Custom Car Parts Additive Manufacturing in Stuttgart: A Comprehensive Guide
Table of Contents
1. Introduction: The Rise of Additive Manufacturing in the Automotive Industry
The automotive industry has undergone a significant transformation in recent years, with additive manufacturing (AM) playing a crucial role in reshaping production processes. Custom car parts manufacturing using 3D printing technology has become increasingly popular among automotive engineers, OEMs, and aftermarket suppliers due to its flexibility, cost-effectiveness, and ability to produce complex geometries.
Key Benefits of Additive Manufacturing in Automotive
- Rapid Prototyping – Allows for quick design iterations and product testing.
- Lightweight Components – Reduces vehicle weight, improving fuel efficiency.
- Customization – Perfect for one-off parts and low-volume production.
- Material Efficiency – Minimizes waste compared to traditional subtractive methods.
- Enhanced Performance – Enables the production of high-performance parts with superior mechanical properties.
With Stuttgart being a global hub for automotive engineering and home to manufacturers such as Mercedes-Benz and Porsche, the demand for custom 3D-printed car parts continues to grow.
2. Market Trends & Growth Potential for Custom Car Parts in Stuttgart
Current Market Trends in Automotive Additive Manufacturing
The adoption of metal 3D printing and polymer additive manufacturing is expanding, particularly in high-performance automotive applications such as motorsports, electric vehicles (EVs), and luxury cars.
Trend | Impact on Automotive Industry |
---|---|
Metal 3D Printing | Enables high-strength, durable car parts for engines, exhausts, and structural components. |
On-Demand Manufacturing | Reduces inventory costs and speeds up replacement part production. |
Sustainable Manufacturing | Lowers material waste and energy consumption. |
Localized Production | Reduces supply chain risks and shipping costs. |
Growth Potential in Stuttgart’s Automotive Sector
- Stuttgart is home to leading automotive manufacturers and suppliers, making it a prime location for 3D-printed custom car parts production.
- The European automotive additive manufacturing market is projected to grow at a CAGR of 20% by 2030.
- Automotive companies are investing in in-house additive manufacturing capabilities to streamline production.
3. Key Factors to Consider When Choosing an Additive Manufacturing Supplier
When selecting an additive manufacturing supplier for custom car parts in Stuttgart, it’s essential to evaluate several factors to ensure high-quality production and reliability.
Checklist for Choosing a Reliable 3D Printing Supplier
Factor | Why It’s Important |
---|---|
Material Expertise | The supplier should offer high-performance metal powders and polymers. |
Printing Technology | Ensure they use Selective Electron Beam Melting (SEBM) or Laser Powder Bed Fusion (LPBF) for optimal results. |
Industry Certifications | Look for ISO 9001 and IATF 16949 certifications for automotive applications. |
Lead Time & Scalability | Fast turnaround and the ability to handle bulk production orders. |
Engineering Support | Design consultation, simulation, and post-processing capabilities. |
Why Metal3DP Stands Out
Metal3DP is a leading additive manufacturing provider, specializing in high-quality metal powders and advanced 3D printing solutions for the automotive industry. With expertise in titanium, stainless steel, and superalloys, Metal3DP ensures exceptional part performance for custom car components.
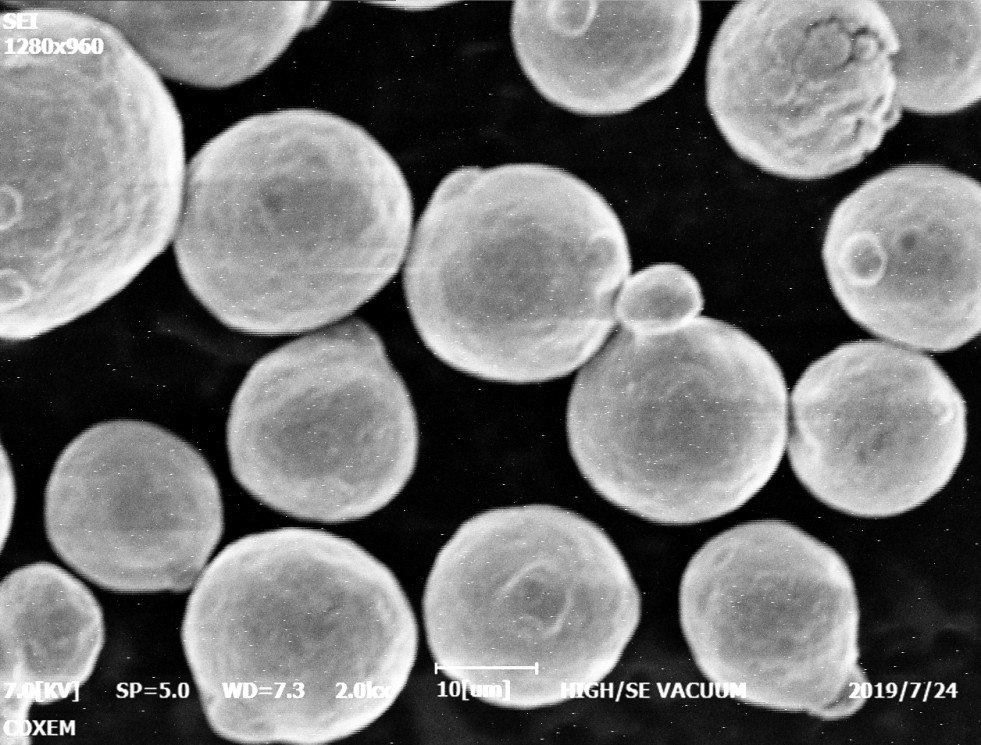
4. Top 5 Additive Manufacturing Companies for Car Parts in Stuttgart
Stuttgart is home to some of the most advanced additive manufacturing companies specializing in custom car parts. These companies offer services ranging from metal 3D printing for automotive components to rapid prototyping and production-grade parts for OEMs and aftermarket suppliers.
Top 5 Additive Manufacturing Companies in Stuttgart
Company | Specialization | Key Strengths |
---|---|---|
EOS GmbH | Industrial 3D printing solutions | High-precision metal & polymer parts, broad material selection |
Trumpf | Laser-based metal AM | Advanced laser powder bed fusion (LPBF) technology, suitable for automotive applications |
DMG Mori | Hybrid AM & CNC machining | Integrated hybrid manufacturing for high-performance automotive components |
Materialise | Custom 3D printing services | Strong expertise in automotive prototyping and lightweight structures |
Metal3DP | High-performance metal powders & SEBM printing | Industry-leading titanium and superalloy 3D printing for custom automotive parts |
Why Stuttgart Is an Ideal Hub for Additive Manufacturing
- Home to major automotive giants: Mercedes-Benz, Porsche, and Bosch.
- Strong research & development ecosystem: Collaboration with Fraunhofer Institute and local universities.
- Government support for Industry 4.0 & digital manufacturing.
- Growing demand for lightweight & custom-built components in EVs and motorsports.
Metal3DP stands out among these suppliers due to its expertise in high-performance metal powders and advanced SEBM printing technology, making it the perfect choice for automotive manufacturers looking for custom, durable, and lightweight 3D-printed parts.
5. Why More Automotive Companies Are Choosing Metal 3D Printing for Custom Parts
Key Advantages of Metal 3D Printing in Automotive Manufacturing
Benefit | Why It Matters for Automotive Parts |
---|---|
Lightweight Design | Reduces vehicle weight, improving fuel efficiency and performance. |
Complex Geometries | Enables intricate designs that traditional machining cannot achieve. |
Material Strength | High-performance metals like titanium and superalloys improve durability. |
Faster Production | Shortens lead times compared to traditional casting or milling. |
Cost Efficiency | Eliminates tooling costs and reduces material waste. |
Applications of Metal 3D Printing in Custom Car Parts
- Engine Components – Lightweight titanium exhaust manifolds, turbochargers, and heat exchangers.
- Brake Systems – High-strength ceramic-coated metal brake calipers.
- Suspension Parts – Custom shock absorbers and wishbones for performance tuning.
- Interior & Aesthetic Parts – Unique dashboard components, gear shifters, and trim panels.
- Electric Vehicle (EV) Parts – Optimized battery cooling systems and lightweight chassis elements.
Metal 3D Printing vs. Traditional Manufacturing
Factor | Metal 3D Printing | Traditional Manufacturing |
---|---|---|
Production Time | Rapid prototyping & shorter lead times | Longer setup & machining times |
Design Flexibility | Freedom to create complex geometries | Limited by tooling & machining constraints |
Material Waste | Minimal waste, efficient material usage | High waste due to subtractive processes |
Customization | Perfect for one-off & small batch production | Expensive for low-volume runs |
With the shift towards EVs, motorsports, and sustainable mobility, leading automotive manufacturers are increasingly turning to high-performance metal additive manufacturing for custom car parts.
6. Why Choose Metal3DP for Custom Car Parts Manufacturing
When it comes to additive manufacturing for automotive components, Metal3DP is a trusted partner for manufacturers looking for high-quality, performance-driven metal parts.
What Sets Metal3DP Apart?
Feature | Metal3DP Advantage |
---|---|
Advanced Powder Manufacturing | Industry-leading gas atomization & PREP technology for high-quality metal powders. |
SEBM Printing Technology | Enables dense, high-strength, defect-free metal parts with superior mechanical properties. |
Material Expertise | Specialized in titanium, stainless steel, superalloys, and CoCrMo for automotive applications. |
Custom Automotive Solutions | Tailored 3D-printed parts for motorsports, EVs, and performance vehicles. |
Reliable Supply Chain | Fast, scalable custom part production with high repeatability. |
Case Study: Custom Titanium Exhaust Manifold with SEBM Printing
A leading high-performance car manufacturer in Stuttgart partnered with Metal3DP to develop a lightweight titanium exhaust manifold using Selective Electron Beam Melting (SEBM).
Results Achieved:
✅ 50% weight reduction compared to traditional stainless steel manifolds.
✅ Increased thermal resistance & durability for high-performance engines.
✅ Complex internal cooling channels that were impossible to manufacture using traditional methods.
✅ Reduced production time from 8 weeks to 2 weeks.
For automotive manufacturers looking for cutting-edge custom car parts, Metal3DP provides unparalleled expertise in metal 3D printing to enhance vehicle performance and efficiency.
7. How to Order Custom Car Parts Using Additive Manufacturing in Stuttgart
Ordering custom car parts using additive manufacturing (AM) can be a seamless process when working with an experienced supplier like Metal3DP. Below is a step-by-step guide to help automotive manufacturers, performance tuners, and OEMs procure high-quality 3D-printed metal parts efficiently.
Step-by-Step Ordering Process
Step | Description |
---|---|
Step 1: Define Requirements | Identify the specific car part you need, including material, dimensions, and performance attributes. |
Step 2: Choose the Right Metal & Printing Method | Select from titanium, stainless steel, superalloys, or CoCrMo based on required strength and thermal properties. |
Step 3: Submit a Design File | Provide a CAD file (STL or STEP format) for evaluation. If needed, Metal3DP can assist with design optimization. |
Step 4: Prototype & Testing | Metal3DP offers rapid prototyping to ensure the part meets structural and functional specifications. |
Step 5: Full Production | Once verified, the part is printed using SEBM or LPBF and undergoes post-processing (heat treatment, surface finishing, etc.). |
Step 6: Quality Inspection & Delivery | Each part undergoes rigorous quality control before being shipped to the customer. |
Why Work with Metal3DP for Ordering Custom Car Parts?
✅ Expertise in Automotive Additive Manufacturing – Decades of experience in high-performance auto parts production.
✅ Advanced SEBM & LPBF Printing – Ensuring precise, defect-free, and high-strength automotive components.
✅ Fast Turnaround – From design review to final product delivery, Metal3DP ensures a quick and efficient process.
✅ Custom Engineering Support – Optimize your designs for better performance and cost-effectiveness.
Learn more about Metal3DP’s metal 3D printing capabilities here.
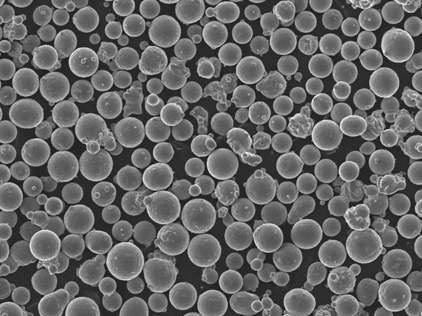
8. FAQs: Common Questions About Custom Car Parts Additive Manufacturing
1. What types of automotive parts can be 3D-printed using metal additive manufacturing?
Metal additive manufacturing is ideal for:
✅ Engine components – Turbochargers, exhaust manifolds, pistons, cylinder heads.
✅ Chassis & suspension – Custom wishbones, dampers, lightweight brackets.
✅ Brake systems – High-performance calipers, cooling ducts.
✅ Interior & exterior parts – Gear levers, dashboard components, decorative trim.
2. What materials are commonly used for 3D-printed car parts?
Metal3DP specializes in:
- Titanium alloys (Ti-6Al-4V) – Lightweight, high-strength, corrosion-resistant.
- Stainless steel (316L, 17-4 PH) – Durable, heat-resistant, ideal for automotive structures.
- Nickel-based superalloys (Inconel 718, 625) – High-temperature resistance for engine applications.
- Cobalt-chrome (CoCrMo) – Ideal for wear-resistant components.
Explore Metal3DP’s high-quality metal powders here.
3. How does metal 3D printing compare to traditional manufacturing methods?
Factor | Metal 3D Printing | Traditional Manufacturing |
---|---|---|
Lead Time | Shorter – Rapid prototyping & production | Longer due to tooling & machining |
Material Waste | Minimal – Efficient powder usage | High – Requires extensive machining |
Customization | Easy – No tooling required | Expensive – High setup costs for custom parts |
Complexity | Unlimited design freedom | Limited by machining constraints |
4. Can I order small batch or one-off custom automotive parts?
Yes! Metal3DP specializes in low-volume production and one-off custom parts, making it ideal for motorsports teams, restorers, and performance tuners who need bespoke components without high tooling costs.
5. How durable are 3D-printed metal car parts?
Metal3DP’s Selective Electron Beam Melting (SEBM) and Laser Powder Bed Fusion (LPBF) technologies ensure high-density, defect-free metal parts that meet or exceed the durability of traditionally machined components.
9. Conclusion & Next Steps
The Future of Custom Automotive Manufacturing with 3D Printing
The automotive industry in Stuttgart is rapidly embracing additive manufacturing to drive innovation, improve efficiency, and enhance performance. With metal 3D printing, manufacturers can achieve:
✅ Lighter, stronger, and more customized parts
✅ Faster prototyping and production
✅ On-demand manufacturing with less material waste
Why Choose Metal3DP for Custom Car Parts Additive Manufacturing?
🚀 Industry-leading SEBM & LPBF technology for high-performance automotive components
🚀 Expertise in high-quality metal powders optimized for automotive applications
🚀 Fast, reliable, and scalable production solutions for OEMs, aftermarket suppliers, and tuning specialists
Next Steps: Get Started with Metal3DP Today!
If you’re looking to order custom 3D-printed car parts, reach out to Metal3DP for expert consultation, design optimization, and cutting-edge metal additive manufacturing solutions.
🔗 Learn more about our advanced 3D printing methods here.
📩 Contact Metal3DP today to discuss your project needs!
By leveraging Metal3DP’s expertise in high-performance metal 3D printing, automotive manufacturers in Stuttgart can create next-generation custom car parts with unmatched precision, durability, and efficiency.
Share On
MET3DP Technology Co., LTD is a leading provider of additive manufacturing solutions headquartered in Qingdao, China. Our company specializes in 3D printing equipment and high-performance metal powders for industrial applications.
Inquiry to get best price and customized Solution for your business!
Related Articles
About Met3DP
Recent Update
Our Product
CONTACT US
Any questions? Send us message now! We’ll serve your request with a whole team after receiving your message.
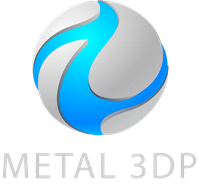
Metal Powders for 3D Printing and Additive Manufacturing