Precision Antenna Supports for Spacecraft: Revolutionizing Aerospace Manufacturing with Metal 3D Printing
Table of Contents
Introduction
In the demanding realm of space exploration, every component must exhibit unparalleled reliability, minimal weight, and exceptional performance. Spacecraft antenna supports, critical elements for communication and navigation, are no exception. Traditionally manufactured through subtractive methods, these supports often face limitations in design complexity, material efficiency, and lead times. However, the advent of metal 3D printing, also known as metal additive manufacturing, is transforming the landscape, offering innovative solutions for producing high-performance antenna supports with intricate geometries and optimized material usage. This blog post delves into the transformative potential of metal 3D printing for spacecraft antenna supports, exploring their applications, the advantages of this advanced manufacturing technique, and the crucial considerations for engineers and procurement managers in the aerospace industry. At Metal3DP, we are at the forefront of this revolution, providing industry-leading metal 3D printing solutions and high-performance metal powders to meet the stringent demands of space applications.
What are Spacecraft Antenna Supports Used For?
Spacecraft antenna supports serve as the structural foundation for mounting and orienting antennas on various types of spacecraft, including satellites, probes, and landers. Their primary function is to securely hold the antenna in the precise position required for optimal signal transmission and reception. These supports must withstand the harsh conditions of space, including extreme temperature variations, vibrations during launch, and exposure to radiation.
The specific applications of spacecraft antenna supports are diverse and crucial for mission success:
- Communication: Supporting antennas used for transmitting telemetry data, receiving commands from ground control, and relaying scientific data back to Earth.
- Navigation: Providing stable mounting for antennas integral to navigation systems, ensuring accurate positioning and trajectory control.
- Scientific Instruments: Holding antennas that are part of scientific payloads, such as radar systems for Earth observation or instruments for studying celestial bodies.
- Inter-Satellite Links: Supporting antennas that facilitate communication between different satellites in orbit, forming complex communication networks.
The design and material selection for these supports are paramount. They must be lightweight to minimize launch costs and maintain the spacecraft’s overall mass budget. Rigidity and dimensional stability are essential to ensure accurate antenna pointing and prevent signal degradation. Furthermore, the materials must exhibit excellent resistance to the space environment.
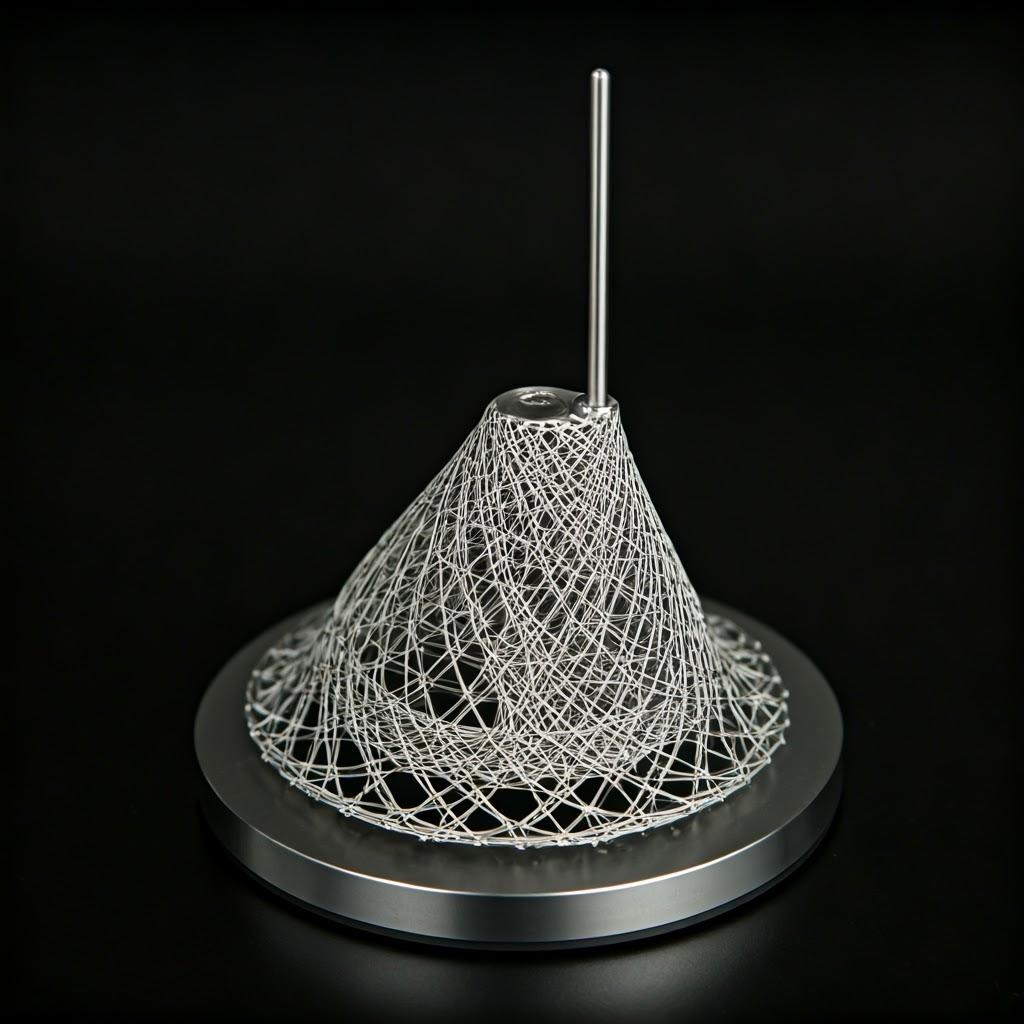
Why Use Metal 3D Printing for Spacecraft Antenna Supports?
Metal 3D printing offers a compelling alternative to traditional manufacturing methods for spacecraft antenna supports, providing a multitude of advantages that directly address the critical requirements of the aerospace industry.
- Design Freedom and Complexity: Additive manufacturing allows for the creation of intricate geometries that are often impossible or cost-prohibitive to achieve with conventional techniques like machining. This enables the optimization of support structures for weight reduction while maintaining or even enhancing stiffness and strength. Engineers can design lattice structures, thin-walled sections, and integrated features, leading to more efficient and functional components.
- Material Efficiency: Unlike subtractive methods that remove material to create the final part, 3D printing builds the component layer by layer, significantly reducing material waste. This is particularly crucial when working with expensive, high-performance alloys commonly used in aerospace applications.
- Weight Optimization: The ability to create complex internal structures and optimize designs for minimal material usage directly translates to lighter components. Reduced weight is a critical factor in the aerospace industry, as it leads to lower launch costs and improved fuel efficiency for long-duration missions.
- Faster Prototyping and Production: Metal 3D printing can significantly shorten the design-to-manufacturing cycle. Prototypes can be produced rapidly, allowing for faster design iterations and testing. For low-volume or highly customized parts, additive manufacturing can also offer quicker production times compared to traditional tooling-intensive methods.
- Customization and Part Consolidation: Each antenna support can be tailored to the specific requirements of the spacecraft and antenna design without the need for expensive tooling changes. Furthermore, 3D printing allows for the consolidation of multiple components into a single, integrated part, reducing assembly time, the number of fasteners, and potential points of failure, thereby enhancing reliability.
- Enhanced Performance: By enabling the use of advanced materials and optimized designs, metal 3D printing can contribute to enhanced performance of the antenna support in terms of stiffness, strength-to-weight ratio, and resistance to the harsh space environment.
Metal3DP recognizes these advantages and has developed advanced Selective Electron Beam Melting (SEBM) printers, such as those highlighted on our metal 3D printing page, which are ideally suited for producing complex, high-performance aerospace components like antenna supports. Our commitment to accuracy and reliability ensures that the parts meet the stringent quality standards of the space industry.
Recommended Materials and Why They Matter
The selection of the right metal powder is paramount to achieving the desired performance characteristics for spacecraft antenna supports. Metal3DP offers a comprehensive portfolio of high-quality metal powders, including the recommended materials for this application: Scalmalloy® and Ti-6Al-4V.
- Scalmalloy®: This high-strength aluminum-magnesium-scandium alloy is specifically designed for additive manufacturing and offers an exceptional strength-to-weight ratio. Its key properties make it highly suitable for spacecraft antenna supports:
- High Strength: Exhibits significantly higher yield and tensile strength compared to conventional aluminum alloys, enabling the design of lightweight yet robust structures.
- Low Density: Its low density contributes to significant weight savings, a critical advantage for aerospace applications.
- Excellent Ductility: Offers good ductility, providing resistance to fracture under stress.
- Good Weldability: Demonstrates good weldability, which can be beneficial for integration with other spacecraft structures.
- Corrosion Resistance: Possesses good corrosion resistance, crucial for long-term performance in the space environment.
- Ti-6Al-4V (Titanium Grade 5): This widely used titanium alloy is renowned for its excellent combination of properties, making it a preferred choice for demanding aerospace applications:
- High Strength-to-Weight Ratio: Offers exceptional strength at a relatively low density, providing a significant weight advantage over steel alloys.
- Excellent Corrosion Resistance: Exhibits outstanding resistance to a wide range of corrosive environments, including those encountered in space.
- High Temperature Performance: Maintains good mechanical properties at elevated temperatures.
- Biocompatibility: While less critical for antenna supports, its biocompatibility is a significant advantage for medical applications, showcasing the versatility of this material.
The choice between Scalmalloy® and Ti-6Al-4V depends on the specific requirements of the antenna support, including the desired strength, weight targets, and thermal environment. Metal3DP‘s expertise in metal powders, developed through our advanced powder making system, ensures that our customers receive materials with high sphericity and flowability, optimized for consistent and high-quality 3D printing. Our range of high-quality metal powders extends beyond these two alloys, allowing us to cater to a wide spectrum of aerospace requirements.
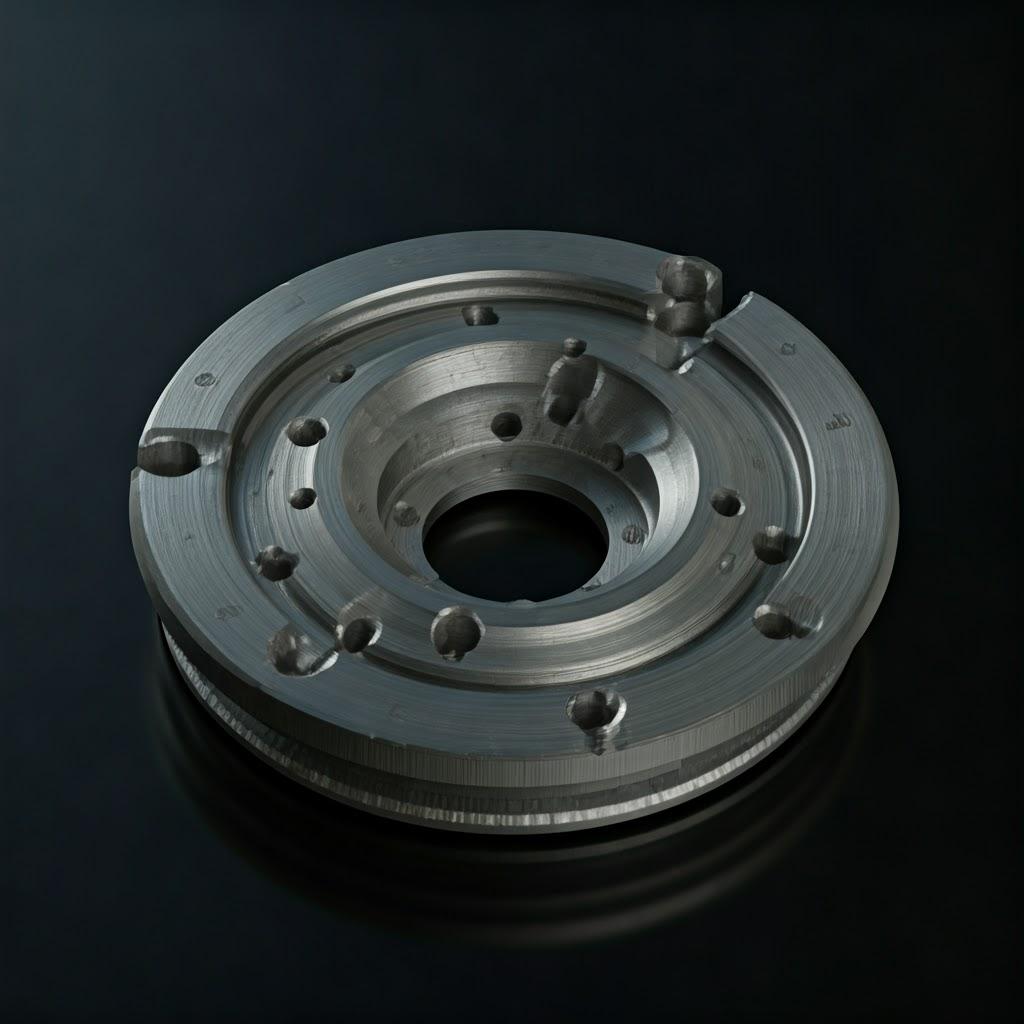
Design Considerations for Additive Manufacturing
Designing spacecraft antenna supports for metal 3D printing requires a different mindset compared to traditional manufacturing. To fully leverage the capabilities of additive manufacturing and achieve optimal performance, engineers must consider several key design principles:
- Topology Optimization: This computational method allows for the creation of highly efficient structures by strategically removing material from low-stress areas while maintaining strength and stiffness. For antenna supports, topology optimization can lead to significant weight reductions and improved structural integrity.
- Lattice Structures: Implementing lattice or grid-like internal structures within the support can provide excellent stiffness-to-weight ratios. Different lattice patterns can be chosen and customized to meet specific load-bearing requirements.
- Generative Design: Utilizing AI-powered algorithms, generative design explores a multitude of design options based on predefined constraints and performance goals. This can lead to innovative and highly optimized support geometries that might not be intuitively conceived through traditional design approaches.
- Part Consolidation: As mentioned earlier, 3D printing enables the integration of multiple components into a single part. For antenna supports, this could involve incorporating features for mounting sensors, cable routing, or thermal management directly into the main structure, reducing assembly time and potential failure points.
- Orientation and Support Structures: The orientation of the part during the printing process significantly impacts surface finish, dimensional accuracy, and the need for support structures. Careful consideration of the build orientation is crucial to minimize support material usage, which can be challenging to remove and may leave surface artifacts.
- Wall Thickness and Feature Size: Minimum wall thicknesses and feature sizes are dictated by the chosen metal powder and printing technology. Designing within these limitations ensures the manufacturability and structural integrity of the support.
- Thermal Management: Spacecraft experience extreme temperature variations. Designing antenna supports with internal channels or optimized geometries can facilitate thermal dissipation or integration with thermal control systems.
Metal3DP‘s team of experienced engineers possesses deep expertise in designing for additive manufacturing. We work closely with our clients to optimize their antenna support designs for performance, weight reduction, and efficient 3D printing on our advanced SEBM systems. Our understanding of the nuances of materials like Scalmalloy® and Ti-6Al-4V allows us to guide design choices that maximize the benefits of these high-performance alloys.
Tolerance, Surface Finish, and Dimensional Accuracy
Achieving the required tolerance, surface finish, and dimensional accuracy is critical for the proper functioning and integration of spacecraft antenna supports. Metal 3D printing technologies have made significant strides in these areas, but careful process control and post-processing may still be necessary depending on the application’s demands.
- Tolerance: The achievable tolerance in metal 3D printing depends on factors such as the printing technology, material, part geometry, and build orientation. Selective Electron Beam Melting (SEBM), the technology employed by Metal3DP, generally offers good dimensional accuracy. However, tight tolerances may require post-processing steps like precision machining.
- Surface Finish: The as-printed surface finish in metal 3D printing is typically rougher than that achieved by machining. The surface roughness is influenced by the metal powder particle size and the layer thickness used during printing. For applications requiring smooth surfaces, post-processing techniques such as polishing, grinding, or media blasting can be employed.
- Dimensional Accuracy: Maintaining dimensional accuracy throughout the printing process is crucial. Factors like thermal expansion and contraction of the material during printing can affect the final dimensions. Optimized build parameters and support structures are essential to minimize distortion. For critical dimensions, post-printing inspection and potentially corrective machining may be necessary.
Metal3DP‘s commitment to delivering high-quality parts includes rigorous process control and inspection procedures to ensure dimensional accuracy. We also offer various post-processing services to achieve the desired surface finish and tighter tolerances, ensuring that the antenna supports meet the precise specifications required for their demanding applications. Our expertise in materials and printing methods allows us to tailor the manufacturing process to achieve the optimal balance between precision and efficiency.
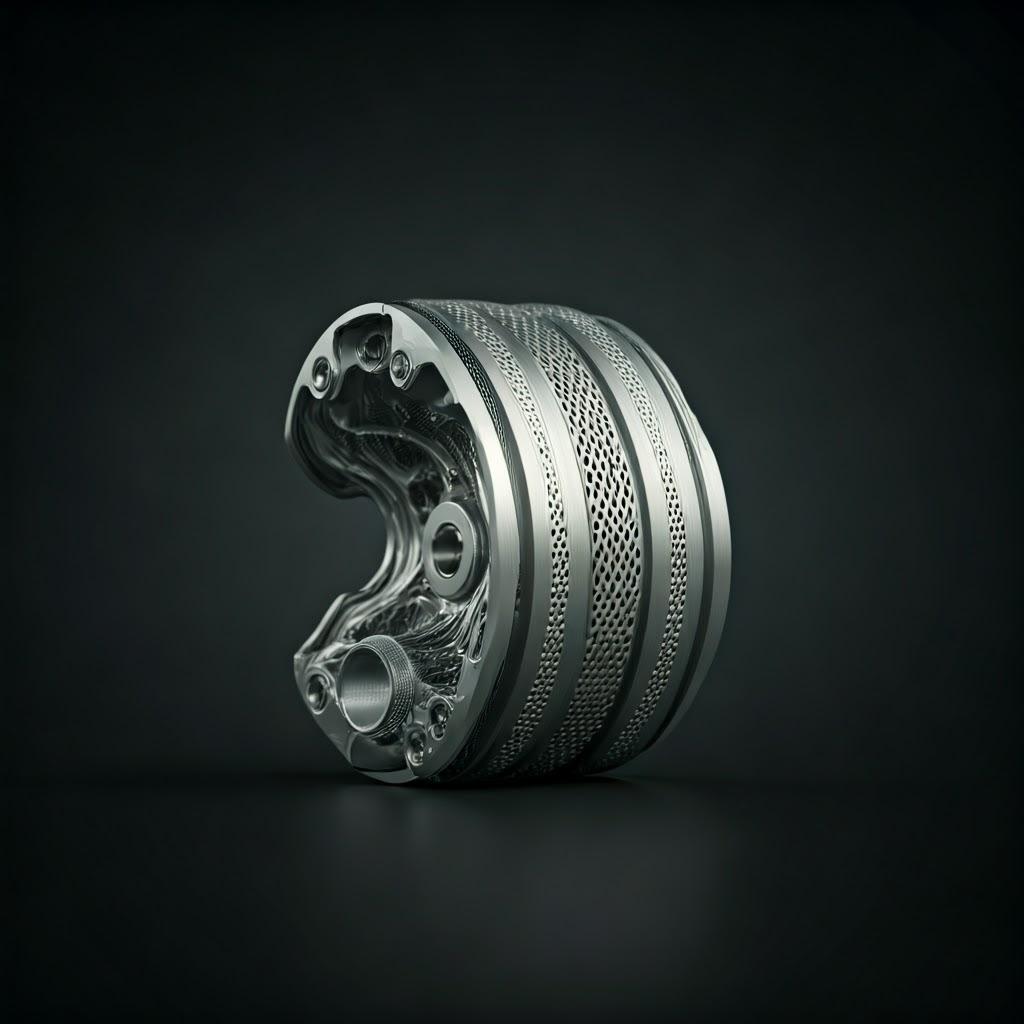
Post-Processing Requirements
While metal 3D printing offers significant advantages, post-processing steps are often required to achieve the final desired properties and finish for spacecraft antenna supports. Common post-processing requirements include:
- Support Removal: Support structures are often necessary during the printing process to prevent warping and ensure the correct geometry of overhanging features. Removing these supports can be a manual or automated process, depending on the complexity of the part and the support design.
- Heat Treatment: Heat treatment is frequently employed to relieve internal stresses developed during the rapid cooling of the printing process and to optimize the mechanical properties of the material, such as strength and ductility. The specific heat treatment cycle depends on the alloy being used (e.g., stress relieving for Ti-6Al-4V or solution annealing and aging for Scalmalloy®).
- Surface Finishing: As mentioned earlier, surface finishing techniques like polishing, grinding, or media blasting may be required to achieve the desired surface roughness for functional or aesthetic reasons.
- CNC Machining: For critical features requiring very tight tolerances or specific surface finishes that are difficult to achieve directly through 3D printing, precision CNC machining may be employed as a secondary operation.
- Inspection and Quality Control: Thorough inspection using techniques like coordinate measuring machines (CMM), non-destructive testing (NDT), and material analysis is crucial to ensure that the printed parts meet the required quality standards and specifications for aerospace applications.
- Coating and Surface Treatment: Depending on the specific mission requirements, antenna supports may require coatings for enhanced corrosion resistance, thermal control, or electrical conductivity.
Metal3DP offers comprehensive post-processing services to ensure that the final parts meet the stringent requirements of the aerospace industry. Our understanding of the specific post-processing needs for materials like Scalmalloy® and Ti-6Al-4V ensures optimal performance and reliability of the printed antenna supports. We adhere to strict quality control procedures throughout the entire manufacturing process, from powder selection to final inspection.
Common Challenges and How to Avoid Them
While metal 3D printing offers numerous benefits, several challenges can arise during the manufacturing of spacecraft antenna supports. Understanding these potential issues and implementing appropriate strategies can help avoid them:
- Warping and Distortion: Thermal stresses during the printing process can lead to warping or distortion of the part, particularly for complex geometries or thin-walled sections. Optimized build orientation, support structure design, and process parameters can mitigate these issues.
- Porosity: Internal voids or porosity within the printed part can compromise its mechanical properties. Using high-quality metal powders with good flowability, optimizing printing parameters (e.g., laser power, scan speed), and ensuring a controlled printing environment can minimize porosity. Metal3DP‘s advanced powder making system ensures the high quality of our metal powders, contributing to the production of dense, high-performance parts.
- Support Removal Difficulties: Intricately designed supports can be challenging and time-consuming to remove, potentially damaging the part’s surface. Designing smart support structures and utilizing dissolvable support materials (where applicable) can ease the removal process.
- Surface Roughness: Achieving a smooth surface finish directly from the printing process can be difficult. Planning for appropriate post-processing techniques early in the design phase is crucial.
- Material Property Consistency: Ensuring consistent material properties throughout the printed part is essential for structural integrity. Optimized process parameters and strict quality control measures are necessary to achieve this.
- Cost Management: While 3D printing can be cost-effective for certain applications, material costs and post-processing can impact the overall price. Careful design optimization to minimize material usage and the need for extensive post-processing is essential for cost management.
Metal3DP leverages its extensive experience and expertise in metal additive manufacturing to address these challenges effectively. Our advanced equipment, optimized process parameters, and skilled engineers ensure that we can produce high-quality spacecraft antenna supports with minimal defects and consistent performance. We work collaboratively with our clients to identify potential challenges early in the design phase and implement strategies to mitigate them.
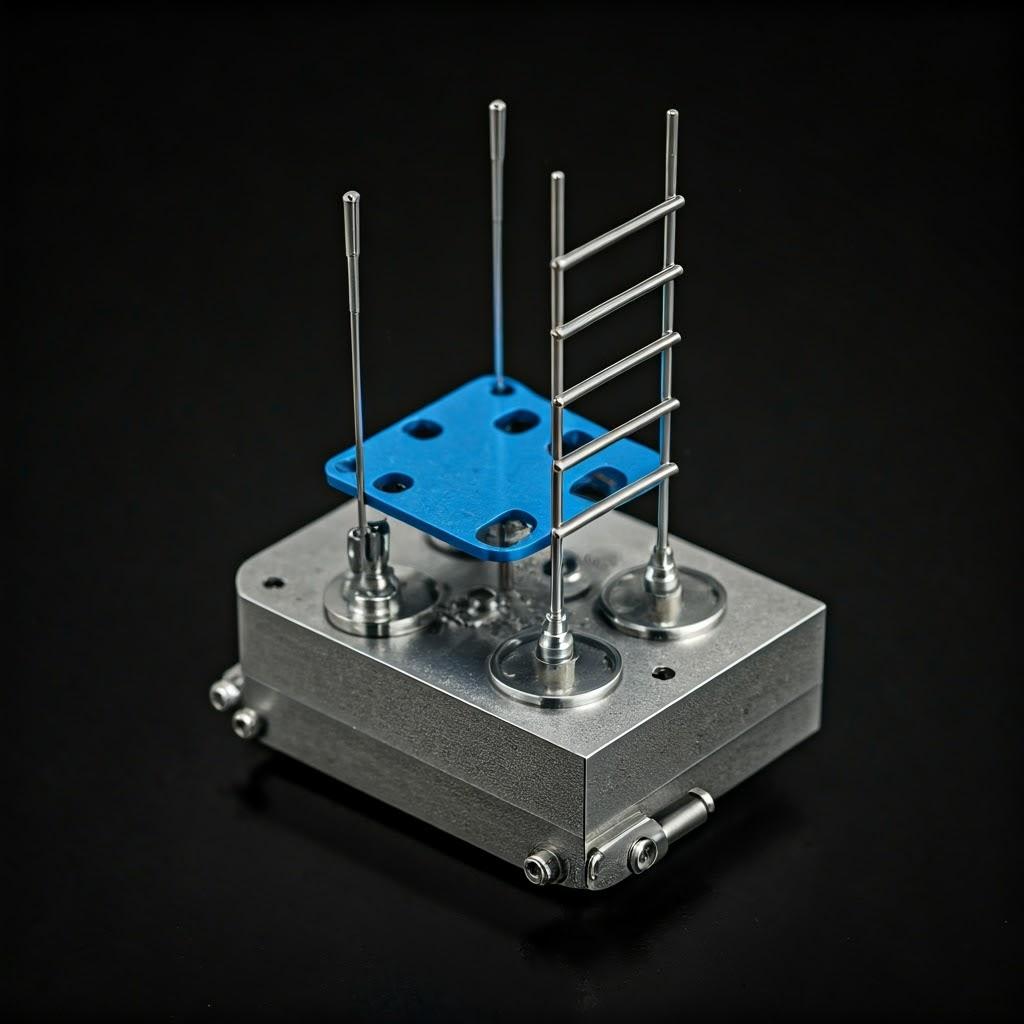
How to Choose the Right Metal 3D Printing Service Provider
Selecting the right metal 3D printing service provider is a critical decision that can significantly impact the quality, cost, and lead time of your spacecraft antenna supports. Consider the following factors when evaluating potential suppliers:
- Material Capabilities: Ensure the provider has experience processing the specific metal powders required for your application, such as Scalmalloy® or Ti-6Al-4V. Verify their expertise in handling these materials and their ability to achieve the desired material properties. Metal3DP boasts extensive experience with a wide range of high-quality metal powders, including those ideal for aerospace applications.
- Technology and Equipment: Understand the types of metal 3D printing technologies the provider utilizes. For high-performance aerospace components, technologies like Selective Electron Beam Melting (SEBM), as employed by Metal3DP, often offer advantages in terms of material density and internal stress. Inquire about the accuracy, build volume, and reliability of their printers. Our printing methods page provides insights into the capabilities of different AM technologies.
- Quality Assurance and Certifications: Verify if the provider has robust quality management systems and relevant certifications, such as AS9100 for aerospace applications. Inquire about their inspection procedures, material testing capabilities, and dimensional accuracy guarantees.
- Design and Engineering Support: Assess whether the provider offers design for additive manufacturing (DfAM) services. Experienced engineers can help optimize your antenna support design for 3D printing, ensuring manufacturability, weight reduction, and performance enhancement. Metal3DP‘s team possesses deep expertise in DfAM and can collaborate with you throughout the design process.
- Post-Processing Capabilities: Determine if the provider offers the necessary post-processing services, such as support removal, heat treatment, surface finishing, and CNC machining. A comprehensive service offering can streamline the manufacturing process and ensure the final part meets your specifications. Metal3DP provides a range of post-processing solutions tailored to the requirements of aerospace components.
- Lead Times and Production Capacity: Discuss lead times for prototyping and production, and ensure the provider has the capacity to meet your project timelines.
- Cost Structure and Transparency: Obtain a clear breakdown of the costs involved, including material, printing, and post-processing. Understand the factors that influence pricing and ensure transparency in their quoting process.
- Communication and Customer Support: Evaluate the provider’s responsiveness, communication effectiveness, and willingness to collaborate. A strong partnership is crucial for a successful project.
Choosing Metal3DP as your metal 3D printing service provider means partnering with a company dedicated to quality, innovation, and customer satisfaction. Our industry-leading SEBM printers, coupled with our expertise in advanced metal powders and comprehensive post-processing services, make us a trusted partner for aerospace applications. You can learn more about our capabilities on our about us page.
Cost Factors and Lead Time
The cost and lead time for producing spacecraft antenna supports using metal 3D printing are influenced by several factors:
Cost Factors:
- Material Costs: The price of the metal powder (e.g., Scalmalloy®, Ti-6Al-4V) is a significant contributor to the overall cost. Specialized aerospace-grade alloys can be more expensive than standard materials.
- Printing Time: The build time depends on the complexity of the part, its size, and the chosen layer height. Longer print times translate to higher machine operating costs.
- Support Material: The volume and complexity of support structures required will impact material usage and post-processing time, thus affecting the cost.
- Post-Processing Costs: The extent of post-processing required (e.g., support removal, heat treatment, machining, surface finishing) will add to the overall cost. Complex post-processing can significantly increase the final price.
- Design Optimization: Investing in design optimization for additive manufacturing can potentially reduce material usage and printing time, leading to cost savings in the long run.
- Quantity: While 3D printing is often cost-effective for low to medium volumes and customized parts, the cost per part may decrease with larger production runs, depending on the specific technology and provider.
Lead Time Factors:
- Design and Engineering: The time required for design optimization and preparation for 3D printing.
- Printing Time: As mentioned above, the actual build time on the 3D printer.
- Post-Processing: The time needed for support removal, heat treatment, surface finishing, and any other required post-processing steps.
- Quality Control and Inspection: Thorough inspection processes can add to the overall lead time.
- Scheduling and Production Queue: The service provider’s current workload and production schedule can influence the lead time.
Metal3DP is committed to providing transparent and competitive pricing while adhering to efficient lead times. We work closely with our clients to understand their specific requirements and optimize the manufacturing process to balance cost and delivery schedules effectively.
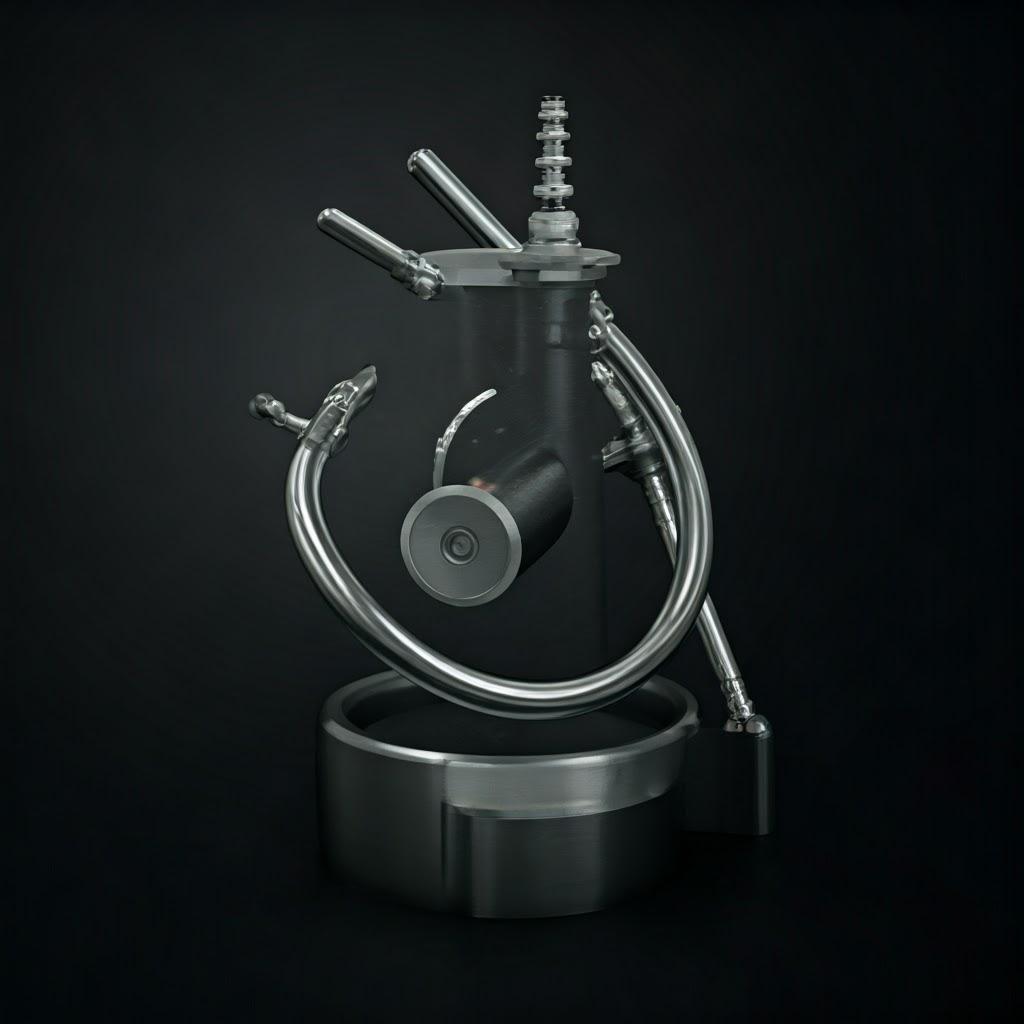
Frequently Asked Questions (FAQ)
- Q: Is metal 3D printing strong enough for spacecraft applications?
- A: Yes, when the appropriate materials and printing parameters are used, metal 3D printed parts can exhibit excellent strength and durability suitable for demanding aerospace environments. Alloys like Scalmalloy® and Ti-6Al-4V, processed on advanced systems like Metal3DP‘s SEBM printers, offer high strength-to-weight ratios and can meet stringent aerospace specifications.
- Q: What are the typical tolerances achievable with metal 3D printing for antenna supports?
- A: Achievable tolerances depend on the specific technology, material, and part geometry. While metal 3D printing offers good dimensional accuracy, tight tolerances may require post-processing like CNC machining. Metal3DP can provide detailed tolerance information based on your specific design and material requirements.
- Q: Can metal 3D printed antenna supports withstand the harsh space environment?
- A: Yes, materials like Ti-6Al-4V offer excellent corrosion resistance and can withstand the temperature variations and radiation encountered in space. Proper material selection and potentially surface treatments are crucial for ensuring long-term performance in the space environment. Metal3DP offers materials and post-processing options suitable for space applications.
Conclusion
Metal 3D printing is revolutionizing the manufacturing of spacecraft antenna supports, offering unprecedented design freedom, material efficiency, and the potential for enhanced performance. By leveraging advanced materials like Scalmalloy® and Ti-6Al-4V and sophisticated printing technologies like Selective Electron Beam Melting, engineers and procurement managers in the aerospace industry can create lightweight, robust, and highly customized components that meet the demanding requirements of space missions. Metal3DP is a leading provider of comprehensive metal additive manufacturing solutions, offering industry-leading printing equipment, high-quality metal powders, and expert application development services. Partner with us to explore how our capabilities can power your organization’s additive manufacturing goals and drive innovation in spacecraft technology. Contact Metal3DP today to discuss your specific needs and discover the transformative potential of metal 3D printing for your next aerospace project.
Share On
MET3DP Technology Co., LTD is a leading provider of additive manufacturing solutions headquartered in Qingdao, China. Our company specializes in 3D printing equipment and high-performance metal powders for industrial applications.
Inquiry to get best price and customized Solution for your business!
Related Articles
About Met3DP
Recent Update
Our Product
CONTACT US
Any questions? Send us message now! We’ll serve your request with a whole team after receiving your message.
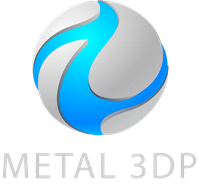
Metal Powders for 3D Printing and Additive Manufacturing
COMPANY
PRODUCT
cONTACT INFO
- Qingdao City, Shandong, China
- [email protected]
- [email protected]
- +86 19116340731