Comprehensive Guide of AM process
Table of Contents
Welcome to the fascinating world of AM process, where the boundaries of traditional manufacturing are constantly being pushed. In this guide, we’ll dive deep into the intricacies of AM, shedding light on various aspects from metal powder models to their applications, advantages, disadvantages, and more. Buckle up for an engaging and informative journey through the modern marvels of manufacturing!
Overview of Additive Manufacturing
Additive Manufacturing, often referred to as 3D printing, is a process of creating three-dimensional objects by adding material layer by layer. Unlike traditional manufacturing methods, which often involve subtracting material from a larger block, AM builds objects from the ground up, allowing for complex designs and reduced waste.
Key Details of the AM Process
- Technology: Layer-by-layer material addition
- Materials Used: Metals, polymers, ceramics, and composites
- Applications: Aerospace, automotive, healthcare, consumer goods, and more
- Advantages: Complex geometries, reduced waste, customization, and rapid prototyping
- Challenges: Material limitations, surface finish, and high initial costs
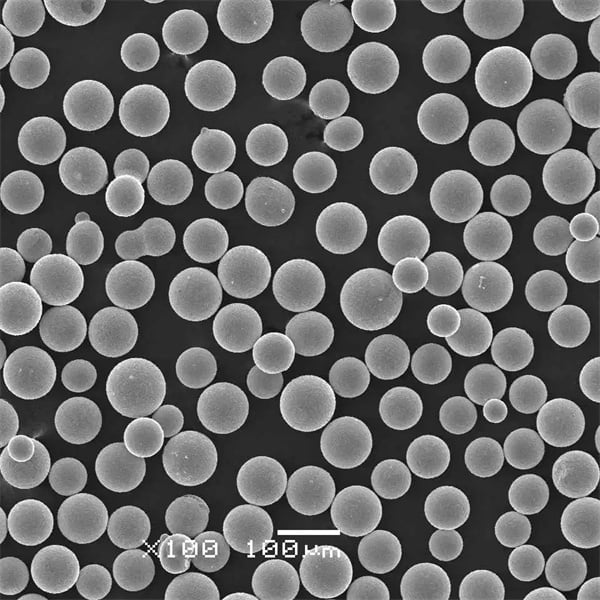
Types of Metal Powders Used in AM
In the realm of AM, metal powders are a critical component. Let’s explore some of the most commonly used metal powders, their compositions, and their unique properties.
Common Metal Powders for AM
Metal Powder | Composition | Properties | Applications |
---|---|---|---|
Titanium (Ti-6Al-4V) | 90% Titanium, 6% Aluminum, 4% Vanadium | High strength, lightweight, corrosion-resistant | Aerospace, medical implants |
Stainless Steel (316L) | 16-18% Chromium, 10-14% Nickel, 2-3% Molybdenum | Corrosion-resistant, durable, good weldability | Medical instruments, food processing |
Aluminum (AlSi10Mg) | 89-91% Aluminum, 9-11% Silicon, 0.2-0.4% Magnesium | Lightweight, good thermal conductivity, strong | Automotive, aerospace |
Inconel (IN718) | 50-55% Nickel, 17-21% Chromium, 4.75-5.5% Niobium | Heat-resistant, high strength at elevated temperatures | Turbines, aerospace components |
Cobalt-Chrome (CoCr) | 55-65% Cobalt, 27-30% Chromium, 5-7% Molybdenum | Wear-resistant, biocompatible, high hardness | Dental implants, orthopedic devices |
Copper (Cu) | 99.9% Copper | Excellent thermal and electrical conductivity | Electrical components, heat exchangers |
Tool Steel (H13) | 0.35-0.45% Carbon, 5-5.5% Chromium, 1-1.2% Molybdenum | High hardness, wear-resistant, good machinability | Molds, dies, cutting tools |
Nickel Alloy (Hastelloy X) | 47-52% Nickel, 20.5-23% Chromium, 17-20% Iron | Oxidation-resistant, high strength at high temperatures | Chemical processing, aerospace |
Magnesium (AZ91D) | 8.5-9.5% Aluminum, 0.6-1.4% Zinc, 0.15% Manganese | Lightweight, good strength-to-weight ratio | Automotive, electronics |
Tungsten (W) | 99.95% Tungsten | Extremely high melting point, dense, strong | Aerospace, defense applications |
Detailed Metal Powder Models
- Titanium (Ti-6Al-4V): Known for its exceptional strength-to-weight ratio and biocompatibility, this alloy is a staple in aerospace and medical industries. It offers impressive resistance to fatigue and corrosion, making it ideal for critical components.
- Stainless Steel (316L): A versatile alloy, 316L stainless steel is prized for its durability and resistance to corrosion. It’s widely used in environments where hygiene and longevity are paramount, such as in medical devices and food processing equipment.
- Aluminum (AlSi10Mg): This alloy is known for its lightweight nature and excellent thermal conductivity. It’s a popular choice in automotive and aerospace sectors where weight reduction is crucial without compromising strength.
- Inconel (IN718): Renowned for its ability to withstand extreme temperatures and mechanical stress, Inconel 718 is extensively used in the aerospace industry for turbine engines and other high-temperature applications.
- Cobalt-Chrome (CoCr): This biocompatible alloy is perfect for medical implants due to its high hardness and wear resistance. It ensures longevity and reliability in orthopedic and dental applications.
- Copper (Cu): With unmatched thermal and electrical conductivity, copper is essential in electrical engineering and heat exchanger applications, where efficient heat transfer is crucial.
- Tool Steel (H13): Ideal for making molds and cutting tools, H13 tool steel offers high hardness and wear resistance, ensuring durability and precision in manufacturing processes.
- Nickel Alloy (Hastelloy X): This alloy excels in high-temperature environments, resisting oxidation and maintaining strength. It’s used in chemical processing and aerospace applications where reliability under extreme conditions is essential.
- Magnesium (AZ91D): As one of the lightest structural metals, magnesium AZ91D is used where weight saving is critical, such as in automotive and electronics industries, providing a good balance of strength and lightness.
- Tungsten (W): Known for its incredibly high melting point and density, tungsten is indispensable in aerospace and defense applications, particularly where exposure to extreme conditions is expected.
Applications of the AM Process
The versatility of AM is reflected in its wide range of applications. Here, we delve into various industries leveraging AM to push the boundaries of innovation.
Industries Utilizing AM
Industry | Applications | Benefits |
---|---|---|
Aerospace | Engine components, structural parts, tooling | Lightweight parts, reduced lead times, complex geometries |
Automotive | Prototypes, custom parts, lightweight components | Design flexibility, rapid prototyping, reduced weight |
Healthcare | Implants, prosthetics, surgical instruments | Customization, biocompatibility, precise geometries |
Consumer Goods | Customized products, wearable technology, home appliances | Personalization, on-demand production, reduced inventory |
Architecture | Scale models, bespoke components, construction tools | Custom designs, rapid production, reduced material waste |
Education | Teaching aids, prototype development, research | Hands-on learning, innovative designs, cost-effective prototyping |
Defense | Lightweight armor, weapon components, field repair tools | Durability, customization, rapid manufacturing |
Energy | Turbine components, heat exchangers, pipelines | High performance, material efficiency, complex designs |
Advantages of AM Process
- Design Flexibility: AM allows for the creation of complex and intricate designs that would be impossible or costly with traditional methods.
- Customization: Products can be tailored to individual needs, making it ideal for medical implants and custom-fit parts.
- Reduced Waste: Material is added layer by layer, minimizing waste compared to subtractive manufacturing processes.
- Rapid Prototyping: AM enables quick iteration and testing of designs, speeding up the development cycle.
- Lightweight Structures: AM can produce lightweight components, crucial in aerospace and automotive industries.
Disadvantages of AM Process
- Material Limitations: Not all materials are suitable for AM, limiting the range of possible applications.
- Surface Finish: Parts produced by AM often require post-processing to achieve the desired surface quality.
- Initial Costs: The initial investment in AM technology and materials can be high, making it less accessible for small-scale operations.
- Production Speed: While AM excels in complexity and customization, it can be slower than traditional mass production methods for large quantities.
Comparing AM Metal Powders
Let’s take a closer look at how these metal powders stack up against each other across various parameters.
Metal Powder | Strength | Weight | Corrosion Resistance | Heat Resistance | Cost |
---|---|---|---|---|---|
Titanium (Ti-6Al-4V) | High | Light | Excellent | Good | High |
Stainless Steel (316L) | Moderate | Heavy | Excellent | Moderate | Moderate |
Aluminum (AlSi10Mg) | Moderate | Very Light | Good | Moderate | Low |
Inconel (IN718) | Very High | Heavy | Good | Excellent | Very High |
Cobalt-Chrome (CoCr) | High | Heavy | Excellent | Good | High |
Copper (Cu) | Low | Heavy | Poor | Poor | Low |
Tool Steel (H13) | High | Heavy | Moderate | Moderate | Moderate |
Nickel Alloy (Hastelloy X) | High | Heavy | Good | Excellent | Very High |
Magnesium (AZ91D) | Low | Very Light | Poor | Poor | Low |
Tungsten (W) | Very High | Very Heavy | Excellent | Excellent | Very High |
Suppliers and Pricing Details
When it comes to sourcing metal powders for AM, it’s essential to know the leading suppliers and their pricing. Here’s a breakdown:
Supplier | Metal Powder | Price (per kg) | Contact Details |
---|---|---|---|
Höganäs AB | Titanium (Ti-6Al-4V) | $300 | www.hoganas.com |
Sandvik | Stainless Steel (316L) | $150 | www.materials.sandvik |
EOS GmbH | Aluminum (AlSi10Mg) | $100 | www.eos.info |
Carpenter Technology | Inconel (IN718) | $400 | www.carpentertechnology.com |
Arcam AB | Cobalt-Chrome (CoCr) | $350 | www.arcam.com |
GKN Hoeganaes | Copper (Cu) | $50 | www.gknpm.com |
Böhler Uddeholm | Tool Steel (H13) | $120 | www.bohler-uddeholm.com |
Haynes International | Nickel Alloy (Hastelloy X) | $450 | www.haynesintl.com |
Advanced Powders & Coatings (AP&C) | Magnesium (AZ91D) | $80 | www.advancedpowders.com |
Buffalo Tungsten Inc. | Tungsten (W) | $500 | www.buffalotungsten.com |
Pros and Cons of AM Process
Every technology has its strengths and weaknesses. Here’s a detailed comparison of the pros and cons of the AM process:
Aspect | Advantages | Limitations |
---|---|---|
Design | Allows for complex geometries, Customization | Limited by material properties |
Material Usage | Reduced waste, Efficient use | Limited range of usable materials |
Production | Rapid prototyping, On-demand production | Slower for large quantities |
Cost | Reduced tooling costs, Less material waste | High initial investment |
Flexibility | Easy design modifications, Versatile applications | Post-processing often required |
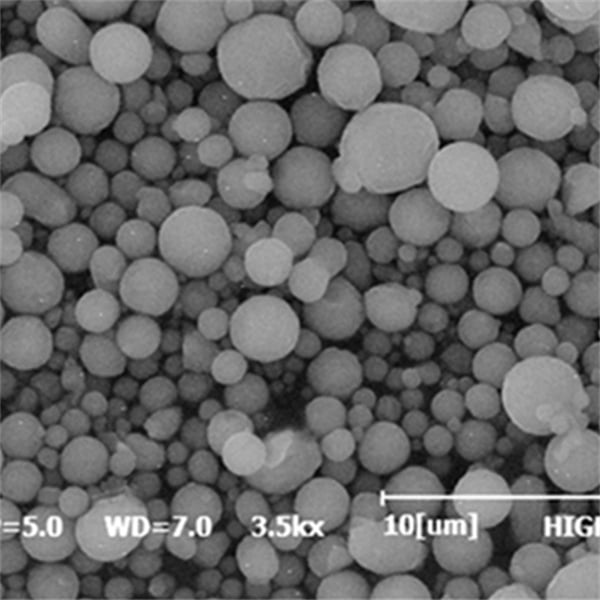
FAQ
Let’s address some common questions about the AM process to clear up any lingering doubts.
Question | Answer |
---|---|
What is Additive Manufacturing (AM)? | AM, or 3D printing, is a process of creating objects by adding material layer by layer, allowing for complex designs and reduced waste. |
What materials can be used in AM? | A variety of materials can be used, including metals, polymers, ceramics, and composites. |
What are the main advantages of AM? | AM offers design flexibility, customization, reduced waste, rapid prototyping, and the ability to create lightweight structures. |
Are there any limitations to AM? | Yes, limitations include material restrictions, surface finish issues, high initial costs, and slower production speeds for large quantities. |
Which industries benefit the most from AM? | Aerospace, automotive, healthcare, consumer goods, architecture, education, defense, and energy industries benefit significantly from AM. |
How does AM compare to traditional manufacturing? | AM excels in creating complex, customized parts with less waste but can be slower and more expensive initially compared to traditional mass production methods. |
What are some common metal powders used in AM? | Common metal powders include Titanium (Ti-6Al-4V), Stainless Steel (316L), Aluminum (AlSi10Mg), Inconel (IN718), Cobalt-Chrome (CoCr), and more. |
Can AM be used for mass production? | While AM is ideal for prototyping and custom parts, it is generally slower and less cost-effective for mass production compared to traditional methods. |
What post-processing is required for AM parts? | Post-processing can include surface finishing, heat treatment, machining, and coating to achieve the desired quality and properties. |
How does the cost of AM materials compare to traditional materials? | AM materials can be more expensive due to their specialized nature, but cost savings can be realized through reduced waste and tooling costs. |
Conclusion
Additive Manufacturing is revolutionizing how we approach design and production, offering unparalleled flexibility and efficiency. From aerospace to healthcare, the applications of AM are vast and varied. While there are challenges to overcome, the benefits of this innovative technology are clear. As the field continues to evolve, we can expect even more exciting developments and broader adoption across industries.
Share On
MET3DP Technology Co., LTD is a leading provider of additive manufacturing solutions headquartered in Qingdao, China. Our company specializes in 3D printing equipment and high-performance metal powders for industrial applications.
Inquiry to get best price and customized Solution for your business!
Related Articles
About Met3DP
Recent Update
Our Product
CONTACT US
Any questions? Send us message now! We’ll serve your request with a whole team after receiving your message.
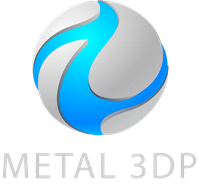
Metal Powders for 3D Printing and Additive Manufacturing
COMPANY
PRODUCT
cONTACT INFO
- Qingdao City, Shandong, China
- [email protected]
- [email protected]
- +86 19116340731