The Best Aerospace Additive Manufacturing in Hamburg: A Comprehensive Guide for B2B Buyers
Table of Contents
1. Introduction to Aerospace Additive Manufacturing in Hamburg
Hamburg is a key hub for aerospace manufacturing in Europe, home to leading companies such as Airbus and Lufthansa Technik. With the growing demand for lightweight, high-performance parts, additive manufacturing (AM) in aerospace has gained significant traction in the region.
Aerospace additive manufacturing involves 3D printing metal and polymer components to enhance aircraft performance, reduce material waste, and accelerate production timelines. This technology is widely used for engine components, structural parts, and intricate geometries that are difficult to manufacture using traditional methods.
Key Benefits of Aerospace 3D Printing
β
Weight Reduction β Optimized part designs reduce overall aircraft weight, improving fuel efficiency.
β
Cost Savings β Minimizes material waste and reduces production costs for complex components.
β
Shorter Lead Times β Rapid prototyping and on-demand production accelerate time-to-market.
β
Enhanced Performance β AM enables the creation of high-strength, intricate parts with superior durability.
As aerospace manufacturers in Hamburg increasingly adopt metal additive manufacturing, sourcing the right 3D printing suppliers and materials is crucial for success.
2. Market Trends and Growth Potential in Aerospace 3D Printing
The aerospace additive manufacturing market is experiencing rapid growth, driven by advancements in metal 3D printing technologies, high-performance materials, and automated production processes.
Key Market Trends
π Increased Adoption of Metal 3D Printing β Aerospace companies favor metal powders like titanium, aluminum, and superalloys for critical components.
π Sustainability Initiatives β Additive manufacturing reduces waste and supports greener production practices.
π Customization & On-Demand Production β Airlines and manufacturers leverage on-demand 3D printing for spare parts, reducing inventory costs.
π Regulatory Approvals & Certifications β Aerospace AM suppliers must meet strict industry standards like AS9100 and Nadcap certification.
Market Growth Statistics | Figures |
---|---|
Global Aerospace AM Market Size (2023) | $3.5 Billion |
Projected CAGR (2023-2030) | 19.8% |
Adoption Rate Among Aerospace OEMs | 85% |
Reduction in Lead Time via AM | 50-70% |
With Hamburgβs strong aerospace ecosystem, companies are investing in advanced additive manufacturing technologies to enhance production efficiency and competitiveness.
3. Key Factors to Consider When Choosing an Aerospace 3D Printing Supplier
Selecting the right aerospace additive manufacturing supplier in Hamburg requires careful evaluation of several critical factors:
1οΈβ£ Experience & Certifications
Ensure the supplier has aerospace industry experience and meets stringent certifications such as:
β AS9100 Certification β Quality management standard for aerospace manufacturers.
β Nadcap Accreditation β Ensures compliance with aerospace additive manufacturing processes.
β ISO 9001 Certification β Demonstrates quality control and consistency in production.
2οΈβ£ Material & Technology Capabilities
Evaluate the 3D printing technologies and metal powder materials the supplier offers:
- Laser Powder Bed Fusion (LPBF) β Ideal for high-precision metal components.
- Electron Beam Melting (EBM) β Suitable for high-strength aerospace parts.
- Direct Energy Deposition (DED) β Used for repair and refurbishment of aircraft components.
πΉ Common Aerospace 3D Printing Materials:
- Titanium Alloys (Ti6Al4V) β Lightweight and corrosion-resistant.
- Nickel-Based Superalloys (Inconel 718, 625) β High-temperature resistance.
- Aluminum Alloys (AlSi10Mg) β Excellent strength-to-weight ratio.
- Stainless Steel (316L, 17-4PH) β High durability and wear resistance.
3οΈβ£ Production Capabilities & Lead Times
β Can the supplier handle high-volume production?
β What are the lead times for prototyping vs. full-scale production?
β Do they offer on-demand production for spare parts?
4οΈβ£ Cost & Scalability
Compare pricing models based on:
π² Material Costs β Metal powders can vary in price depending on composition and purity.
π¦ Production Costs β Evaluate per-part pricing for small vs. large production runs.
π Scalability β Can the supplier scale production based on demand fluctuations?
By carefully considering these factors, aerospace manufacturers in Hamburg can select the best 3D printing partner to support their production needs.
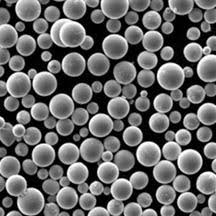
4. Top Aerospace Additive Manufacturing Companies in Hamburg
Hamburg is a major hub for aerospace innovation, home to leading additive manufacturing companies that specialize in metal 3D printing for aircraft and spacecraft components. Below are some of the top aerospace additive manufacturing providers in the region:
π Leading Aerospace 3D Printing Suppliers in Hamburg
Company Name | Key Capabilities | Certifications | Specialty |
---|---|---|---|
Airbus Additive Manufacturing | Metal & polymer 3D printing, prototyping, production | AS9100, Nadcap | Aircraft structural components |
Lufthansa Technik | Repair & maintenance via metal 3D printing | EASA, FAA, AS9100 | Spare parts & engine components |
Materialise | Aerospace-grade metal & polymer printing | ISO 9001, AS9100 | Lightweight aircraft parts |
FIT Additive Manufacturing Group | High-end metal 3D printing, complex geometries | AS9100, ISO 13485 | Aircraft & space applications |
Metal3DP | High-performance SEBM & LPBF metal 3D printing, advanced metal powders | ISO 9001, Industry-leading expertise | Titanium, superalloys, aerospace-grade materials |
Each of these suppliers brings unique strengths to aerospace additive manufacturing. However, Metal3DP stands out with its specialized focus on metal powders and high-precision 3D printing solutions that meet the rigorous demands of aerospace.
5. Why More Aerospace Manufacturers Are Adopting Additive Manufacturing
The adoption of metal 3D printing in aerospace is accelerating as manufacturers recognize its numerous advantages over traditional production methods.
π Key Reasons for Adoption
β Lightweight Design for Fuel Efficiency
- 3D printing enables the creation of hollow lattice structures and topology-optimized parts, significantly reducing weight.
- Lighter aircraft consume less fuel, improving operational efficiency and sustainability.
β Reduced Waste & Sustainability
- Traditional machining wastes up to 80% of raw material, whereas additive manufacturing uses only the necessary material.
- Closed-loop recycling systems allow manufacturers to reuse metal powder, reducing overall waste.
β Rapid Prototyping & Faster Production
- Traditional aerospace parts take months to produce due to complex supply chains.
- With additive manufacturing, production cycles are cut by 50-70%, enabling faster iteration and market readiness.
β On-Demand Spare Parts Production
- Airlines and MRO (Maintenance, Repair, Overhaul) providers can 3D print spare parts on demand, reducing inventory costs.
- This is particularly useful for rare, discontinued, or customized aircraft components.
β Superior Material Properties
- Metal 3D printing produces high-strength, corrosion-resistant components that outperform traditionally manufactured parts.
- Advanced alloys such as Ti6Al4V, Inconel 718, and CoCrMo are widely used in jet engines, landing gear, and structural components.
As the aerospace industry continues to evolve, companies that integrate additive manufacturing into their production workflows gain a competitive edge in cost, speed, and innovation.
6. Why Choose Metal3DP as Your Aerospace 3D Printing Partner?
When it comes to high-performance aerospace additive manufacturing, Metal3DP is a trusted partner for OEMs, Tier-1 suppliers, and research institutions.
πΉ What Sets Metal3DP Apart?
1οΈβ£ Industry-Leading Metal 3D Printing Technologies
- Selective Electron Beam Melting (SEBM) β Ideal for high-precision titanium and superalloy parts.
- Laser Powder Bed Fusion (LPBF) β Ensures tight tolerances and fine surface finishes for aerospace components.
2οΈβ£ High-Quality Metal Powders for Aerospace Applications
- Our company manufactures aerospace-grade metal powders using gas atomization and PREP technology.
- Available materials:
β Titanium Alloys (Ti6Al4V, TiAl, TiNbZr) β Used in airframes, engine parts, and landing gear.
β Superalloys (Inconel 718, CoCrMo, Ni-based alloys) β Ideal for high-temperature jet engine components.
β Stainless Steels (316L, 17-4PH) β Corrosion-resistant and durable for aircraft interiors and structural parts.
3οΈβ£ Certified & Reliable Aerospace Manufacturing
- ISO 9001-certified production facility ensures the highest quality standards.
- In-house powder characterization and quality control guarantee consistent particle size, flowability, and purity.
4οΈβ£ Expertise in Aerospace Applications
- Decades of experience in aerospace additive manufacturing.
- Close collaboration with leading aerospace firms to develop cutting-edge 3D-printed components.
π Explore Our Metal Powders & 3D Printing Solutions:
π Learn More About Metal3DPβs Metal 3D Printing Capabilities
By partnering with Metal3DP, aerospace manufacturers gain access to top-tier additive manufacturing expertise, high-performance materials, and cutting-edge printing technologies to enhance their production efficiency and competitiveness.
7. How to Source High-Quality Metal Powders for Aerospace 3D Printing
Sourcing high-quality metal powders is crucial for achieving precision, durability, and performance in aerospace additive manufacturing. The right metal powder ensures optimal printability, mechanical properties, and safety compliance. Hereβs how aerospace manufacturers can source the best materials for their 3D printing needs.
πΉ Key Factors to Consider When Choosing Metal Powders
Factor | Why It Matters |
---|---|
Particle Size Distribution (PSD) | Affects powder flowability and layer uniformity in AM processes. |
Powder Morphology (Shape and Surface Quality) | Spherical powders improve packing density and reduce defects. |
Purity and Contamination Levels | High-purity powders ensure stronger, defect-free components. |
Oxidation and Moisture Sensitivity | Oxidized powders can degrade mechanical properties. |
Printability & Compatibility | The powder must be optimized for LPBF, SEBM, or DED processes. |
πΉ Recommended Metal Powders for Aerospace 3D Printing
Material | Application in Aerospace |
---|---|
Titanium Alloys (Ti6Al4V, TiAl, TiNbZr) | Lightweight & corrosion-resistant β used in airframes, engine parts. |
Nickel-Based Superalloys (Inconel 718, Inconel 625) | High-temperature resistance β ideal for jet engine components. |
Cobalt-Chrome (CoCrMo) | High wear resistance β used in turbine blades, exhaust systems. |
Stainless Steels (316L, 17-4PH) | Strong & corrosion-resistant β used in aircraft interiors, structural parts. |
πΉ Why Choose Metal3DPβs Metal Powders?
β
Industry-Leading Purity & Quality β Manufactured using gas atomization and PREP technology for superior sphericity and flowability.
β
Aerospace-Grade Certifications β Compliant with ISO 9001 standards, ensuring high-performance, defect-free prints.
β
Optimized for Additive Manufacturing β Powders tailored for LPBF, SEBM, and DED processes.
π Explore Metal3DPβs Full Range of Metal Powders:
π View Our Metal Powder Products
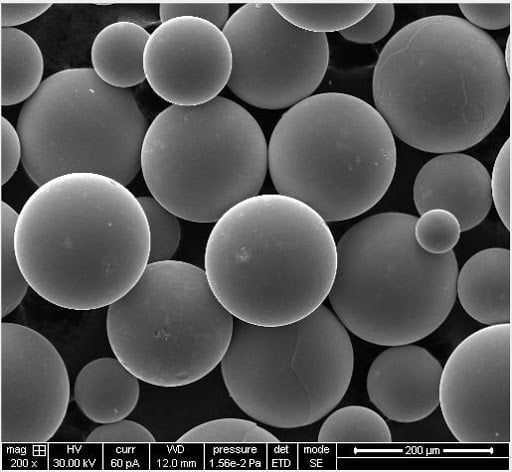
8. How to Order Aerospace 3D Printing Services in Hamburg
For aerospace manufacturers looking to integrate additive manufacturing into their production workflows, partnering with the right supplier is essential. Hereβs how to order aerospace 3D printing services with a streamlined process.
Step-by-Step Guide to Ordering Aerospace 3D Printing Services
Step 1: Define Your Requirements
π Determine the part specifications:
- Material type (e.g., Ti6Al4V, Inconel 718)
- Print technology (LPBF, SEBM, or DED)
- Tolerance requirements
- Mechanical performance needs
Step 2: Select a Trusted Supplier
- Choose Metal3DP for high-precision aerospace printing and advanced metal powders.
- Ensure supplier certifications (AS9100, ISO 9001) align with industry standards.
Step 3: Request a Quote & Feasibility Analysis
π© Provide a 3D CAD file (STEP/STL format) to Metal3DP for evaluation.
π Receive a technical feasibility assessment & cost estimate.
Step 4: Prototype & Testing Phase
π¬ Prototype production for functional testing and validation.
π Material characterization to ensure compliance with aerospace standards.
Step 5: Full-Scale Production & Delivery
π Batch production of aerospace components using high-precision 3D printing.
π¦ Quality inspection & certification before final delivery.
π Get Started with Aerospace Additive Manufacturing:
π Contact Metal3DP for Ordering
9. FAQs: Common Questions About Aerospace Additive Manufacturing
Q1: What are the main advantages of additive manufacturing in aerospace?
Aerospace 3D printing provides:
β Weight reduction for improved fuel efficiency
β Cost savings by minimizing material waste
β Rapid prototyping for faster product development
β On-demand spare parts production
Q2: Which metal powders are best for aerospace 3D printing?
πΉ Titanium alloys (Ti6Al4V, TiAl, TiNbZr) β Lightweight, high strength
πΉ Nickel-based superalloys (Inconel 718, 625) β Heat-resistant, durable
πΉ Cobalt-chrome (CoCrMo) β High wear resistance for turbine blades
Q3: How does Metal3DP ensure metal powder quality?
β
Gas atomization & PREP production ensures high sphericity, minimal impurities
β
ISO-certified quality control for consistent particle size and flowability
Q4: How long does it take to produce aerospace 3D printed parts?
β³ Lead times vary based on complexity and production volume:
- Prototypes: 1-2 weeks
- Full production: 4-8 weeks
Q5: How can I request a custom aerospace 3D printing project?
π© Submit your CAD file & material requirements to Metal3DP.
π Receive a customized production plan & pricing estimate.
π Learn More About Metal3DPβs Aerospace 3D Printing Solutions:
π Explore Our Metal 3D Printing Capabilities
Final Thoughts & Next Steps
Aerospace additive manufacturing is revolutionizing the industry, offering lighter, stronger, and more efficient parts for modern aircraft. With Hamburgβs growing 3D printing ecosystem, manufacturers can leverage high-performance metal powders and advanced printing technologies to gain a competitive edge.
π Why Choose Metal3DP?
β
Industry-leading aerospace 3D printing solutions
β
High-purity, aerospace-grade metal powders
β
Precision manufacturing for mission-critical components
π Get Started with Metal3DP Today:
π Contact Us for Aerospace 3D Printing Services
By following this guide, aerospace manufacturers in Hamburg can successfully integrate additive manufacturing into their supply chain, ensuring high-quality, cost-effective production of critical aircraft components.
Share On
MET3DP Technology Co., LTD is a leading provider of additive manufacturing solutions headquartered in Qingdao, China. Our company specializes in 3D printing equipment and high-performance metal powders for industrial applications.
Inquiry to get best price and customized Solution for your business!
Related Articles
About Met3DP
Recent Update
Our Product
CONTACT US
Any questions? Send us message now! Weβll serve your request with a whole team after receiving your message.Β
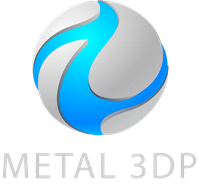
Metal Powders for 3D Printing and Additive Manufacturing