Tool steel 3D printing metal powder
Table of Contents
Imagine crafting complex tools directly from a digital file, with intricate geometries and exceptional strength. This isn’t science fiction; it’s the reality of 3D printing metal powders for tool steel. This innovative technology is transforming manufacturing, offering unparalleled design freedom, reduced lead times, and superior part performance.
But what exactly is tool steel 3D printing metal powder, and how does it work? Buckle up, because we’re diving deep into this revolutionary process, exploring its applications, advantages, challenges, and the future it holds.
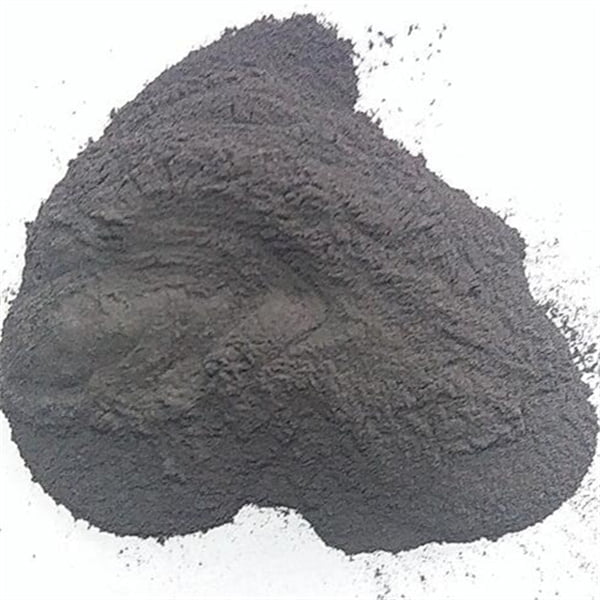
Applications of 3D Printing Metal Powder on Tool Steel
Tool steels are renowned for their toughness, wear resistance, and ability to hold their shape under extreme pressure. Traditionally, these tools were machined from solid blocks, a process that can be time-consuming, wasteful, and limited in design complexity.
3D printing metal powder for tool steel changes the game entirely. Here’s a glimpse into the exciting applications:
- Injection Molding Tools: Imagine crafting intricate mold cores and cavities with internal cooling channels – all in one go. 3D printing allows for near-net-shape production, minimizing machining needs and reducing cycle times significantly.
- Die Casting Tools: Complex die components with conformal cooling channels can be readily printed, leading to faster cooling, improved casting quality, and extended tool life compared to conventionally manufactured counterparts.
- Forming Tools: Think punches, dies, and bending tools with intricate geometries. 3D printing unlocks the potential to create lightweight tools with internal strengthening ribs, optimizing strength-to-weight ratios.
- Cutting and Stamping Tools: Imagine crafting custom inserts for cutting and stamping dies, each tailored to the specific job at hand. This allows for rapid prototyping and optimization of cutting performance.
- Repair and Refurbishment: Worn-out sections of a tool can be selectively printed and reintegrated, extending the tool’s lifespan and minimizing downtime.
These are just a few examples. The possibilities are truly endless, as 3D printing empowers manufacturers to create complex tool geometries that were previously impossible or uneconomical with traditional methods.
Types of 3D Printed Metal Powders for Tool Steel
Not all tool steel powders are created equal. Different powder types offer distinct advantages depending on the specific application:
- Pre-alloyed Powders: These powders contain all the alloying elements pre-mixed, offering consistent material properties throughout the printed part. They are ideal for high-performance tools demanding dimensional accuracy and consistent performance.
- Mixed Element Powders: Individual metal powders (like iron, chromium, and molybdenum) are blended together. This offers greater flexibility in tailoring the material properties but requires precise control during the printing process.
- Water-Atomized Powders: Produced by a high-pressure water jet, these powders are generally coarser and more affordable. They are suitable for applications where surface finish is less critical, such as base layers in multi-material printing.
- Gas-Atomized Powders: These finer powders are created by rapidly cooling molten metal droplets with an inert gas. They offer superior flowability, leading to better packing density and smoother surface finishes in the printed parts. This makes them ideal for intricate tool geometries.
The choice of powder depends on factors like the desired tool properties, printer compatibility, and cost considerations. Working with a reputable 3D printing service provider can help you navigate these options and select the best powder for your specific needs.
The Advantages of 3D Printing Metal Powder on Tool Steel
The benefits of using 3D printing metal powder for tool steel are numerous and impactful:
- Design Freedom: Unleash your creativity. Complex internal features, cooling channels, and lightweight structures become readily achievable, pushing the boundaries of tool design.
- Reduced Lead Times: Gone are the days of lengthy machining processes. 3D printing allows for rapid prototyping and production of tools, accelerating your time-to-market.
- Material Efficiency: With near-net-shape printing, minimal material waste occurs compared to traditional machining methods. This translates to cost savings and a more environmentally friendly manufacturing process.
- Improved Performance: 3D printing allows for the creation of tools with conformal cooling channels, leading to faster cycle times and improved product quality in processes like injection molding.
- Lightweight Tools: The ability to create complex internal structures allows for lighter tool designs without compromising strength. This translates to reduced machine wear, lower energy consumption, and improved ergonomics.
- Customization: 3D printing empowers you to personalize tools for specific applications, optimizing performance and meeting unique production needs.
These advantages are revolutionizing the manufacturing landscape, allowing companies to bring innovative tools to market faster and more efficiently.
The Challenges of 3D Printing Metal Powder on Tool Steel
While the potential of 3D printing metal powder for tool steel is undeniable, there are challenges to consider:
- High Cost: The technology is still evolving, and the cost of 3D printing metal powder, along with the printers themselves, can be significantly higher compared to traditional manufacturing methods.
- Surface Finish: While advancements are being made, 3D printed metal parts can have a rougher surface finish compared to machined components. This may require additional post-processing steps depending on the application.
- Material Properties: Achieving the exact material properties of traditionally manufactured tool steel can be a challenge with 3D printing. Careful selection of powder type and optimization of printing parameters are crucial.
- Limited Printer Availability: Industrial-grade 3D metal printers are not as widely available as traditional CNC machines. This can limit accessibility for smaller manufacturers.
- Process Expertise: Operating a 3D metal printer requires specialized knowledge and skillsets. Companies may need to invest in training or partner with experienced service providers.
Despite these challenges, the rapid advancements in 3D printing technology are continuously pushing the boundaries. As costs decrease, printer availability increases, and material properties improve, 3D printing metal powder for tool steel is poised to become a mainstream manufacturing technique.
Considering 3D Printing Metal Powder for Tool Steel
Is 3D printing metal powder for tool steel right for you? Here are some key factors to consider:
- Complexity of your tool design: If your tool requires intricate geometries or internal features, 3D printing can offer significant advantages in design freedom.
- Production volume: For high-volume production runs, traditional methods might still be more cost-effective. However, 3D printing shines for low-volume, custom, or complex tools.
- Lead time requirements: Need to get your tool to market quickly? 3D printing can significantly reduce lead times compared to traditional machining.
- Budget: While costs are coming down, 3D printing metal powder can be expensive. Carefully evaluate the return on investment for your specific application.
Here are some additional tips for success:
- Partner with a reputable 3D printing service provider: Their expertise can guide you through the process, select the right powder and printing parameters, and ensure optimal results.
- Invest in design for additive manufacturing (DFAM): Understanding the design principles for 3D printing can help you design tools that leverage the full potential of this technology.
- Start small and iterate: Begin with a simple tool design and gradually progress towards more complex geometries as you gain experience and confidence with the process.
By carefully considering these factors and following these tips, you can leverage the power of 3D printing metal powder for tool steel to create innovative tools, improve your production efficiency, and gain a competitive edge.
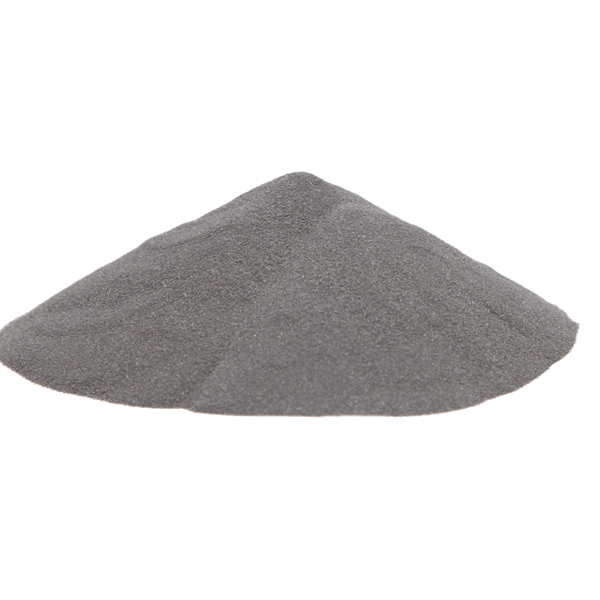
FAQ
Q: What are the different types of 3D printers used for tool steel printing?
A: Several 3D printing technologies can be used for tool steel, including:
- Selective Laser Melting (SLM): A high-powered laser beam selectively melts the metal powder layer by layer, building the tool. It offers excellent resolution and detail but can be expensive.
- Electron Beam Melting (EBM): Similar to SLM, but uses an electron beam for melting, often resulting in faster printing speeds and larger build volumes.
- Binder Jetting: A more affordable option that uses a liquid binder to inkjet metal powder layers together. The part then undergoes a high-temperature sintering process. This method can be limited in terms of material properties compared to SLM and EBM.
The best printing technology for your application depends on factors like budget, desired part properties, and complexity of the tool design.
Q: How strong are 3D printed tool steel parts?
A: The strength of 3D printed tool steel parts can be comparable to traditionally manufactured tools, depending on the specific powder type, printing parameters, and post-processing techniques used. 3D printing even allows for the creation of tools with internal structures that enhance strength-to-weight ratios.
Q: What are the post-processing steps involved in 3D printed tool steel parts?
A: Depending on the application and desired surface finish, post-processing steps like heat treatment, machining, and polishing may be required. Working with your 3D printing service provider can help determine the necessary post-processing steps for your specific needs.
Q: Is 3D printing metal powder for tool steel environmentally friendly?
A: Compared to traditional machining, 3D printing metal powder for tool steel offers several potential environmental benefits:
- Reduced Material Waste: Traditional machining can generate significant scrap metal. With near-net-shape printing, 3D printing minimizes material waste, leading to a more sustainable manufacturing process.
- Lower Energy Consumption: 3D printing allows for the creation of lightweight tools. This translates to reduced energy consumption during tool operation compared to heavier traditionally manufactured counterparts.
- Potential for On-Demand Manufacturing: 3D printing empowers companies to produce tools locally, minimizing transportation needs and associated emissions.
However, there are also some environmental considerations to keep in mind:
- Energy Consumption of 3D Printing: The 3D printing process itself can be energy-intensive, especially for metal printing technologies like SLM and EBM.
- Powder Handling and Disposal: Metal powders can be hazardous if not handled properly. Implementing proper safety protocols and responsible disposal procedures are crucial.
As 3D printing technology continues to evolve, the focus is on developing more energy-efficient printing processes and sustainable powder management solutions. Overall, the potential environmental benefits of reduced material waste and on-demand manufacturing make 3D printing metal powder a promising technology for a more sustainable future in tool manufacturing.
The Future of Tool Steel 3D Printing Metal Powder
The future of 3D printing metal powder for tool steel is bright. Here’s a glimpse into what we can expect:
- Reduced Costs: As technology matures and adoption increases, the cost of 3D printing metal powders and printers is expected to decrease, making it more accessible to a wider range of manufacturers.
- Advanced Powders: Development of new and improved tool steel powders with even better material properties and printability is an ongoing area of research.
- Multi-Material Printing: The ability to combine different metal powders within the same print job will open doors for even more complex and functional tool designs.
- Larger Build Volumes: Advancements in printer technology will lead to larger build volumes, enabling the creation of bigger and more intricate tools.
- Integration with AI and Machine Learning: Artificial intelligence and machine learning will play a growing role in optimizing printing parameters, ensuring consistent part quality, and potentially even automating post-processing steps.
These advancements will further expand the possibilities of 3D printing metal powder for tool steel, revolutionizing the way tools are designed, manufactured, and used across various industries.
Share On
MET3DP Technology Co., LTD is a leading provider of additive manufacturing solutions headquartered in Qingdao, China. Our company specializes in 3D printing equipment and high-performance metal powders for industrial applications.
Inquiry to get best price and customized Solution for your business!
Related Articles
About Met3DP
Recent Update
Our Product
CONTACT US
Any questions? Send us message now! We’ll serve your request with a whole team after receiving your message.
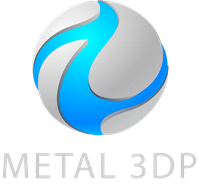
Metal Powders for 3D Printing and Additive Manufacturing