Additive Manufacturing Powder
Table of Contents
Overview
Additive manufacturing (AM), also known as 3D printing, utilizes metal powders to construct components layer by layer based on digital models. The powder acts as the feedstock and is selectively melted, sintered, or bound by precision heat sources guided by the CAD geometries.
Popular AM processes for metals include binder jetting, directed energy deposition, powder bed fusion, and sheet lamination. Each technique requires powder with specific characteristics to achieve optimal density, surface finish, dimensional precision, and mechanical properties in the printed parts.
This guide provides an in-depth look at metal powder for AM, including alloy options, production methods, key powder properties, applications, specifications, suppliers, and purchasing considerations when sourcing material. Helpful comparison tables summarize technical data to assist with powder selection and qualification.
Sourcing optimized AM powder enables manufacturers to improve print quality, reduce defects, and fully leverage 3D printing benefits like design freedom, faster iteration, and part consolidation. Connecting with knowledgeable suppliers simplifies raw material qualification.
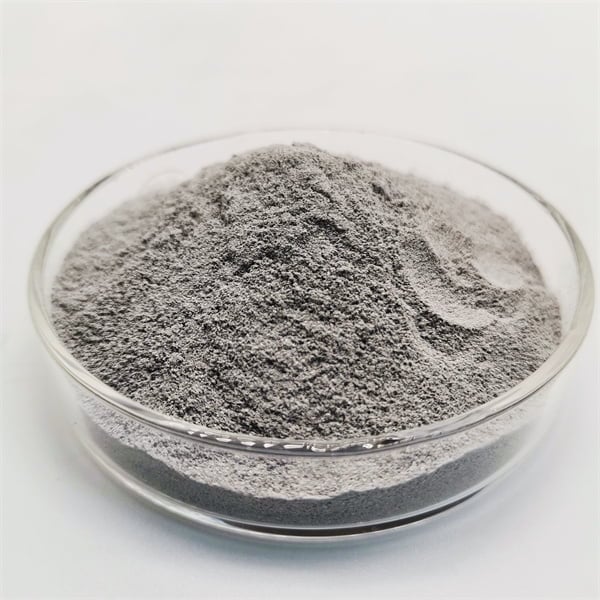
Alloy Options for AM Powder
A wide range of metals and alloys are available as optimized powder feedstock for 3D printing processes:
Common Alloy Systems for Additive Manufacturing Powder
- Stainless steels
- Tool steels
- Titanium and titanium alloys
- Aluminum alloys
- Nickel superalloys
- Cobalt-chrome alloys
- Precious metals like gold, silver
- Exotic alloys like copper, tantalum, tungsten
Both standard and custom alloys can be sourced to meet specific needs in terms of corrosion resistance, strength, hardness, conductivity, or other properties.
Metal Powder Production Methods for AM
Additive manufacturing utilizes metal powder produced through:
Typical Metal Powder Manufacturing Methods for AM
- Gas atomization
- Water atomization
- Plasma atomization
- Electrolysis
- Carbonyl iron process
- Mechanical alloying
- Metal hydriding/dehydriding
- Plasma spheroidization
- Granulation
Spherical atomized powders provide optimal flow and dense packing required for most AM processes. Some techniques allow nanoscale or customized alloy particles.
Key Characteristics of AM Metal Powder
Critical powder characteristics for AM include:
Metal Additive Manufacturing Powder Properties
Characteristic | Typical Values | Importance |
---|---|---|
Particle size distribution | 10 to 45 microns | Affects densification, surface finish |
Particle shape | Spherical | Improves powder flow and packing |
Apparent density | 2 to 4 g/cc | Influences powder bed density |
Tap density | 3 to 6 g/cc | Indicates compressibility |
Hall flow rate | 25-50 s/50g | Ensures smooth powder spreading |
Loss on ignition | 0.1-0.5% | Low moisture content improves printing |
Oxygen content | <0.1% | Minimizes defects from oxides |
Precisely controlling characteristics like particle size, shape, and chemistry is critical to achieving fully dense AM parts with desired properties.
Applications of AM Metal Powder
Additive manufacturing enables complex geometries impossible through conventional techniques:
Metal Additive Manufacturing Applications
Industry | Uses | Benefits |
---|---|---|
Aerospace | Turbine blades, structures | Design freedom, weight reduction |
Medical | Implants, prosthetics, instruments | Customized shapes |
Automotive | Lightweighting prototypes and tools | Rapid iteration |
Defense | Drone parts, protective structures | Quick prototypes and short runs |
Energy | Heat exchangers, manifolds | Part consolidation and topology optimization |
Electronics | Shielding, cooling devices, EMI | Complex enclosed structures |
Lightweighting, part consolidation, and high-performance alloys for extreme environments provide key advantages over traditional manufacturing methods.
Specifications for AM Metal Powder
International specifications help standardize AM powder characteristics:
Metal Powder Standards for Additive Manufacturing
Standard | Scope | Parameters | Test Methods |
---|---|---|---|
ASTM F3049 | Guide for characterizing AM metals | Sampling, size analysis, chemistry, defects | Microscopy, diffraction, SEM-EDS |
ASTM F3001-14 | Titanium alloys for AM | Particle size, chemistry, flow | Sieving, SEM-EDS |
ASTM F3301 | Nickel alloys for AM | Particle shape and size analysis | Microscopy, image analysis |
ASTM F3056 | Stainless steel for AM | Chemistry, powder properties | ICP-OES, pycnometry |
ISO/ASTM 52921 | Standard terminology for AM powders | Definitions and powder characteristics | Various |
Compliance with published specifications ensures repeatable, high quality powder feedstock for critical applications.
Global Suppliers of AM Metal Powder
Leading international suppliers of AM-optimized metal powders include:
Metal Powder Manufacturers for Additive Manufacturing
Supplier | Materials | Typical Particle Size |
---|---|---|
Sandvik | Stainless, tool steel, nickel alloys | 15-45 microns |
Praxair | Titanium, superalloys | 10-45 microns |
AP&C | Titanium, nickel, cobalt alloys | 5-25 microns |
Carpenter Additive | Cobalt chrome, stainless, copper | 15-45 microns |
LPW Technology | Aluminum alloys, titanium | 10-100 microns |
EOS | Tool steel, cobalt chrome, stainless | 20-50 microns |
Many focus on fine spherical powders specifically engineered for common AM methods like binder jetting, powder bed fusion, and directed energy deposition.
Purchasing Considerations for AM Metal Powder
Key aspects to discuss with suppliers:
- Desired alloy composition and properties
- Target particle size distribution and shape
- Envelope density and hall flowability
- Allowable impurity levels like oxygen and moisture
- Required testing data and powder characterization
- Available quantity range and lead times
- Special handling precautions for pyrophoric alloys
- Quality systems and powder origin traceability
- Technical expertise in AM powder requirements
- Logistics and delivery mechanisms
Work closely with suppliers experienced in AM-specific powders to ensure ideal material selection for your process and components.
Pros and Cons of AM Metal Powder
Benefits vs Limitations of Metal Powder for Additive Manufacturing
Advantages | Disadvantages |
---|---|
Allows complex, customized geometries | Higher cost than conventional materials |
Shortens development time dramatically | Powder handling precautions required |
Simplifies assemblies and lightweights | Post-processing often needed on as-printed parts |
Achieves properties nearing wrought materials | Size and build volume constraints |
Eliminates expensive tooling | Thermal stresses can cause cracking and distortion |
Enables parts consolidation and topology optimization | Lower production volumes than traditional methods |
Improves buy-to-fly ratio greatly | Requires rigorous powder characterization and parameter development |
When used appropriately, metal AM provides game-changing benefits but requires expertise to implement successfully.
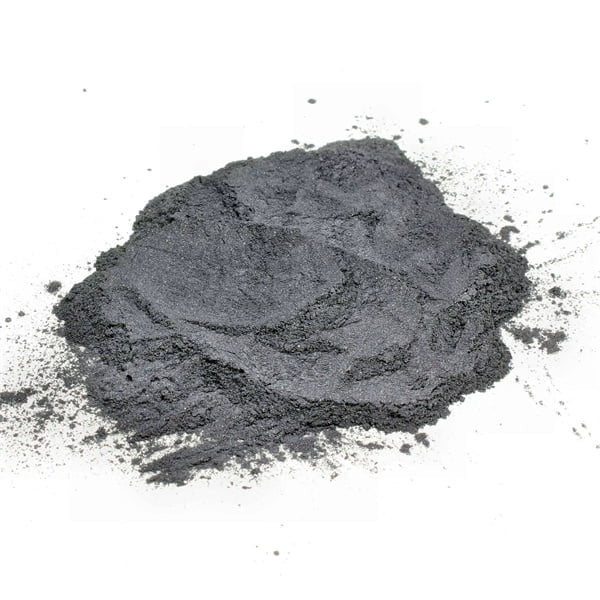
FAQs
How small can particle size be for metal additive manufacturing?
Specialized atomization techniques can produce powder down to 1-10 microns, however most metals printers work best with minimum size around 15-20 microns for good flow and packing.
What causes poor surface finish in printed metal parts?
Surface roughness arises from partially melted powder adhered to surfaces, spatter, staircase stepping, and suboptimal melt pool characteristics. Using finer powders and dialing in ideal processing parameters smoothens finish.
Do all metal 3D printing methods work with the same powders?
While there is overlap, binder jetting generally uses a broader powder size distribution than powder bed fusion. Some processes are limited to certain alloys based on melting points or reactivity.
How are mixed or bimetallic powders made?
Prealloyed powders ensure uniform properties but for composites, physical powder blending or specialized atomization techniques provide custom blended elemental powder mixes.
How long does it take to change powder material in a metal printer?
A full purge and changeover between significantly different alloys requires 6-12 hours typically. Quick changes between similar materials can be under an hour.
Conclusion
Optimized metal powders enable additive manufacturing processes to construct complex, robust metal components with superior properties. Matching alloy chemistry and powder characteristics to the printing method and component performance requirements is critical to high quality results. By partnering with experienced powder suppliers, end users leverage expertise in both powder production and 3D printing processes to develop parts faster and more reliably. Continued advances in metal powders help drive increased adoption of additive techniques across critical industries.
Share On
MET3DP Technology Co., LTD is a leading provider of additive manufacturing solutions headquartered in Qingdao, China. Our company specializes in 3D printing equipment and high-performance metal powders for industrial applications.
Inquiry to get best price and customized Solution for your business!
Related Articles
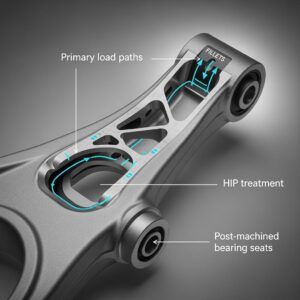
Metal 3D Printing for U.S. Automotive Lightweight Structural Brackets and Suspension Components
Read More »About Met3DP
Recent Update
Our Product
CONTACT US
Any questions? Send us message now! We’ll serve your request with a whole team after receiving your message.