Common types of additive manufacturing equipment
Table of Contents
Additive manufacturing, also known as 3D printing, has transformed the way we design and produce objects. Imagine building something layer by layer, like constructing a miniature brick castle one tiny piece at a time. That’s the essence of 3D printing, where a digital blueprint is translated into a physical object through the meticulous stacking of materials. But just like there are different types of bricks (think Legos versus real bricks), there’s a whole arsenal of additive manufacturing equipment, each with its own strengths and specialties. Let’s delve into the fascinating world of these 3D printing workhorses and explore the ones that have revolutionized the manufacturing landscape.
Melt Deposition Modeling (FDM)
Think of a hot glue gun on steroids, and you’ve got a good idea of how FDM, or Fused Deposition Modeling, works. This widely used technology uses a continuous filament of thermoplastic material (think ABS, PLA, or nylon) that’s fed through a heated nozzle. The nozzle melts the plastic, and as it moves across a platform layer by layer, it deposits the molten material, building the object one skinny strand at a time.
The Perks of FDM:
- Accessibility: FDM printers are some of the most affordable and user-friendly options on the market. This makes them perfect for hobbyists, makerspaces, and even classrooms where students can experiment with 3D design and printing.
- Versatility: FDM offers a wide range of filament choices, allowing you to create objects with varying strengths, flexibilities, and even colors.
- Durability: FDM-printed parts can be surprisingly strong, making them suitable for functional prototypes and even some end-use applications.
The Flip Side of FDM:
- Surface Finish: FDM-printed objects often have a visible layer-by-layer texture, which can be undesirable for applications requiring a smooth finish. Post-processing techniques like sanding and painting can improve aesthetics, but they add time and effort.
- Limited Resolution: Compared to other technologies, FDM printers have a larger nozzle diameter, resulting in lower resolution prints. This might not be ideal for intricate details or highly complex geometries.
Who should consider FDM?
FDM is a fantastic starting point for anyone new to 3D printing. Its affordability, user-friendliness, and wide range of materials make it a versatile tool for prototyping, creating functional parts, and even artistic endeavors.
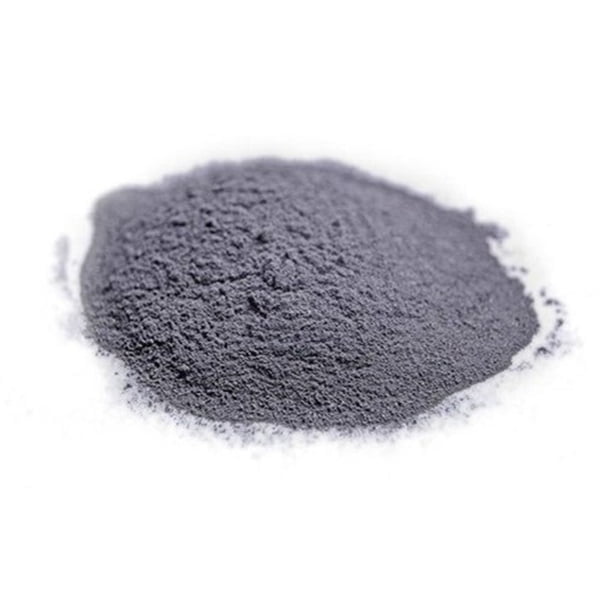
Additive manufacturing equipment: Stereolithography (SLA)
Imagine a vat filled with liquid plastic that hardens when exposed to light. That’s the basic principle behind Stereolithography Apparatus (SLA) printing. Here, a laser beam selectively cures thin layers of photosensitive resin in a vat, meticulously building the object from the bottom up.
The Allure of SLA:
- Unmatched Detail: SLA printers boast incredible resolution, producing objects with smooth surfaces and sharp features. This makes them ideal for applications demanding intricate details, such as jewelry prototypes, dental prosthetics, and even high-quality figurines.
- Wide Range of Materials: Similar to FDM, SLA offers a variety of resins with different properties, catering to specific needs like transparency, biocompatibility, or high-temperature resistance.
The Challenges of SLA:
- Cost: SLA printers tend to be more expensive than FDM machines. The cost of resin can also add up, especially for larger prints.
- Post-Processing: SLA prints require a cleaning process to remove excess resin and support structures. Depending on the complexity of the design, this can be time-consuming.
Who should consider SLA?
If high-resolution detail and a smooth finish are paramount, SLA is the way to go. It’s ideal for professionals like jewelers, dentists, and product designers who require precise and visually stunning prototypes.
Selective Laser Sintering (SLS)
Think of SLS (Selective Laser Sintering) as a metal version of SLS printing. Here, a high-powered laser beam selectively melts tiny particles of metal powder, fusing them together layer by layer to create a solid object.
The Power of SLS:
- Metal Printing: SLS opens doors to printing functional metal parts. This empowers engineers and designers to create prototypes and even end-use metallic components with complex geometries that traditional manufacturing might struggle with.
- High Strength: SLS-printed metal parts boast excellent strength and durability, rivaling traditionally manufactured components.
The Considerations for SLS:
- Cost: SLS printers are expensive, and the cost of metal powders can be high as well. This technology is typically used for industrial applications where the investment is justified by the creation of high-value metallic parts.
- Safety: Due to the use of metal powder and high-powered lasers, SLS printers require a controlled environment and proper safety protocols to operate.
Who should consider SLS?
SLS is a powerful tool for industries like aerospace, automotive, and medical where functional and robust metal parts are needed. It’s ideal for creating prototypes, complex components, and even some end-use metallic applications.
Multi Jet Fusion (MJF)
Multi Jet Fusion (MJF) is a relatively new kid on the block that’s making waves in the additive manufacturing world. This HP-developed technology utilizes inkjet printing principles but with a twist. Instead of ink, it uses a combination of fusing and detailing agents. Here’s a breakdown:
- Fusing Agent: This inkjet-deposited material acts like a glue, binding the powder particles together.
- Detailing Agent: This agent modifies the properties of specific areas in the powder bed, allowing for intricate features and internal channels within the printed object.
The Advantages of MJF:
- Speed Demon: MJF boasts impressive printing speeds, making it a great choice for high-volume production runs.
- Functional Parts: Similar to SLS, MJF can produce functional parts with good mechanical properties, making it suitable for prototyping and even some end-use applications.
- Fine Detail: While not quite on par with SLA, MJF offers a good balance between speed and resolution, producing parts with decent detail and a smooth surface finish.
The Considerations for MJF:
- Limited Material Options: Currently, MJF has a smaller range of material options compared to some other technologies.
- Post-Processing: MJF prints require some post-processing steps like infiltration to enhance strength and remove unbound powder.
Who should consider MJF?
MJF is a compelling option for companies looking for a balance between speed, functionality, and detail. It’s well-suited for prototyping, low-volume production runs, and applications where a smooth surface finish is desired.
Binder Jetting
Binder jetting takes a unique approach to 3D printing. Imagine a 3D inkjet printer that, instead of ink, deposits a binding agent onto a bed of powder particles. Here’s a simplified explanation:
- Powder Bed: The powder bed can be made from various materials, including sand, metal, or even ceramics.
- Binder Agent: The inkjet head selectively deposits a liquid binder that glues the powder particles together, building the object layer by layer.
The Strengths of Binder Jetting:
- Material Versatility: One of the biggest advantages of binder jetting is its ability to work with a wide range of materials, including metals, ceramics, and even sand. This opens doors to diverse applications.
- Full-Color Printing: Some binder jetting systems can even incorporate multiple binder agents with different colors, enabling full-color 3D printing.
The Considerations for Binder Jetting:
- Strength: The strength of binder-jetted parts depends on the material and the binder used. In some cases, the parts might require additional post-processing steps like infiltration for enhanced strength.
- Resolution: Binder jetting printers typically have a larger nozzle diameter compared to other technologies, resulting in a slightly lower resolution.
Who should consider Binder Jetting?
Binder jetting is a versatile technology suitable for various applications. It’s a good choice for prototyping, creating full-color models, and printing with unique materials like sand for creating complex molds.
Electron Beam Melting (EBM)
Electron Beam Melting (EBM) is an advanced additive manufacturing technology that utilizes a high-powered electron beam to melt metal powder layer by layer. Here’s a closer look:
- High-Vacuum Environment: EBM printing takes place in a high-vacuum chamber to prevent oxidation of the molten metal.
- Electron Beam: A focused electron beam melts the metal powder particles, fusing them together to create a dense and strong metallic object.
The Allure of EBM:
- Superior Strength: EBM-printed parts boast exceptional strength and excellent mechanical properties, making them ideal for demanding applications.
- Biocompatible Materials: EBM can work with certain biocompatible metal powders like titanium, making it suitable for medical implants.
The Considerations for EBM:
- Cost: EBM printers are expensive, and the metal powders used can be quite pricey as well. This technology is typically used for high-value applications where exceptional strength is crucial.
- Surface Finish: EBM-printed parts often have a rough surface texture that might require additional machining for a smoother finish.
Who should consider EBM?
EBM is a powerful tool for industries like aerospace, automotive, and medical where high-performance metal parts are needed. It’s ideal for creating components that demand exceptional strength, such as turbine blades, implants, and other demanding applications.
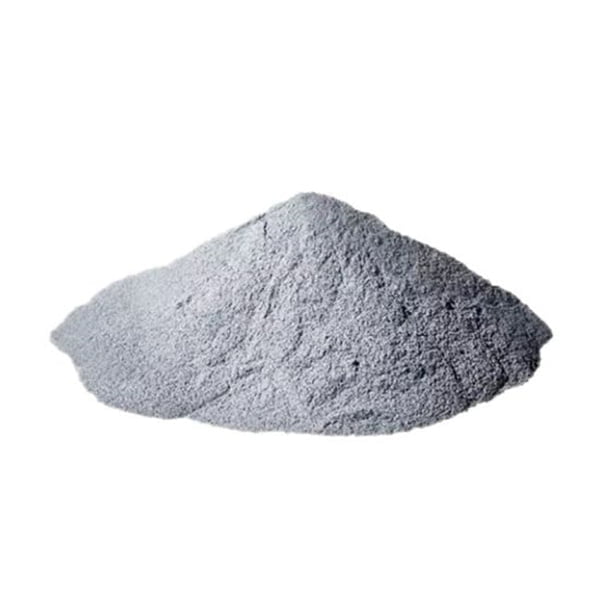
Digital Light Processing (DLP)
Digital Light Processing (DLP) shares some similarities with SLA printing but with a technological twist. Here’s how it works:
- Digital Projector: Instead of a single laser beam, DLP utilizes a digital projector that flashes a light pattern across a vat of photosensitive resin.
- Layer-by-Layer Curing: The light pattern cures entire layers of resin at once, significantly speeding up the printing process compared to SLA.
The Benefits of DLP:
- High Speed: DLP printers boast impressive printing speeds, making them a good option for high-volume production runs of resin-based parts.
- Smooth Surface Finish: Similar to SLA, DLP produces objects with a smooth surface finish, ideal for applications requiring high aesthetics.
The Considerations for DLP:
- Resolution: The resolution of DLP prints can be slightly lower compared to SLA due to the pixel size of the projector.
- Material Options: DLP printers typically have a smaller range of material options compared to SLA.
Who should consider DLP?
DLP is a compelling choice for companies looking for a balance between speed, quality, and affordability for resin-based printing. It’s well-suited for applications like creating high-quality prototypes, dental molds, and even jewelry production.
Material Jetting
Material jetting is another inkjet-based 3D printing technology that offers unique advantages. Here’s a breakdown of the process:
- Multi-Material Printing: Unlike traditional inkjet printers with a single ink cartridge, material jetting printers can utilize multiple printheads loaded with different materials.
- Droplet-on-Demand Printing: These printheads jet droplets of various materials onto a build platform, meticulously building the object layer by layer.
The Strengths of Material Jetting:
- High Resolution: Material jetting printers offer exceptional resolution, producing objects with incredibly fine details and smooth surface finishes.
- Multi-Material Capability: The ability to use different materials within a single print opens doors to creating objects with varying properties, colors, and functionalities.
The Considerations for Material Jetting:
- Cost: Material jetting printers are on the higher end of the cost spectrum. The materials used can also be expensive, especially for multi-material prints.
- Limited Material Options: While it offers multi-material printing, the overall range of materials available for material jetting is still evolving.
Who should consider Material Jetting?
Material jetting is ideal for applications demanding exceptional detail, multi-material functionality, and a high-quality finish. It’s a valuable tool for creating prototypes, detailed models, and even functional parts with integrated features.
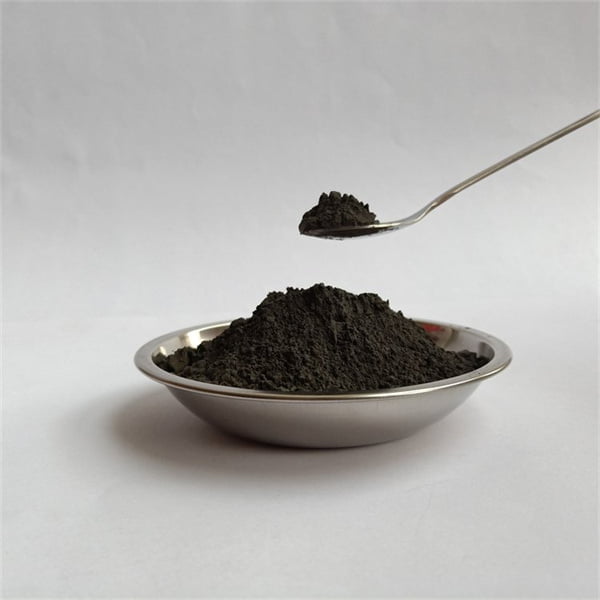
FAQs
Here are some frequently asked questions (FAQs) about common types of additive manufacturing equipment, presented in a table format for easy reference:
Question | FDM | SLA | SLS | MJF | Binder Jetting | EBM | DLP | Material Jetting |
---|---|---|---|---|---|---|---|---|
What materials can it print with? | Thermoplastics (ABS, PLA, Nylon, etc.) | Photosensitive Resin | Metal Powders | Nylon Powders (limited options) | Various Powders (sand, metal, ceramic) | Metal Powders (typically Titanium) | Photosensitive Resin | Various materials (depending on printheads) |
What are the advantages? | Affordable, User-friendly, Wide range of materials | High resolution, Smooth surface finish | Functional metal parts, High strength | High speed, Good detail, Functional parts | Material versatility, Full-color printing possible | Exceptional strength, Biocompatible materials | Speedy production, Smooth surface finish | High resolution, Multi-material capability |
What are the disadvantages? | Lower resolution, Visible layer lines | Expensive, Post-processing required | Expensive, Limited materials, Safety considerations | Limited materials, Post-processing required | Lower resolution, Weaker parts (might require infiltration) | Expensive, Rough surface finish | Slightly lower resolution compared to SLA | Expensive, Limited material options |
Share On
MET3DP Technology Co., LTD is a leading provider of additive manufacturing solutions headquartered in Qingdao, China. Our company specializes in 3D printing equipment and high-performance metal powders for industrial applications.
Inquiry to get best price and customized Solution for your business!
Related Articles
About Met3DP
Recent Update
Our Product
CONTACT US
Any questions? Send us message now! We’ll serve your request with a whole team after receiving your message.
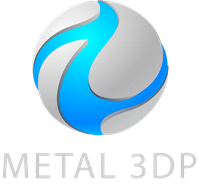
Metal Powders for 3D Printing and Additive Manufacturing