3D Printer Powder Suppliers
Table of Contents
3D printing technology relies on powdered material to build objects layer-by-layer. Selecting the right powder is critical for part quality, mechanical properties, accuracy, detail resolution, and surface finish. This article provides an overview of different types of powders used in major 3D printing processes, their composition, key properties, applications, and leading global suppliers.
Overview of 3d printer powder suppliers
3D printing, also known as additive manufacturing, utilizes powdered polymers, metals, ceramics, or composites as raw material input stock. Based on the technology and materials used, powders can be engineered with specific particle size distributions, morphology, flow characteristics, melting points, and other physical and chemical attributes tailored to the printing process.
Types of 3D Printer Powders
Several key technologies rely on powder bed fusion to selectively melt and solidify material layer-by-layer to fabricate 3D objects. Popular processes and associated powders include:
Process | Materials |
---|---|
Selective Laser Sintering (SLS) | Thermoplastic powders like nylon, TPU, PEEK |
Direct Metal Laser Sintering (DMLS) | Metal powders like aluminum, titanium, steel alloys |
Electron Beam Melting (EBM) | Titanium alloys, cobalt chrome, stainless steel |
Binder Jetting | Stainless steel, tool steel, tungsten carbide |
Stereolithography (SLA) | Ceramic suspended photopolymer resins |
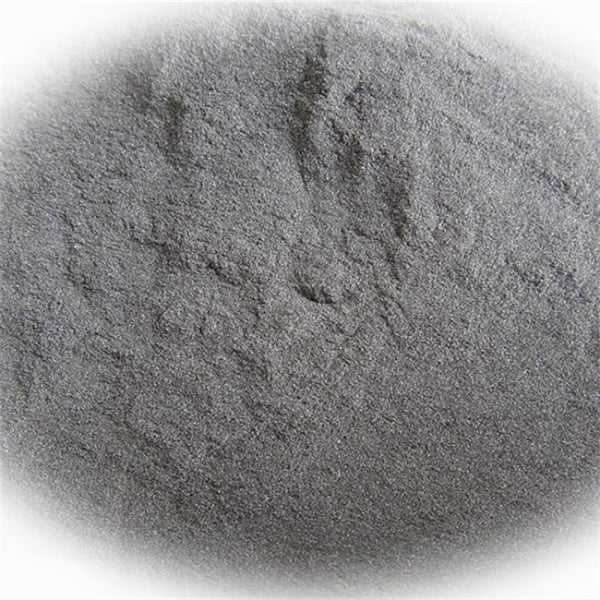
Composition of Polymer Powders for SLS
Selective laser sintering relies on fine polymer powders with controlled particle size distribution and morphology. Common materials include:
Polymer | Key Properties | Applications |
---|---|---|
Nylon 12 | Toughness, flexibility | Functional prototypes, end-use parts |
Nylon 11 | High strength, heat resistance, bio-compatibility | Aerospace, automotive, medical |
TPU | Elasticity, abrasion resistance | Flexible parts, sporting goods |
PEEK | Extreme temperature/chemical resistance | Aerospace, oil/gas, medical |
Nylon 12 is the most widely used polymer powder for laser sintering. The composition includes base nylon polymer, flow agents, and other additives:
Nylon 12 Powder Composition
Component | Function |
---|---|
Base polymer | Provides mechanical properties, melting behavior |
Flow agents | Improve powder flow and reduce agglomeration |
Anti-aging additives | Enhance thermal stability and prevent material degradation over time |
Types of Metal Powders for AM Processes
Common metal powders used in powder bed fusion and binder jetting include:
Material | Alloys/Grades | Properties | Key Applications |
---|---|---|---|
Aluminum | AlSi10Mg, AlSi7Mg | Lightweight, corrosion resistant | Aerospace, automotive |
Titanium | Ti-6Al-4V, Ti 6242 | High strength-to-weight ratio | Aerospace, medical implants |
Stainless steels | 316L, 17-4PH, 420 | Corrosion/heat resistance | Pumps, valves, tooling |
Tool steels | H13, P20, D2 | Hardness, wear resistance | Injection molds, dies |
Cobalt Chrome | Co28Cr6Mo | Biocompatibility, fatigue/corrosion resistance | Dental, medical |
Inconel | IN625, IN718 | High temperature strength | Turbine blades, rocket nozzles |
Titanium alloys like Ti-6Al-4V are extensively used to fabricate strong, lightweight structural components across aerospace, automotive, and medical sectors via DMLS and EBM.
Metal Powder Composition and Production
Most commercial metal powders are produced via gas or water atomization process. The composition includes a base alloying element like titanium or aluminum and other alloying ingredients:
Ti-6Al-4V Powder Composition
Element | Weight % | Purpose |
---|---|---|
Titanium (Ti) | Balance | Principal element |
Aluminum (Al) | 5.5-6.75% | Strengthening |
Vanadium (V) | 3.5-4.5% | Grain refinement |
Iron (Fe) | < 0.3% | Impurity |
Other common production methods for metal AM powders include plasma atomization, electrolysis, and chemical reduction. These influence powder characteristics like particle shape, size distribution, flowability, apparent density, and microstructure.
Ceramic & Composite Powders
Ceramics and composites can also be processed via powder bed technologies to create high-performance components:
Material | Properties | Applications |
---|---|---|
Alumina | High hardness, temperature/corrosion resistance | Cutting tools, wear parts |
Silicon carbide | Extreme hardness, thermal shock resistance | Metal cutting, abrasives |
PEEK polymer | Thermo-mechanical performance | Aerospace composites |
Continuous fiber composites | High strength-to-weight ratio | Structural components |
Photo-curable ceramic resin powders containing silicone dioxide nanoparticles suspended in photopolymer are commonly used in high-precision stereolithography printers.
Powder Characteristics and Specifications
3D printer powders must meet strict specifications in terms of particle size distribution, morphology, flow rate, density, and microstructure. Typical values are shown below:
Polymer Powder Specifications
Parameter | Typical Value |
---|---|
Particle size | 15-150 μm |
Particle shape | Spherical |
Apparent density | 0.35-0.55 g/cm<sup>3</sup> |
Melting point | 172-185°C (nylon 12) |
Metal Powder Specifications
Parameter | Typical Value |
---|---|
Particle size | 15-45 μm |
Apparent density | 2.5-4.5 g/cm<sup>3</sup> |
Flow rate | 25-35 s/50g |
Oxide content | < 0.4 wt.% |
Microstructure | Fully dense spherical |
Manufacturers provide powder material data sheets specifying physical properties, chemical composition test reports, particle size distribution analysis, flow rate measurements, and scanning electron microscopy images.
Applications of 3D Printing Powders
Polymer and metal powders enable production of end-use components across diverse industries. Some examples include:
Polymer Parts
- Functional prototypes
- Automotive ducting, housings
- Consumer products, sporting goods
- Aerospace interior components
Metal Parts
- Aircraft engine/structural parts
- Turbine blades, impellers
- Biomedical implants, devices
- Injection molds, cutting tools
3D printing powders facilitate complex geometries with enhanced mechanical properties unattainable via traditional casting or machining processes.
Powder Suppliers
Leading global suppliers of powders tailored for major 3D printing technologies include:
Polymer Powders
Company | Materials |
---|---|
BASF | Ultrasint PA6, PA11, PA12, TPU |
Henkel | Loctite PA12, PP, TPE |
EOS | PA2200, PA3200GF |
Evonik | Vestosint polymers |
Metal Powders
Company | Materials |
---|---|
AP&C | Titanium, nickel, cobalt alloys |
Sandvik Osprey | Stainless steels, tool steels, superalloys |
Praxair | Titanium, aluminum, cobalt chrome |
GE Additive | Stainless steels, CoCr, Inconel |
These companies offer a wide range material grades tailored for SLS, DMLS, EBM, binder jetting with specialized particle size distributions, shapes, purity levels, and alloy chemistries.
Powder Cost Analysis
Material cost is a significant factor in adopting metal AM. Powder pricing depends on composition, production method, quality, and order volume:
Powder | Price Range |
---|---|
Nylon 12 | $60-100/kg |
Aluminum AlSi10Mg | $50-150/kg |
Titanium Ti-6Al-4V | $200-500/kg |
Nickel IN625 | $100-250/kg |
Cobalt Chrome | $150-600/kg |
Polymer powders can be 40-90% cheaper compared to exotic aerospace alloys. Recycling used powder via sieving and blending with fresh stocks helps lower material costs.
Pros and Cons of Powder-Based AM
Advantages | Limitations |
---|---|
Complex geometries unattainable by other processes | Generally slower build speeds than traditional methods |
Consolidated assemblies, reduced part count | Powder removal/cleanup post-processing |
Customized alloys, composite blends | Anisotropic material properties |
Reduced machining compared to subtractive methods | Porosity issues in some laser/e-beam processes |
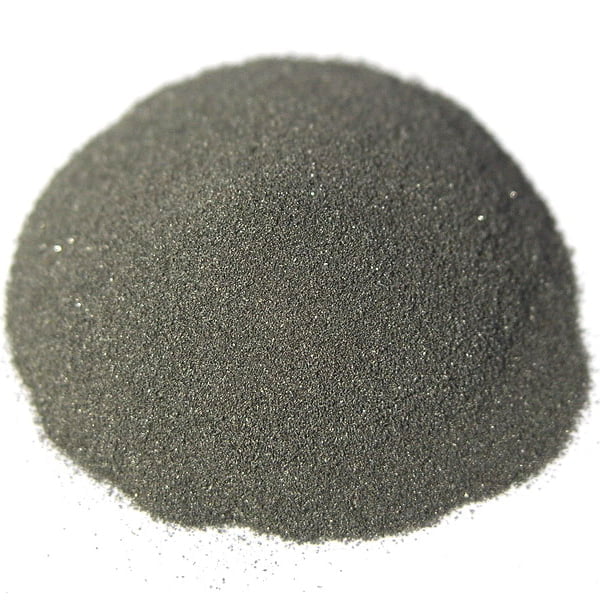
Summary
In summary, powder bed fusion and binder jetting rely on specially engineered plastic, metal, ceramic, or composite powders with tailored size, shape, composition, and microstructure. Leading polymer options include nylon 12, PEEK, and TPU while common metals encompass aluminum, titanium, and nickel-based alloys. Global suppliers offer wide material selection validated for major AM systems. Choosing application-specific powders matching mechanical requirements and properties is critical for part performance.
FAQs
What are the main types of 3D printing powders?
The four major categories are plastics like nylon 12 and PEEK, metals including aluminum, titanium, and tool steel alloys, ceramics such as alumina or silicon carbide, and polymer/fiber composites.
What powder size is ideal for AM processes?
A typical range is 15-100 microns for metals and 15-150 microns for polymers. Size distribution influences density, flowability, surface roughness, accuracy, and speed.
What production methods are used to manufacture metal powders?
Common techniques include inert gas atomization using argon or nitrogen and water atomization. Some niche alloys rely on plasma atomization, electrolysis or chemical processes.
How do you evaluate fitness of powders for AM?
Key parameters are particle size distribution, flow rate, apparent density, morphology and microstructure. Material certification reports confirm chemical composition, gas/oxide content, and trace impurities.
What post-processing is needed on 3D printed powder parts?
Depending on the material and process, common steps involve support removal, media blasting, annealing, HIP and machining to achieve dimensional accuracy and desired finishes.
What are typical bulk pricing tiers for metal AM powders?
1-5 kg samples cost $100-300/kg. Typical volume orders of 10-100 kg range from $60-250/kg. High-volume >500 kg orders can reach $30-150/kg for common aerospace/tooling alloys.
How does recycled powder impact part quality and mechanical performance?
Repeated recycling beyond 2-3 builds can result in changed size distribution, contamination, buildup of satellites, powder degradation issues causing lower density and poorer mechanicals. Fresh powder blending helps overcome this.
What improvements are expected in future metal powders?
Key focus areas are custom alloys, better powder spreadability and packing density for faster builds, lower porosity and higher density leading to enhanced material properties and surface finishes.
Share On
MET3DP Technology Co., LTD is a leading provider of additive manufacturing solutions headquartered in Qingdao, China. Our company specializes in 3D printing equipment and high-performance metal powders for industrial applications.
Inquiry to get best price and customized Solution for your business!
Related Articles
About Met3DP
Recent Update
Our Product
CONTACT US
Any questions? Send us message now! We’ll serve your request with a whole team after receiving your message.
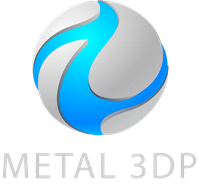
Metal Powders for 3D Printing and Additive Manufacturing