5083 Metal Powder for SLS
Table of Contents
Additive manufacturing, also known as 3D printing, has revolutionized how we design and produce complex parts. Selective laser sintering (SLS) is a powerful 3D printing technique that uses a laser beam to selectively melt and fuse together metal powder particles, layer by layer, to build a three-dimensional object. The choice of metal powder plays a crucial role in the success of SLS projects. Here, we delve into the world of 5083 metal powder, a popular choice for SLS applications due to its unique properties and versatility.
Overview of 5083 Metal Powder
5083 aluminum alloy powder is a workhorse material in the world of SLS. Imagine a bag of silver-grey dust, each tiny particle brimming with potential. This aluminum-magnesium alloy boasts excellent strength-to-weight ratio, good corrosion resistance, and outstanding weldability – all qualities that translate beautifully into robust, lightweight 3D printed parts.
But what exactly makes 5083 powder tick? Let’s take a closer look at its composition and key characteristics.
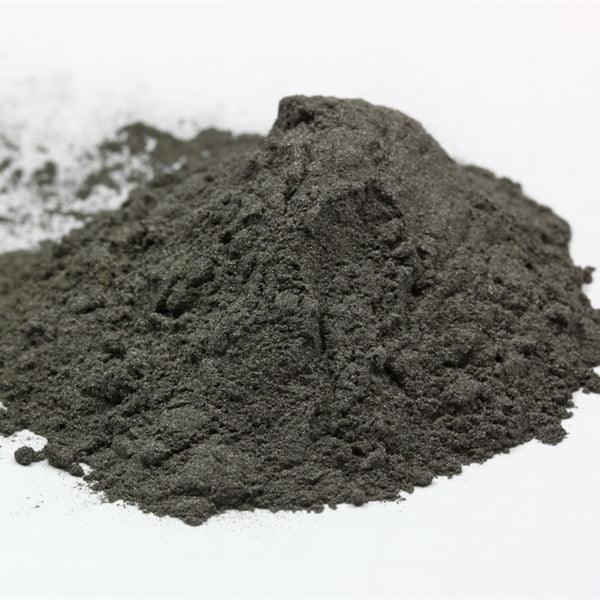
Composition and Key Characteristics of 5083 Metal Powder for SLS
Property | Description |
---|---|
Material | Aluminum-Magnesium Alloy (Al-Mg) |
Alloy Designation | 5083 |
Primary Alloying Element | Magnesium (Mg) |
Typical Composition (wt%) | 95.5-96.5 Al, 4.0-4.9 Mg, 0.05-0.1 Fe, 0.1 Max Si, 0.25 Max Mn, 0.05 Max Cu |
Density (g/cm³) | ~2.67 |
Melting Point (°C) | ~565 |
Strength (MPa) | Up to 325 (yield), Up to 345 (tensile) |
Elongation (%) | Up to 35 |
Corrosion Resistance | Good |
Weldability | Excellent |
Surface Finish | Spherical particles with smooth surfaces |
Particle Size Distribution | Typically controlled for optimal packing and laser interaction |
Breaking it Down: The magic of 5083 lies in its carefully balanced composition. Magnesium, the primary alloying element, contributes to increased strength and improved weldability compared to pure aluminum. The low levels of other elements like iron, silicon, and manganese help maintain good corrosion resistance and workability.
Spherical Power for Seamless Printing: The smooth, spherical shape of 5083 powder particles is no accident. This design optimizes flowability within the SLS machine, ensuring consistent powder distribution and facilitating a smooth printing process. Additionally, the controlled particle size distribution allows for optimal packing density, minimizing porosity – those tiny air pockets – within the finished part.
Applications of 5083 Metal Powder
With its impressive strength and printability, 5083 metal powder finds application across diverse industries:
- Aerospace & Defense: Lightweight, high-strength components for aircraft, drones, and satellites.
- Automotive: Prototypes, functional parts like brackets and housings, and even lightweight engine components.
- Medical & Dental: Custom prosthetics, implants, and surgical instruments.
- Consumer Goods: Durable and intricate sports equipment, bicycle frames, and custom jewelry pieces.
The ability to create complex geometries with 5083 powder allows for the design of parts with internal channels, lattices, and other features that are difficult or impossible to achieve with traditional manufacturing techniques. Imagine creating a custom bike frame with weight-optimized tubing or a medical implant perfectly tailored to a patient’s anatomy – that’s the power of 5083 in action.
Specifications, Sizes, Grades & Standards
When selecting 5083 powder for your SLS project, several factors come into play:
Factor | Description |
---|---|
Particle Size | Typically ranges from 15 to 90 microns, with specific choices affecting surface finish and mechanical properties. Finer particles create smoother surfaces but may be more challenging to work with. |
Powder Grade | Can vary depending on the manufacturer, with options for different levels of purity and oxygen content. Higher purity powders may offer improved mechanical properties. |
Standards | Look for powders that comply with industry standards like ASTM International (ASTM) or Aerospace Material Specifications (AMS) to ensure consistent quality and performance. |
Picking the Perfect Powder: The choice of particle size and grade depends on your specific application. For parts requiring a high-quality surface finish, finer particles might be ideal. However, if dimensional accuracy and strength are paramount, a slightly coarser particle size might be preferable. Consulting with your SLS service provider or the powder manufacturer can help you navigate these choices and select the optimal 5083 powder for your project.
Suppliers and Pricing of 5083 Metal Powder
Several reputable suppliers offer 5083 metal powder for SLS applications. Prices can vary depending on factors like:
- Quantity: Larger quantities typically come at a lower price per unit weight.
- Particle size and grade: Finer particles and higher purity grades may command a premium.
- Manufacturer: Brand reputation and established quality control processes can influence pricing.
Here’s a table outlining some potential suppliers (Disclaimer: This is not an exhaustive list, and inclusion does not constitute endorsement):
Supplier | Website | Additional Notes |
---|---|---|
AM Powder | http://ampowder.ch/ | Offers a variety of 5083 powder options with different particle sizes and purities. |
Höganäs | https://www.hoganas.com/en/ | Renowned manufacturer with a reputation for high-quality metal powders, including 5083 for SLS. |
LPW | https://www.carpenteradditive.com/news-events/lpw-technology-am-metal-powder-manufacturing | Leading provider of metal powders for additive manufacturing, including 5083 for SLS. |
Materialise | https://www.materialise.com/en | Offers a range of metal powders, including 5083, with a focus on supporting the entire SLS printing process. |
Beyond the Price Tag: While cost is a consideration, prioritizing quality is crucial. Look for suppliers with a proven track record and a commitment to rigorous quality control procedures. This ensures consistent powder characteristics and minimizes the risk of printing failures.
the Pros and Cons of 5083 Metal Powder for SLS
Advantages:
- Excellent Strength-to-Weight Ratio: 5083 offers impressive strength for its weight, making it ideal for applications demanding both performance and lightweight design. Think of crafting a strong yet feather-light drone component.
- Good Corrosion Resistance: Compared to pure aluminum, 5083 holds up well against environmental factors like moisture and salt spray. This makes it suitable for parts exposed to the elements, like outdoor equipment or marine applications.
- Outstanding Weldability: The ability to join 5083 parts seamlessly through welding expands the design possibilities for SLS projects. Imagine creating a complex assembly with intricate welds, all printed in one go.
- Wide Range of Applications: The versatility of 5083 makes it a popular choice across diverse industries, from aerospace to consumer goods.
Limitations:
- Lower Strength Compared to Some Alloys: While strong for an aluminum alloy, 5083 might not be the best choice for applications requiring the absolute highest strength. For those scenarios, other metal powders like titanium alloys might be a better fit.
- Susceptible to Stress Corrosion Cracking: In specific environments with high stress and certain corrosive agents, 5083 can be susceptible to stress corrosion cracking. Consulting with a materials engineer is crucial if your application involves such conditions.
- Post-Processing Requirements: SLS parts made from 5083 might require post-processing steps like heat treatment or surface finishing to achieve optimal mechanical properties or aesthetics.
By understanding these pros and cons, you can make an informed decision about whether 5083 metal powder is the right choice for your SLS project.
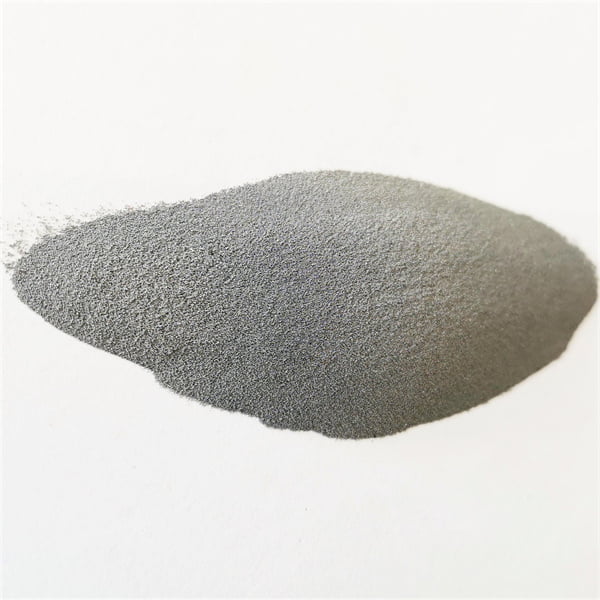
Comparing 5083 to Other Popular SLS Powders
With a plethora of metal powders available for SLS, it’s natural to wonder how 5083 stacks up against the competition. Let’s delve into a head-to-head comparison with some other commonly used SLS metal powders:
1. 5083 Aluminum vs. 17-4 PH Stainless Steel:
- Strength: 17-4 PH stainless steel boasts significantly higher strength compared to 5083.
- Corrosion Resistance: Both materials offer good corrosion resistance, with 17-4 PH excelling in harsher environments due to its higher chromium content.
- Weight: 5083 is significantly lighter than 17-4 PH, making it ideal for weight-sensitive applications.
- Applications: 17-4 PH finds use in parts requiring high strength and corrosion resistance, like medical implants or aerospace components. 5083 shines in applications where weight is a concern, such as automotive parts or lightweight consumer goods.
2. 5083 Aluminum vs. Inconel 625:
- Strength: Inconel 625 is a high-strength superalloy that outperforms 5083 by a significant margin.
- Heat Resistance: Inconel 625 boasts exceptional heat resistance, making it suitable for high-temperature applications like jet engine components. 5083 is not recommended for such extreme temperatures.
- Cost: Inconel 625 is a considerably more expensive material compared to 5083.
- Applications: Inconel 625 is the go-to choice for parts requiring exceptional strength and heat resistance in demanding environments like aerospace and power generation. 5083 remains a cost-effective option for applications with less extreme temperature requirements.
3. 5083 Aluminum vs. Titanium 6Al-4V:
- Strength: Titanium 6Al-4V offers superior strength to 5083, making it ideal for highly stressed components.
- Weight: While lighter than steel, Titanium 6Al-4V is still denser than 5083.
- Biocompatibility: Titanium 6Al-4V exhibits good biocompatibility, making it a valuable material for medical implants.
- Cost: Titanium 6Al-4V is a more expensive material compared to 5083.
- Applications: Titanium 6Al-4V finds use in demanding applications requiring high strength and weight reduction, such as aerospace components and medical implants. 5083 remains a cost-effective alternative for applications where weight is a concern but absolute top-tier strength is not essential.
FAQ
Q: Is 5083 metal powder safe to handle?
A: Like any metal powder, 5083 can pose inhalation risks if not handled properly. It’s crucial to follow safety protocols like wearing appropriate gloves, respirators, and working in a well-ventilated environment.
Q: Can I post-process 5083 SLS parts to improve their strength?
A: Yes, heat treatment can be used to enhance the mechanical properties of 5083 SLS parts. Consulting with a heat treatment specialist is recommended to determine the optimal process for your application.
Q: How does the surface finish of 5083 metal powder affect the final SLS part?
A: Finer powder particles generally result in smoother surface finishes on the final part. However, this can come at the expense of slightly lower strength and potentially more challenging printability. The choice of particle size depends on the desired balance between surface finish, mechanical properties, and printing efficiency.
Q: What are some emerging trends in 5083 metal powder for SLS?
A: Research is ongoing to develop 5083 powder with improved properties, such as higher strength or enhanced printability. Additionally, there’s growing interest in using recycled 5083 powder in SLS, promoting sustainability in the additive manufacturing process.
Share On
MET3DP Technology Co., LTD is a leading provider of additive manufacturing solutions headquartered in Qingdao, China. Our company specializes in 3D printing equipment and high-performance metal powders for industrial applications.
Inquiry to get best price and customized Solution for your business!
Related Articles
About Met3DP
Recent Update
Our Product
CONTACT US
Any questions? Send us message now! We’ll serve your request with a whole team after receiving your message.
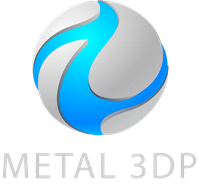
Metal Powders for 3D Printing and Additive Manufacturing