Aerospace-Grade Titanium 3D Printing in the USA: A Comprehensive Guide for B2B Buyers
Table of Contents
1. Introduction: The Role of Aerospace-Grade Titanium in 3D Printing
Why Titanium Is Crucial for Aerospace Applications
Titanium is widely used in the aerospace industry due to its high strength-to-weight ratio, corrosion resistance, and superior thermal properties. With advancements in additive manufacturing (AM), aerospace manufacturers are now leveraging titanium 3D printing to produce complex parts with reduced lead times and material waste.
Key Benefits of Aerospace-Grade Titanium in 3D Printing
- Lightweight & Strong – Essential for fuel efficiency and aircraft performance.
- Corrosion & Heat Resistant – Ensures durability in extreme aerospace environments.
- High Precision & Complexity – Additive manufacturing allows for intricate geometries.
- Material Efficiency – Less waste compared to traditional machining methods.
Common Aerospace Applications of Titanium 3D Printing
Application | Titanium 3D Printed Component |
---|---|
Jet Engines | Turbine blades, combustion chambers |
Aircraft Frames | Structural components, brackets |
Spacecraft | Satellite components, rocket nozzles |
UAVs (Drones) | Lightweight structural parts |
With the rise of laser and electron beam powder bed fusion (PBF) technologies, aerospace manufacturers can now create customized titanium components that were previously impossible to manufacture using traditional machining techniques.
2. Market Trends & Growth Potential of Titanium 3D Printing in Aerospace
The Growing Demand for Aerospace 3D Printing
The aerospace industry has been one of the largest adopters of 3D printing, with titanium leading the way. According to industry reports:
- The global aerospace 3D printing market is projected to grow to $10 billion by 2030.
- Titanium-based additive manufacturing is expected to see a CAGR of 20%+ over the next decade.
- Leading aerospace companies like Boeing, SpaceX, and Lockheed Martin are investing heavily in 3D-printed titanium parts.
Factors Driving the Growth of Titanium 3D Printing in Aerospace
- Cost Reduction – 3D printing reduces material waste and lowers production costs.
- Customization & Complexity – Enables lightweight, optimized parts.
- Faster Prototyping – Rapid production of functional aerospace components.
- Sustainability – Minimizes raw material usage and supports eco-friendly manufacturing.
Adoption of Additive Manufacturing by Aerospace OEMs
Aerospace OEM | 3D Printing Adoption |
---|---|
Boeing | Uses titanium 3D printing for structural parts |
Airbus | Implements AM for lightweight aircraft parts |
NASA | 3D prints titanium rocket engine parts |
SpaceX | Uses AM for spacecraft and propulsion systems |
The USA is one of the leading markets for aerospace 3D printing, with advanced suppliers and research institutions driving innovation in additive manufacturing technologies.
3. Key Factors to Consider When Choosing a Titanium 3D Printing Supplier
Selecting the right titanium 3D printing supplier is critical for aerospace manufacturers. Here are the key factors to evaluate:
1. Material Quality & Certification
- Ensure the supplier provides aerospace-grade titanium powders with high sphericity and purity.
- Look for certifications such as AS9100, ISO 9001, and NADCAP compliance.
2. Printing Technology & Expertise
- Does the supplier use Selective Electron Beam Melting (SEBM) or Laser Powder Bed Fusion (LPBF)?
- Evaluate their experience in manufacturing aerospace components.
3. Production Capacity & Lead Times
- Check if the supplier can meet your volume requirements.
- Assess their lead times and ability to deliver on tight project deadlines.
4. Post-Processing Capabilities
- Verify if they provide heat treatment, machining, and surface finishing for aerospace parts.
- Post-processing is crucial for enhancing the mechanical properties of titanium components.
5. Cost-Effectiveness & Scalability
- Compare pricing models and ensure a cost-effective solution for large-scale production.
- Ask about bulk discounts for repeat orders.
6. Industry Experience & Client Portfolio
- Look for suppliers who work with leading aerospace companies.
- Check case studies and testimonials to gauge their reliability.
Comparison of Key Selection Factors
Factor | Importance |
---|---|
Material Quality | ⭐⭐⭐⭐⭐ |
Printing Technology | ⭐⭐⭐⭐⭐ |
Certifications | ⭐⭐⭐⭐⭐ |
Post-Processing | ⭐⭐⭐⭐ |
Lead Times | ⭐⭐⭐⭐ |
Cost & Scalability | ⭐⭐⭐⭐ |
A trusted titanium 3D printing supplier should offer high-quality materials, cutting-edge technologies, and industry certifications to ensure compliance with aerospace manufacturing standards.
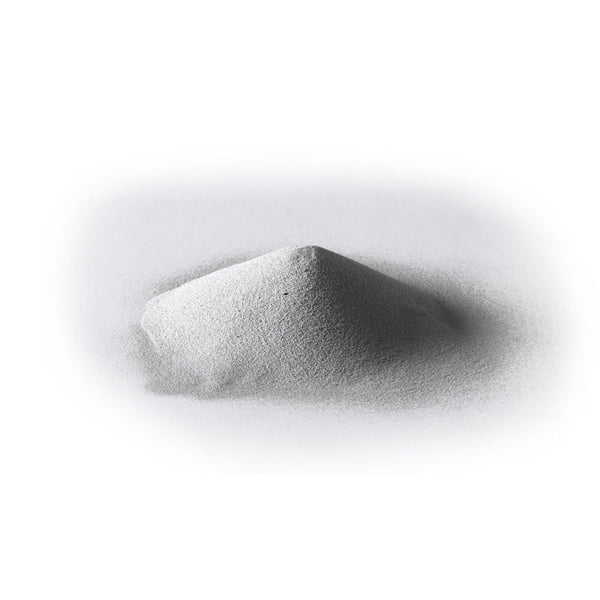
4. Top Aerospace-Grade Titanium 3D Printing Suppliers in the USA
The USA is home to some of the world’s leading aerospace additive manufacturing (AM) providers. These companies specialize in aerospace-grade titanium 3D printing, offering a range of solutions for aircraft, spacecraft, and defense applications.
Leading Titanium 3D Printing Suppliers in the USA
Supplier | Specialization | Key Aerospace Clients | Certifications |
---|---|---|---|
Metal3DP | Metal powders & SEBM 3D printing | Aerospace, defense, medical | AS9100, ISO 9001 |
3D Systems | Direct Metal Printing (DMP) | Boeing, Lockheed Martin | AS9100, NADCAP |
Stratasys Direct | Laser Powder Bed Fusion (LPBF) | SpaceX, NASA | ISO 9001 |
EOS North America | Industrial additive manufacturing | Aerospace & automotive | AS9100D |
Sintavia | Aerospace & defense metal 3D printing | Rolls-Royce, GE Aviation | NADCAP, AS9100 |
Carpenter Additive | Titanium powder supply & AM parts | Aerospace & defense | ITAR, AS9100 |
Why Choose a Specialized Aerospace 3D Printing Supplier?
- Expertise in Titanium Additive Manufacturing – Ensures superior quality and compliance with aerospace standards.
- Industry Certifications – Guarantees adherence to safety and performance requirements.
- Advanced 3D Printing Technologies – Providers should offer SEBM, LPBF, and DED processes for titanium.
- Proven Track Record – Look for suppliers with major aerospace OEMs as clients.
5. Why More Aerospace Manufacturers Are Adopting 3D Printing for Titanium Parts
Key Reasons for Adoption in Aerospace
- Weight Reduction for Fuel Efficiency
- Titanium 3D printing enables lightweight structures, reducing aircraft and spacecraft fuel consumption.
- Complex Geometry & Design Freedom
- Traditional machining cannot produce intricate, optimized aerospace parts like 3D printing can.
- Lower Material Waste & Cost Savings
- Additive manufacturing uses only the required material, reducing titanium waste.
- Rapid Prototyping & Faster Production Cycles
- Speeds up component development & testing for aerospace applications.
- On-Demand Manufacturing & Supply Chain Efficiency
- Reduces dependency on long lead-time titanium forging and casting processes.
Case Study: How 3D Printing Transforms Aerospace Manufacturing
Boeing’s Use of Titanium 3D Printing
- Boeing implemented additive manufacturing for titanium structural components in the 787 Dreamliner.
- The company reduced production costs by 30%, thanks to 3D printing.
NASA’s 3D-Printed Rocket Engine Parts
- NASA has successfully 3D-printed rocket nozzles, turbopumps, and combustion chambers using titanium alloys.
- This approach enhanced performance while reducing weight for space missions.
Titanium 3D Printing in Space Exploration
Application | 3D-Printed Titanium Component |
---|---|
Satellites | Lightweight mounting structures |
Rocket Engines | Turbopumps, nozzles |
Lunar & Mars Landers | Structural components |
Space Telescopes | Precision brackets & optics mounts |
The aerospace industry is shifting towards digital manufacturing, and titanium 3D printing is leading this transformation.
6. Why Choose Metal3DP for Aerospace-Grade Titanium 3D Printing?
About Metal3DP: A Leading Aerospace 3D Printing Partner
Metal3DP is a pioneer in metal 3D printing solutions, specializing in high-performance titanium powders and additive manufacturing systems.
Key Advantages of Choosing Metal3DP
1. High-Quality Titanium Powders for Aerospace Applications
- Advanced gas atomization & PREP technologies ensure spherical titanium powders with excellent flowability.
- Compliant with AS9100 & ISO 9001 aerospace standards.
2. Industry-Leading SEBM Printing Technology
- Selective Electron Beam Melting (SEBM) allows for high-density titanium aerospace parts with excellent mechanical properties.
- Ensures superior fatigue resistance and lightweight optimization.
3. Aerospace-Optimized Metal 3D Printers
- High-precision large-scale printing capabilities.
- Ideal for jet engine components, satellite structures, and defense applications.
4. Customization & Rapid Prototyping
- Tailored titanium AM solutions for aerospace OEMs & suppliers.
- Faster production cycles for aircraft and spacecraft development.
5. Cost-Effective & Scalable Production
- Bulk pricing available for large-scale titanium 3D printing.
- Reduces material waste & machining costs for aerospace manufacturers.
Comparison: Metal3DP vs. Other Titanium 3D Printing Suppliers
Feature | Metal3DP | Other Suppliers |
---|---|---|
Titanium Powder Quality | High sphericity & purity | Varies |
Printing Technology | SEBM & LPBF | Mostly LPBF |
Aerospace Certifications | AS9100, ISO 9001 | Some have AS9100 |
Customization & R&D Support | Yes | Limited |
Bulk Production Pricing | Competitive | Higher costs |
Trusted by Aerospace & Defense Manufacturers
Metal3DP partners with leading aerospace, space exploration, and defense organizations to deliver high-performance metal AM solutions.
📌 Interested in aerospace-grade titanium 3D printing? Contact Metal3DP today!
7. How to Order Aerospace-Grade Titanium 3D Printed Parts in the USA
If you are an aerospace manufacturer, defense contractor, or space technology company looking to source high-quality titanium 3D printed parts, it’s essential to follow a structured procurement process. Below is a step-by-step guide to ordering aerospace-grade titanium components from a reliable supplier like Metal3DP.
Step 1: Define Your Project Requirements
Before reaching out to a supplier, clearly outline your project needs, including:
- Component specifications – Size, weight, and design constraints.
- Material selection – Choose the right titanium alloy (e.g., Ti6Al4V, TiAl, TiNbZr).
- Application type – Aerospace, spacecraft, defense, or UAVs.
- Performance requirements – Corrosion resistance, heat tolerance, and mechanical strength.
- Production volume – Prototype, low-volume batch, or large-scale production.
Step 2: Select a Reliable Titanium 3D Printing Supplier
When choosing a supplier, consider the following factors:
- Experience in aerospace additive manufacturing
- Certifications (AS9100, ISO 9001, NADCAP)
- Printing technologies available (SEBM, LPBF, DED)
- Post-processing capabilities (heat treatment, machining, finishing)
- Lead time and scalability for production
🔹 Metal3DP is a trusted supplier with industry-leading titanium powders and advanced 3D printing solutions for aerospace applications. Learn more about our metal 3D printing capabilities here.
Step 3: Submit a Quote Request
Most suppliers, including Metal3DP, offer an online RFQ (Request for Quote) process.
- Provide 3D CAD files (STEP, STL) of your component.
- Specify material preferences and required tolerances.
- Include expected quantity and delivery timeline.
- Request pricing breakdowns for bulk orders.
Step 4: Review Supplier Proposal & Finalize Order
Once you receive a proposal, evaluate:
- Cost-effectiveness – Ensure competitive pricing for titanium 3D printing.
- Lead times – Confirm if the supplier can meet your deadlines.
- Post-processing options – Verify finishing services (polishing, heat treatment).
- Shipping & logistics – Ensure secure, ITAR-compliant delivery for aerospace parts.
Step 5: Prototype & Approval
- Conduct initial prototyping to validate design and performance.
- Perform mechanical and aerospace qualification testing.
- Approve final design modifications before full-scale production.
Step 6: Bulk Production & Delivery
Once the prototype is approved:
- The supplier manufactures the full order based on the agreed timeline.
- Components undergo strict quality inspection to meet aerospace regulations.
- Final products are packaged and shipped securely to your facility.
📌 Need a quote for aerospace titanium 3D printing? Contact Metal3DP today!
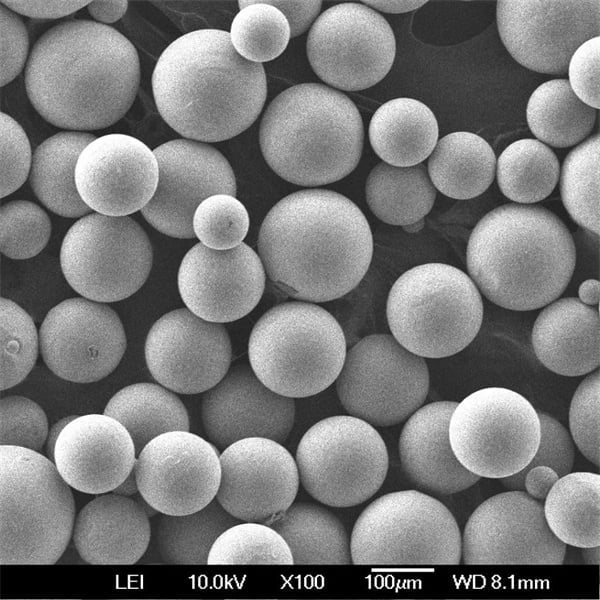
8. Frequently Asked Questions (FAQs) About Titanium 3D Printing
1. What are the best titanium alloys for aerospace 3D printing?
The most commonly used titanium alloys in aerospace additive manufacturing include:
- Ti6Al4V (Grade 5) – High strength, corrosion-resistant, widely used in aircraft.
- TiAl (Titanium Aluminide) – Ideal for jet engine turbine blades.
- TiNbZr – Advanced titanium alloy for spacecraft applications.
2. What are the advantages of Selective Electron Beam Melting (SEBM) for aerospace?
SEBM technology, used by Metal3DP, offers:
✅ High-density titanium parts with excellent fatigue resistance.
✅ Minimal residual stress, reducing post-processing needs.
✅ Ability to produce large aerospace components with precision.
3. How does titanium 3D printing compare to traditional machining?
Feature | Titanium 3D Printing | Traditional Machining |
---|---|---|
Material Waste | Minimal (powder reusability) | High (subtractive process) |
Complexity of Designs | Can produce intricate, lightweight structures | Limited by machining constraints |
Lead Time | Faster production cycles | Longer, multi-step process |
Cost Efficiency | More cost-effective for complex parts | Expensive for high-complexity parts |
4. Can 3D printed titanium parts be certified for aerospace use?
Yes, certified suppliers like Metal3DP ensure all titanium AM parts meet AS9100 and NADCAP standards for aerospace applications.
5. How long does it take to manufacture titanium 3D printed aerospace parts?
Production timelines vary based on part complexity, size, and post-processing needs. On average:
- Prototyping: 2-4 weeks
- Low-volume production: 4-6 weeks
- Full-scale production: 6-12 weeks
6. How much does titanium 3D printing cost for aerospace components?
Cost depends on:
- Material type (Ti6Al4V, TiAl, etc.)
- Part size & complexity
- Required precision & finishing
- Production volume
For bulk orders, Metal3DP offers competitive pricing. Request a quote here.
9. Conclusion & Next Steps
Why Aerospace Manufacturers Should Adopt Titanium 3D Printing
💡 Key Takeaways:
✅ Titanium 3D printing enables lightweight, high-strength aerospace components.
✅ SEBM & LPBF technologies offer superior mechanical properties for aircraft and spacecraft.
✅ Metal3DP provides certified titanium powders & advanced 3D printing solutions.
✅ Faster lead times, lower material waste, and cost savings make additive manufacturing the future of aerospace production.
Next Steps for Aerospace B2B Buyers
🔹 Step 1: Define your titanium component requirements.
🔹 Step 2: Select a trusted aerospace 3D printing supplier.
🔹 Step 3: Request a custom quote from Metal3DP.
🔹 Step 4: Begin prototyping & production for your aerospace project.
📌 Start Your Aerospace Titanium 3D Printing Project Today!
Contact Metal3DP for a customized solution. 🚀
Share On
MET3DP Technology Co., LTD is a leading provider of additive manufacturing solutions headquartered in Qingdao, China. Our company specializes in 3D printing equipment and high-performance metal powders for industrial applications.
Inquiry to get best price and customized Solution for your business!
Related Articles
About Met3DP
Recent Update
Our Product
CONTACT US
Any questions? Send us message now! We’ll serve your request with a whole team after receiving your message.
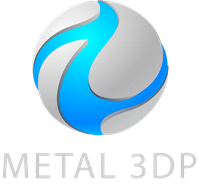
Metal Powders for 3D Printing and Additive Manufacturing