4 types of 3D printing equipments
Table of Contents
The world of 3D printing has exploded onto the scene, transforming the way we design, prototype, and manufacture objects. Gone are the days of clunky, industrial machines – today’s 3D printers are becoming increasingly accessible and sophisticated, allowing anyone from hobbyists to engineers to bring their creations to life. But with this exciting new technology comes a crucial question: which 3D printing process is right for you?
This comprehensive guide delves into the four cornerstones of 3D printing – Fused Deposition Modeling (FDM), Stereolithography (SLA), Selective Laser Sintering (SLS), and Electron Beam Melting (EBM). We’ll explore the inner workings of each technology, compare their strengths and weaknesses, and unveil the types of projects they excel at. So, buckle up and get ready to unlock the secrets behind these fascinating machines!
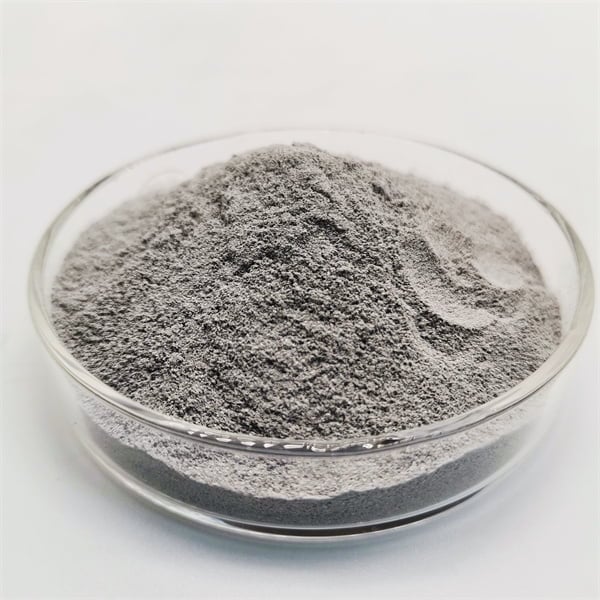
Fused Deposition Modeling (FDM)
Imagine a hot glue gun on steroids, meticulously building an object layer by layer. That’s the essence of FDM, the most widely used 3D printing process. A spool of filament, typically made of plastic like ABS or PLA, is fed through a heated nozzle. The molten plastic is extruded precisely, following the digital blueprint, and solidifies upon contact with the build platform. Layer by layer, your 3D masterpiece takes shape.
Advantages of FDM:
- Affordability: FDM printers are generally the most budget-friendly option, making them perfect for beginners or hobbyists.
- Wide Material Range: FDM boasts a vast selection of filament materials, catering to diverse needs. You can print with PLA for lightweight prototypes, ABS for tougher parts, or even wood-fill filaments for a rustic aesthetic.
- Ease of Use: FDM printers are known for their user-friendly operation. With readily available software and a plethora of online resources, getting started is a breeze.
Disadvantages of FDM:
- Surface Finish: Compared to other techniques, FDM prints can exhibit visible layer lines, resulting in a somewhat rougher surface texture.
- Dimensional Accuracy: FDM printing involves molten plastic cooling and solidifying, which can introduce slight dimensional inconsistencies. For highly precise parts, other methods might be better suited.
- Limited Material Properties: While the material range is impressive, FDM filaments generally don’t offer the same strength, heat resistance, or intricate details achievable with other technologies.
Applications of FDM:
- Prototyping: The affordability and ease of use make FDM ideal for quickly creating functional or visual prototypes to test designs and concepts.
- Toys and figurines: FDM’s vibrant filament options bring characters and creations to life, perfect for hobbyists and makers.
- Educational Tools: FDM printers are valuable tools in classrooms and workshops, allowing students to visualize and create physical models from their designs.
Stereolithography (SLA)
If you crave high-resolution prints with a smooth, near-flawless finish, then SLA is your champion. This technology utilizes a vat of liquid resin and a laser beam to build objects with incredible detail and accuracy. Think of it like a refined sculptor meticulously carving a miniature masterpiece from a pool of light-sensitive liquid.
Advantages of SLA:
- Superior Surface Finish: SLA prints boast exceptional smoothness and detail, making them ideal for applications demanding a polished look or intricate features like jewelry or dental models.
- Dimensional Accuracy: The laser-curing process in SLA ensures highly precise prints, perfect for parts requiring tight tolerances.
- Wide Range of Resins: Similar to FDM’s filament options, SLA offers a variety of resins with unique properties, including castable resins for creating metal molds and biocompatible resins for medical applications.
Disadvantages of SLA:
- Cost: SLA printers typically have a higher price tag compared to FDM.
- Limited Material Properties: While resin options are expanding, SLA materials generally aren’t as strong or heat resistant as some filaments used in FDM.
- Post-Processing: SLA prints require additional steps after printing, including cleaning and potentially post-curing under UV light to achieve optimal strength.
Applications of SLA:
- Jewelry and Prototypes: The exceptional detail and smooth finish make SLA ideal for creating intricate jewelry pieces, high-resolution prototypes for design verification, and even dental models for the medical field.
- Art and Miniatures: Artists and hobbyists leverage SLA to create detailed figurines, miniatures, and sculptures with exceptional surface quality.
- Medical Applications: The biocompatible resin options enable SLA to play a role in creating medical models and potentially even custom prosthetics.
FDM vs. SLA: A Head-to-Head Showdown
Choosing between FDM and SLA boils down to prioritizing your project’s needs. Here’s a breakdown to help you decide:
Price: FDM wins hands down. Budget-conscious makers and beginners will find FDM a much more affordable entry point.
Surface Finish and Detail: The clear winner here is SLA. Its laser-guided precision delivers smooth, near-perfect finishes with intricate details, ideal for projects requiring a polished look or fine features. FDM, while offering a decent range, can exhibit visible layer lines.
Material Properties: FDM offers a wider variety of materials catering to diverse needs, including options like wood-fill filaments for a unique aesthetic. However, SLA materials generally boast superior strength and heat resistance for specific applications. Biocompatible resins in SLA even open doors for medical uses.
Dimensional Accuracy: Both technologies have their merits. FDM can introduce slight dimensional inconsistencies due to material cooling. However, for truly high-precision parts with tight tolerances, SLA’s laser-curing process reigns supreme.
Ease of Use: FDM is generally considered the more user-friendly option. With readily available software and abundant online resources, getting started with FDM is often easier. SLA might require a bit more learning curve for cleaning and post-processing steps.
Applications:
- Choose FDM for: Affordable prototypes, functional parts, hobbyist creations (toys, figurines), educational tools, and projects where a high degree of detail isn’t crucial.
- Choose SLA for: High-resolution prototypes requiring precise details, jewelry making, medical applications (dental models, prosthetics), art and miniatures with a polished finish, and projects where a smooth surface finish is paramount.
The Verdict:
Ultimately, the best choice depends on your specific project requirements. If affordability and ease of use are top priorities, FDM is a fantastic option. But if achieving a flawless surface finish, intricate details, and high dimensional accuracy are essential, then SLA is the way to go.
Selective Laser Sintering (SLS)
Stepping into the realm of industrial 3D printing, we encounter Selective Laser Sintering (SLS). This powerhouse technology utilizes a bed of fine powder particles, typically nylon or plastic-based. A laser beam selectively fuses these particles layer by layer, building the desired object with impressive strength and durability. Imagine a miniaturized factory floor where a laser acts as a construction foreman, meticulously binding powder into a solid form.
Advantages of SLS:
- High Strength and Durability: SLS-printed parts boast exceptional strength and heat resistance, making them ideal for functional applications and end-use parts.
- Design Freedom: SLS allows for intricate geometries and internal structures due to the powder-based approach, unlocking possibilities for complex designs.
- Wide Material Range: Similar to FDM, SLS offers a diverse selection of materials beyond just nylons. Users can choose from materials with unique properties like flame retardancy or even metal-filled options for added weight and strength.
Disadvantages of SLS:
- Cost: SLS printers are significantly more expensive than FDM or SLA machines, making them primarily suited for professional or industrial applications.
- Post-Processing: SLS prints require additional steps after printing, including removing excess powder and potentially heat treatment for optimal strength.
- Limited Surface Finish: While SLS offers good surface quality, it might not achieve the same level of smoothness as SLA due to the powder-based nature of the process.
Applications of SLS:
- Functional Prototypes and End-Use Parts: SLS excels at creating strong, durable prototypes and even end-use parts for applications demanding high performance, like automotive components, machine parts, and functional housings.
- Medical and Aerospace: The strength and biocompatible material options make SLS valuable in medical applications like prosthetics and in the aerospace industry for lightweight, high-strength components.
Electron Beam Melting (EBM)
For those seeking the ultimate in strength and precision when working with metals, Electron Beam Melting (EBM) emerges as the champion. This cutting-edge technology utilizes a high-powered electron beam to melt metal powder layer by layer, building incredibly strong and complex metal parts. Imagine a miniature foundry where a focused electron beam acts as a molten metal sculptor, meticulously crafting intricate metallic objects.
Advantages of EBM:
- Unmatched Strength and Durability: EBM-printed parts boast exceptional strength, heat resistance, and near-net-shape capabilities, making them ideal for demanding applications.
- Metal Printing Freedom: EBM allows for the printing of a wide range of metals, including titanium, stainless steel, and Inconel, unlocking possibilities for intricate and high-performance metal parts.
- Complex Geometries: Similar to SLS, EBM enables the creation of intricate geometries and internal structures due to the powder-based approach. This opens doors for designing lightweight yet strong components with internal channels or complex lattices.
Disadvantages of EBM:
- Cost: EBM printers are the most expensive option on this list, typically reserved for high-value applications or industrial settings.
- Safety Considerations: Due to the high-powered electron beam and the use of metal powders, EBM requires a controlled environment and adherence to strict safety protocols.
- Surface Finish: Like SLS, EBM parts might exhibit a slightly rougher surface texture compared to some machining techniques. However, post-processing techniques can improve the surface finish to a degree.
Applications of EBM:
- Aerospace and Defense: EBM’s ability to print strong, lightweight metal parts with complex geometries makes it ideal for aerospace applications like aircraft components and even rocket engine parts. Additionally, the technology plays a role in creating intricate parts for the defense industry.
- Medical Implants: The biocompatible nature of certain EBM-printable metals allows for the creation of custom-designed medical implants like prosthetic joints or spinal implants with exceptional strength and biocompatibility.
- High-Performance Tools and Dies: EBM-printed tools and dies can offer superior strength, heat resistance, and wear resistance compared to traditionally manufactured options, leading to longer tool life and improved efficiency in certain production processes.
SLS vs. EBM
Choosing between SLS and EBM hinges on the material and application needs. Here’s a breakdown to guide your decision:
Material:
- SLS: Primarily utilizes nylon or plastic-based powders, but offers a wider range of material options including flame-retardant or metal-filled varieties.
- EBM: Focuses on metal powders, allowing for the printing of a diverse range of metals like titanium, stainless steel, and Inconel.
Cost: SLS is significantly less expensive than EBM.
Strength and Durability: EBM reigns supreme when it comes to printing exceptionally strong and heat-resistant metal parts.
Applications:
- Choose SLS for: Functional prototypes, strong plastic parts for end-use applications, medical applications (potentially using biocompatible materials), and projects requiring design freedom with a wider material selection.
- Choose EBM for: High-performance metal parts demanding exceptional strength and heat resistance, applications in aerospace, defense, medical implants (using biocompatible metals), and creation of complex metal tools and dies.
The Verdict:
SLS offers a compelling balance of affordability, design freedom, and good material strength for various applications. However, if your project demands the ultimate in strength, heat resistance, and metal printing capabilities, then EBM is the way to go, even with its higher cost and stricter safety considerations.
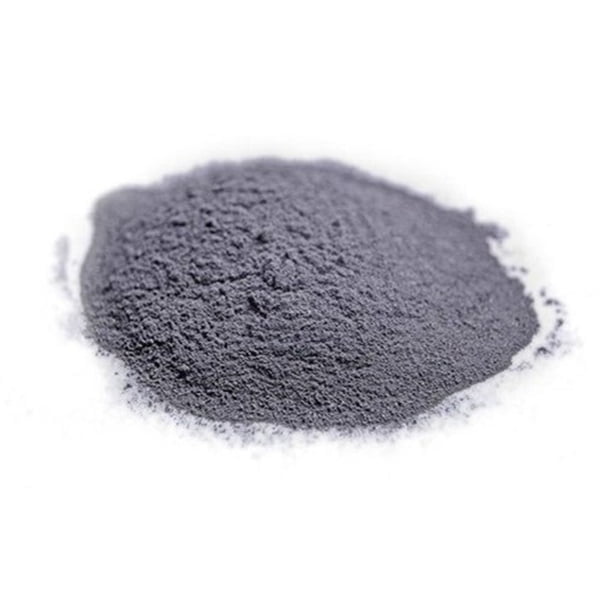
Choosing the Right 3D Printing Technology
The world of 3D printing offers a diverse range of technologies, each with its own strengths and weaknesses. By understanding the core principles of FDM, SLA, SLS, and EBM, you can make an informed decision about the best fit for your project. Consider factors like budget, desired material properties, surface finish requirements, and the complexity of your design.
Remember, 3D printing is a continuously evolving field. As technology advances, we can expect even more innovative and powerful options to emerge, pushing the boundaries of what’s possible in the realm of design and manufacturing. So, embrace the possibilities, explore these fascinating technologies, and unleash your creativity in the exciting world of 3D printing!
FAQ
Question | Answer |
---|---|
What is the cheapest 3D printing technology? | Fused Deposition Modeling (FDM) is generally the most affordable option. |
What 3D printing technology offers the best surface finish? | Stereolithography (SLA) excels at creating smooth, near-perfect finishes with intricate details. |
What 3D printing process is best for metal printing? | Electron Beam Melting (EBM) is the champion for printing strong, high-precision metal parts. |
Is 3D printing good for prototyping? | Absolutely! FDM and SLA are excellent choices for creating functional or visual prototypes to test designs and concepts. |
What are some limitations of 3D printing? | Current limitations include cost (especially for metal printing technologies), limited material selection compared to traditional manufacturing, and potential for post-processing steps depending on the technology used. |
Share On
MET3DP Technology Co., LTD is a leading provider of additive manufacturing solutions headquartered in Qingdao, China. Our company specializes in 3D printing equipment and high-performance metal powders for industrial applications.
Inquiry to get best price and customized Solution for your business!
Related Articles
About Met3DP
Recent Update
Our Product
CONTACT US
Any questions? Send us message now! We’ll serve your request with a whole team after receiving your message.
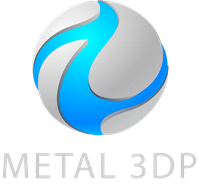
Metal Powders for 3D Printing and Additive Manufacturing