Mechanical Alloying for 3D Printing Metal Powder
Table of Contents
Detailed Introduction to Mechanical Alloying 3D Printing Metal Powder:
Imagine crafting intricate objects layer by layer, not with clay or paint, but with metal. This futuristic vision is the essence of 3D Printing Metal Powder, and mechanical alloying plays a crucial role in creating the metallic building blocks – the 3D printing metal powders.
Unlike traditional methods that involve melting and atomizing bulk metals, mechanical alloying offers a powder-to-powder approach. It harnesses the power of high-energy ball milling to transform elemental or pre-alloyed powders into a uniform mixture with tailored properties. This opens doors to a universe of possibilities in the realm of 3D printing metals, allowing engineers to unlock the potential of advanced alloys with unique characteristics.
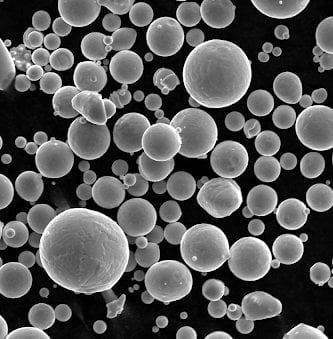
Key Parameters of Mechanical Alloying and their Impact on Final Powder Quality:
The dance between powder quality and mechanical alloying parameters is a delicate one. Mastering these parameters is crucial for achieving the desired microstructure, morphology, and flowability of the final powder. Let’s delve deeper into some key players:
- Milling time and speed: Imagine shaking a cocktail shaker. Extending the shaking time (milling time) and increasing the intensity (milling speed) lead to finer particles and more homogenous mixing. However, overdoing it can introduce contamination and excessive particle fragmentation, affecting flowability.
- Ball-to-powder ratio (BPR): Picture the balls in the shaker as tiny hammers. A higher BPR (more balls) signifies more impacts on the powder particles, leading to faster mixing and finer powders. However, an excessively high BPR can also trap powder between balls, hindering efficient mixing.
- Milling atmosphere: Just like adding ice affects your cocktail, the environment matters in milling. Using an inert gas atmosphere like argon prevents oxidation and maintains the desired powder chemistry.
These parameters, along with powder material properties and mill geometry, work together to orchestrate the creation of high-quality 3D printing metal powders.
Exploring the Metal Powder Landscape
The world of 3D printing metal powders is teeming with diverse options, each boasting unique strengths and applications. Here are 10 compelling examples:
1. Stainless Steel 316L:
- Composition: Primarily iron, chromium, nickel, and molybdenum
- Properties: Excellent corrosion resistance, biocompatibility, and high strength
- Applications: Widely used in medical implants, aerospace components, and jewelry
2. Inconel 625:
- Composition: Nickel-chromium-based superalloy with additions of molybdenum, niobium, and iron
- Properties: Exceptional high-temperature strength, oxidation resistance, and creep resistance
- Applications: Ideal for turbine blades, heat exchangers, and rocket engine components
3. Titanium-6 Aluminum-4 Vanadium (Ti-6Al-4V):
- Composition: Titanium alloy with aluminum and vanadium additions
- Properties: Excellent strength-to-weight ratio, biocompatibility, and good corrosion resistance
- Applications: Widely used in aerospace components, medical implants, and prosthetics
4. Aluminum Si10Mg:
- Composition: Aluminum alloy with silicon and magnesium additions
- Properties: Good strength, lightweight, and excellent castability
- Applications: Suitable for automotive components, electronics enclosures, and consumer goods
5. Copper:
- Composition: Pure copper
- Properties: Excellent electrical conductivity and thermal conductivity
- Applications: Used in heat sinks, electrical connectors, and heat exchangers
6. Nickel:
- Composition: Pure nickel
- Properties: Good corrosion resistance, electrical conductivity, and ductility
- Applications: Used in battery electrodes, chemical processing equipment, and electronic components
7. Hastelloy C-276:
- Composition: Nickel-chromium-molybdenum-tungsten superalloy
- Properties: Exceptional corrosion resistance to a wide range of chemicals, high-temperature strength, and good wear resistance
- Applications: Used in chemical processing equipment, pollution control systems, and nuclear power plants
8. CoCrMo (Cobalt-Chromium-Molybdenum):
- Composition: Cobalt-chromium alloy with molybdenum additions
- Properties: Excellent biocompatibility, wear resistance, and high strength
- Applications: Widely used in orthopedic implants, dental restorations, and joint replacements
9. Maraging Steel:
- Composition: Iron-based alloy with additions of nickel, molybdenum, titanium, and aluminum
- Properties: High strength, toughness, and good ductility even at high strengths
- Applications: Used in aerospace components, tooling, and high-performance sporting goods
10. Nickel-Aluminum Bronze:
- Composition: Copper alloy with additions of nickel and aluminum
- Properties: Good corrosion resistance, wear resistance, and excellent castability
- Applications: Used in marine hardware, bearings, and wear plates
This diverse selection showcases just a glimpse of the vast potential of 3D printing metal powders. Each material offers unique advantages, making them suitable for a wide range of applications in various industries.
Applications of Mechanical Alloyed Powders in 3D Printing:
The ability to tailor the properties of metal powders through mechanical alloying opens doors to exciting possibilities in 3D printing:
- Production of complex geometries: Unlike traditional manufacturing methods limited by geometry, 3D printing allows for the creation of intricate shapes and internal features with these powders.
- Lightweighting: By using metal powders with high strength-to-weight ratios, engineers can design and manufacture lightweight components for applications like aerospace and automotive industries.
- Material innovation: Mechanical alloying facilitates the development of novel metal alloys with properties not achievable through conventional methods, pushing the boundaries of what’s possible in material science.
- Customization: The ability to precisely control powder properties allows for tailoring materials to specific application requirements, leading to performance optimization.
Pros and Cons of Mechanical Alloying for 3D Printing Metal Powders:
Advantages:
- Tailored properties: Allows for the creation of powders with specific microstructures, morphologies, and flowability to meet diverse printing and application needs.
- Powder-to-powder approach: Eliminates the need for melting and atomization, potentially reducing costs and energy consumption.
- Scalability: The process can be scaled up or down to meet production demands.
- Compatibility with various 3D printing technologies: Mechanically alloyed powders can be used in various additive manufacturing techniques like selective laser melting (SLM) and electron beam melting (EBM).
Disadvantages:
- Cost: The process can be more expensive compared to traditional methods like gas atomization, especially for large-scale production.
- Powder contamination: Careful process control is necessary to minimize contamination from milling media and the environment.
- Limited production capacity: Compared to high-volume atomization techniques, mechanical alloying might have lower production capacities.
- Process optimization: Each material and desired powder characteristic requires careful optimization of milling parameters, which can be time-consuming and require expertise.
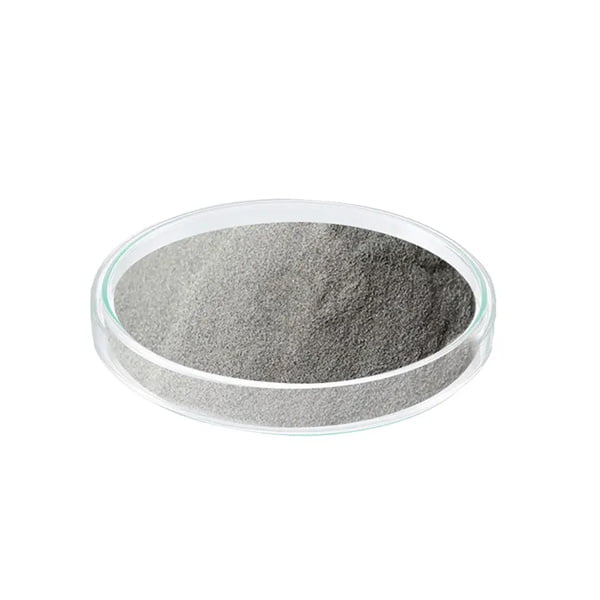
FAQ
Q: What are the advantages of using mechanically alloyed powders in 3D printing?
A: The main advantages include the ability to tailor powder properties, potentially lower cost and energy consumption compared to some traditional methods, scalability, and compatibility with various 3D printing technologies.
Q: What are the disadvantages of using mechanically alloyed powders in 3D printing?
A: The disadvantages include potentially higher cost compared to high-volume atomization, risk of powder contamination, limitations in production capacity, and the need for process optimization for each material and desired powder characteristic.
Q: What are some of the applications of mechanically alloyed powders in 3D printing?
A: These powders can be used to produce complex geometries, lightweight components, novel materials with unique properties, and customized parts tailored to specific needs.
Q: What are some of the challenges associated with mechanical alloying for 3D printing metal powders?
A: Some challenges include controlling costs, minimizing contamination, ensuring sufficient production capacity, and optimizing the process for different materials and desired powder characteristics.
Conclusion
Mechanical alloying presents a powerful tool for unlocking the potential of 3D printing metals. By enabling the creation of tailored metal powders with unique properties, this technology paves the way for innovation and advancement in various industries. As research and development continue, we can expect to see even more sophisticated applications emerge, further blurring the lines between imagination and reality in the realm of 3D printing.
Share On
MET3DP Technology Co., LTD is a leading provider of additive manufacturing solutions headquartered in Qingdao, China. Our company specializes in 3D printing equipment and high-performance metal powders for industrial applications.
Inquiry to get best price and customized Solution for your business!
Related Articles
About Met3DP
Recent Update
Our Product
CONTACT US
Any questions? Send us message now! We’ll serve your request with a whole team after receiving your message.
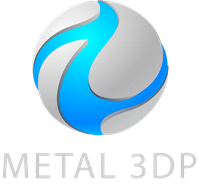
Metal Powders for 3D Printing and Additive Manufacturing