3D Printing Copper Powder
Table of Contents
Overview of 3D Printing Copper Powder
3D printing copper powder is a metal powder made of pure copper or copper alloys used as the raw material in various 3D printing technologies for manufacturing end-use copper parts and products.
Some key properties and advantages of using 3D printing with copper powder include:
- High electrical and thermal conductivity desired for electronics applications
- Very high machinability ratings for good finish and post-processing
- Excellent mechanical properties like strength and ductility
- Corrosion resistance due to protective copper oxide layer formation
- Bio-compatible for medical devices and implants
- Cost advantage compared to conventional copper machining
Several metal 3D printing processes utilize copper powder, most commonly:
Types of 3D Printing Using Copper Powder
3D Printing Technology | Description |
---|---|
Binder Jetting | Glues copper powder using liquid binding agents |
Directed Energy Deposition (DED) | Uses laser or electron beam to melt copper powder |
Selective Laser Melting (SLM) | Selectively laser melts and fuses copper powder bed |
These additive manufacturing techniques allow creating complex geometries with copper not feasible by casting or machining. Parts can be fabricate on demand without tooling or molds.
Now let’s take a deeper look into copper grades for 3D printing, properties, applications, specifications, pricing, comparisons and more.
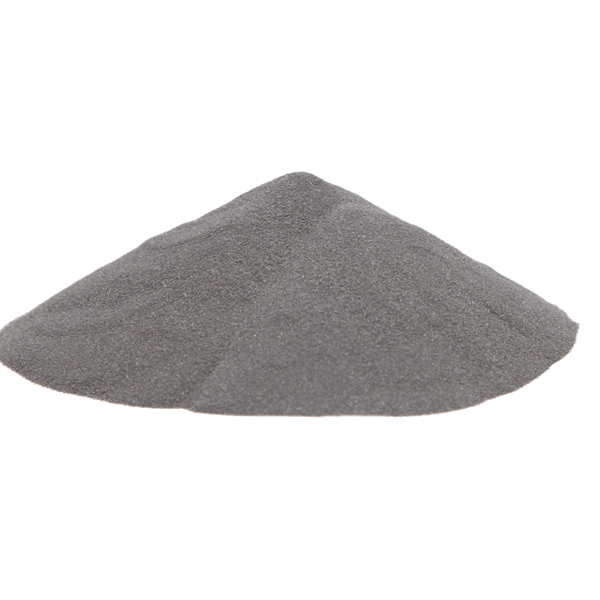
Composition of 3D Printing Copper Powder
There are a few main types of copper metal powders used in additive manufacturing:
Compositions of 3D Printing Copper Powder
Powder Type | Typical Composition |
---|---|
Pure Copper | 99.7% Cu minimum |
Copper-tin alloy | Cu-10Sn bronze alloy |
Copper-nickel alloy | 90Cu-10Ni or 70Cu-30Ni |
Characteristics of 3D Printed Pure Copper Parts
- Excellent electrical conductivity for electronics
- Ductile material allowing post-processing
- Annealing can further enhance ductility
- Low hardness at 100 HV after printing
Pros
- Highest thermal and electrical conductivity
- Easy to machine, plate, coat post-build
- Bio-compatible for medical uses
- Welding dissimilar metals is simplified
Cons
- Soft low-strength textures and features
- Risk of delamination between layers
- Oxide film formation prone to contamination
Characteristics of 3D Printed Cu-Sn Bronze Parts
- Better mechanical properties with tin alloying
- Up to double the hardness and strength
- Move wear-resistant surface finish
- Higher temperature resistance
Pros
- Stronger parts to resist deformation
- Allows printing fine details and textures
- Small amounts of tin enhance properties
- Good corrosion resistance
Cons
- Lower thermal and electrical conductivity
- Higher density increases weight
- Still require supports during printing
Characteristics of 3D Printed Cu-Ni Alloy Parts
- Excellent combination of strength plus conductivity
- Maintains high ductility and thermal properties
- Adds hardness for wear protection
- Solders well with other copper components
Pros
- Tunable properties balancing strength, hardness and conductivity
- Strong parts able to withstand stress
- Just 10% nickel doubles the yield strength
- Lower melting point benefits lower-temp printing
Cons
- Not bio-compatible for medical devices
- Nickel can initiate galvanic corrosion
- Higher material costs than pure copper
Applications of 3D Printed Copper
Thanks to its versatile material properties, 3D printing with copper powder is used across industries:
Applications of 3D Printing Copper Powder
Industry | Common Applications |
---|---|
Electronics | Interconnects, contacts, terminals, EMI shielding |
Electrical | Bus bars, rotor windings, electromagnets |
Heat exchangers | Heat sinks, evaporators, condensers |
Automotive | Welding tips, bushings, bearings |
Architecture | Decorative facades, panels, modeling |
Medical | Electrodes,GREENs, implants, surgical tools |
Some specific product examples include:
Electronics: Conductive traces, wires, antennae, batteries, sensors
Automotive: Light housings, quick connect fittings, threaded inserts
Aerospace: Brackets, torque control components, radio hardware
Consumer goods: Buttons, closures, zippers, decorative parts
Hardware: Gears, locks, springs, fasteners like nuts and bolts
Leveraging copper’s properties in 3D printing unlocks innovative geometries impossible with subtractive methods that can enhance functionality and efficiency.
Specifications of Copper Metal Powder for 3D Printing
3D printer manufacturers characterize copper powder based on metrics like:
Copper Powder Specifications for 3D Printing
Parameter | Typical Specification Range |
---|---|
Powder shape | Predominantly spherical |
Size range | 15-45 microns |
Min apparent density | 3.5 g/cm3 |
Typical layer thickness | 20-100 microns |
Flow rate | >=25 sec for 50 g |
Residual oxygen | 0.3% max |
Other important powder measurements:
- Tap density: After settling ranges 4-4.5 g/cm3
- Hall flow rate: Time for 50g powder to flow through funnel aperture
- Hausner ratio: Tap density divided by apparent density indicates flowability
Narrow distribution ensures dense and uniform powder spreading during printing. Low oxygen prevents excess oxides impeding layer bonding.
Copper Metal Powder Prices, Suppliers, and Comparisons
Copper powder costs fluctuate based on market prices, composition, quantity and source location:
Copper Powder Cost Comparison
Type | Average Price Range | Key Suppliers |
---|---|---|
Pure copper | $50-80 per kg | AP&C, Sandvik Osprey, Carpenter Additive |
Cu-10Sn bronze | $55-90 per kg | ECKA Granules, BASF Additive Mfg, LPW Technology |
CuNi10 alloy | $65-105 per kg | Linde, Arconic Components, Praxair |
Buying high purity grades from certified metal powder manufacturers ensures reliable quality. Overseas suppliers offer lower cost options but can lack consistency.
When comparing copper powder materials for a print job, consider:
Pros and Cons of Different Copper Powders
Type | Pros | Cons |
---|---|---|
Pure copper | Highest thermal/electrical performance<br>Lowest cost | Soft parts prone to wear<br>Risk of delamination |
Cu bronze alloy | Stronger components<br>Better fine detail resolution | Heavier components<br>Lower conductivity |
Copper-nickel | Balanced strength plus conductivity <br>Controlled friction/wear | Not bio-compatible<br>More difficult to machine |
In summary, pure copper suits electronics needs emphasizing conductivity and ductility at low cost whereas alloys better meet mechanical requirements with higher strength and hardness.
Printing Parameters, Thresholds and Recommendations
Dialing in optimal print settings is key to successfully utilizing copper powder:
Print Profile Settings for Copper Powder
Parameter | Typical Range | Recommendations |
---|---|---|
Layer thickness | 20-100 microns | Thinner layers improve interlayer bonding |
Laser power (for SLM) | 100-500 W | Higher density and wetting at increased power |
Scan speed | 100-500 mm/s | Faster speeds reduce heat input and residual stress |
Beam size | 20-100 microns | Laser diameter close to layer thickness |
Support structures | Tree-like | Prevent warping then remove through post-processing |
Shielding gas | Argon or nitrogen | Prevent oxidation during builds |
Build plate heating | 50-250°C | Heatsink once deposited if cooling is too fast |
Stress relief | Anneal 1-3 hrs at 400°C | Reduce residual stresses promoting layer integrity |
Hot isostatic pressing | 1000-10000 psi at 500-950°C | Increase density by collapsing voids |
Surface finishing | Tumbling, machining, grinding, polishing etc | Smoothen surface roughness |
Monitoring the melt pool size and temperatures aids real-time calibration of laser parameters. Match the energy input to the print area to achieve good fusion without excess heating.
For high quality parts, thermal management is key along with mitigating residual stress through strategic heating/cooling cycles during printing as well as post-build heat treatments. Leverage standard metalworking/machining methods for finishing copper printed components.
Industry Standards for 3D Printing Using Metal Powders
Standards Organizations for Metal Additive Manufacturing
Organization | Relevant Metal AM Standards |
---|---|
ASTM International | F3049, F2971, F3184, F3301 etc. for amenable alloys, process requirements, qualities |
International Organization for Standardization (ISO) | ISO/ASTM 52915, 52921 covering design, processes, testing |
SAE International | AMS7001A Aerospace material and process specs |
American Society of Mechanical Engineers (ASME) | BPVC Section IX Welding codes |
National Institute of Standards and Technology (NIST) | Reference copper powder data and measurement science |
International Electrotechnical Commission (IEC) | IEC 62890 benchmarking metal powder bed fusion process performance |
These share best practices and quantify repeatable performance criteria to qualify parts for end use.
For aerospace and aviation components, additional CAA and FAA standards need compliance as well. Automotive parts also reference UL, A2LA, NADCAP specifications.
In medical device applications, meeting FDA and CE regulations is mandatory before commercialization to ensure biocompatibility and patient safety.
Overall, standards sync technology development across the metal additive manufacturing industry.
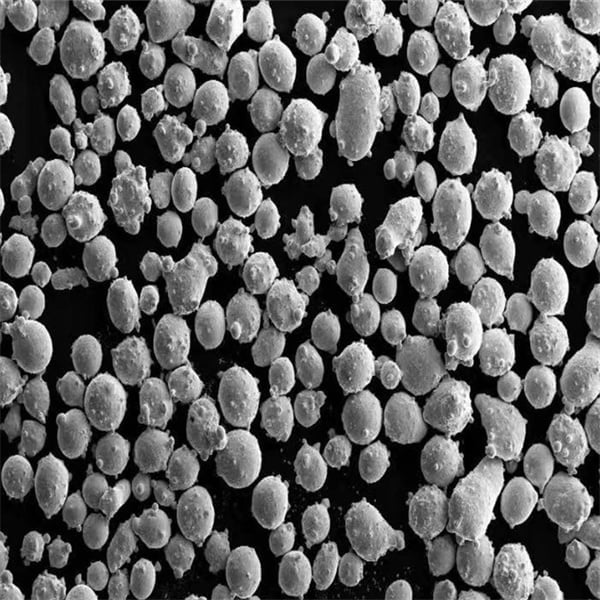
FAQs
Q: How to choose the right copper alloy for my application?
A: Most products emphasize either strength, hardness, and wear performance or thermal/electrical conductivity. Tuning the alloying elements like tin or nickel accordingly allows custom property optimization.
Q: Does copper powder require inert gas shielding when printing?
A: Yes, heating copper powder to high temperatures causes surface oxidation losing alloying elements. Shielding with argon or nitrogen prevents excessive material loss.
Q: What causes cracking between layers when 3d printing copper?
A: Differential cooling rates plus alloy shrinkage can introduce stresses leading to interlayer cracks. Better thermal controls during builds and stress-relief heat treatments post-process reduce these defects.
Q: Why does my 3d printed copper part have poor surface finish and texture?
A: Insufficient melting of powder particles from low laser power causes porous uneven textures needing extensive finish machining. Printing calibration, adequate layer overlap and higher energy density improves surface quality.
Q: Is direct metal printing with copper powder very expensive?
A: Yes, both printer system costs running over $100,000 plus recursive metal powder purchases make it prohibitively expensive for small productions. However, cost per part drops significantly for volume production runs due to no tooling requirements.
Share On
MET3DP Technology Co., LTD is a leading provider of additive manufacturing solutions headquartered in Qingdao, China. Our company specializes in 3D printing equipment and high-performance metal powders for industrial applications.
Inquiry to get best price and customized Solution for your business!
Related Articles
About Met3DP
Recent Update
Our Product
CONTACT US
Any questions? Send us message now! We’ll serve your request with a whole team after receiving your message.
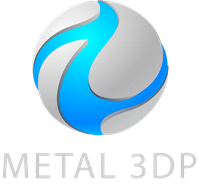
Metal Powders for 3D Printing and Additive Manufacturing