolyte Commonly Used for Preparing 3D Printed Metal Powders by Electrolysis Method
The specific electrolyte used in the electrolysis method depends on the desired metal powder. However, some common electrolytes include:
- Metal Salts: These salts, such as copper sulfate (CuSO4) for copper powder or nickel sulfate (NiSO4) for nickel powder, dissolve in water to provide the metal ions for the electrolysis process.
- Conductive Agents: These agents, often acids or bases, increase the conductivity of the electrolyte solution, allowing for efficient flow of the electric current. Examples include sulfuric acid (H2SO4) or hydrochloric acid (HCl).
- Complexing Agents: These chemicals can be added to the electrolyte to improve the stability and control the morphology of the deposited metal particles. They work by selectively binding to specific metal ions, influencing their behavior during the electrolysis process.
It’s important to note that selecting the optimal electrolyte composition requires careful consideration of factors like desired metal, purity requirements, and process efficiency.
Process Parameters for Preparing 3D Printed Metal Powders Using Electrolysis Method
Several key process parameters significantly impact the quality and characteristics of the produced metal powder in the electrolysis method:
- Current Density: This parameter refers to the amount of current applied per unit area of the cathode. Higher current densities generally lead to faster deposition rates but can also result in larger and less uniform particles.
- Electrolyte Temperature: Maintaining a controlled temperature throughout the process is crucial. Too high temperatures can lead to rapid particle growth and non-uniformity, while excessively low temperatures can hinder the deposition process.
- Electrolyte Composition: As mentioned earlier, the specific composition of the electrolyte, including the type and concentration of metal salts, conductive agents, and complexing agents, significantly influences the particle morphology and purity.
- Agitation: Gentle agitation of the electrolyte solution can help ensure uniform deposition and prevent the formation of agglomerates (clumps) of metal particles.
Optimizing these parameters requires a deep understanding of the interplay between them and the desired characteristics of the final metal powder. This optimization process often involves experimentation and collaboration between engineers and scientists.
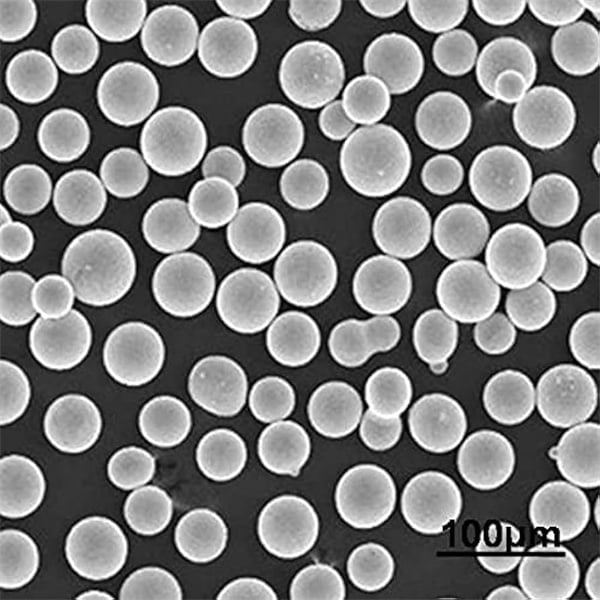
Conclusion
The field of 3D printing continues to evolve at a rapid pace, and the development of advanced powders like those produced through electrolysis is fueling this growth. While challenges like limited metal compatibility and energy consumption remain, the potential benefits of electrolysis are undeniable. As research and development efforts continue, we can expect to see advancements in:
- Expanding the range of compatible metals: Researchers are actively investigating ways to adapt the electrolysis process for a wider variety of metals, including those traditionally considered difficult to produce via this method.
- Enhancing production efficiency: Optimizing process parameters, exploring alternative electrolytes, and developing innovative reactor designs are all areas of focus to improve production rates and reduce energy consumption.
- Reducing costs: Through advancements in technology and larger-scale production, the overall cost of electrolytically produced powders is expected to decrease, making them more accessible for various applications.
These advancements, coupled with the inherent advantages of high purity, fine particle size, and precise control over morphology, position electrolytic metal powders as a powerful and versatile tool for the future of 3D printing. From intricate aerospace components to personalized medical implants, the possibilities for utilizing these powders in diverse sectors are vast and continuously expanding. As we move forward, the journey of developing and refining this technology holds immense promise for shaping the future of manufacturing and design.
Share On
MET3DP Technology Co., LTD is a leading provider of additive manufacturing solutions headquartered in Qingdao, China. Our company specializes in 3D printing equipment and high-performance metal powders for industrial applications.
Inquiry to get best price and customized Solution for your business!
Related Articles
About Met3DP
Recent Update
Our Product
CONTACT US
Any questions? Send us message now! We’ll serve your request with a whole team after receiving your message.
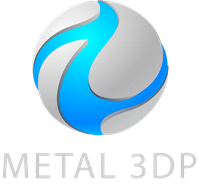
Metal Powders for 3D Printing and Additive Manufacturing