Storage and processing of 3D printed metal powders
Table of Contents
Imagine crafting intricate metal objects with unparalleled precision, layer by layer, from the comfort of your workshop. That’s the magic of 3D printed metal powders! But before these tiny metallic grains transform into awe-inspiring creations, they require meticulous storage and processing. Just like a gourmet chef needs the finest ingredients and careful preparation to create a masterpiece, high-quality 3D printed metal parts depend on the proper handling of these metal powders.
Storage of 3D Printed Metal Powders
Metal powders for 3D printing are no ordinary dust bunnies. These fine particles, often composed of reactive metals like titanium, stainless steel, or aluminum, are susceptible to environmental foes. Let’s delve into the critical aspects of metal powder storage:
- Moisture, Moisture Everywhere: Think of metal powders as tiny sponges. They readily absorb moisture from the air, which can lead to oxidation (think rust) and clumping. Imagine trying to build a smooth, strong structure with lumpy, damp sand! To combat this, metal powders are stored in desiccators, which are essentially airtight containers with moisture-absorbing materials like silica gel. These act like tiny moisture vacuums, keeping the environment around the powder nice and dry.
- Heatstroke for Powders? Absolutely! Just like we wouldn’t leave chocolate bars in a hot car (melty mess, anyone?), extreme heat can wreak havoc on metal powders. High temperatures can alter the flow properties of the powder, making it difficult for the 3D printer to lay down smooth, even layers. This can lead to weak and potentially defective parts. So, cool, dry storage areas are a must for these metallic marvels.
- Light Can Be Deceiving: Metal powders, particularly those containing reactive elements like magnesium, can be sensitive to light. Exposure to light can trigger unwanted chemical reactions, affecting the powder’s performance during printing. Imagine a once vibrant paint fading in the sunlight – that’s the kind of negative impact light can have on some metal powders. To prevent this, metal powders are typically stored in opaque containers or nitrogen-inerted environments, where light is excluded or minimized.
- The Importance of Proper Packaging: Metal powders are often hefty, and their fine particles can be easily airborne. Imagine flour dust billowing everywhere – not ideal for a clean and safe work environment! To ensure safe handling and prevent contamination, metal powders are typically sold in sealed metal containers or multi-layered plastic bags with inert gas purging. These packaging solutions keep the powders secure and minimize the risk of exposure to air and moisture.
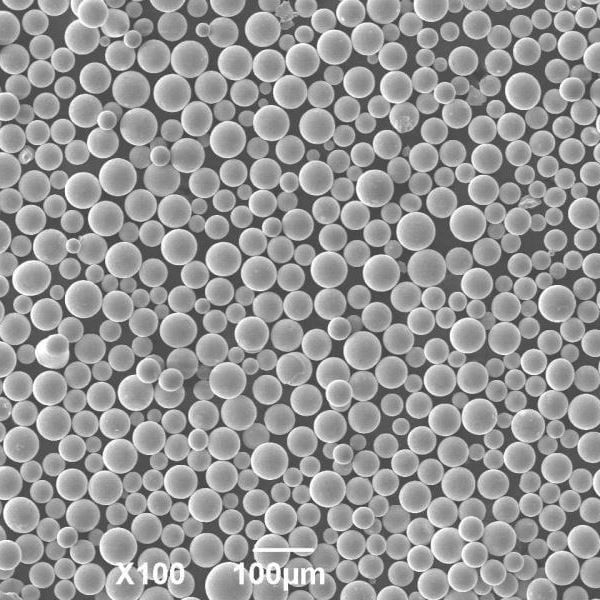
Processing of 3D Printed Metal Powders
Once stored correctly, the metal powders are ready for the printing process. But there’s still some work to be done! Here’s a closer look at the key processing steps involved:
- Preheating the Powder Bed: Think of a cake batter needing to be at the right temperature for even baking. Similarly, for optimal printing, the metal powder bed needs to be preheated to a specific temperature depending on the material. This ensures proper flow and bonding of the powder particles during the printing process. Imagine trying to build a snowman with lukewarm snow – it just wouldn’t hold its shape!
- Spreading the Powder: The magic of 3D printing lies in the precise application of the metal powder. A layer of powder is meticulously spread across the preheated bed using a recoater blade or a roller mechanism. This creates a smooth, even surface for the printer to “draw” on with the laser or other energy source, building the object layer by layer.
- The Printing Process: Depending on the specific 3D printing technology employed (e.g., Selective Laser Melting (SLM), Electron Beam Melting (EBM)), a focused energy source like a laser beam or electron beam selectively melts the powder particles in each layer, following the digital design. Imagine using a hot pen to meticulously draw and connect tiny metallic dots to create a 3D structure – that’s the essence of the printing process!
- Post-Processing: Freshly printed metal parts might require some additional TLC before they’re ready for use. This could involve support structure removal (if used during printing), heat treatment for improved mechanical properties, and surface finishing for aesthetic or functional purposes. Think of it like the final touches a baker gives to a cake – frosting, sprinkles, the whole shebang!
Some Specific Storage and Processing Methods for 3D Printed Metal Powders
The world of 3D printing is vast, and so are the storage and processing methods for metal powders. Here are a few noteworthy examples:
- Inert Gas Environments: For highly reactive metal powders like titanium, storing them in an inert gas environment like argon or nitrogen is crucial. These gases are non-reactive and help displace oxygen and moisture, preventing oxidation and ensuring optimal powder performance. Imagine submerging your precious metals in a protective bubble – that’s what inert gas environments do!
- Moisture Management Systems: Some advanced storage units for metal powders incorporate moisture management systems. These systems continuously monitor and regulate the humidity levels within the container, ensuring the powder stays consistently dry. Think of them as tiny air conditioners specifically designed for metal powders!
- Automated Powder Handling Systems: In large-scale 3D printing operations, automated powder handling systems come into play. These systems automate the entire process of transferring metal powder from storage containers to the printer bed, minimizing operator exposure and ensuring consistent powder flow. Imagine a robotic arm meticulously scooping and delivering the perfect amount of powder for each print job – that’s the power of automation!
Advantages and Considerations of Different Storage and Processing Methods
The choice between various storage and processing methods depends on several factors, including:
- Metal powder type: Highly reactive powders like titanium require more stringent storage conditions compared to less reactive materials like stainless steel.
- 3D printing technology: Different printing technologies might have specific requirements for powder preheating, layer thickness, or post-processing techniques.
- Production scale: Large-scale printing operations might necessitate automated powder handling systems for efficiency and safety.
- Cost: Inert gas environments and advanced moisture management systems offer superior protection but come at a higher cost compared to basic desiccators.
The Importance of Safety
Metal powders can pose safety hazards, especially when airborne. Here are some crucial safety considerations:
- Personal Protective Equipment (PPE): When handling metal powders, wear appropriate PPE like gloves, safety glasses, and respirators to minimize inhalation risks. Safety first, always!
- Proper Ventilation: Ensure adequate ventilation in your workspace to prevent the accumulation of airborne metal particles. Think of opening windows or using dedicated ventilation systems to keep the air clean.
- Training and Awareness: Anyone working with metal powders should undergo proper training on safe handling procedures and potential health risks. Knowledge is power, especially when it comes to safety!
Common Challenges and Troubleshooting
Even with proper storage and processing, there can be occasional hiccups. Here are some common challenges and troubleshooting tips:
- Poor Powder Flow: If the metal powder is clumpy or has absorbed moisture, it might not flow smoothly during printing. Desiccation or using a different powder batch might be the solution.
- Inconsistent Layer Formation: Uneven powder distribution can lead to weak or defective parts. Calibrating the recoater blade or adjusting printing parameters could rectify this issue.
- Surface Defects: Oxidation or contamination of the metal powder can cause surface imperfections on the printed part. Verifying proper storage conditions and cleaning the printing environment might help.
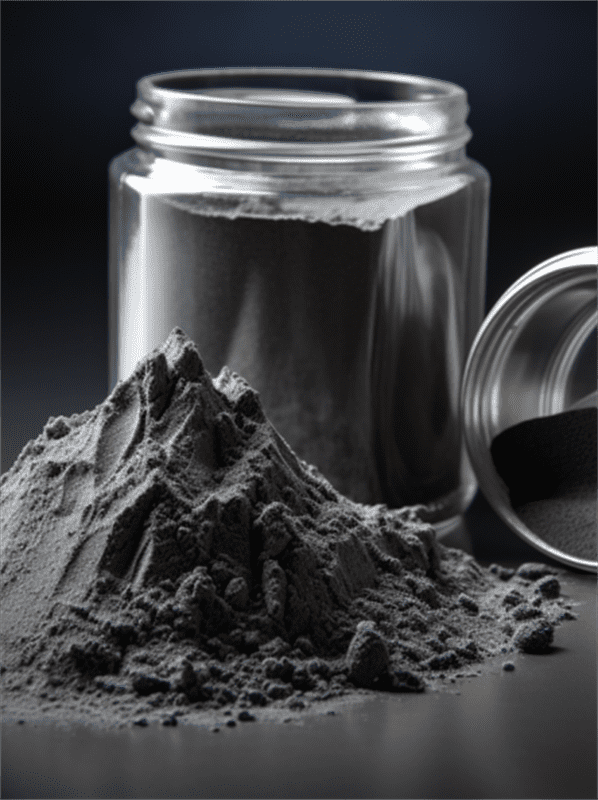
The Future of Metal Powder Storage and Processing
The field of 3D printing is constantly evolving, and so are the methods for storing and processing metal powders. Here are some exciting trends to watch out for:
- Smart Storage Systems: The future might see smart storage systems that use sensors to monitor powder quality and environmental conditions in real-time, ensuring optimal powder performance. Imagine a self-regulating storage unit that keeps your metal powders happy and healthy!
- Advanced Powder Characterization Techniques: New techniques for powder characterization will likely emerge, allowing for more precise analysis of powder properties and their impact on printability. Think of having a microscopic “powder doctor” to ensure your metal powders are in top condition!
- Sustainable and Recyclable Powders: The development of sustainable and recyclable metal powders is gaining traction. This could minimize waste and create a more eco-friendly 3D printing ecosystem. Imagine using metal powders that are good for the environment and create fantastic parts – a win-win!
FAQ
Question | Answer |
---|---|
What are some of the key factors to consider when choosing metal powder storage methods? | The type of metal powder, printing technology, production scale, and cost are all important factors to consider. |
How can I ensure the safety of my metal powders? | Use proper PPE, maintain adequate ventilation, and provide training for anyone handling the powders. |
What are some common signs of poor powder quality? | Clumpy powder, inconsistent layer formation, or surface defects on the printed parts could indicate problems with the powder. |
What are the benefits of using inert gas environments for storing metal powders? | Inert gas environments prevent oxidation and ensure optimal powder performance |
Share On
MET3DP Technology Co., LTD is a leading provider of additive manufacturing solutions headquartered in Qingdao, China. Our company specializes in 3D printing equipment and high-performance metal powders for industrial applications.
Inquiry to get best price and customized Solution for your business!
Related Articles
About Met3DP
Recent Update
Our Product
CONTACT US
Any questions? Send us message now! We’ll serve your request with a whole team after receiving your message.
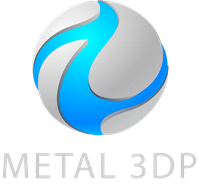
Metal Powders for 3D Printing and Additive Manufacturing
COMPANY
PRODUCT
cONTACT INFO
- Qingdao City, Shandong, China
- [email protected]
- [email protected]
- +86 19116340731