3D Printing Powder Suppliers
Table of Contents
3D printing powder is the raw material that enables powder-based additive manufacturing technologies like selective laser sintering (SLS), direct metal laser sintering (DMLS), electron beam melting (EBM), binder jetting and others. There are a growing number of providers offering these specialty powders.
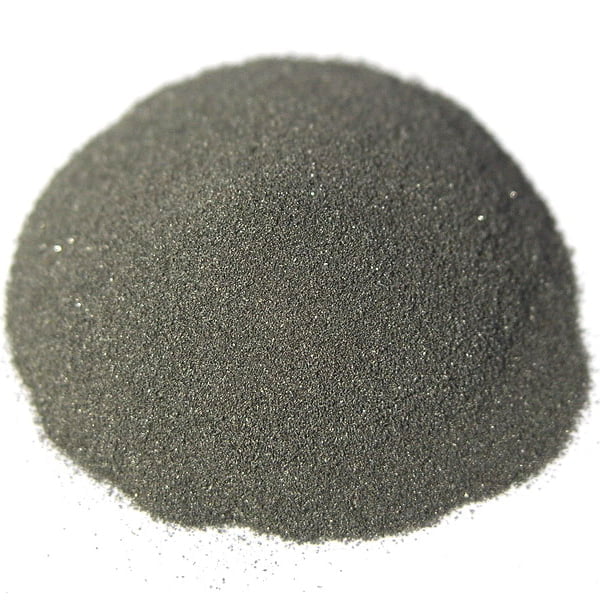
Types of 3D Printing Powder Manufacturers
There are several major categories of companies involved in this market:
Powder Type | Printing Process | Material Properties | Applications | Advantages | Disadvantages |
---|---|---|---|---|---|
Polymer Powders | Selective Laser Sintering (SLS) | – Various thermoplastics (Nylon, PA, PA 12, etc.) – High strength and durability – Good heat resistance – Wide range of colors available | – Functional prototypes – End-use parts – Manufacturing jigs and fixtures – Automotive components – Consumer goods | – High accuracy and resolution – Excellent mechanical properties – Supports complex geometries – Minimal post-processing required | – Relatively high cost per print – Limited material selection compared to other methods |
Metal Powders | Selective Laser Melting (SLM) | – Stainless steel – Titanium alloys – Inconel – Aluminum alloys – High strength-to-weight ratio – Excellent heat resistance – Corrosion resistance | – Aerospace components – Medical implants – Dental prosthetics – High-performance tools and dies – Jewelry | – Offers exceptional mechanical properties for demanding applications – Enables creation of lightweight and complex metal parts | – Requires a controlled atmosphere for printing – High cost of materials and equipment – Specialized safety precautions necessary |
Inorganic Powders | Binder Jetting | – Sand (for casting) – Ceramics (alumina, zirconia) – Glass – Biocompatible materials (hydroxyapatite) – High melting point – Wide range of material properties depending on the powder | – Sand casting molds – Production of complex ceramic and glass components – Medical and dental applications – Bone implants | – Relatively low cost per print – Wide variety of materials available – Offers good detail and resolution | – Lower strength compared to some other 3D printing methods – Requires additional post-processing steps (e.g., sintering) |
Composite Powders | Multi-Jet Fusion (MJF) | – Combinations of polymer and other materials (e.g., metal, ceramic) – Offer unique properties based on the composite mix | – Functional prototypes – Lightweight and strong components – Manufacturing aids | – Enables creation of parts with tailored properties – Offers good strength and heat resistance | – Limited availability of composite powder materials – Printing process can be complex |
Leading Global Suppliers of 3D Printing Powder
Many of the largest metal powder companies now offer 3D printing varieties:
Supplier | Material Focus | Key Products | Applications | Reputation |
---|---|---|---|---|
GKN Powder Metallurgy | Metals (Nickel alloys, titanium alloys, tool steels) | Osprey® powders – gas-atomized powders for superior flowability and printability | Aerospace (turbine blades, landing gear components), medical (dental implants), automotive (lightweight components) | Industry leader in metal powders, known for consistent quality and broad material portfolio |
Sandvik AB | Metals (Stainless steels, tool steels, superalloys) | Höganäs AM powders – offered in various particle sizes and chemistries | Aerospace (engine components, rocket parts), medical (prosthetic implants), energy (gas turbines) | Renowned for high-performance metal powders with excellent printability across various 3D printing technologies |
Arkema | Polymers (PA 12, PA 11, TPU) | Kepstan® PA powders – bio-based and sustainable polyamide powders | Automotive (interior parts, prototypes), consumer goods (sportswear, electronics), medical (drug delivery devices) | Pioneering bio-based materials for 3D printing, offering a sustainable alternative for various applications |
BASF SE | Polymers (PA 12, PA 6, TPU), Metals (stainless steel, aluminum) | Ultrafuse® and Adsorb materials – offering a range of properties for diverse applications | Automotive (functional prototypes, lightweight components), aerospace (cabin parts), medical (surgical instruments) | Diversified chemical giant providing a comprehensive portfolio of powders for both polymer and metal 3D printing |
Evonik Industries AG | Polymers (PA 12, PA 6, PEEK), Metal Additives | INFINAM® powders – high-performance and application-specific materials | Medical (orthopedic implants, surgical instruments), aerospace (structural components), industrial (jigs and fixtures) | Material science expert offering innovative powders with tailored properties for demanding applications |
Carpenter Technology | Metals (Nickel alloys, titanium alloys, specialty alloys) | Atomized powders for superior performance in demanding environments | Aerospace (high-temperature components), medical (implants requiring high biocompatibility), oil & gas (corrosion-resistant parts) | Specialty steel producer known for high-quality powders for critical applications |
LPW Technology | Metals (Nickel alloys, titanium alloys, aluminum alloys) | ScRAM (Scalable Rapid Additive Manufacturing) powders – optimized for LPW 3D printing systems | Medical (prosthetic limbs, dental implants), aerospace (structural components for launch vehicles) | Metal powder supplier with a strong focus on LPW technology, offering application-specific powders |
Höganäs AB | Metals (Steel, iron, copper) | AM powders with focus on cost-effectiveness and recyclability | Automotive (mass-produced parts), consumer goods (jewelry, decorative items), industrial (tools, functional prototypes) | Leading provider of metal powders for cost-sensitive applications, promoting sustainable practices |
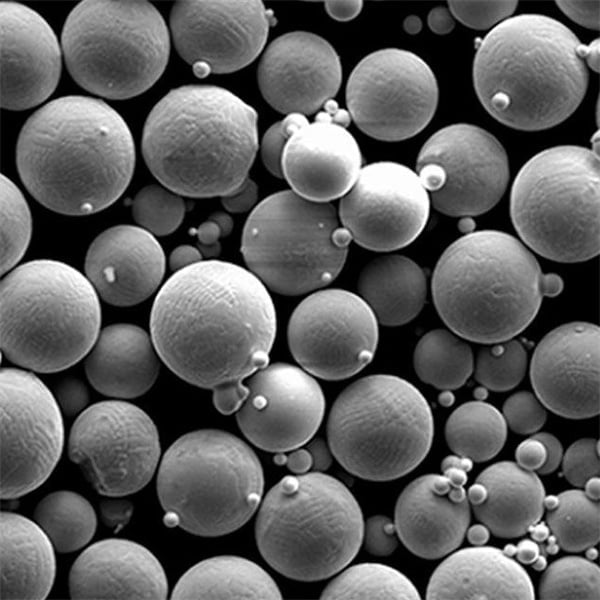
Major Polymer Material Suppliers for 3D Printing Powder
Most polymer powder for additive manufacturing still derives from large chemical producers:
Supplier | Material Focus | Key Products | Applications | Strengths | Considerations |
---|---|---|---|---|---|
GKN Powder Metallurgy | Metals | Nickel alloys, titanium alloys, stainless steel, aluminum alloys | Aerospace, automotive, medical implants | – Renowned for high-quality, spherical powders – Extensive portfolio for various printing processes (SLM, LPBF, EBM) – Strong commitment to research and development | – Limited availability of some materials in smaller quantities |
Sandvik AB | Metals & Polymers | Titanium, stainless steel, tool steel, polyamide (PA) 12 | Aerospace, medical implants, tooling | – Leading provider of gas-atomized metal powders – Offers customized powder solutions – Broad range of polymer powders for selective laser sintering (SLS) | – Focus primarily on metal powders, with a smaller selection of polymers |
Arkema | Polymers | Polyamide (PA) 12, polyamide 11 (PA11), biocompatible PA powders | Automotive, consumer goods, medical devices | – Pioneering innovations in high-performance polymer powders – Materials specifically designed for various SLS applications – Strong focus on lightweight and sustainable solutions | – Limited offering of metal powders |
BASF SE | Metals & Polymers | Nickel alloys, cobalt chrome, polyamide (PA) 12, high-temperature resistant polymers | Aerospace, automotive, chemical processing | – Extensive material portfolio for diverse applications – Offers customized powder formulations – Expertise in metal and polymer powder production | – Pricing may be higher compared to some competitors |
Evonik Industries AG | Polymers & Metal Additives | Polyamide (PA) 12, polyether ether ketone (PEEK), calcium phosphate for bone implants | Medical devices, aerospace, automotive | – Specializes in high-performance polymers for demanding applications – Biocompatible materials for medical 3D printing – Offers metal powder additives for improved printability | – Limited range of base metal powders |
Höganäs AB | Metal Powders | Steel, stainless steel, iron, copper | Additive manufacturing, metal injection molding (MIM) | – Leading producer of atomized metal powders – Consistent powder quality and tight particle size distribution – Cost-effective solutions for various applications | – Focus primarily on standard metal powders, with limited customization options |
Carpenter Technology Corporation | Metals | Nickel alloys, stainless steel, specialty alloys | Aerospace, oil & gas, medical implants | – Expertise in developing high-performance metal alloys – Powders optimized for specific printing processes – Strong focus on material properties and performance | – Relatively smaller production volume compared to some larger players |
LPW Technology Ltd. | Metals | Nickel alloys, titanium alloys, aluminum alloys, refractory metals | Aerospace, medical implants, automotive | – Offers powders specifically validated for LPBF technology – Tight collaboration with leading printer manufacturers – Focus on high-density and flowability characteristics | – Limited availability through a select network of distributors |
Distributors and Resellers of 3D Printing Powders
In addition to direct ordering from manufacturers, there are several supply chain intermediaries:
Metal Powder Distributors for Additive
Company | Key Materials Carried | Geographies Served |
---|---|---|
North American Höganäs | Metal powders from Höganäs and others | USA & Canada |
Atlantic Equipment Engineers | Broad range of ferrous and non-ferrous | USA |
Powder Alloy Corporation | Nickel, titanium, aluminum grades | USA |
American Elements | Wide variety of metals and chemicals | Global |
LPW Technology | Manufacturer and distributor | Europe, North America |
These larger distributors offer value-added services like inventory storage, logistics, and technical assistance in addition to sourcing and supplying materials. They help connect regional buyers with leading powder makers worldwide.
There are also various national distributors in countries like China, Singapore, India and others that serve more local markets. These include companies like Shanghai ST-powder Equipment. As the AM industry growth accelerates globally, more powder distributors are likely to emerge.
Polymer Material Resellers
Most major chemical firms works through networks of regional distributors and compounds to deliver their sinterable polymer powder. Leading plastic resin and filament suppliers like Polymaker, Clariant, and MakerBot also now carry 3D printing powders. And various ecommerce stores focused on serving the maker community have recently added powdered printing materials to their offerings.
As accessibility expands, more channels for obtaining polymers for powder bed fusion and binder jetting continue to open up.
Range of Materials Available from Powder Suppliers
3D printing providers and powder manufacturers now offer diverse material choices:
Metal Powder Materials for AM
Material Class | Alloy Types | Characteristics |
---|---|---|
Stainless steels | 316L, 304L, 17-4PH, 15-5PH | Corrosion resistance, bio-compatibility |
Tool steels | H13, M2, M4 | Heat and wear resistance |
Aluminum alloys | AlSi10Mg, AlSi7Mg | Light weighting, thermal conductivity |
Nickel alloys | Inconel 718, 625, Hastelloy | High strength, chemical resistance |
Cobalt chrome | CoCrMo, CoCrWNi | Biocompatibility, wear and heat resistance |
Titanium alloys | Ti6Al4V, TiAl | Aerospace & medical suitability |
New alloys continue to emerge for high temperature, wear, biocompatibility and other needs.
Polymer Powders for Additive
Material | Key Properties | Printer Compatibility |
---|---|---|
Nylon 11, 12 | Strong, versatile | Selective laser sintering |
TPU plastics | Flexible, elastic | Multi jet fusion, laser powder bed |
PEEK | Heat resistance | Laser powder bed fusion |
PEKK | Very high temperature performance | New powder bed systems |
PPSU | Hydrostability, sterilizable | Capable on various printers |
The available materials span the range of metal alloys to high performance polymers, though qualify and optimization for 3D printing continues across providers.
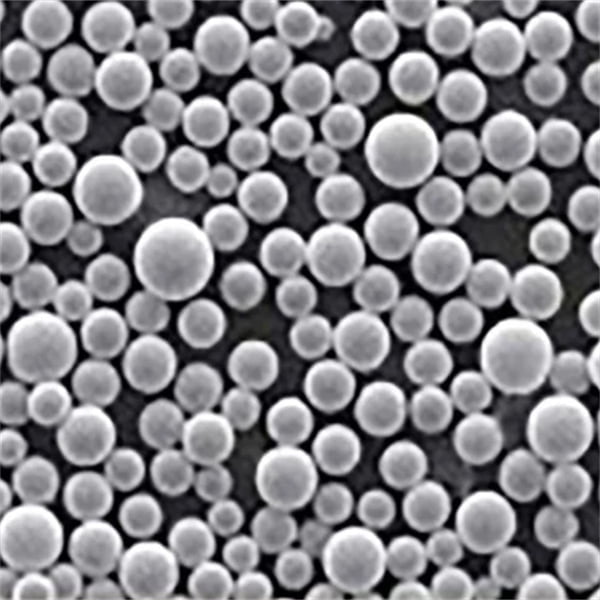
Buying Considerations for 3D Printing Powder
Factor | Description | Impact on Print | Examples |
---|---|---|---|
Application & Material Properties | This is the foundation of your decision. What will you be printing? Consider the mechanical properties (strength, flexibility), thermal properties (heat resistance), and chemical resistance needed for the final part. Will it be for functional use or a decorative piece? | Directly affects the success and functionality of the print. The wrong material can lead to warping, cracking, or not meeting its intended purpose. | – Printing a phone case: Needs a strong, slightly flexible material like Nylon 12 (PA12) for impact resistance. – Creating a gear for a machine: Requires a high-strength material like Polycarbonate (PC) that can withstand stress. – Building a decorative figurine: A more aesthetic-focused material like colored Sandstone is suitable. |
Particle Size & Distribution | The size and consistency of the powder particles significantly impact the printing process. Consistent particle size ensures even layering and minimizes printing defects. | Influences surface quality, printability, and post-processing requirements. Inconsistent particle size can lead to uneven sintering, weak layers, and the need for additional smoothing. | – Finer particles (< 50 microns) create smoother surface finishes but may be trickier to handle and require specialized printers. – Larger particles (> 100 microns) offer better flowability but can result in a rougher surface texture. |
Powder Flowability | This refers to how easily the powder moves and spreads within the printer bed. Good flowability ensures consistent material deposition and avoids printing issues. | Affects printability and influences the final part’s density and structural integrity. Poor flowability can lead to uneven layers, weak bonds, and potential printing failures. | – Powders with spherical particles tend to flow better than those with irregular shapes. – Manufacturers often offer powders with additives to improve flowability. |
Sinterability & Melting Point | Sinterability determines how well the powder particles bond together during the printing process. Melting point influences the laser or heat source settings required for proper fusion. | Crucial for achieving strong and dense final parts. Incorrect settings or a material with poor sinterability can result in weak or delaminated prints. | – SLS (Selective Laser Sintering) powders like Nylon typically have lower melting points compared to those used in SLM (Selective Laser Melting) for metals. – Materials with good sinterability require less energy input, reducing printing time and energy consumption. |
Compatibility with Printer | Ensure the chosen powder is compatible with your specific 3D printer model and printing technology (SLS, SLA, Binder Jetting, etc.). | Incompatible powders can damage the printer or lead to unsuccessful printing. | – Most printer manufacturers recommend specific powders for optimal performance. – Third-party vendors may offer compatible powders, but thorough research is necessary to ensure proper functionality. |
Safety & Handling | Some 3D printing powders, particularly metals, may pose health and safety risks. Consider the hazards associated with the material and proper handling procedures. | Protects your health and ensures a safe printing environment. | – Metal powders can be flammable, require proper ventilation, and necessitate the use of personal protective equipment (PPE). – Always refer to the Material Safety Data Sheet (MSDS) for specific handling guidelines. |
Cost & Availability | Consider the cost per unit weight and the overall budget for your project. Factor in powder waste and potential recycling options. | Impacts project budget and printing efficiency. | – Popular materials like Nylon 12 are generally more affordable than specialty materials like metal powders. – Purchasing larger quantities of powder often comes at a discounted price. |
Where to Buy 3D Printing Powder
Material | Description | Typical Price (kg) | Retailers (US) | Applications |
---|---|---|---|---|
Nylon 12 (PA12) | A versatile and robust plastic powder, ideal for functional prototypes and end-use parts. Offers a good balance between strength, stiffness, and durability. | $599 – $649 (6kg) | * MatterHackers [MatterHackers Formlabs Nylon 12 Powder] | * Automotive parts * * Gears and functional components * * Housings and enclosures * * Manufacturing jigs and fixtures |
TPU 90A | A flexible and tear-resistant powder, well-suited for creating prototypes and end-use parts that require rubber-like properties. | $799 (unknown kg) | * SourceGraphics [SourceGraphics Formlabs TPU 90A SLS Powder] | * * Gaskets and seals * * Medical wearables * * Sports equipment grips * * Prototyping elastomeric components |
Sinterit PA12 Smooth V2 | A variation of Nylon 12 powder known for its smooth surface finish, ideal for parts requiring a high aesthetic quality. | $300 (2kg) | * Top 3D Shop [Top 3D Shop Sinterit PA12 Smooth V2 Fresh Powder] | * * Concept models * * Snap-fit parts * * Consumer goods prototypes |
Metal Powders (e.g., Stainless Steel, Titanium) | Used in Selective Laser Melting (SLM) for creating high-strength and temperature-resistant metallic parts. | * Price varies depending on metal type | * 3D Powder Hub [3D Powder Hub Metal Powders] * EOS GmbH [EOS Metal Powders] * MSE Supplies [MSE Supplies Metal Powders for 3D Printing] | * * Aerospace components * * Medical implants * * Tooling and molds * * Jewelry |
Anycubic DLP Craftsman Resin | Not technically a powder, but a resin containing ceramic fillers, used in vat polymerization for creating objects with a ceramic-like finish. | $33.31 (unknown weight) | * AliExpress [AliExpress Anycubic DLP Craftsman Resin] | * * Architectural models * * Art and design prototypes * * Limited functional applications |
How Much Does 3D Printing Powder Cost?
Cost varies substantially by material:
Typical 3D Printing Powder Pricing
Material | Price per kg |
---|---|
Aluminum alloy | $25 – $65 |
Stainless steel 316L | $35 – $85 |
Tool steel H13 | $45 – $120 |
Titanium Ti64 | $170 – $450 |
Cobalt chrome | $110 – $350 |
Inconel 718 | $140 – $600 |
PA11, PA12 | $55 – $120 |
PEEK | $100 – $600 |
Prices decline at higher purchase volumes. Less common specialty grades are far more expensive. Additional costs accrue for quality checks, special handling, regulated powders. Work with suppliers to optimize delivery, testing protocols and inventory turns for your production profile and risk exposure.
Pros and Cons of Key Powder Manufacturers
Pros | Cons |
---|---|
Design Freedom and Complexity | Material Availability and Cost |
Key 3D printing powders enable the creation of intricate geometries and lattice structures that are impossible or highly complex to achieve through traditional manufacturing methods. This opens doors for innovation in lightweighting, heat dissipation, and fluid dynamics. | The variety of metal and plastic powders readily available for 3D printing is constantly expanding, but it still lags behind traditional materials. Additionally, certain high-performance powders can be significantly more expensive than their more common counterparts. |
Excellent Material Properties | Safety and Handling |
Powders can be formulated to achieve a wide range of material properties, including high strength, heat resistance, and corrosion resistance. This makes them suitable for demanding applications in aerospace, automotive, and medical industries. | Metal powders, particularly those containing fine particles, can pose a health risk if inhaled. Proper ventilation and personal protective equipment are crucial during handling and printing processes. Additionally, some reactive powders can be flammable or explosive, requiring special storage and handling procedures. |
Lightweight Parts | Post-Processing Requirements |
3D printing with certain powders, like titanium or aluminum alloys, allows for the creation of lightweight parts with high strength-to-weight ratios. This is crucial in applications where weight reduction is a primary concern, such as aerospace and prosthetics. | Most 3D printed parts from powder require some degree of post-processing, which can add time and cost to the overall production process. This may involve support structure removal, heat treatment for stress relief, and surface finishing techniques. |
Rapid Prototyping and On-Demand Manufacturing | Environmental Impact |
The ability to print directly from a digital design file allows for rapid prototyping of new designs, accelerating the development cycle. Additionally, 3D printing with powder enables on-demand manufacturing, reducing the need for large inventories and minimizing waste. | The production of metal powders can be energy-intensive, and the disposal of waste powder requires careful consideration to minimize environmental impact. Research is ongoing to develop more sustainable powder production methods and recycling processes. |
Reduced Material Waste | Printer Compatibility |
3D printing with powder utilizes a near net-shape manufacturing process, minimizing material waste compared to traditional subtractive techniques like machining. This not only reduces costs but also promotes sustainable manufacturing practices. | Not all 3D printers are compatible with all types of powders. The specific powder material, particle size, and flow characteristics need to be matched with the capabilities of the printer to ensure successful printing. |
Qualifying and Testing 3D Printing Powder
Powder producers must verify quality while part makers need to validate materials:
How Manufacturers Test Metal Powder
- Chemistry analysis via optical emission or X-ray fluorescence spectroscopy
- Particle size distribution by laser diffraction
- Shape and morphology via SEM imaging
- Density and flowability per MPIF standard methods
- Mechanical testing on pressed or sintered samples
- Short runs through customer printers for feedstock validation
How End Users Should Qualify Materials
- Review alloy chemistry certificate of analysis
- Confirm particle size distribution meets printer guidelines
- Test flow rate through system powder handling system
- Produce test parts based on standard geometry like tensile bars
- Evaluate achievable density relative to wrought properties
- Assess mechanicals like hardness, tensile strength on printed parts
- Check chemical and microstructural uniformity via microscopy
Both input stock quality and printed output characteristics must meet application requirements over multiple production lots.
Standards Around 3D Printing Powders
Aspect | Description | Importance for Successful 3D Printing |
---|---|---|
Powder Characterization | This initial phase involves analyzing the physical and chemical properties of the powder. Key tests include: | Ensures the powder is compatible with your chosen 3D printing process and delivers the desired final part properties. Inconsistent powder can lead to printing defects, poor mechanical performance, and wasted time and materials. |
* Particle size and distribution (PSD) | Measures the range of particle sizes and their relative abundance. Ideal PSD promotes good flowability, packing density, and minimizes segregation during printing. | * Influences printability, surface finish, and mechanical strength. |
* Particle morphology (shape) | Analyzes the shape of the powder particles (spherical, irregular, etc.). | * Affects packing density, flowability, and laser absorption in metal printing. |
* Chemical composition | Identifies the elements and their proportions within the powder. | * Crucial for material properties, printability, and post-processing requirements. Impurities can hinder flow, cause porosity, or alter final part characteristics. |
* Flowability | Measures how easily the powder flows under its own weight. | * Impacts printability, layer formation, and density of the final part. Poor flowability can lead to uneven layers and printing defects. |
* Apparent and tap density | Determines the packing density of the powder in loose and tapped states. | * Influences material usage, shrinkage during printing, and final part density. |
Powder Bed & Printability | This stage evaluates how the powder behaves during the printing process. Tests include: | Optimizes printing parameters for consistent, high-quality results. Improper settings can lead to printing defects, warping, or even machine failure. |
* Laser Sinterability/Melt Pool Analysis (Metal Printing) | Assesses the melting behavior and fusion characteristics of the powder under laser energy. | * Optimizes laser power, scan speed, and hatch spacing for proper melting and layer bonding. |
* Spreading & Recoating Analysis | Evaluates the powder’s ability to be spread into a uniform layer and recoated after each printing pass. | * Ensures consistent layer thickness and minimizes printing defects like delamination. |
Mechanical Properties | This stage assesses the mechanical performance of 3D printed parts from the qualified powder. Tests include: | Verifies that the final parts meet the intended application’s requirements. Subpar material properties can lead to part failure and compromise functionality. |
* Tensile strength, yield strength, and elongation | Measure the material’s ability to withstand pulling forces. | * Crucial for parts under stress, such as structural components. |
* Compressive strength | Measures the material’s resistance to crushing forces. | * Important for parts subjected to compression, like bearings. |
* Hardness | Measures the material’s resistance to indentation. | * Relevant for wear resistance and applications requiring a hard surface. |
* Fatigue strength | Evaluates the material’s ability to withstand repeated loading and unloading. | * Critical for parts experiencing cyclic stress. |
Counterfeit Powder Concerns
Aspect | Potential Risk | Example | Action to Take |
---|---|---|---|
Ingredients | * Unknown or harmful substances * Incorrect dosages of active ingredients * Absence of key ingredients | * Industrial talc (linked to cancer) in baby powder * Ineffective medication in counterfeit pain relievers * Lack of essential vitamins in fake nutritional supplements | * Look for a complete list of ingredients on the label * Research common counterfeit ingredients * Verify with a trusted source (doctor, pharmacist) if unsure |
Safety | * Contamination with bacteria or mold * Improper manufacturing processes leading to product instability * Inert fillers causing allergic reactions | * Skin irritation or infection from contaminated makeup powder * Powders that clump or cake due to poor manufacturing * Rashes or breathing problems from unknown fillers in laundry detergent | * Check for tamper-evident seals * Purchase from reputable retailers * Look for certifications from safety organizations |
Effectiveness | * Reduced or absent functionality * Inaccurate claims about the product * No discernible benefit | * Makeup powder that doesn’t provide advertised coverage * Sports drink powder with minimal electrolytes * Ineffective weight loss supplements | * Research independent reviews of the product * Compare ingredients to legitimate brands * Consult a doctor or nutritionist for product recommendations |
Economic Impact | * Loss of revenue for legitimate companies * Funding of criminal activity * Unfair competition in the marketplace | * Supports businesses that invest in research and development * Discourages illegal manufacturing practices * Protects consumer choice and quality standards | * Purchase from authorized distributors * Report suspected counterfeiting to relevant authorities * Be aware of pricing that seems too good to be true |
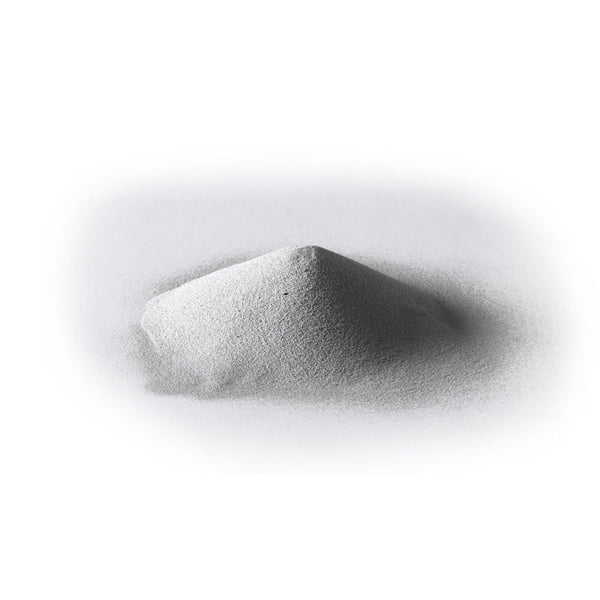
Future Outlook for 3D Printing Powder Market
The industry is poised for continued strong expansion:
- Broader materials – More metals, composites, and polymers developed
- Improved powders – Higher purity, finely tailored characteristics
- Supply logistics – Increased stocking distributors provide market access
- Price reductions – As adoption scales, costs decline expanding applications
- Quality standards – Specifications, test methods enable performance guarantees
But further progress requires:
- Continued material advancements meeting application demands
- Printer OEMs validating new grades to expand options
- Smooth supply chainintegration ensuring stock availability
- Measurement techniques to verify acceptable reuse levels
- Defined repeatability metrics to provide user safeguards
With further collaboration between powder manufacturers, printer builders, and end part makers, availability and reliability will continue improving to support a self-sustaining user base.
FAQ
Who are the best 3D printing powder suppliers?
The major global providers like Sandvik, Höganäs, Rio Tinto, Carpenter Powder Products, AP&C and Arcam EBM offer high quality materials for most common AM processes. Which is “best” depends on your specific printer, application, risk tolerance, and location.
Where can I buy small volumes of custom 3D printing powder?
Many major metal powder producers offer prototyping volumes of new alloys. Additional sources for custom powder include toll processors Pyrogenesis, Pyromet, and Specialty Metals Processing. These providers can atomize small batches of new compositions tailored to your requirements.
Should I work directly with a manufacturer or distributor to source powder?
Distributors can provide valuable warehousing, inventory management and shipping services alongside powders sourced from the top producers. This may simplify logistics significantly. But you may access a wider material selection from engaging directly with manufacturers. Define your top requirements around quality, risk, and services to pick the optimal channel.
Are there materials differences across laser and e-beam printers?
Yes, the higher temperature of electron beam melting allows higher alloying levels, larger particles sizes and faster build rates. Materials tailored for DMLM/SLM systems using lasers typically require much tighter chemistry control, smaller particles and lower apparent density. Work closely with your machine vendor to match appropriate powder specifically to your system.
Share On
MET3DP Technology Co., LTD is a leading provider of additive manufacturing solutions headquartered in Qingdao, China. Our company specializes in 3D printing equipment and high-performance metal powders for industrial applications.
Inquiry to get best price and customized Solution for your business!
Related Articles
About Met3DP
Recent Update
Our Product
CONTACT US
Any questions? Send us message now! We’ll serve your request with a whole team after receiving your message.
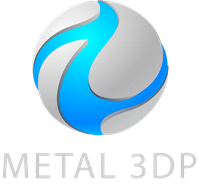
Metal Powders for 3D Printing and Additive Manufacturing