3D printed metal powders: How to control the particle size and shape
Table of Contents
Imagine building intricate metal structures layer by layer, with unparalleled design freedom and complex geometries. This isn’t science fiction; it’s the reality of 3D metal printing, a revolutionary technology transforming countless industries. But at the heart of this magic lies a crucial element: metal powder. The size and shape of these tiny particles significantly impact the quality, functionality, and printability of the final product. So, buckle up as we delve into the fascinating world of controlling particle size and shape in 3D printed metal powders!
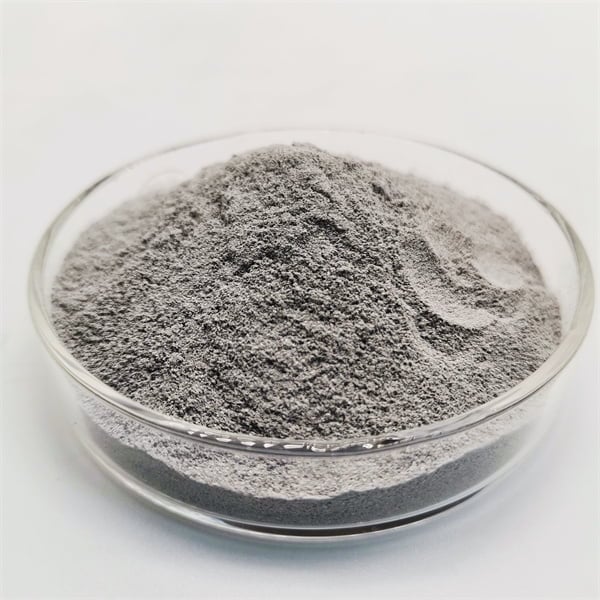
The Influence of Particle Size and Shape
Think of metal powder like the building blocks of your 3D printed masterpiece. Just like bricks come in various sizes and shapes, metal powder particles also exhibit a range of characteristics. Here’s how these properties influence the printing process and the final outcome:
- Particle Size: Imagine pouring sand versus pebbles. Finer particles, typically ranging from 15 to 100 micrometers, flow more smoothly, enabling precise layering during printing. This translates to intricate details and a smooth surface finish on the final product. However, excessively fine particles can clump together, hindering flow and potentially causing printing defects. Conversely, larger particles (think coarse sand) might not pack densely enough, leading to weak spots and a rougher surface finish.
- Particle Shape: Spherical particles are the gold standard for 3D printing. They flow effortlessly, ensuring a consistent and even distribution during printing. Imagine marbles rolling compared to oddly shaped rocks getting stuck. Non-spherical particles can create voids, impacting the final product’s density and strength. Additionally, sharp edges on irregular particles can increase wear and tear on the printing equipment.
The Balancing Act: Achieving the Perfect Harmony
The ideal scenario involves a balanced approach. We want a narrow particle size distribution, with most particles falling within a specific size range. This ensures consistent flow and packing during printing. Additionally, spherical or near-spherical particles are highly desirable for optimal results.
Here’s an analogy: Imagine building a sandcastle. A mix of fine and coarse sand allows for intricate details and overall stability. However, throwing in large pebbles disrupts the structure and weakens the final product. Similarly, in 3D metal printing, the right balance of particle size and shape is key to achieving exceptional results.
3D printed metal powder for Controlling the Particle Size
Creating metal powders with the desired size distribution involves a multi-step process. Let’s explore some of the most common techniques:
- Atomization: This method involves melting the target metal and rapidly breaking it down into tiny droplets using high-pressure gas or water jets. The size of the droplets can be controlled by adjusting factors like the melt temperature and gas/water pressure. Rapid solidification of these droplets creates the metal powder.
- Milling: Here, larger metal particles are subjected to a grinding or crushing process using high-energy mills. This technique refines the particle size and can also influence the particle shape to a certain extent.
- Classification: Once the initial powder is produced, it undergoes classification to achieve a narrow size distribution. Techniques like sieving and air classification separate particles based on their size, allowing for the selection of the desired powder fraction.
Methods for Controlling the Shape of Metal Powder in 3D Printing
While achieving perfectly spherical particles remains a challenge, several methods can influence the shape to a significant degree:
- Atomization Techniques: Modifying the parameters used in atomization, such as gas flow patterns and nozzle design, can influence the final shape of the particles. Techniques like Rapid Solidification (RS) can promote the formation of more spherical particles.
- Shot Peening: This post-processing technique involves bombarding the metal powder with small spherical media. The impact deforms the particles slightly, promoting a more spherical shape and smoother surface.
- Chemical Methods: Certain chemical treatments can be employed to selectively etch away specific facets of the particles, nudging them towards a more spherical form.
The Evolving Landscape: Advancements in Powder Production
The field of metal powder production for 3D printing is constantly evolving. Researchers are exploring novel techniques like gas-atomized molten metal deposition (GAMMD) and laser-induced breakdown in liquids (LIBD) to achieve tighter control over particle size and shape. Additionally, advancements in characterization techniques like laser diffraction and image analysis enable more precise monitoring and control of powder properties.
Choosing the Right Metal Powder for Your Project
With a diverse range of metal powders available, selecting the optimal choice depends on several factors:
- The metal type: Different metals have varying melting points and flow characteristics, influencing the choice of powder.
- The desired properties of the final product (continued): Need exceptional strength? Go for a powder known for its high density, often achieved with a narrower particle size distribution and more spherical shapes. Conversely, if surface finish is paramount, a slightly larger particle size with a smoother morphology might be preferable.
- The 3D printing technology: Different 3D printing processes have varying requirements for powder properties. For instance, techniques like Laser Beam Melting (LBM) can handle a wider range of particle sizes compared to Selective Laser Sintering (SLS), which benefits from finer and more spherical powders.
Beyond the Basics: Additional Considerations
While particle size and shape are crucial factors, other powder characteristics also play a role:
- Flowability: The powder’s ability to flow freely and consistently through the printing system is essential for smooth operation and precise layering. Spherical particles generally exhibit better flowability.
- Apparent Density: This refers to the bulk density of the powder, impacting the amount of material used per unit volume in the printed part. Higher apparent density can be advantageous for certain applications.
- Chemical Composition: The presence of impurities or oxides in the powder can affect the final product’s properties, such as its mechanical strength and corrosion resistance.
A Collaborative Approach: Working with Powder Manufacturers
Given the complexities involved, successful 3D metal printing often involves collaboration between end-users and powder manufacturers. Experienced manufacturers can offer valuable insights into powder selection based on your specific project requirements and the chosen 3D printing technology. They can also provide characterization data on their powders, including particle size distribution, shape analysis, and flowability measurements.
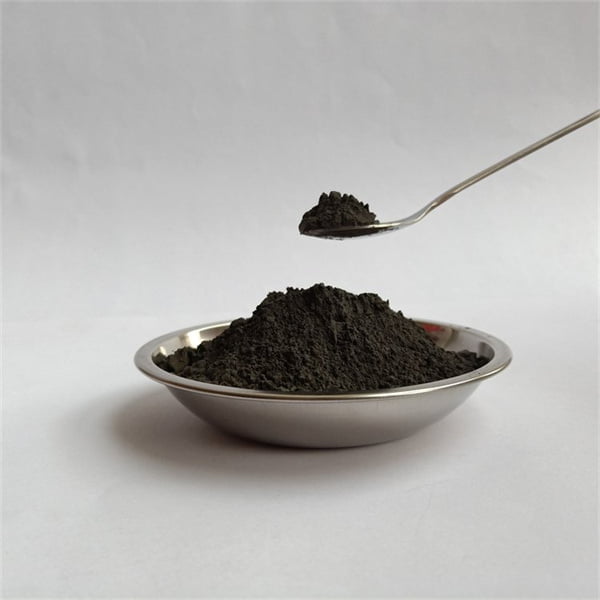
FAQs
Here are some frequently asked questions regarding 3D printed metal powder, presented in a clear and concise table format:
Question | Answer |
---|---|
What is the typical size range for metal powders used in 3D printing? | Typically, metal powders for 3D printing range from 15 to 100 micrometers in size. |
Why are spherical particles preferred for 3D printing? | Spherical particles offer superior flowability, leading to consistent powder deposition and improved surface finish in the final product. |
What are some methods used to control particle size in metal powders? | Atomization, milling, and classification are common techniques used to achieve the desired particle size distribution. |
How can the shape of metal powder particles be influenced? | Modifying atomization parameters, shot peening, and certain chemical treatments can influence the shape of metal powder particles. |
What factors should be considered when choosing a metal powder for 3D printing? | The type of metal, desired properties of the final product, and the specific 3D printing technology are all crucial factors to consider. |
What additional properties of metal powder are important for 3D printing? | Flowability, apparent density, and chemical composition also play a role in successful 3D printing. |
The Future of Metal Powders
As the field of 3D metal printing continues to evolve, advancements in powder production techniques will unlock a world of possibilities. Finer powders with near-perfect sphericity, along with the development of novel materials, promise to push the boundaries of what’s achievable. Imagine printing intricate components with exceptional strength and conductivity, or even printing structures with functionally graded properties – the possibilities are truly endless.
This journey into the world of metal powders for 3D printing highlights the intricate relationship between these tiny particles and the remarkable world of 3D-printed metal objects. By understanding how particle size and shape influence the printing process and the final product, we can unlock the full potential of this transformative technology.
Share On
MET3DP Technology Co., LTD is a leading provider of additive manufacturing solutions headquartered in Qingdao, China. Our company specializes in 3D printing equipment and high-performance metal powders for industrial applications.
Inquiry to get best price and customized Solution for your business!
Related Articles
About Met3DP
Recent Update
Our Product
CONTACT US
Any questions? Send us message now! We’ll serve your request with a whole team after receiving your message.
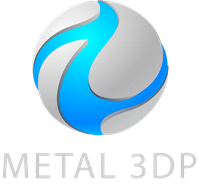
Metal Powders for 3D Printing and Additive Manufacturing