Comprehensive Guide of AM machines
Table of Contents
Overview of Additive Manufacturing (AM) Machines
Additive Manufacturing (AM), commonly known as 3D printing, is revolutionizing the manufacturing industry. By adding material layer by layer, AM machines can create complex geometries that were previously impossible or highly expensive to produce with traditional manufacturing methods. In this article, we’ll dive deep into the world of AM machines, focusing on metal powder models, their applications, specifications, pros and cons, and more. So, let’s get started on this exciting journey!
What are AM Machines?
Additive Manufacturing (AM) machines are devices that create three-dimensional objects from a digital file by laying down successive layers of material. The materials used can range from plastics and ceramics to metals and composites. The process is controlled by a computer, which ensures high precision and repeatability.
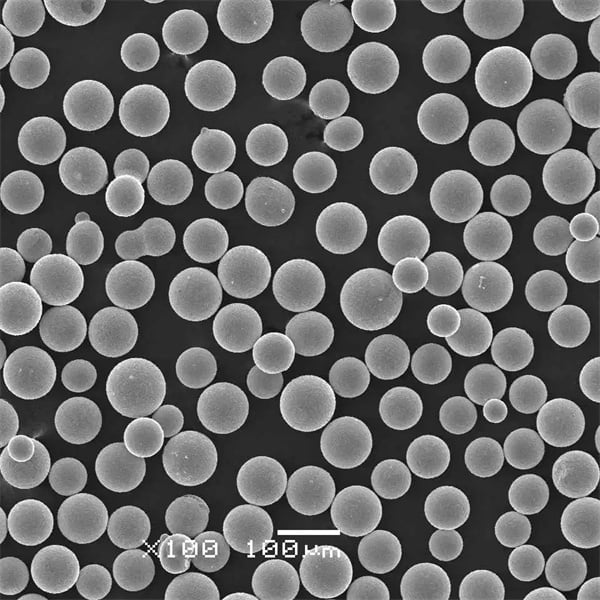
Types of AM Machines
There are various types of AM machines, each with its own unique process and suitable materials. Here’s a quick overview:
Type | Process | Materials | Applications |
---|---|---|---|
Stereolithography (SLA) | Uses UV laser to cure liquid resin | Photopolymers | Prototypes, dental models |
Selective Laser Sintering (SLS) | Uses laser to sinter powdered material | Nylon, metals, ceramics | Functional prototypes, end-use parts |
Fused Deposition Modeling (FDM) | Melts and extrudes thermoplastic filament | ABS, PLA, PETG | Prototypes, jigs, fixtures |
Direct Metal Laser Sintering (DMLS) | Uses laser to sinter metal powder | Stainless steel, titanium | Aerospace, medical implants |
Electron Beam Melting (EBM) | Uses electron beam to melt metal powder | Titanium, cobalt-chrome | Aerospace, medical implants |
Specific Metal Powder Models
When it comes to metal powders for AM machines, selecting the right model is crucial for achieving the desired properties and performance. Here are ten popular metal powder models used in AM machines:
- 316L Stainless Steel
- Description: Highly corrosion-resistant steel.
- Applications: Medical devices, marine components, chemical processing equipment.
- 17-4 PH Stainless Steel
- Description: Precipitation-hardening martensitic stainless steel.
- Applications: Aerospace components, nuclear reactor parts, surgical instruments.
- AlSi10Mg Aluminum Alloy
- Description: Lightweight alloy with good thermal properties.
- Applications: Automotive parts, aerospace components, heat exchangers.
- Ti6Al4V Titanium Alloy
- Description: High-strength, lightweight alloy.
- Applications: Aerospace, medical implants, high-performance sports equipment.
- Inconel 625
- Description: Nickel-based superalloy with excellent oxidation resistance.
- Applications: Jet engines, gas turbines, chemical processing equipment.
- Inconel 718
- Description: Nickel-chromium alloy known for its high tensile strength.
- Applications: Aerospace engines, power generation, oil and gas.
- Maraging Steel (MS1)
- Description: High-strength, low-carbon martensitic steel.
- Applications: Tooling, aerospace components, high-performance parts.
- CoCr (Cobalt-Chrome) Alloy
- Description: Highly wear-resistant and biocompatible alloy.
- Applications: Dental implants, orthopedic implants, aerospace components.
- Copper (Cu)
- Description: Excellent thermal and electrical conductivity.
- Applications: Electrical components, heat exchangers, inductors.
- H13 Tool Steel
- Description: High toughness and wear resistance.
- Applications: Injection molds, die-casting tools, high-temperature applications.
Applications of AM Machines
AM machines are used across various industries due to their versatility and precision. Here are some of the key applications:
Industry | Applications |
---|---|
Aerospace | Lightweight structural components, engine parts |
Medical | Custom implants, prosthetics, surgical instruments |
Automotive | Prototyping, end-use parts, tooling |
Consumer Goods | Customized products, prototypes |
Construction | Architectural models, components |
Energy | Turbine blades, heat exchangers |
Specifications, Sizes, Grades, and Standards
Understanding the specifications, sizes, grades, and standards of metal powders used in AM machines is crucial for ensuring quality and performance. Here’s a detailed table:
Metal Powder | Particle Size (µm) | Grade | Standard |
---|---|---|---|
316L Stainless Steel | 15-45 | AISI 316L | ASTM A240 |
17-4 PH Stainless Steel | 10-50 | AISI 630 | ASTM A564 |
AlSi10Mg Aluminum Alloy | 20-63 | AlSi10Mg | ASTM F3318 |
Ti6Al4V Titanium Alloy | 15-45 | Grade 5 | ASTM F2924 |
Inconel 625 | 15-53 | UNS N06625 | ASTM B446 |
Inconel 718 | 15-45 | UNS N07718 | ASTM B637 |
Maraging Steel (MS1) | 10-45 | 18Ni(300) | ASTM A538 |
CoCr (Cobalt-Chrome) Alloy | 10-45 | CoCrMo | ASTM F75 |
Copper (Cu) | 15-45 | C11000 | ASTM B152 |
H13 Tool Steel | 15-53 | H13 | ASTM A681 |
Suppliers and Pricing Details
When sourcing metal powders for AM machines, it’s essential to compare suppliers and pricing to ensure the best value. Here’s a comparative table:
Supplier | Metal Powder | Price (per kg) | Location |
---|---|---|---|
LPW Technology | 316L Stainless Steel | $150 | UK |
Carpenter Technology | 17-4 PH Stainless Steel | $200 | USA |
AP&C (GE Additive) | AlSi10Mg Aluminum Alloy | $120 | Canada |
Arcam AB | Ti6Al4V Titanium Alloy | $450 | Sweden |
Höganäs AB | Inconel 625 | $300 | Sweden |
Sandvik | Inconel 718 | $320 | Sweden |
Höganäs AB | Maraging Steel (MS1) | $250 | Sweden |
HC Starck | CoCr (Cobalt-Chrome) Alloy | $400 | Germany |
Valimet | Copper (Cu) | $100 | USA |
Sandvik | H13 Tool Steel | $220 | Sweden |
Advantages of AM Machines
Additive Manufacturing comes with a plethora of advantages that make it a preferred choice for many industries. Here’s why:
- Design Flexibility: AM allows for the creation of complex geometries that are not possible with traditional manufacturing methods. You can design intricate internal structures, custom parts, and even consolidated components that reduce the need for assembly.
- Material Efficiency: Unlike subtractive manufacturing, which removes material to create parts, AM only uses the material necessary to build the part, leading to less waste and cost savings.
- Rapid Prototyping: AM significantly reduces the time needed to produce prototypes, enabling faster iteration and development cycles. This rapid prototyping capability is invaluable for innovation and product development.
- Customization: AM enables mass customization, where each part can be tailored to specific requirements without additional tooling or setup costs. This is particularly beneficial in the medical and dental industries for patient-specific implants and prosthetics.
- Reduced Lead Times: By eliminating the need for molds and tooling, AM can drastically reduce lead times, allowing for quicker turnaround from design to production.
Disadvantages of AM Machines
While AM machines offer numerous benefits, they also come with some limitations. It’s important to consider these drawbacks when deciding whether AM is the right solution for your needs:
- High Initial Costs: The initial investment in AM machines and materials can be high. Although costs have been decreasing, they are still significant compared to traditional manufacturing methods.
- Limited Material Availability: Not all materials can be used in AM processes. While the range of available materials is expanding, it is still more limited than traditional manufacturing.
- Surface Finish and Post-Processing: Parts produced by AM often require post-processing to achieve the desired surface finish and mechanical properties. This can add time and cost to the overall production process.
- Build Size Constraints: AM machines have build size limitations, which can be a constraint for producing larger parts. While there are large-format AM machines available, they are less common and more expensive.
- Anisotropic Properties: Parts produced by AM can have anisotropic mechanical properties, meaning their strength and other properties can vary depending on the direction of the build layers. This can impact the performance of the part in certain applications.
Comparing AM Machines: Pros and Cons
To make an informed decision about which AM machine to use, it’s helpful to compare their pros and cons. Here’s a comparative table:
Type of AM Machine | Pros | Cons |
---|---|---|
Stereolithography (SLA) | High precision, smooth surface finish | Limited material choices, post-processing needed |
Selective Laser Sintering (SLS) | No support structures, versatile materials | Rough surface finish, powder handling issues |
Fused Deposition Modeling (FDM) | Low cost, easy to use | Lower resolution, visible layer lines |
Direct Metal Laser Sintering (DMLS) | Strong, complex metal parts | High cost, post-processing required |
Electron Beam Melting (EBM) | Excellent material properties, faster build times | High cost, limited material choices |
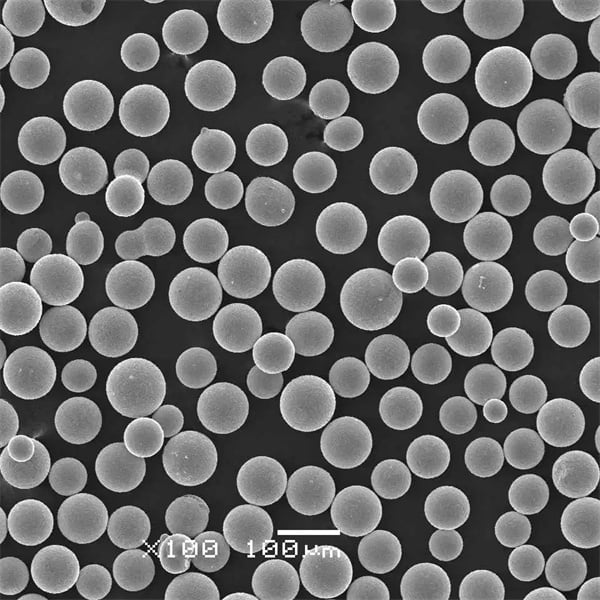
FAQ
Let’s address some common questions about AM machines to help you better understand their capabilities and applications.
Question | Answer |
---|---|
What is the difference between AM and 3D printing? | Additive Manufacturing (AM) is a broader term that encompasses various technologies, including 3D printing. 3D printing specifically refers to the layer-by-layer construction of objects. |
How does AM benefit the aerospace industry? | AM allows for the production of lightweight, complex parts with high strength, which is crucial for aerospace applications. It also reduces material waste and lead times. |
Can AM machines use multiple materials in a single build? | Some advanced AM machines can use multiple materials in a single build, enabling the creation of parts with varying properties. |
What are the environmental benefits of AM? | AM generates less waste compared to traditional manufacturing, and it allows for on-demand production, reducing the need for excess inventory. |
Is AM suitable for mass production? | AM is typically more suited for low to medium volume production, prototyping, and custom parts. However, advancements are being made to make AM viable for mass production. |
What are the common post-processing steps for AM parts? | Common post-processing steps include removing support structures, surface finishing, heat treatment, and machining to achieve the desired properties and appearance. |
How accurate are AM machines? | The accuracy of AM machines varies depending on the technology and machine. Some AM machines can achieve tolerances within microns, making them suitable for precision applications. |
Conclusion
Additive Manufacturing is a game-changer in the manufacturing industry, offering unparalleled design freedom, material efficiency, and customization capabilities. By understanding the different types of AM machines, the specific metal powders used, and their applications, you can harness the full potential of this innovative technology. Whether you’re looking to produce lightweight aerospace components, custom medical implants, or functional prototypes, AM machines provide a versatile and efficient solution.
In this comprehensive guide, we’ve explored the intricacies of AM machines, from specific metal powder models to their advantages and disadvantages. With this knowledge, you’re well-equipped to make informed decisions and take your manufacturing capabilities to the next level.
Share On
MET3DP Technology Co., LTD is a leading provider of additive manufacturing solutions headquartered in Qingdao, China. Our company specializes in 3D printing equipment and high-performance metal powders for industrial applications.
Inquiry to get best price and customized Solution for your business!
Related Articles
About Met3DP
Recent Update
Our Product
CONTACT US
Any questions? Send us message now! We’ll serve your request with a whole team after receiving your message.
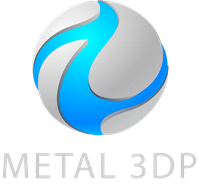
Metal Powders for 3D Printing and Additive Manufacturing