advantages of Gas Atomization for 3D Printing Metal Powders
Table of Contents
The world of 3D Printing Metal Powders continues to evolve at an astonishing pace, pushing the boundaries of what’s possible in manufacturing. At the heart of this revolution lies a crucial ingredient: metal powders. These tiny, versatile particles act as the building blocks for creating complex, functional metal objects layer by layer. But not all metal powders are created equal. Enter gas atomization, a process that stands out for its ability to produce superior metal powders, ideally suited for the demands of 3D printing.
Gas Atomization: Spherical Shape, Superior Performance
Imagine molten metal, hot enough to flow like liquid, being blasted into a high-velocity stream of gas. This, in essence, is the core principle of gas atomization. The rapidly atomized metal droplets solidify in mid-air, taking on a nearly perfect spherical shape.
But why is sphericity so crucial? Unlike irregularly shaped particles, spheres offer several advantages:
- Improved Flowability: Spherical particles flow freely, resembling tiny ball bearings, and can be easily packed and moved around during the 3D printing process. This smooth flowability is essential for consistent powder deposition and optimal printing performance.
- Enhanced Packing Density: Imagine packing oranges versus misshapen fruits in a box. Similarly, spherical metal powders pack together more efficiently, leading to higher packing density. This translates to stronger and more robust 3D printed parts with improved mechanical properties.
- Reduced Surface Area: Compared to non-spherical particles, spheres have a lower overall surface area. This translates to reduced reactivity with the surrounding environment, minimizing oxidation and other unwanted chemical reactions that can compromise powder quality and printed part performance.
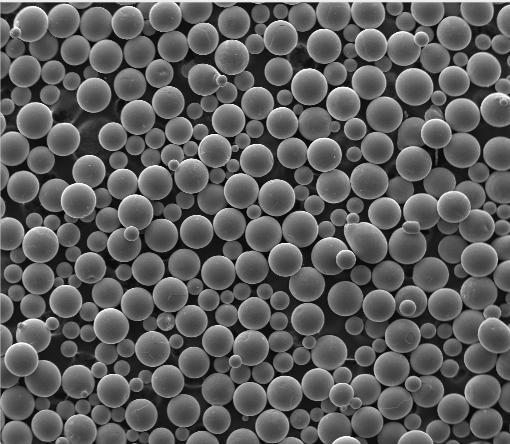
High Purity of Gas Atomization for 3D Printing Metal Powders
Gas atomization doesn’t just excel in shaping metal particles; it also plays a vital role in maintaining their purity. During the process, the molten metal is atomized in a tightly controlled inert gas environment, typically nitrogen or argon. These gases are chemically unreactive, preventing them from interacting with the metal and introducing impurities.
The result? Highly pure metal powders with minimal contamination. This purity translates to several benefits:
- Improved Mechanical Properties: Impurities can act as weak points in the 3D printed structure, compromising its strength, ductility, and fatigue resistance. High-purity powders ensure the final part exhibits the desired mechanical properties and performs reliably.
- Enhanced Corrosion Resistance: Certain impurities can accelerate corrosion, leading to premature component failure. Minimizing these impurities through gas atomization helps create corrosion-resistant parts, especially important for applications in harsh environments.
- Consistent Printability: Consistent powder composition is crucial for predictable printing behavior. High-purity powders offer consistent flow and melting characteristics, leading to repeatable and reliable 3D printing results.
Customizability: Tailoring Powders to Specific Needs
The beauty of gas atomization lies not only in its ability to produce high-quality powders but also in its customizability. By adjusting various process parameters, such as the flow rate of the molten metal and the gas pressure, manufacturers can fine-tune the properties of the resulting powder. This allows for the creation of metal powders specifically tailored to the requirements of different 3D printing technologies and desired final part characteristics.
For example, finer powders are better suited for laser-based 3D printing, while larger particles might be preferred for other methods like binder jetting. Additionally, gas atomization can be used to create alloy powders by combining different elements in a controlled manner, further expanding the range of materials available for 3D printing applications.
Beyond the Basics: A Glimpse into Advanced Techniques
Gas atomization is constantly evolving, with advanced techniques emerging to push the boundaries of powder quality and functionality. Here are some exciting developments worth mentioning:
- Electrode Induction Gas Atomization (EIGA): This technique utilizes an electromagnetic field to induce turbulence in the molten metal, leading to even finer and more uniform powder particles. This is particularly beneficial for creating high-performance parts with intricate features.
- Ultrasonic Gas Atomization (UGA): By introducing ultrasonic vibrations during the atomization process, UGA allows for the production of even smaller and more spherical powder particles. This opens doors for 3D printing of micro- and nano-scale structures.
These advancements highlight the ongoing effort to refine gas atomization and unlock its full potential in the ever-evolving world of 3D printing.
Beyond 3D Printing: Broader Applications of Gas Atomized Powders
While 3D printing is a major driving force behind the development of gas atomization technology, its applications extend far beyond this realm. Gas-atomized powders are also widely used in various other industries, including:
- Thermal Spray Coating: In this process, gas-atomized powders are melted and propelled onto a substrate to create a protective or functional coating. This coating can enhance the surface properties of the substrate, improving its wear resistance, corrosion resistance, thermal conductivity, and even electrical conductivity. Applications of thermal spray coatings include turbine engines, medical implants, and automotive parts.
- Additive Manufacturing (AM) Techniques Beyond 3D Printing: While 3D printing builds objects layer by layer, other AM techniques utilize gas-atomized powders differently. For example, in cold spray and directed energy deposition (DED), the powder is directly injected into a high-velocity stream of gas or laser beam, which melts and deposits it onto a substrate, building up the desired geometry. These techniques are particularly valuable for repairing damaged components or creating intricate features on existing parts.
- Metal Injection Molding (MIM): This process combines the benefits of metal powder and plastic molding. Gas-atomized powders are mixed with a binder to form a feedstock, which is then molded into the desired shape. The binder is later removed through a thermal debinding process, leaving behind a near-net-shape metal component. MIM is ideal for producing complex and small metal parts with high precision and repeatability.
Considering Gas Atomization for Your Needs: Key Factors to Ponder
If you’re exploring the use of metal powders in your projects, gas atomization presents a compelling option. However, it’s crucial to consider several key factors before making a decision:
- Cost: Gas atomization is a complex and energy-intensive process, which can make the resulting powders more expensive compared to other production methods.
- Material Compatibility: Not all metals are suitable for gas atomization. The process can be challenging for highly reactive materials or those with high melting points.
- Powder Requirements: The specific characteristics you need in your powder, such as particle size, shape, and composition, will influence the feasibility and cost of using gas atomization.
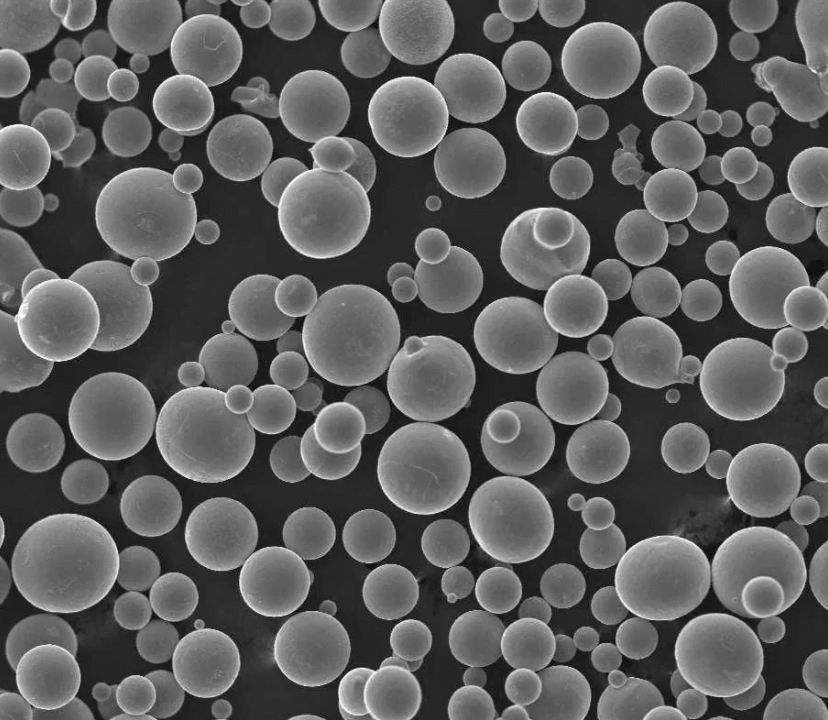
FAQs
Q: What are the advantages of gas atomization compared to other metal powder production methods like water atomization?
A: Gas atomization offers several advantages over water atomization, including:
- Spherical shape: As discussed earlier, the spherical shape of gas-atomized powders improves flowability, packing density, and reduces surface area, leading to better printing performance and reduced reactivity.
- Higher purity: The inert gas environment in gas atomization minimizes contamination, resulting in purer powders with improved mechanical properties and corrosion resistance.
- Finer particle size: Gas atomization allows for the production of finer powder particles compared to water atomization, which can be beneficial for certain 3D printing technologies and applications.
Q: Are there any limitations to gas atomization?
A: As mentioned earlier, gas atomization can be a more expensive process compared to some alternatives, and not all materials are suitable for it. Additionally, the complexity of the process requires specialized equipment and expertise, which can limit its accessibility for small-scale users.
Q: What are some future trends in gas atomization technology?
A: We can expect continued advancements in gas atomization, focusing on:
- Further refinement of powder properties: Techniques like EIGA and UGA are paving the way for even finer, more uniform, and specialized powders.
- Development of cost-effective alternatives: Exploring new methods and optimizations could potentially lead to more affordable gas-atomized powders, making them accessible to a wider range of applications.
- Expansion of material compatibility: Research efforts are ongoing to explore gas atomization for a broader variety of materials, further expanding its potential in various industries.
By understanding the advantages, limitations, and considerations surrounding gas atomization, you can make informed decisions about whether it’s the right choice for your specific metal powder needs. This technology is poised to play a crucial role in shaping the future of 3D printing and beyond, offering exciting possibilities for diverse applications across various industries.
Share On
MET3DP Technology Co., LTD is a leading provider of additive manufacturing solutions headquartered in Qingdao, China. Our company specializes in 3D printing equipment and high-performance metal powders for industrial applications.
Inquiry to get best price and customized Solution for your business!
Related Articles
About Met3DP
Recent Update
Our Product
CONTACT US
Any questions? Send us message now! We’ll serve your request with a whole team after receiving your message.
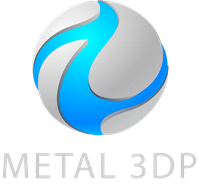
Metal Powders for 3D Printing and Additive Manufacturing