Copper 3D printing metal powder
Table of Contents
Copper, the reddish-brown metal that’s been around since the dawn of civilization, is undergoing a renaissance in the age of 3D printing. Imagine crafting intricate components with the exceptional conductivity of copper – that’s the magic of copper 3D printing metal powders. But what exactly are these powders, and how do they transform into functional objects? Buckle up, because we’re about to embark on a journey exploring the fascinating world of copper 3D printing metal powders.
Production Process of Copper 3D Printed Metal Powder
Copper 3D printing metal powders aren’t your average glitter. These meticulously crafted particles are the building blocks of high-performance 3D printed components. Here’s a peek behind the curtain of their production process:
- Atomization: The magic begins with molten copper, heated to a scorching temperature. This molten metal is then blasted with an inert gas (like argon or nitrogen) using various techniques like gas atomization or water atomization. The high-pressure gas stream breaks the molten copper into tiny droplets, which rapidly solidify into spherical copper particles.
- Classification: Not all copper particles are created equal. After atomization, the powder undergoes a rigorous classification process. Sieves or air classifiers separate the particles based on their size and morphology (shape). A consistent particle size distribution is crucial for successful 3D printing, ensuring smooth powder flow and proper melting during the printing process.
- Surface Modification: Sometimes, an extra layer of sophistication is added. For specific applications, the copper particles might be coated with a thin layer of another element or compound. This surface modification can enhance properties like flowability, printability, or even introduce new functionalities like improved corrosion resistance.
The Final Product: After these meticulous steps, we have our hero – copper 3D printing metal powder. These free-flowing, spherical particles, typically ranging from 15 to 53 micrometers in diameter, are ready to be fed into 3D printers and coaxed into complex and functional objects.
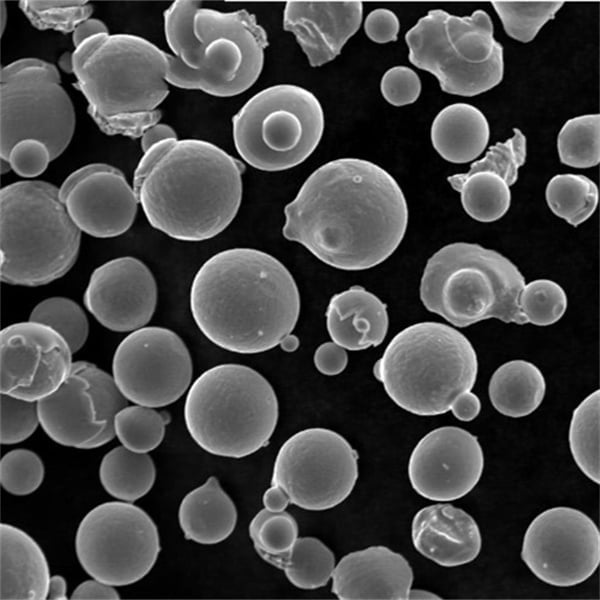
Applications of Copper 3D Printing Metal Powder
Copper’s unique blend of properties – exceptional thermal and electrical conductivity, good corrosion resistance, and excellent machinability – makes it a highly sought-after material for various applications. 3D printing unlocks a new dimension in utilizing these properties, allowing the creation of intricate copper components with unprecedented design freedom. Here are some captivating applications where copper 3D printing metal powder shines:
- Electronics: Copper’s stellar electrical conductivity makes it ideal for fabricating intricate electrical components like waveguides, antennas, and heat sinks used in high-frequency circuits. 3D printing allows for the creation of complex internal structures within these components, optimizing performance and miniaturization.
- Heat Exchangers: Efficient heat transfer is vital for numerous applications, from automotive radiators to power generation plants. 3D printed copper heat exchangers offer intricate designs with superior heat dissipation capabilities compared to traditional manufacturing methods. Imagine a customized heat exchanger designed specifically for a high-performance race car engine – that’s the power of 3D printing with copper.
- Aerospace and Defense: Weight reduction is paramount in aerospace and defense applications. Copper’s excellent conductivity-to-weight ratio makes it an attractive material for components like lightweight heat sinks and electromagnetic shielding structures used in aircraft and spacecraft. 3D printing allows for the creation of complex, topology-optimized designs that shave off precious weight while maintaining structural integrity.
- Medical Devices: Biocompatible copper alloys, developed specifically for medical applications, can be 3D printed into intricate medical implants like stents and heat sinks for medical equipment. The customizable nature of 3D printing allows for the creation of patient-specific implants that perfectly match their anatomy.
These are just a few examples, and as 3D printing technology matures, we can expect to see even more innovative applications for copper 3D printing metal powders emerge.
Suppliers of Copper 3D Printing Metal Powders
The landscape of suppliers for copper 3D printing metal powders is dynamic and ever-evolving. Here are some of the leading players:
- Elementum 3D: This company offers a range of copper and copper alloy powders specifically designed for additive manufacturing using Laser Powder Bed Fusion (LPBF) technology. Their powders are known for their high purity, spherical morphology, and excellent printability.
- Höganäs: A renowned powder metallurgy company, Höganäs offers copper-based alloy powders like CuSn (copper-tin) and forAM® CuCr1Zr (copper-chromium-zirconium).
- AP Powder: This company provides a variety of copper and copper alloy powders, including atomized copper and pre-alloyed powders like CuMg (copper-magnesium). They cater to different 3D printing technologies like LPBF and Binder Jetting.
- Custom Engineered Materials (CEM): CEM offers a diverse portfolio of metal powders, including copper and copper alloys. They specialize in customizing powder properties to meet specific application requirements.
- LPW Technology: While primarily a 3D printer manufacturer, LPW Technology also offers copper and copper alloy powders optimized for their LPBF machines. This ensures compatibility and optimal performance during the printing process.
These are just a few prominent suppliers, and the market boasts numerous other companies offering copper 3D printing metal powders. Choosing the right supplier depends on various factors, including:
- Powder Properties: Consider the specific properties required for your application, such as particle size distribution, chemical composition, and surface morphology.
- 3D Printing Technology: Different 3D printing technologies might have varying powder requirements. Ensure the chosen powder is compatible with your chosen printing method (e.g., LPBF, Binder Jetting).
- Pricing and Availability: Powder prices can vary depending on the supplier, alloy composition, and powder characteristics. Factor in availability and lead times when making your selection.
Additional Considerations: Aside from the aforementioned suppliers, some companies specialize in recycling copper scrap metal into 3D printable powders. This sustainable approach offers a cost-effective option and reduces environmental impact.
Advantages and Disadvantages of Copper 3D Printing Metal Powders
Advantages:
- Design Freedom: 3D printing allows for the creation of intricate geometries that are impossible or highly challenging with traditional manufacturing methods. This opens doors for lightweight, high-performance components with optimized internal structures.
- High Conductivity: Copper’s exceptional thermal and electrical conductivity translates directly to 3D printed parts. This makes them ideal for applications like heat exchangers, waveguides, and electrical components.
- Material Efficiency: 3D printing utilizes a powder-bed fusion approach, minimizing material waste compared to traditional subtractive manufacturing techniques. This is particularly beneficial for expensive materials like copper.
- Customization: 3D printing allows for the creation of custom-designed components, perfectly tailored to specific needs. This is valuable for applications like medical implants or aerospace components requiring unique configurations.
Disadvantages:
- Cost: Copper 3D printing metal powders can be expensive compared to traditional materials like plastics. Additionally, the 3D printing process itself might incur higher costs compared to mass production techniques.
- Surface Roughness: 3D printed metal parts can exhibit a slightly rougher surface finish compared to machined components. Post-processing techniques like polishing might be required depending on the application requirements.
- Limited Material Selection: While the range of copper and copper alloy powders is expanding, it’s still not as vast as options available for traditional manufacturing methods. Research and development are ongoing to broaden the material selection for 3D printing with copper.
- Process Complexity: 3D printing with metal powders involves a higher level of complexity compared to polymer 3D printing. Factors like powder handling, machine calibration, and process parameters need to be meticulously controlled for successful printing.
Despite these limitations, the advantages of copper 3D printing metal powders are significant. As technology advances and costs decrease, we can expect this technology to become even more widespread across various industries.
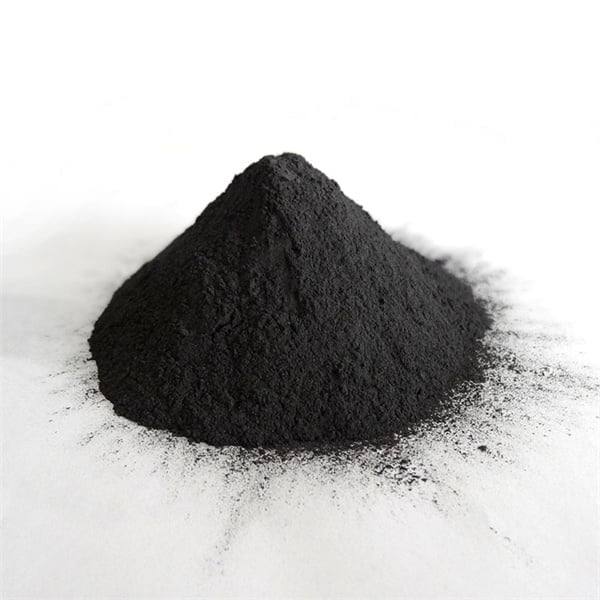
FAQ
Building on the initial table, here’s an expanded FAQ section that dives deeper into specific aspects of copper 3D printing metal powders:
Question | Answer |
---|---|
What factors influence the choice of copper 3D printing metal powder? | Several factors play a crucial role: <br> * Powder Properties: Particle size distribution significantly impacts flowability and printability. Chemical composition determines conductivity, strength, and other properties. Surface morphology can influence factors like sintering behavior. <br> * 3D Printing Technology: Different printing methods (e.g., Laser Powder Bed Fusion, Binder Jetting) might have varying powder requirements. Compatibility with your chosen printer is essential. <br> * Application Requirements: The specific application dictates the properties needed. For instance, a heat exchanger might prioritize high thermal conductivity, while an antenna might require excellent electrical conductivity. |
How does the cost of copper 3D printing metal powders compare to other materials? | Copper powders are generally more expensive than commonly used 3D printing materials like polymers (ABS, PLA). However, the exceptional properties of copper, like its high conductivity, can outweigh the initial cost in specific applications. |
Can copper 3D printed parts achieve the same level of surface finish as machined components? | In their raw state, 3D printed metal parts, including those made with copper, might exhibit a slightly rougher surface finish compared to machined components. However, post-processing techniques like polishing, tumbling, or sandblasting can significantly improve the surface finish to meet specific requirements. |
What are some future trends in copper 3D printing metal powders? | We can expect to see advancements in several areas: <br> * Material Development: The development of new copper alloys specifically designed for 3D printing, offering a wider range of properties and functionalities. <br> * Powder Production Techniques: Refined atomization techniques for tighter particle size control and potentially lower costs. <br> * Recycling Technologies: Advancements in recycling copper scrap metal into high-quality 3D printable powders, promoting sustainability and cost-effectiveness. |
Is copper 3D printing metal powder safe to handle? | Copper powder, like any fine metal dust, can pose health risks if inhaled. Proper safety precautions are crucial, including using a well-ventilated workspace, wearing appropriate personal protective equipment (PPE) like respirators and gloves, and following safe handling practices recommended by the powder supplier. |
Share On
MET3DP Technology Co., LTD is a leading provider of additive manufacturing solutions headquartered in Qingdao, China. Our company specializes in 3D printing equipment and high-performance metal powders for industrial applications.
Inquiry to get best price and customized Solution for your business!
Related Articles
About Met3DP
Recent Update
Our Product
CONTACT US
Any questions? Send us message now! We’ll serve your request with a whole team after receiving your message.
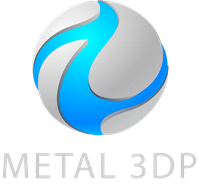
Metal Powders for 3D Printing and Additive Manufacturing