Stainless steel 3D printed metal powder
Table of Contents
The world of 3D printing has unveiled a treasure trove of possibilities, revolutionizing the way we design and manufacture objects. At the forefront of this revolution lies a game-changer: Stainless steel 3D printed metal powder. But what exactly is this innovative material, and how is it transforming various industries? Buckle up, because we’re diving deep into the fascinating world of Stainless steel 3D printed metal powder.
Classification of Stainless steel 3D printed metal powder
Stainless steel, renowned for its strength, corrosion resistance, and aesthetic appeal, takes center stage in the 3D printing arena. However, not all stainless steels are created equal for this purpose. Here’s a breakdown of the most commonly used types:
- 316L: This superstar boasts excellent corrosion resistance, making it ideal for applications exposed to harsh environments like saltwater or chemicals.
- 17-4 PH: Imagine a material that’s both strong and ductile (bendable). That’s 17-4 PH, perfect for parts requiring high strength and some flexibility.
- 304L: A cost-effective option, 304L offers good corrosion resistance for general-purpose applications where extreme environments aren’t a concern.
These are just a few examples, and the selection process hinges on the specific properties needed for the final product.
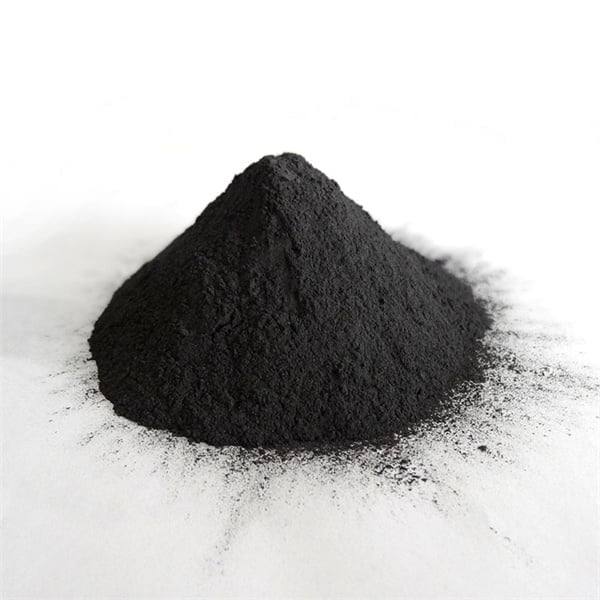
The Widespread Application of Stainless Steel 3D Printing Metal Powder
Stainless steel 3D printed metal powder isn’t a one-trick pony. Its versatility extends across numerous industries, leaving its mark in exciting ways:
- Aerospace: Think lightweight, high-strength components for rockets and satellites. 3D printing with stainless steel powder allows for intricate designs that traditional manufacturing might struggle with, leading to weight reduction and improved fuel efficiency.
- Medical: Imagine custom-made implants perfectly tailored to a patient’s anatomy. This becomes a reality with stainless steel 3D printing. The biocompatible nature of certain grades makes them ideal for surgical instruments and prosthetics.
- Automotive: From intricate engine parts to lightweight car components, stainless steel 3D printing metal powder is making waves in the automotive industry. The ability to create complex geometries with high strength-to-weight ratios pushes the boundaries of car design.
- Consumer Goods: Ever dreamt of a custom-designed bike frame or a unique piece of jewelry? Stainless steel 3D printing metal powder makes it possible. The ability to create complex shapes with a high-quality finish unlocks a new era of personalized products.
These are just a glimpse of the vast potential. As 3D printing technology matures, we can expect even more innovative applications to emerge in various fields.
Advantages of Stainless Steel 3D Printing Metal Powder
So, what makes Stainless steel 3D printed metal powder such a compelling choice? Here are some key benefits that set it apart:
- Design Freedom: Unlike traditional manufacturing methods, 3D printing unlocks a world of design possibilities. Complex geometries, intricate internal features, and lightweight structures become achievable, pushing the boundaries of what’s possible.
- Material Efficiency: Traditional manufacturing often involves significant material waste. 3D printing with metal powder minimizes this waste, as material is only deposited where needed. This translates to cost savings and a more environmentally friendly approach.
- Rapid Prototyping: Imagine going from concept to a functional prototype in a matter of days. 3D printing allows for rapid prototyping, significantly accelerating the product development cycle. This translates to faster time-to-market and a competitive edge.
- Customization: Need a one-of-a-kind component or a product tailored to specific needs? 3D printing with stainless steel powder makes it possible. This opens doors for personalized products and niche applications.
These advantages make stainless steel 3D printing metal powder a powerful tool for engineers, designers, and manufacturers across various industries.
Considering the Challenges: A Look at the Drawbacks
While Stainless steel 3D printed metal powder offers a plethora of advantages, it’s essential to acknowledge some challenges:
- Cost: Compared to traditional manufacturing techniques, 3D printing with metal powder can be more expensive, especially for large-scale production runs. However, the cost is continuously decreasing as the technology matures.
- Surface Finish: The surface finish of 3D printed metal parts might require post-processing techniques like polishing or machining to achieve a desired aesthetic or functional smoothness.
- Material Properties: The properties of 3D printed metal parts can differ slightly from conventionally manufactured parts due to the layering process. However, advancements in printing techniques are continuously narrowing this gap.
- Limited Material Selection: While there’s a growing variety of metal powders available for 3D printing compared to traditional manufacturing, the selection of materials for 3D printing is still evolving. This can limit the applicability of the technology for certain projects requiring specific properties not yet readily achievable with 3D printed metals.
Understanding these challenges empowers you to make informed decisions about whether stainless steel 3D printing metal powder is the right fit for your project.
The Printing Process
Now that we’ve explored the applications and considerations, let’s delve into the fascinating world of Stainless steel 3D printed metal powder. Here’s a simplified breakdown of the process:
- Design and Preparation: The journey begins with a 3D model of the desired object. This model is then sliced into thin layers by slicing software, essentially creating a digital blueprint for the printer.
- Powder Bed Fusion: This is where the magic happens! Several 3D printing techniques utilize powder bed fusion for stainless steel printing. In this method, a layer of fine metal powder is spread across a platform. A laser beam then selectively melts the powder particles according to the sliced digital model, fusing them together. Layer by layer, the object takes shape.
- Building and Support Removal: Once complete, the printed object is encased in unmelted powder. This support structure is then removed through various techniques like sandblasting or high-pressure water jets, revealing the final product.
- Post-Processing: Depending on the desired finish and application, the printed object might undergo additional processes like heat treatment, machining, or polishing for a smoother surface or enhanced mechanical properties.
This simplified explanation provides a glimpse into the intricate dance of technology that transforms metal powder into functional objects.
Stainless Steel 3D Printed Metal Powder vs. Other Metal Printing Options
With a growing array of metal printing options available, it’s natural to wonder how stainless steel powder stacks up against the competition. Here’s a breakdown of some key comparisons:
- Stainless Steel vs. Titanium: Both offer excellent corrosion resistance, but titanium boasts a higher strength-to-weight ratio, making it ideal for aerospace applications where weight reduction is paramount. However, stainless steel comes at a lower cost, making it a more budget-friendly option for many projects.
- Stainless Steel vs. Aluminum: Aluminum shines with its lightweight properties, making it perfect for applications where weight is a critical factor. However, stainless steel surpasses aluminum in terms of strength and corrosion resistance, making it a better choice for demanding environments.
- Stainless Steel vs. Nickel Alloys: For applications requiring exceptional heat resistance and resistance to harsh chemicals, nickel alloys take the crown. However, their higher cost and potential health hazards during printing make them a more specialized choice.
The best option for your project depends on the specific requirements of weight, strength, corrosion resistance, cost, and post-processing needs.
The Evolving Landscape of Stainless Steel 3D Printed Metal Powder
The future of Stainless steel 3D printed metal powder is brimming with exciting possibilities. Here are some trends to watch:
- Reduced Cost: As the technology matures and production scales up, the cost of 3D printing with metal powder is expected to decrease, making it more accessible for a wider range of applications.
- Material Advancements: The development of new metal powders with enhanced properties like improved strength, ductility, and corrosion resistance is on the horizon, further expanding the capabilities of this technology.
- Multi-Material Printing: Imagine combining different metal powders within a single print to create objects with unique properties in different zones. This futuristic concept is actively being explored, opening doors for groundbreaking applications.
- Integration with AI: The integration of artificial intelligence with 3D printing could revolutionize the design and optimization of parts for 3D printing with stainless steel powder, leading to even more efficient and innovative creations.
By embracing these advancements, stainless steel 3D printing metal powder is poised to play a transformative role in shaping the future of manufacturing across various industries.
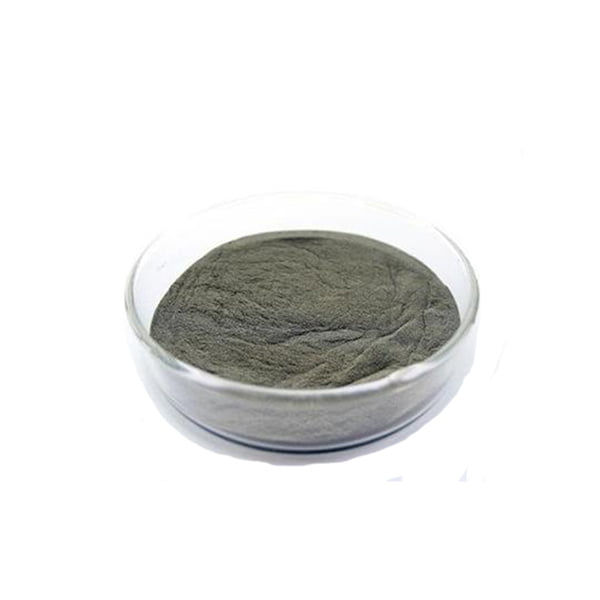
FAQ
1. What are the benefits of using stainless steel 3D printing metal powder compared to traditional manufacturing techniques?
Stainless steel 3D printing offers design freedom, allows for rapid prototyping and customization, and minimizes material waste.
2. What are some of the limitations of stainless steel 3D printing metal powder?
The cost can be higher compared to traditional methods, surface finish might require post-processing, material properties can differ slightly, and the selection of materials is still evolving.
3. What are some of the common applications of stainless steel 3D printing metal powder?
Applications span across aerospace, medical, automotive, and consumer goods industries, including aircraft components, custom implants, lightweight car parts, and even personalized jewelry.
4. What are the different types of stainless steel used in 3D printing metal powder?
Some commonly used types include 316L (excellent corrosion resistance), 17-4 PH (high strength and some flexibility), and 304L (cost-effective with good corrosion resistance). The choice depends on the specific properties needed for the final product.
5. What is the process of 3D printing with stainless steel metal powder?
The process involves design and preparation (creating a 3D model and slicing it into layers), powder bed fusion (using a laser to selectively melt powder particles layer-by-layer), building and support removal (removing the unmelted powder support structure), and post-processing (optional steps like heat treatment or polishing).
6. How does stainless steel 3D printing metal powder compare to other metal printing options like titanium or aluminum?
- Stainless Steel vs. Titanium: Stainless steel is generally more cost-effective, while titanium offers a higher strength-to-weight ratio, making it ideal for weight-critical applications.
- Stainless Steel vs. Aluminum: Aluminum is lighter but less strong and corrosion-resistant compared to stainless steel.
- Stainless Steel vs. Nickel Alloys: Nickel alloys boast superior heat and chemical resistance but come at a higher cost and potential health risks during printing.
Share On
MET3DP Technology Co., LTD is a leading provider of additive manufacturing solutions headquartered in Qingdao, China. Our company specializes in 3D printing equipment and high-performance metal powders for industrial applications.
Inquiry to get best price and customized Solution for your business!
Related Articles
About Met3DP
Recent Update
Our Product
CONTACT US
Any questions? Send us message now! We’ll serve your request with a whole team after receiving your message.
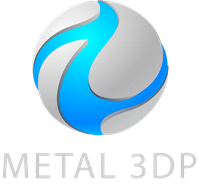
Metal Powders for 3D Printing and Additive Manufacturing
COMPANY
PRODUCT
cONTACT INFO
- Qingdao City, Shandong, China
- [email protected]
- [email protected]
- +86 19116340731