3D printed metal powders
Table of Contents
Imagine crafting intricate metal objects with unparalleled precision, layer by layer, from the comfort of your workshop. This isn’t science fiction; it’s the revolutionary world of 3D printing with metal powders. But what exactly are these metal powders, and how do they transform into stunning and functional metal parts? Buckle up, because we’re about to embark on a journey into the fascinating world of 3D printed metal powders!
Different 3D Printing Processes Have Different Requirements for 3D printed metal powders
Not all 3D printers are created equal, and the same goes for metal powders. The type of 3D printing process you’re using will dictate the specific requirements for your metal powder. Here are two of the most common methods:
- Selective Laser Melting (SLM): This high-powered laser technology precisely melts specific regions of the metal powder bed, fusing them together to build the desired object. SLM requires metal powders with exceptional flowability – the ability to move freely – to ensure smooth layer formation. Additionally, the powder particles need a spherical shape for optimal packing density and laser absorption.
- Electron Beam Melting (EBM): This powerhouse technology utilizes an electron beam in a vacuum chamber to melt the metal powder. EBM offers a wider process window compared to SLM, meaning it can handle a slightly broader range of powder properties. However, EBM still benefits from powders with good flowability and a high melting point to withstand the intense electron beam.
Think of it this way: Imagine building a sandcastle. Fine, well-distributed sand particles (like our metal powders with good flowability) make it easier to construct intricate shapes.
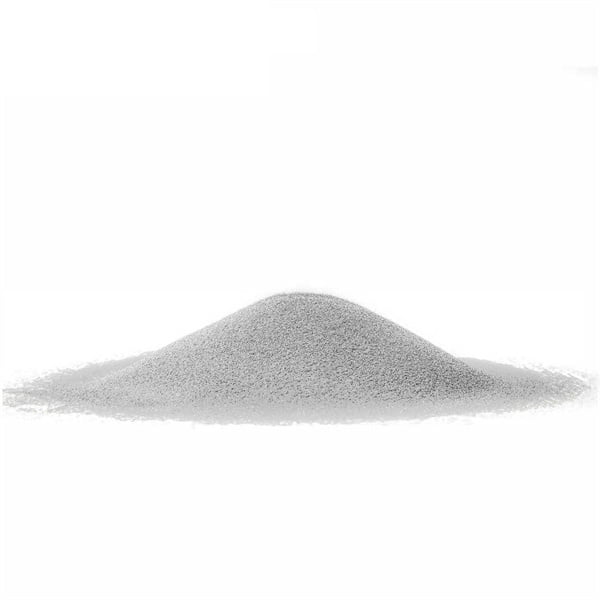
Different Applications Have Different Requirements for the Performance of Metal Materials
The purpose of your 3D printed object will significantly influence the type of metal powder you choose. Here’s a breakdown of some key considerations:
- Strength and Durability: For parts that need to withstand high stress, like aerospace components or engine parts, metal powders with high tensile strength and fatigue resistance are crucial. Alloys like Titanium (Ti64) and Inconel 718 are popular choices for their exceptional strength-to-weight ratio.
- Corrosion Resistance: Objects exposed to harsh environments, such as marine components or medical implants, require metal powders with excellent corrosion resistance. Stainless steel 316L is a go-to option due to its superior resistance to rust and other forms of corrosion.
- Biocompatibility: For applications in the medical field, like dental implants or prosthetics, biocompatibility is paramount. Metal powders like Cobalt-Chrome (CoCr) are often used because they are well-tolerated by the human body.
In essence, you’re selecting the right tool for the job. Building a bridge requires strong, durable materials, while crafting jewelry might prioritize aesthetics over sheer strength.
There’s a Symphony of Properties in Metal Powders
Metal powders for 3D printing are not just randomly ground-up bits of metal. They are meticulously crafted with specific properties in mind. Here are some key characteristics that influence the printability and performance of the final object:
- Particle Size and Distribution: The size and distribution of the metal powder particles significantly impact the resolution and surface finish of the printed object. Finer powders generally create smoother surfaces but may be more challenging to work with due to flowability issues. Conversely, larger particles offer better flowability but can result in a rougher surface finish.
- Particle Morphology: The shape of the metal powder particles also plays a crucial role. Spherical particles offer superior flowability and packing density, leading to more consistent printing results. Irregularly shaped particles, while printable, can sometimes hinder flow and lead to inconsistencies in the printed object.
- Chemical Composition: The specific elements and their ratios within the metal powder determine the final properties of the printed object. Alloys are a prime example, combining different metals to achieve a unique blend of strength, corrosion resistance, and other desired traits.
- Powder Flowability: As mentioned earlier, good flowability is essential for smooth layer formation during the printing process. Powders that flow freely ensure consistent material distribution and minimize printing defects.
Imagine these properties as the ingredients in a recipe. The right combination creates a perfectly printed metal masterpiece, while the wrong mix can lead to a printing disaster.
Advantages and Disadvantages of Different Metal Powders
No single metal powder reigns supreme. Each type offers distinct advantages and disadvantages that need to be weighed against your specific project requirements. Here’s a closer look at some common choices:
- Stainless Steel 316L:
- Advantages: Excellent corrosion resistance, good biocompatibility, readily available, relatively inexpensive.
- Disadvantages: Moderately high melting point compared to some other options, may not be the strongest choice for high-stress applications.
- Titanium (Ti64):
- Advantages: Exceptionally high strength-to-weight ratio, excellent corrosion resistance, biocompatible.
- Disadvantages: Relatively high cost, higher melting point compared to steel, can be more challenging to print due to its reactive nature.
- Inconel 718:
- Advantages: Exceptional strength and high-temperature resistance, good corrosion resistance.
- Disadvantages: Very high cost, challenging to print due to its high melting point, may require specific post-processing techniques.
- Cobalt-Chrome (CoCr):
- Advantages: Excellent biocompatibility, high wear resistance, good corrosion resistance.
- Disadvantages: Can be brittle compared to some other options, may require specific post-processing techniques.
Choosing the right metal powder is like picking the perfect paint color for your masterpiece. You consider factors like durability, compatibility with the environment, and the overall look you’re trying to achieve.
How Metal Powders are Born
Metal powders for 3D printing aren’t your average playground sand. They undergo a meticulous production process to achieve the desired properties. Here’s a glimpse into their journey:
- Atomization: This is where the magic begins. Molten metal is broken down into tiny droplets using various techniques like gas atomization or water atomization. The method used influences the size, shape, and surface characteristics of the resulting powder particles.
- Classification: Not all the metal droplets are created equal. After atomization, the powder is classified to achieve a desired particle size distribution. This ensures consistent flowability and printing results.
- Spheroidization: While some processes naturally produce near-spherical particles, others may require an additional step called spheroidization. This process refines the powder morphology, further enhancing flowability and packing density.
- Powder Analysis: Before hitting the shelves (or rather, the printers), the metal powder undergoes rigorous quality control checks. These checks analyze factors like particle size distribution, chemical composition, and flowability to ensure the powder meets the required specifications.
Think of it like baking a cake. You need the right ingredients (the molten metal), precise techniques (atomization), and quality checks (powder analysis) to achieve a perfect final product (the metal powder).
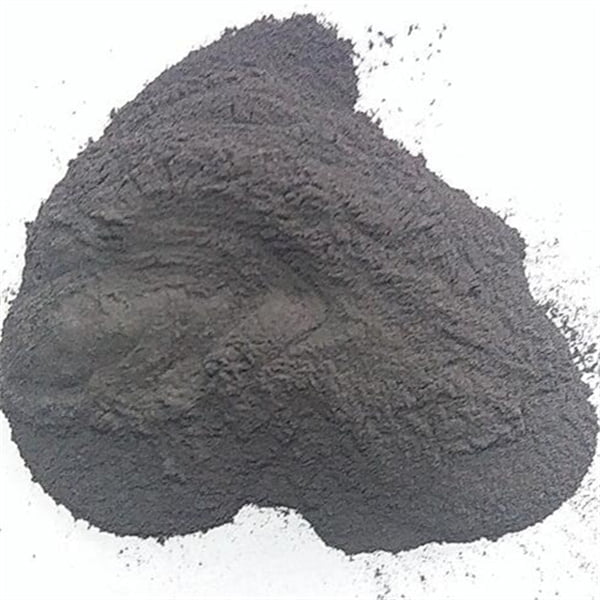
A Peek into the Price Tag of Metal Powders
The price of metal powders can vary significantly depending on several factors. Here are some key influencers:
- Material Cost: The base metal itself plays a big role. Exotic or high-performance alloys like Inconel 718 will naturally be more expensive than common materials like steel.
- Production Complexity: The production methods used to create the powder can also impact the cost. Powders requiring additional processing steps, like spheroidization, may be more expensive.
- Powder Purity: The higher the purity of the metal powder, the more it will cost. Powders with minimal impurities offer superior printability and performance.
- Supply and Demand: Basic economic principles apply here. Powders in high demand or with limited availability will generally carry a higher price tag.
The cost of metal powders can range from a few dollars per pound for common steel powders to hundreds of dollars per pound for exotic alloys. Remember, the cost of the powder is just one piece of the puzzle. The overall cost of your 3D printed metal part will also factor in printing time, post-processing requirements, and machine depreciation.
FAQ
Here are some of the most common questions people have about 3D printed metal powders, answered in a clear and concise format:
Question | Answer |
---|---|
What are the different types of metal powders used in 3D printing? | Common types include Stainless Steel 316L, Titanium (Ti64), Inconel 718, and Cobalt-Chrome (CoCr). Each offers unique advantages and disadvantages depending on the application. |
What factors influence the choice of metal powder for 3D printing? | The desired properties of the final object, such as strength, corrosion resistance, biocompatibility, and cost, all play a role in selecting the most suitable metal powder. |
How are metal powders for 3D printing produced? | Metal powders undergo a multi-step process typically involving atomization, classification |
Share On
MET3DP Technology Co., LTD is a leading provider of additive manufacturing solutions headquartered in Qingdao, China. Our company specializes in 3D printing equipment and high-performance metal powders for industrial applications.
Inquiry to get best price and customized Solution for your business!
Related Articles
About Met3DP
Recent Update
Our Product
CONTACT US
Any questions? Send us message now! We’ll serve your request with a whole team after receiving your message.
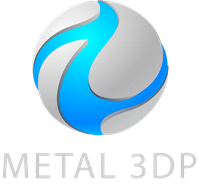
Metal Powders for 3D Printing and Additive Manufacturing