Types of 3D printing services
Table of Contents
Imagine a world where your imagination takes physical form, where intricate designs materialize from a digital blueprint, and where innovation is democratized. This, my friend, is the captivating realm of 3D printing. But within this realm lies a vast landscape of services, each catering to specific needs and applications. Buckle up, because we’re about to embark on a journey to explore the captivating world of 3D printing services!
Rapid prototyping: Bringing Ideas to Life in a Flash
Ever dreamt of transforming a napkin sketch into a tangible prototype overnight? Well, rapid prototyping with 3D printing makes that dream a reality. It’s the perfect tool for product designers, engineers, and inventors who need to quickly create physical models to test form, fit, and functionality.
Think of it like this: traditionally, prototyping involved sculpting, machining, or other time-consuming techniques. With 3D printing, you simply upload your CAD file, choose your material, and hit print. In a matter of hours (or even minutes!), you’re holding a real-life representation of your design. This rapid turnaround allows for swift iterations, enabling you to refine your concept and identify potential issues before investing in expensive mass production.
Popular materials for rapid prototyping:
- FDM (Fused Deposition Modeling): Affordable and versatile, FDM uses plastic filaments to create prototypes with a good balance of functionality and aesthetics.
- SLA (Stereolithography): Known for its exceptional detail and smooth surface finish, SLA is ideal for creating highly detailed prototypes that closely resemble the final product.
- SLS (Selective Laser Sintering): This process uses nylon powder to build strong and functional prototypes, making it perfect for testing mechanical properties.
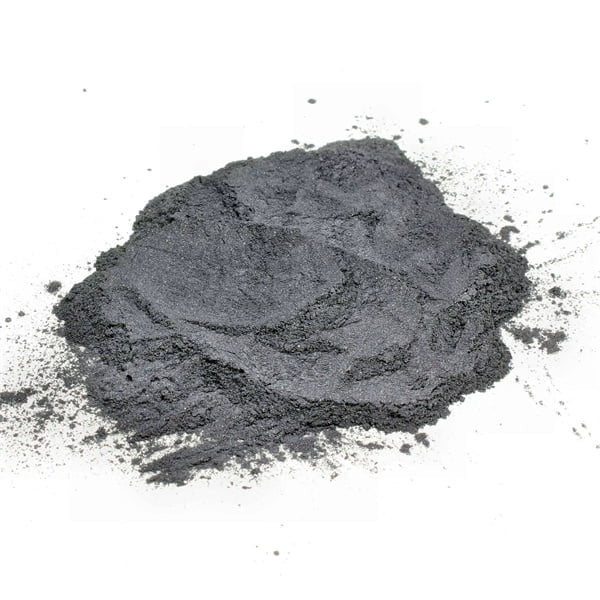
Mold manufacturing: From Prototype to Production
Once your prototype is perfected, 3D printing can also help bridge the gap to mass production. Through mold manufacturing, you can create custom molds directly from your 3D model. This eliminates the need for traditional mold-making techniques, which can be expensive and time-consuming.
There are two main approaches to 3D-printed molds:
- Direct investment casting: This method involves creating a mold using a high-resolution 3D printing process like SLA. The mold is then filled with molten metal, creating a precise replica of your design.
- Silicone mold making: 3D-printed masters are used to create flexible silicone molds. These molds can then be used for casting a variety of materials like resin, concrete, or even chocolate!
Advantages of 3D-printed molds:
- Cost-effective: Compared to traditional methods, 3D-printed molds can be significantly cheaper, especially for low-volume production runs.
- Faster turnaround: The digital-to-physical workflow streamlines the mold-making process, leading to quicker time-to-market.
- Design freedom: 3D printing allows for intricate geometries that would be difficult or impossible to achieve with traditional methods.
Things to consider:
- Material limitations: Not all 3D-printed materials can withstand the high temperatures involved in some casting processes.
- Surface finish: Depending on the 3D printing process used, the surface finish of the mold might require additional post-processing.
Part manufacturing: Printing the Future, One Layer at a Time
Forget about bulky warehouses and complex supply chains. 3D printing services are now making it possible to manufacture end-use parts directly on demand. This is a game-changer for businesses of all sizes, enabling them to:
- Reduce inventory costs: Print parts only as needed, eliminating the need to store large quantities of stock.
- On-demand production: Create customized parts or replacements quickly and efficiently.
- Local manufacturing: Print parts locally, reducing transportation costs and environmental impact.
Popular materials for part manufacturing:
- FDM: Ideal for functional parts requiring a balance of cost and durability.
- SLS: Strong and heat-resistant, SLS is suitable for parts that need to withstand mechanical stress.
- Metal 3D printing: Processes like DMLS (Direct Metal Laser Sintering) enable the creation of high-strength metal parts for demanding applications.
Applications of 3D-printed parts:
- Automotive: Custom brackets, prototypes, and even functional end-use parts.
- Aerospace: Lightweight and high-strength components for aircraft and spacecraft.
- Medical: Patient-specific prosthetics, surgical models, and bioprinting applications.
- Consumer goods: Customized phone cases, jewelry, and even sporting equipment.
Unveiling the Arsenal: A Look at Popular 3D Printing Technologies
Now that we’ve delved into the different services, let’s peek under the hood and explore the most common 3D printing technologies that power these services. Understanding these technologies will empower you to choose the best fit for your project, considering factors like budget, material properties, and desired level of detail.
1. Fused Deposition Modeling (FDM):
Imagine a hot glue gun meticulously building your design layer by layer. That’s essentially the essence of FDM, the most widely used 3D printing technology. It works by extruding a thin filament of molten plastic through a heated nozzle, depositing it in precise paths to create your 3D object.
Pros:
- Affordable: FDM printers are generally the most cost-effective option, making them ideal for hobbyists, startups, and rapid prototyping.
- Versatile material selection: FDM works with a wide range of plastic filaments, offering possibilities for different functionalities and aesthetics. From tough ABS for mechanical parts to flexible TPU for gaskets, there’s an FDM filament for nearly every need.
- Easy to use: FDM printers are relatively user-friendly, with a lower barrier to entry compared to other technologies.
Cons:
- Limited detail: Compared to other technologies, FDM prints can exhibit visible layer lines, impacting the overall smoothness of the surface finish.
- Strength variations: The strength of FDM parts can vary depending on the printing orientation and infill density.
2. Stereolithography (SLA):
For those seeking unparalleled detail and smooth surface finishes, SLA is the champion. This technology uses a laser beam to cure thin layers of liquid resin into a solid 3D object. Think of it like a high-tech sculptor, meticulously carving your design with pinpoint accuracy.
Pros:
- Exceptional detail: SLA produces incredibly smooth and detailed prints, making it ideal for intricate models, jewelry prototypes, and applications requiring a high visual quality.
- Wide range of materials: SLA resins are available in a variety of properties, including clear, opaque, and even biocompatible options for medical applications.
Cons:
- Higher cost: SLA printers and materials tend to be more expensive compared to FDM.
- Limited strength: SLA prints are generally not as strong as FDM parts and might not be suitable for functional applications requiring high mechanical stress.
3. Selective Laser Sintering (SLS):
If you need strong and functional prototypes or end-use parts, SLS is a compelling option. This technology uses a laser beam to selectively sinter (fuse) tiny particles of nylon or other plastic powder into a solid object. Imagine a layer cake, where each layer is made of fused powder particles, meticulously stacked to form your design.
Pros:
- Strong and functional: SLS parts are known for their impressive strength and durability, making them suitable for a wide range of applications.
- Design freedom: SLS allows for complex geometries with internal channels and undercuts, which can be challenging with other technologies.
Cons:
- Higher cost: Similar to SLA, SLS printers and materials come at a premium price point.
- Post-processing: SLS prints require post-processing steps like removing excess powder, which can add time and complexity to the workflow.
4. Multi Jet Fusion (MJF):
Consider MJF as the high-performance cousin of SLS. It also uses a powder bed fusion approach, but instead of a single laser, MJF utilizes thousands of inkjet nozzles to deposit fusing and detailing agents across the powder bed. This allows for faster printing times and superior surface finishes compared to traditional SLS.
Pros:
- Faster printing: MJF boasts significantly faster printing speeds compared to SLS, making it ideal for high-volume production runs.
- Exceptional detail and finish: MJF prints deliver a smooth surface finish and fine details, rivaling even SLA in some cases.
Cons:
- Limited material selection: Currently, MJF has a narrower range of materials compared to SLS, though this is expected to expand in the future.
- Higher upfront cost: MJF printers are a significant investment, making them more suitable for established businesses with high production needs.
5. Metal 3D Printing:
Metal 3D printing encompasses various technologies like DMLS (Direct Metal Laser Sintering) and Electron Beam Melting (EBM) that use lasers or electron beams to melt metal powder layer by layer, building a solid metal object. This opens doors to entirely new design possibilities for industries like aerospace, automotive, and medical.
Pros:
- High strength and functionality: Metal 3D printing allows for the creation of complex and high-strength metal parts, pushing the boundaries of traditional manufacturing.
- Lightweighting: Metal 3D printing enables the creation of intricate lattice structures within metal parts, reducing weight without sacrificing strength. This is a game-changer for applications like aerospace components where weight reduction is critical.
Cons:
- Highest cost: Metal 3D printing is the most expensive option on this list, with both the printers and materials carrying a hefty price tag.
- Safety considerations: Metal 3D printing processes can involve high temperatures and hazardous materials, requiring proper safety protocols and trained personnel.
Choosing the Right Technology:
The best 3D printing technology for your project depends on a variety of factors:
- Budget: FDM is the most budget-friendly option, while metal 3D printing requires a significant investment.
- Material needs: Consider the desired properties of your final part, such as strength, flexibility, heat resistance, and biocompatibility.
- Part complexity: Some technologies, like SLS and MJF, excel at creating intricate geometries with internal features.
- Surface finish: If a smooth and visually appealing finish is crucial, SLA or MJF might be better choices than FDM.
- Production volume: For high-volume production runs, MJF’s speed might be advantageous.
The Future of 3D Printing:
The world of 3D printing is constantly evolving, with new technologies and materials emerging all the time. Here are some exciting trends to keep an eye on:
- Multi-material printing: The ability to combine different materials within a single print opens doors for creating parts with unique properties and functionalities.
- Bioprinting: The use of 3D printing to create living tissues and organs holds immense potential for medical applications.
- Nano-printing: Printing at the nanoscale could revolutionize fields like electronics and materials science.
- Increased affordability: As the technology matures, we can expect 3D printers and materials to become more affordable, making them even more accessible to businesses and individuals.
As 3D printing continues to develop, its impact on various industries is undeniable. From rapid prototyping and custom part creation to revolutionizing manufacturing and healthcare, 3D printing is poised to reshape the way we design, create, and interact with the world around us.
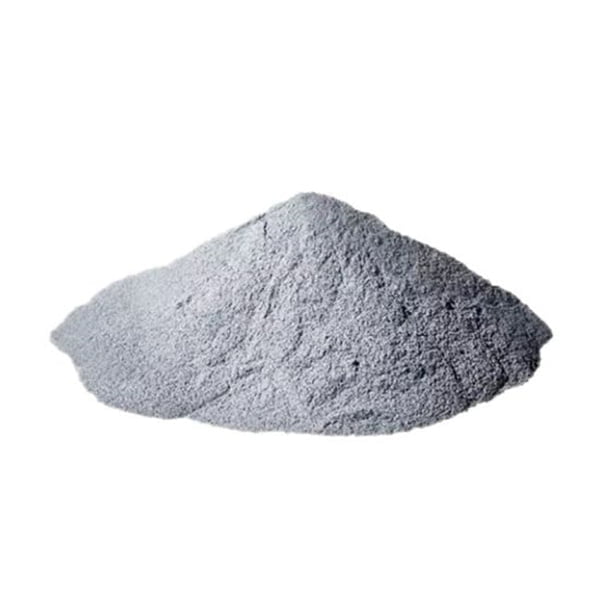
FAQ
Here are some of the most frequently asked questions regarding 3D printing services:
Question | Answer |
---|---|
What file formats do 3D printing services typically accept? | Most 3D printing services accept popular file formats like STL, OBJ, and 3MF. |
How much does it cost to 3D print something? | The cost of 3D printing depends on several factors, including the technology used, material selection, part size, and complexity. However, services typically offer quotes based on your 3D model upload. |
Can I 3D print my own designs? | Absolutely! There are desktop 3D printers available for personal use, allowing you to bring your designs to life at home. However, these printers might have limitations compared to professional 3D printing services. |
What are the benefits of using a 3D printing service? | 3D printing services offer access to a wider range of technologies, materials, and expertise compared to owning a personal 3D printer. They can also handle larger and more complex projects. |
How do I find a reputable 3D printing service? | Look for online directories or ask for recommendations from within your industry. When choosing a service, consider factors like their experience, technology offerings, material selection, turnaround times, and pricing structure. |
Share On
MET3DP Technology Co., LTD is a leading provider of additive manufacturing solutions headquartered in Qingdao, China. Our company specializes in 3D printing equipment and high-performance metal powders for industrial applications.
Inquiry to get best price and customized Solution for your business!
Related Articles
About Met3DP
Recent Update
Our Product
CONTACT US
Any questions? Send us message now! We’ll serve your request with a whole team after receiving your message.
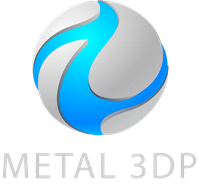
Metal Powders for 3D Printing and Additive Manufacturing