3D Printing Titanium Powder
Table of Contents
Overview of 3d printing titanium powder
Titanium is a strong, lightweight, corrosion-resistant metal that is ideal for 3D printing complex geometries for aerospace, automotive, medical, and other demanding applications. Titanium powder can be used to print full-density metal parts with excellent mechanical properties using powder bed fusion technologies like selective laser melting (SLM) and electron beam melting (EBM).
This article provides a comprehensive guide to 3d printing titanium powder covering composition, properties, specifications, applications, pros/cons, suppliers, costs, and more.
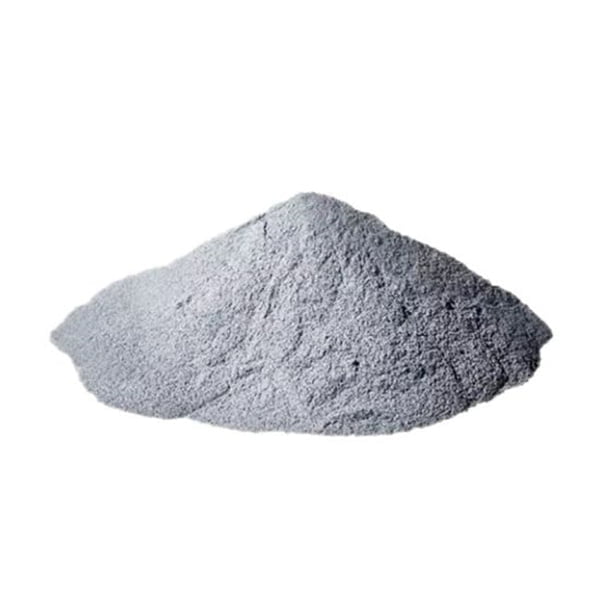
Composition of 3d printing titanium powder
Titanium powder for additive manufacturing consists almost entirely of the element titanium. However, small amounts of other elements like aluminum, vanadium, iron, oxygen, nitrogen and carbon can be present.
Titanium Grades for Powder Bed Fusion
Grade | Composition |
---|---|
Ti 6Al-4V | 90% titanium, 6% aluminum, 4% vanadium |
Ti 6Al-4V ELI | Same as Ti 6Al-4V but with lower limits for interstitial oxygen, iron and nitrogen |
Commercially Pure Titanium Grade 1 | 99.2% Minimum Titanium |
Commercially Pure Titanium Grade 2 | 99.5% Minimum Titanium |
Commercially Pure Titanium Grade 3 | 99.8% Minimum Titanium |
Commercially Pure Titanium Grade 4 | 99.9% Minimum Titanium |
Ti 6Al-4V is the most common grade used in additive manufacturing today due to its excellent strength-to-weight ratio, weldability, and corrosion resistance. The ELI variant has improved ductility and fracture toughness.
Commercially pure titanium grades have lower strength but better biocompatibility for medical implants. Grade 5 titanium with higher oxygen content is generally not used for powder bed fusion.
Properties of 3d printing titanium powder Parts
3D printed titanium parts can achieve properties similar to or exceeding traditionally manufactured titanium, with the added benefit of design freedom.
Mechanical Properties
Property | Ti 6Al-4V | Ti 6Al-4V ELI | CP Ti Grade 2 |
---|---|---|---|
Tensile Strength | 930 – 1050 MPa | 860 – 965 MPa | 345 – 485 MPa |
Yield Strength | 825 – 890 MPa | 795 – 875 Mpa | ≥ 275 MPa |
Elongation at Break | 8 – 15% | ≥10% | 20% |
Fatigue Strength | ≥ 400 MPa | ≥ 550 MPa | 275 – 550 MPa |
Fracture Toughness | 55 – 115 MPa√m | ≥ 100 MPa√m | N/A |
3D printed titanium has stiffness, hardness and wear resistance comparable to traditional titanium manufacturing methods. Post-processing like hot isostatic pressing (HIP) can further improve material properties.
Advantages
- High strength-to-weight ratio
- Corrosion resistance
- Biocompatibility and osseointegration
- Design freedom for topology optimization
- Reduced waste compared to subtractive methods
- Conformal cooling channels enable performance gains
Limitations
- High reactivity with oxygen makes handling difficult
- Print defects like porosity can reduce fatigue life
- Expensive powder material and recycling challenges
- Post-processing may be required to achieve material specs
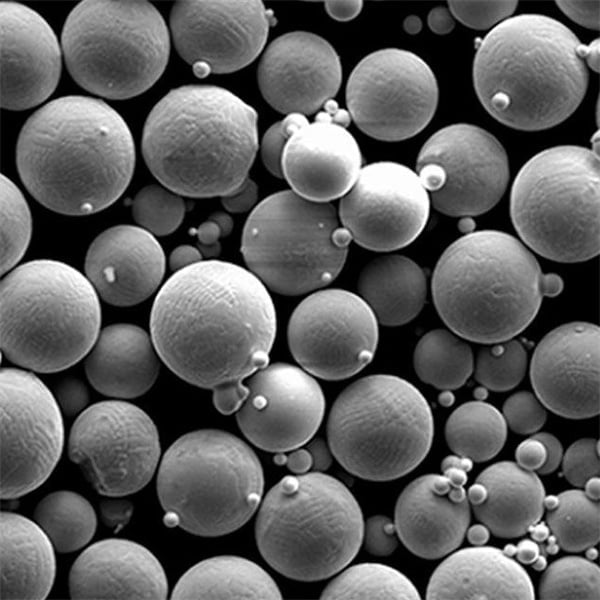
Specifications of 3d printing titanium powder
Titanium powder used for additive manufacturing needs to meet exacting standards for particle size distribution, morphology, chemistry, and other attributes.
Size Distribution
Parameter | Typical Value | Role |
---|---|---|
Particle size range | 15 – 45 microns | Determines minimum feature resolution, powder spreadability |
D10 | 20 microns | Indicates finer powder fraction |
D50 | 30 microns | Median particle size |
D90 | 40 microns | Indicates larger particles |
Apparent density | 2.7 g/cc | Packed density of powder bed, affects reproducibility |
The powder should have a near-spherical morphology with few satellites for smooth powder spreading. Chemistry must conform to grade specifications with low impurity levels.
Other Critical Attributes
- Flowability
- Residual oxygen and nitrogen content
- Apparent and tap density consistency
- Recyclability
- Chemical compatibility with process
- Handling characteristics
Meeting stringent quality requirements for each parameter is critical for defect-free builds.
Applications of 3d printing titanium powder
Industry | Application | Advantages of 3D Printing Titanium |
---|---|---|
Aerospace & Aviation | – Aircraft components (wing parts, landing gear components) – Rocket engine parts – Satellite structures | – Lightweighting: Reduced weight translates to increased fuel efficiency and longer flight ranges. – High Strength-to-Weight Ratio: Titanium parts can be strong yet light, crucial for aircraft performance. – Design Freedom: Complex, internal structures can be printed for optimized performance and weight distribution. |
Medical & Dental | – Implants (hip replacements, knee replacements, dental implants, cranial implants) – Surgical instruments – Custom prosthetics | – Biocompatibility: Titanium is well-tolerated by the human body, minimizing risk of rejection. – Customization: 3D printing allows for patient-specific implants that perfectly match their anatomy for improved fit and function. – Porous Structures: Implants can be printed with a porous structure that encourages bone ingrowth for better long-term stability. |
Automotive | – High-performance engine components (connecting rods, pistons) – Lightweight car parts – Racing components | – Strength & Durability: Titanium withstands high temperatures and pressure common in engines. – Weight Reduction: Lighter parts contribute to improved fuel economy and handling. – Complex Geometries: 3D printing allows for intricate internal channels for cooling or oil flow. |
Consumer Goods & Sports | – High-end bicycles frames – Sports prosthetics – Jewelry and eyewear | – Unique Design & Customization: 3D printing enables personalized designs and features. – Strength & Lightweight: Ideal for applications requiring both durability and minimal weight. – Biocompatibility: Suitable for prosthetics and some jewelry applications that come into contact with skin. |
Oil & Gas | – Downhole tools & equipment – Corrosion-resistant pipes & valves | – Corrosion Resistance: Titanium excels in harsh environments with exposure to chemicals and saltwater. – High Strength: Withstands the high pressure and stress encountered in oil and gas extraction. – Weight Reduction: Lighter tools can be easier to maneuver in deep wellbores. |
Research & Development | – Prototyping complex parts – Testing new designs and materials | – Rapid Iteration: 3D printing allows for quick creation and testing of new designs. – Design Freedom: Complex geometries can be printed for research purposes. – Material Exploration: Allows for printing with different titanium alloys or composites for property evaluation. |
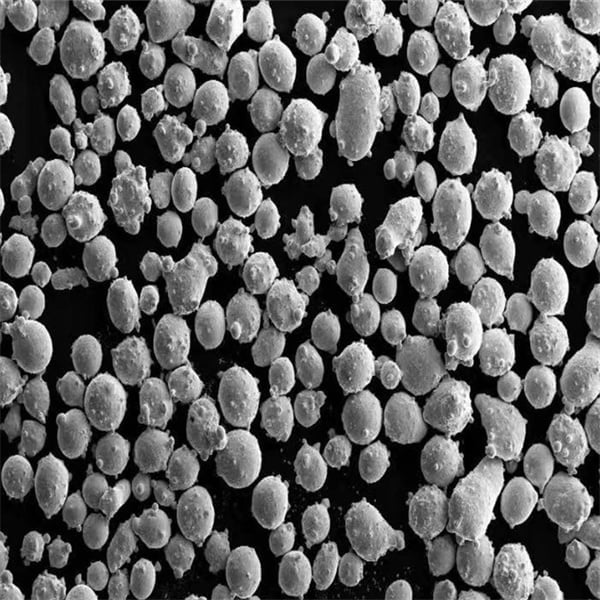
Suppliers of 3d printing titanium powder
Most titanium powder suppliers offer Ti 6Al-4V grade tailored for additive manufacturing. Some also provide custom alloy design services.
Major Titanium Powder Companies
Company | Grades Offered | Services |
---|---|---|
AP&C | Ti 6Al-4V, Ti 6Al-4V ELI | Custom alloy development |
Tekna | Ti 6Al-4V, Ti 6Al-4V ELI | Advanced plasma spheroidization |
Carpenter Additive | Ti 6Al-4V, Ti 6Al-4V ELI | Extensive QA testing |
Praxair | Ti 6Al-4V | Nitrogen atomization |
Epoch | Commercially Pure Titanium | Small quantity orders |
Many 3D printer OEMs like EOS and SLM Solutions also offer associated titanium powders. Recycled powders are lower cost but have higher impurity levels.
Titanium Powder Cost
Grade | Morphology | Price Range |
---|---|---|
Ti 6Al-4V | Spherical | $350-$1000 per kg |
Ti 6Al-4V ELI | Spherical | $500-$2000 per kg |
CP Ti grade 1-4 | Irregular | $100-$500 per kg |
Cost depends significantly on order volume, quality, supplier margins, and recycling.
Pros and Cons of 3d printing titanium powder
Feature | Pros | Cons |
---|---|---|
Material Properties | * High Strength-to-Weight Ratio: Titanium boasts exceptional strength while remaining lightweight, ideal for applications demanding weight reduction in aerospace and automotive industries. * Corrosion Resistance: Titanium’s natural resistance to corrosion makes it perfect for components exposed to harsh environments like marine or chemical settings. * Biocompatibility: The biocompatible nature of titanium allows for its safe use in medical implants, promoting osseointegration (fusion with bone) for long-term functionality. | * Limited Material Selection: Compared to traditional manufacturing with a wider variety of materials, 3D printing with titanium powder is currently restricted to a specific range of titanium alloys. |
Design and Production | * Design Freedom: 3D printing unlocks the creation of complex geometries previously impossible with traditional subtractive manufacturing methods. This allows for intricate designs that optimize performance and reduce weight. * Rapid Prototyping: The ability to quickly print prototypes from digital models facilitates faster design iterations and product development cycles. * Reduced Material Waste: Unlike subtractive manufacturing that generates significant scrap, 3D printing with titanium powder uses only the necessary material for the design, minimizing waste and production costs. | * High Initial Investment: The cost of 3D printers specifically designed for titanium powder can be substantial, making it an investment primarily suitable for high-value applications or large production facilities. * Post-Processing Requirements: 3D printed titanium parts often require additional post-processing steps such as heat treatment, support removal, and surface finishing to achieve the desired mechanical properties and aesthetics. |
Applications | * Aerospace: The ability to create lightweight, high-strength components for aircraft structures, airframes, and engine parts makes titanium 3D printing a valuable tool in the aerospace industry. * Medical: Biocompatible titanium implants like prosthetics, dental implants, and cranial implants benefit from 3D printing’s ability to create customized parts for patient-specific needs. * Motorsports: Weight reduction is crucial in motorsports. 3D printed titanium components like pistons, connecting rods, and suspension parts contribute to improved performance and handling. | * Limited Availability and Expertise: The specialized equipment and expertise required for 3D printing titanium powder can limit its widespread adoption, particularly for smaller manufacturers or applications with lower production volumes. * Safety Concerns: The process of handling titanium powder can pose health risks due to its flammability and potential for respiratory issues. Proper safety protocols and equipment are essential for a safe working environment. |
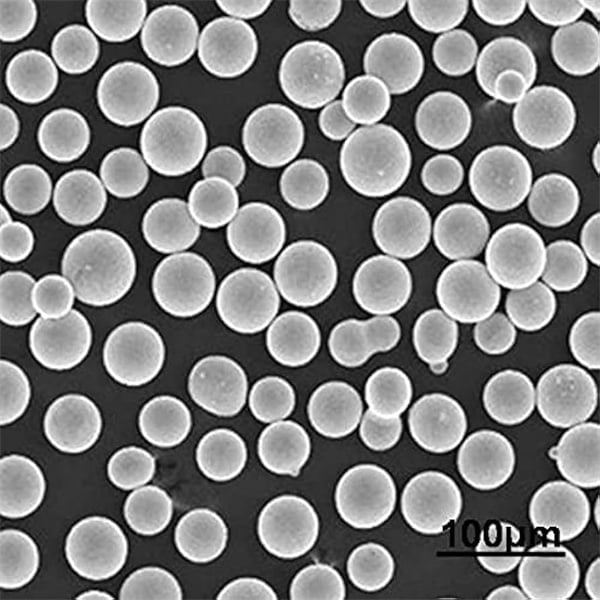
Comparison of Titanium Print Processes
Process | Technology | Material Feedstock | Build Envelope (in³) | Advantages | Disadvantages | Applications |
---|---|---|---|---|---|---|
Electron Beam Melting (EBM) | A high-powered electron beam melts titanium powder layer-by-layer in a vacuum chamber. | Titanium powder | Up to 50 x 50 x 50 | – Excellent surface finish and dimensional accuracy – Strong, near-net-shape parts with high strength-to-weight ratio – Minimal residual stress | – High cost of equipment and operation – Limited build envelope compared to other methods – Rough surface texture on non-support surfaces | – Aerospace components (turbine blades, landing gear) – Medical implants (hip sockets, dental implants) |
Laser Beam Melting (LBM) | A high-powered laser beam melts titanium powder layer-by-layer in an inert gas environment. | Titanium powder | Up to 120 x 120 x 120 | – High precision and resolution – Wide range of compatible titanium alloys – Good mechanical properties | – Requires a sealed chamber with inert gas – Higher laser power consumption compared to EBM | – Medical and dental implants – Automotive parts (lightweight components) – Aerospace components (structural parts) |
Directed Energy Deposition (DED) | A focused energy source (laser or electron beam) melts titanium wire or powder, depositing it onto a substrate layer-by-layer. | Titanium wire or powder | Up to 1000 x 1000 x 1000 | – Large build envelope for printing large-scale parts – Faster printing speeds compared to powder bed fusion – Can be used for repair and cladding applications | – Lower resolution and surface finish compared to LBM/EBM – Higher risk of warping and distortion – Limited support for complex geometries | – Large-scale structural components (bridges, pressure vessels) – Repair of existing parts – Functional prototypes |
Binder Jetting (BJ) | A liquid binder jethead selectively deposits a binder onto a bed of titanium powder, creating a solid green part. The part is then debound and sintered. | Titanium powder and liquid binder | Up to 700 x 500 x 500 | – Lower cost per part compared to other methods – Suitable for printing complex geometries with internal channels – Wide range of materials (not limited to titanium) | – Relatively weak parts after debinding, requiring sintering – Lower mechanical properties compared to fusion methods – Post-processing steps can be time-consuming | – Non-critical automotive components (interior parts) – Medical prototypes – Low-stress functional parts |
Standards for Titanium Powder and Printed Parts
Aspect | Standards Organizations | Key Considerations | Typical Standards |
---|---|---|---|
Powder Feedstock | ASTM International (ASTM), ISO | – Chemical composition – Particle size and distribution – Flowability – Powder morphology | – ASTM B348: Standard Specification for Titanium and Titanium-Alloy Strip, Sheet, and Plate – ASTM F3056: Standard Specification for Additive Manufacturing (AM) Titanium Powder – ISO 5832-2: Aerospace series – Metallic materials – Titanium alloy bars, strips and sheets – Part 2: Technical specifications – UNS R56400 (Ti-6Al-4V) |
Mechanical Properties | ASTM International (ASTM) | – Tensile strength – Yield strength – Elongation – Fatigue strength – Hardness | – ASTM F136: Standard Specification for Sheet and Plate for Structural Applications – ASTM F3001: Standard Specification for Additive Manufacturing (AM) Powders for Laser Beam Melting – ASTM F3302: Standard Specification for Densification of Titanium and Titanium Alloy Powders by Laser Beam Melting (LBM) |
Microstructure and Porosity | ASTM International (ASTM) | – Grain size – Porosity level and distribution – Surface roughness | – ASTM E112: Standard Test Methods for Determining the Average Grain Size of Metallic Materials – ASTM B924: Standard Test Methods for Examination and Classification of Oxide Discoloration in Titanium – ASTM F2904: Standard Practice for Microstructural Characterization of Additively Manufactured Metal Alloys |
Part Design for Additive Manufacturing (AM) | ASTM International (ASTM), Wohlers Report | – Minimum wall thickness – Design for support structures – Internal features and lattice structures – Surface roughness considerations | – ASTM F4269: Standard Practice for Additive Manufacturing with Powder Bed Fusion of Metals – Wohlers Report [Wohlers Report on Additive Manufacturing State of the Industry] – Design guidelines from machine manufacturers |
Non-Destructive Testing (NDT) | ASTM International (ASTM) | – X-ray radiography – Computed tomography (CT) – Ultrasonic testing – Eddy current testing | – ASTM E1742: Standard Practice for Radiographic Examination of Metallic Materials for Porosity and Inclusions – ASTM F2789: Standard Test Method for Computed Tomography (CT) Imaging of Additive Manufacturing (AM) Processes – ASTM E114: Standard Practice for Ultrasonic Examination of Metallic Materials – ASTM E2194: Standard Guide for Electromagnetic (Eddy Current) Testing of Metal Products |
Post-Processing | ASTM International (ASTM) | – Heat treatment – Hot Isostatic Pressing (HIP) – Machining and finishing | – ASTM F67: Standard Test Method for Determining the Shear Strength of Titanium Screws and Pins – ASTM B967: Standard Specification for Chemical Descaling, Electrocleaning, and Passivation of Titanium and Titanium Alloys – Machining and finishing guidelines from machine manufacturers |
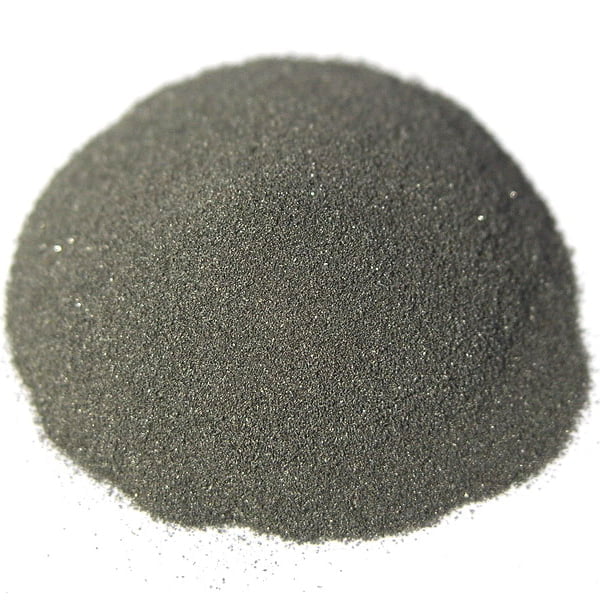
FAQ
What is the best titanium alloy for 3D printing?
Ti 6Al-4V is currently the most common titanium alloy powder used for additive manufacturing due to its excellent mechanical properties and corrosion resistance combined with commercial availability. Ti 6Al-4V ELI provides improved fracture toughness.
What methods can 3D print titanium parts?
Selective laser melting (SLM) and electron beam melting (EBM) are the major powder bed fusion technologies used for printing titanium. Directed energy deposition (DED) methods are also capable but have more porosity.
Does titanium need supports when 3D printing?
Yes, titanium requires supports during printing because it solidifies quickly. Carefully optimized supports are needed to avoid surface defects and wasting material while still providing adequate anchoring.
Is it cheaper to 3D print or machine titanium?
For one-off custom parts, 3D printing titanium is often cheaper since there is no tooling required. For mass production, CNC machining titanium can have a lower per part cost but has higher upfront setup expenses and material waste.
What industries use 3D printed titanium parts?
Aerospace is the largest adopter of titanium printing today thanks to buy-to-fly ratio improvements on complex components. Medical, automotive, oil and gas, sporting goods, and consumer sectors also leverage 3D printed titanium.
How much does titanium powder for 3D printing cost?
Titanium powder can range from $100-2000 per kilogram depending on composition, quality, order quantity, and other factors. Ti 6Al-4V and Ti 6Al-4V ELI spherical powders for critical applications command premium pricing over $500/kg.
What are some examples of 3D printed titanium parts?
3D printing enables innovative titanium parts like airframe brackets, turbines, motorsports components, customized prosthetics, conformally-cooled injection molds, and even eyewear or jewelry leveraging complex lattice designs.
Share On
MET3DP Technology Co., LTD is a leading provider of additive manufacturing solutions headquartered in Qingdao, China. Our company specializes in 3D printing equipment and high-performance metal powders for industrial applications.
Inquiry to get best price and customized Solution for your business!
Related Articles
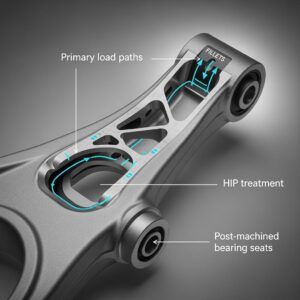
Metal 3D Printing for U.S. Automotive Lightweight Structural Brackets and Suspension Components
Read More »About Met3DP
Recent Update
Our Product
CONTACT US
Any questions? Send us message now! We’ll serve your request with a whole team after receiving your message.