Detailed explanation of plasma atomized 3D Printing Metal Powder
Table of Contents
Imagine holding the future in your hand. Not a crystal ball, but a tiny, unassuming pile of plasma atomized metal powder. These microscopic marvels, born from the fiery embrace of plasma and molten metal, are the building blocks of countless industries, shaping everything from the sleek curves of airplanes to the intricate components of medical devices.
But what exactly is plasma atomization, and how does it transform molten metal into these potent powders? Buckle up, because we’re about to delve into the fascinating world of this transformative technology.
What is Plasma Atomization?
In essence, plasma atomization is a metal powder production technique that utilizes the immense heat and power of plasma. Plasma, often referred to as the fourth state of matter, is a supercharged gas composed of ionized atoms and free electrons. This superheated state allows it to melt even the most refractory metals, those with incredibly high melting points, with ease.
Here’s a breakdown of the process:
- Feedstock Preparation: The chosen metal is transformed into a feedstock, typically molten metal droplets or metal wires.
- Plasma Generation: High-pressure gas, like argon or helium, is passed through an electric arc, creating an intensely hot plasma torch.
- Atomization: The molten metal feedstock is injected into the plasma stream, causing it to fragment and rapidly solidify into tiny, spherical particles.
- Powder Collection: The cooled metal particles are collected using a classification system to achieve the desired particle size distribution.
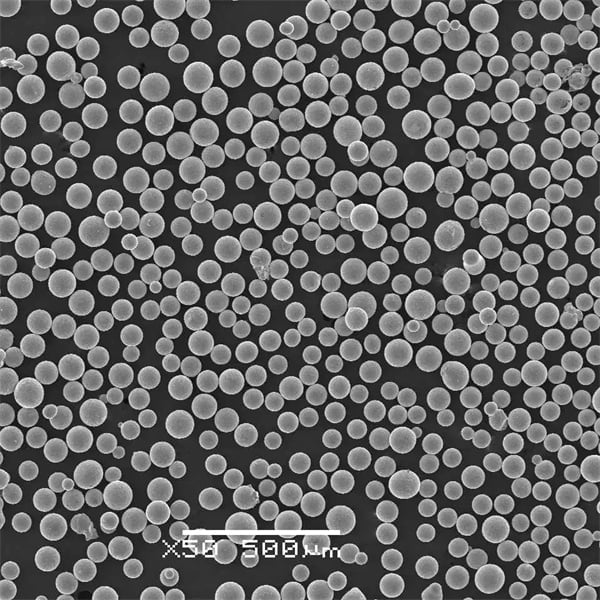
The Many Faces of Plasma Atomized Powders:
Plasma atomization isn’t a one-size-fits-all process. Depending on the desired properties and applications, various metal powder models are available, each boasting unique advantages:
- Titanium Powders: Renowned for their high strength-to-weight ratio, excellent corrosion resistance, and biocompatibility, titanium powders find extensive use in aerospace, medical implants, and sporting goods.
- Nickel Powders: Offering a combination of strength, ductility, and high-temperature performance, nickel powders are crucial for applications in chemical processing, oil & gas exploration, and power generation.
- Cobalt Powders: Valued for their magnetic properties, wear resistance, and high-temperature strength, cobalt powders are vital for cutting tools, turbine blades, and hardfacing applications.
- Stainless Steel Powders: As the name suggests, stainless steel powders offer excellent corrosion resistance alongside good mechanical properties, making them ideal for applications in food processing, medical devices, and automotive components.
- Aluminum Powders: Lightweight and highly conductive, aluminum powders are sought after in aerospace, automotive, and electronics industries for their ability to reduce weight and enhance conductivity.
- Copper Powders: Boasting exceptional electrical conductivity and thermal conductivity, copper powders are utilized in electrical components, heat sinks, and thermal management applications.
- Iron Powders: Offering high magnetic permeability and good machinability, iron powders are the workhorses of the powder metallurgy industry, used in components ranging from gears and bearings to filters and magnetic cores.
- Inconel Powders: A family of nickel-chromium superalloys, Inconel powders offer outstanding high-temperature strength, oxidation resistance, and creep resistance, making them the preferred choice for jet engines, rocket engines, and chemical processing equipment.
- Tungsten Powders: Renowned for their exceptional hardness, high melting point, and good wear resistance, tungsten powders are used in cutting tools, welding electrodes, and armor-piercing projectiles.
- Molybdenum Powders: Offering excellent high-temperature stability, good corrosion resistance, and high melting point, molybdenum powders are utilized in electronic components, heating elements, and crucibles.
This is just a glimpse into the diverse world of plasma atomized metal powders. Each type possesses its own unique set of properties and caters to specific industry needs.
The Power of Plasma: Unleashing the Potential of Metal Powders
Beyond the diverse range of metal powders, plasma atomization offers several advantages that set it apart from other metal powder production methods:
- Highly Spherical Particles: Plasma atomization produces near-perfectly spherical particles with minimal satellite particles (fused or partially fused particles). This translates to improved flowability, packing density, and printability in additive manufacturing applications.
- Superior Purity: The high temperatures and rapid solidification achieved during plasma atomization result in minimal gas entrapment and reduced levels of impurities, leading to higher-quality powders with improved mechanical properties.
Applications Galore: Where Plasma Atomized Powders Shine
The versatility of plasma atomized metal powders extends beyond their diverse material properties. These microscopic marvels find applications in a multitude of industries, shaping the world around us in fascinating ways:
1. Additive Manufacturing (AM): Often referred to as 3D printing, AM is revolutionizing the way we manufacture complex objects. Plasma atomized powders, with their excellent flowability and near-perfect sphericity, are the ideal feedstock for various AM techniques, including laser melting, electron beam melting, and binder jetting. These powders enable the creation of intricate components with reduced waste, design flexibility, and lightweight construction.
2. Aerospace Industry: The relentless pursuit of lightweight, high-strength materials for aircraft and spacecraft has led the aerospace industry to embrace plasma atomized powders. Titanium and aluminum powders, renowned for their strength-to-weight ratio, are extensively used in aircraft structures, engine components, and lightweight spacecraft parts. Additionally, nickel and cobalt-based superalloy powders find application in turbine blades and rocket engine components due to their exceptional high-temperature strength and oxidation resistance.
3. Medical Devices: The medical field heavily relies on materials that are both biocompatible and possess superior mechanical properties. Plasma atomized titanium and tantalum powders fit the bill perfectly, being used in joint replacements, dental implants, and surgical instruments. Their excellent biocompatibility minimizes the risk of rejection by the body, while their strength and durability ensure long-term functionality of implants.
4. Automotive Industry: The quest for fuel efficiency and lightweight vehicles has driven the automotive industry towards innovative materials. Aluminum and steel powders produced through plasma atomization are increasingly being utilized in car components like body panels, engine blocks, and suspension parts. These powders offer weight reduction benefits while maintaining the required strength and performance.
5. Energy Sector: The ever-growing demand for clean energy has opened doors for plasma atomized powders in the energy sector. Nickel and cobalt powders are crucial components in fuel cell electrodes, playing a vital role in the conversion of chemical energy into electrical energy. Additionally, tungsten and molybdenum powders find application in high-temperature components within nuclear power plants.
6. Other Applications: The reach of plasma atomized powders extends beyond the aforementioned industries. These versatile powders are utilized in various other applications, including:
- Thermal spraying: Coating surfaces for wear resistance, corrosion protection, and thermal management.
- Metal injection molding (MIM): Producing complex, near-net-shape metal components with intricate details.
- Brazing and welding: Joining dissimilar materials using high-melting point powders.
- Catalytic converters: Employing platinum and palladium powders to reduce harmful emissions in automotive exhaust systems.
Weighing the Pros and Cons
While plasma atomization offers numerous advantages, it’s important to acknowledge the limitations associated with this technology:
Pros:
- Highly pure and spherical powders: Leading to improved performance in various applications.
- Wide range of materials: Catering to diverse industry needs.
- Fine particle size control: Enabling the creation of intricate features and high-resolution components.
Cons:
- High energy consumption: The process demands significant amounts of energy, impacting the environmental footprint and production cost.
- Complex and expensive equipment: Setting up and maintaining plasma atomization equipment requires substantial investment.
- Limited production capacity: Compared to other powder production methods, plasma atomization often has a lower production rate.
Finding the Right Plasma Atomized Metal Powder Supplier
With a plethora of plasma atomized metal powder suppliers in the market, selecting the right one can be daunting. Here are some key factors to consider:
- Material availability: Ensure the supplier offers the specific metal powder you require.
- Powder specifications: Verify that the powder’s size, morphology, and purity meet your application’s needs.
- Quality control: Choose a supplier with a robust quality control system to ensure consistent and reliable powder quality.
- Technical expertise: Opt for a supplier with a team of experts who can provide technical support and guidance.
- Pricing and lead times: Compare pricing and delivery times from different suppliers to find the best fit for your budget and project timeline.
Demystifying Plasma Atomized Metal Powder Costs
Just like any other product, the cost of plasma atomized metal powders varies depending on several factors:
1. Material: The type of metal used is a significant cost driver. Rare earth metals like tantalum and precious metals like platinum generally command higher prices compared to common metals like iron and aluminum. This variation reflects the rarity, extraction difficulty, and overall processing costs of the raw materials.
2. Powder Specifications: The desired particle size, morphology, and purity significantly impact the cost. Finer powders, powders with specific morphologies (e.g., highly spherical), and powders with higher purity levels require more intricate processing steps and stricter quality control measures, leading to a higher price tag.
3. Volume: As with most products, bulk purchases typically offer cost benefits compared to smaller orders. This is due to economies of scale, where the production cost per unit decreases as the total volume increases.
4. Supplier: Different suppliers may have varying pricing structures based on their production capacity, overhead costs, and geographical location. Comparing quotes from multiple reputable suppliers is crucial to ensure you get the best value for your budget.
Here’s an illustrative example:
A kilogram of commercially pure titanium powder with an average particle size of 50 micrometers might cost around $50-70, while the same quantity of high-purity, near-spherical titanium powder with a finer particle size of 10 micrometers could cost upwards of $100-150. In contrast, a kilogram of iron powder with a larger particle size of 100 micrometers might be priced as low as $5-10.
It’s important to note that these are just estimated ranges, and the actual price may vary depending on the specific factors mentioned above.
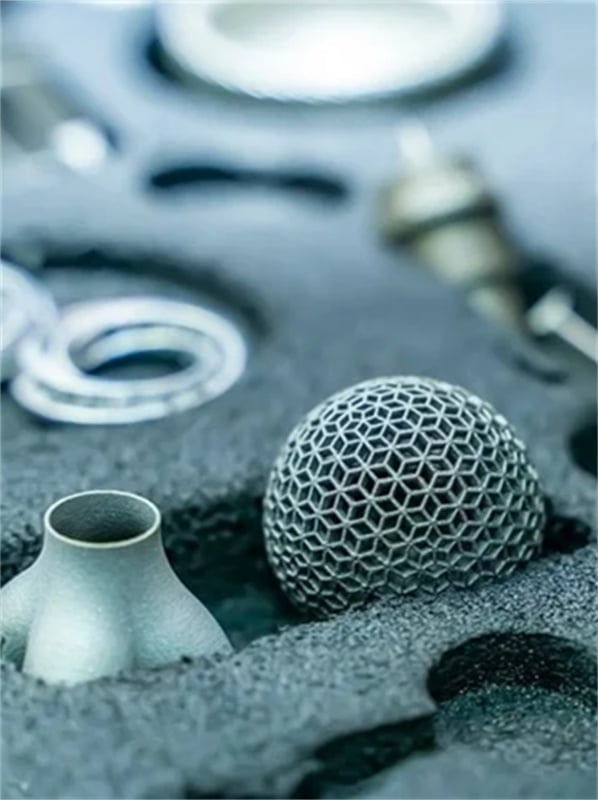
FAQ
Q: What are the advantages of plasma atomized metal powders compared to other powder production methods?
A: Plasma atomization offers several advantages, including:
- Highly spherical particles: Improved flowability, packing density, and printability in AM applications.
- Superior purity: Minimal gas entrapment and reduced impurities, leading to higher-quality powders.
- Fine particle size control: Enables the creation of intricate features and high-resolution components.
Q: What are the limitations of plasma atomized metal powders?
A: The limitations of plasma atomization include:
- High energy consumption: Impacts the environmental footprint and production cost.
- Complex and expensive equipment: Requires substantial investment for setup and maintenance.
- Limited production capacity: Compared to other powder production methods, plasma atomization often has a lower production rate.
Q: How do I choose the right plasma atomized metal powder supplier?
A: When selecting a supplier, consider the following factors:
- Material availability: Ensure they offer the specific metal powder you require.
- Powder specifications: Verify that the powder meets your application’s needs.
- Quality control: Choose a supplier with a robust quality control system.
- Technical expertise: Opt for a supplier with a team of experts who can provide support.
- Pricing and lead times: Compare pricing and delivery times from different suppliers.
Q: What does the future hold for plasma atomization technology?
A: The future of plasma atomization is promising, with ongoing research focused on:
- Reducing energy consumption: Exploring alternative energy sources and optimizing processes.
- Developing new materials: Tailoring powder properties for specific applications.
- Increasing production rates: Implementing advancements in technology to enhance productivity.
Share On
MET3DP Technology Co., LTD is a leading provider of additive manufacturing solutions headquartered in Qingdao, China. Our company specializes in 3D printing equipment and high-performance metal powders for industrial applications.
Inquiry to get best price and customized Solution for your business!
Related Articles
About Met3DP
Recent Update
Our Product
CONTACT US
Any questions? Send us message now! We’ll serve your request with a whole team after receiving your message.
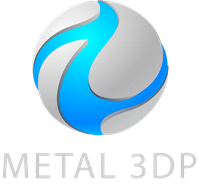
Metal Powders for 3D Printing and Additive Manufacturing