How Gas Atomization makes 3D Printing Metal Powders
Table of Contents
Imagine building intricate objects layer by layer, not with bricks and mortar, but with metallic particles. This futuristic vision is now a reality thanks to 3D printing. But creating 3D Printing Metal Powders requires a special ingredient: metal powders. And one of the leading methods for producing these powders is gas atomization.
Gas Atomization Process: Breaking Down Molten Metal into Tiny Spheres
Think of gas atomization as a high-tech shower for molten metal. Here’s how it works:
- Melting the Metal: The metal, in its solid form, is first heated up to its melting point using various methods like induction heating or electric arc furnaces. This transforms the metal into a molten liquid state.
- Atomization Chamber: The molten metal is then fed into an atomization chamber. This chamber is filled with an inert gas, typically nitrogen or argon, to prevent oxidation (rusting) during the process.
- High-Pressure Gas Jet: Inside the chamber, the molten metal stream is forced through a nozzle. A high-pressure gas jet, also made of the inert gas, is then blasted onto the molten metal stream.
- Fragmentation: This high-pressure gas jet breaks the molten metal stream into tiny droplets. Imagine a garden hose spraying water, but instead of water, we have molten metal, and the spray is forceful enough to shatter it into tiny fragments.
- Solidification and Collection: Due to the surface tension of the metal and the rapid cooling caused by the inert gas, these droplets quickly solidify into spherical metal particles. These tiny metal spheres then fall through the chamber and are collected at the bottom.
The size and distribution of the metal powder particles can be controlled by adjusting various parameters in the process, such as the pressure of the gas jet, the size of the nozzle, and the flow rate of the molten metal. This precise control over particle size is crucial for different 3D printing techniques.
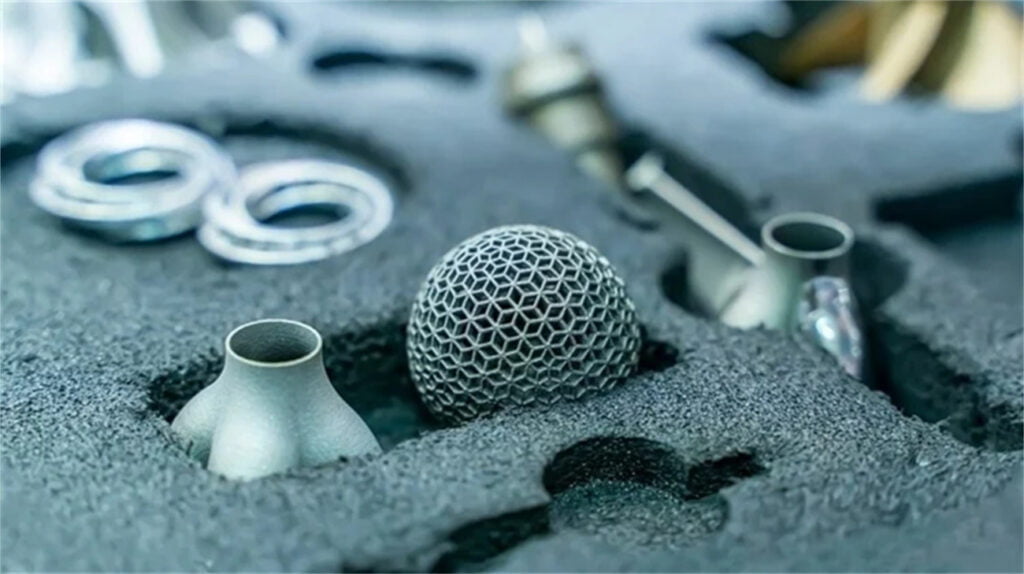
Gas atomization can produce powders with a controlled and fine particle size:
One of the key advantages of gas atomization is its ability to produce metal powders with a highly controlled and fine particle size. This is crucial for 3D Printing Metal Powders because:
- Finer particles allow for higher resolution and intricate details in the printed objects. Imagine trying to build a miniature Eiffel Tower with large, chunky pebbles versus tiny, smooth grains of sand. The finer the “grains” (metal powder particles), the more intricate and detailed the final object can be.
- Smaller particles also flow better, which is essential for many 3D printing processes. Just like pouring sand is easier than pouring large rocks, finer metal powders flow more easily through the printing equipment, ensuring a smooth and consistent printing process.
Here’s a table summarizing the key characteristics of gas-atomized metal powders:
Characteristic | Description |
---|---|
Particle Shape | Primarily spherical |
Particle Size Distribution | Tightly controlled, ranging from 10 to 150 microns (micrometers) |
Flowability | Excellent |
Purity | High |
3D Printing Metal Powders: Diverse Applications of Gas-Atomized Powders
While 3D Printing Metal Powders is a major application, gas-atomized powders have a wider range of uses:
- Metal Injection Molding (MIM): This process uses gas-atomized powders to create complex metal parts through a molding and sintering process. MIM is used to manufacture various components, such as gears, sprockets, and medical implants.
- Thermal Spraying: In this process, gas-atomized powders are melted and sprayed onto a surface to create a protective coating. This coating can improve the wear resistance, corrosion resistance, or other properties of the underlying material.
- Additive Manufacturing: Beyond 3D printing, gas-atomized powders are also used in other additive manufacturing techniques, such as laser cladding and directed energy deposition.
Advantages and Considerations of Gas Atomization
Gas atomization offers several advantages:
- High purity: The inert gas environment minimizes contamination during the process, leading to high-purity metal powders.
- Tight control over particle size and distribution: This allows for precise tailoring of the powder for specific applications.
- Scalability: The process can be scaled up to produce large quantities of powder, making it suitable for industrial applications.
Disadvantages of Gas Atomization:
- High cost: (continued) Compared to other methods like water atomization, gas atomization requires specialized equipment and controlled environments, resulting in higher production costs. This can be a barrier for smaller-scale applications or research and development purposes.
- Environmental impact: While the inert gas minimizes immediate environmental concerns, the process still requires significant energy consumption. This can be a factor to consider when choosing a powder production method, especially in the context of sustainability.
Looking Ahead: The Future of Gas Atomization
Despite these considerations, gas atomization remains a vital technology for creating high-quality metal powders for various applications. As 3D Printing Metal Powders and other additive manufacturing techniques continue to evolve, the demand for gas-atomized powders is expected to grow. Here are some exciting developments on the horizon:
- Advancements in atomization technology: Researchers are continuously exploring ways to improve the efficiency and sustainability of the gas atomization process. This includes exploring alternative energy sources, reducing gas consumption, and optimizing process parameters.
- Development of new materials: Gas atomization is not limited to traditional metals. The technology is being adapted to produce powders from a wider range of materials, including alloys, composites, and even biomaterials. This opens up exciting possibilities for creating novel materials with unique properties for diverse applications.
- Integration with automation and robotics: As automation and robotics become more sophisticated, their integration with gas atomization processes can further improve efficiency, consistency, and safety. This can lead to cost reductions and increased production capacity.
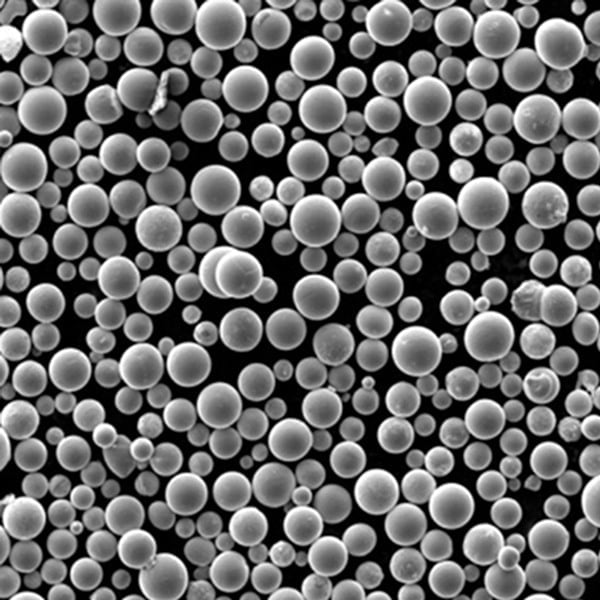
FAQ
1. What are the different types of gas atomization systems?
There are two main types of gas atomization systems: single-fluid and two-fluid. In single-fluid systems, the same gas is used for both atomization and cooling. Two-fluid systems utilize separate gas streams for atomization and cooling, offering greater control over the process.
2. What are the limitations of gas atomization?
While gas atomization offers numerous advantages, it has limitations. The high cost, potential environmental impact, and limited ability to produce certain types of powders (e.g., very fine or reactive powders) are some key considerations.
3. What are some alternatives to gas atomization?
Other methods for creating metal powders include water atomization, centrifugal atomization, and chemical reduction. Each method has its own advantages and disadvantages, and the choice of method depends on the specific application and desired powder characteristics.
4. How is the quality of gas-atomized powders controlled?
The quality of gas-atomized powders is monitored through various tests, including:
- Chemical analysis: To ensure the powder meets the desired chemical composition.
- Particle size distribution: To ensure the particles are within the specified size range.
- Flowability: To assess how easily the powder flows, which is crucial for many applications.
- Microstructure: To analyze the structure of the powder particles, which can affect their mechanical properties.
5. Where can I learn more about gas atomization?
Several resources are available online and in libraries to learn more about gas atomization, including technical articles, research papers, and industry publications. Additionally, companies specializing in gas atomization can provide valuable information about the process and its capabilities.
In conclusion, gas atomization plays a crucial role in transforming molten metal into the building blocks of a new era of manufacturing. By offering high-quality, precisely controlled metal powders, gas atomization empowers 3D printing and other advanced fabrication techniques to create intricate and innovative objects. As the technology continues to evolve and adapt, gas atomization is poised to remain a key player in shaping the future of manufacturing and material science.
Share On
MET3DP Technology Co., LTD is a leading provider of additive manufacturing solutions headquartered in Qingdao, China. Our company specializes in 3D printing equipment and high-performance metal powders for industrial applications.
Inquiry to get best price and customized Solution for your business!
Related Articles
About Met3DP
Recent Update
Our Product
CONTACT US
Any questions? Send us message now! We’ll serve your request with a whole team after receiving your message.
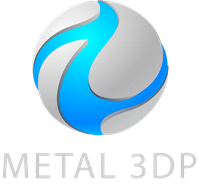
Metal Powders for 3D Printing and Additive Manufacturing