introduction of Atomization
Table of Contents
Imagine a world where everything existed in giant, unusable chunks. Cars wouldn’t fit in garages, paint wouldn’ Metal components would be cumbersome and impractical. Thankfully, we have a process called atomization that breaks down materials into tiny particles, unlocking a vast array of applications. But what exactly is atomization, and how does it work? Buckle up, because we’re diving deep into the fascinating world of transforming bulk materials into microscopic marvels.
Process Principle of Atomization
At its core, atomization is the process of breaking down a bulk liquid or solid material into much finer droplets or particles. Think of it like taking a giant chocolate bar and pulverizing it into cocoa powder. This transformation happens through various techniques, each with its own advantages and applications. Here are some of the most common methods:
- Pressure atomization: Imagine a garden hose on steroids. In pressure atomization, liquid is forced through a tiny nozzle at high pressure. The sheer force breaks the liquid into a fine mist.
- Two-fluid atomization: This method introduces a gas (usually air) alongside the liquid. The high-velocity gas shears the liquid into smaller droplets as it exits the nozzle.
- Rotary atomization: Picture a high-speed blender. Rotary atomization uses a rapidly spinning disc to break up the liquid as it flows across its surface.
- Ultrasonic atomization: This method employs high-frequency sound waves to create microscopic vibrations within the liquid, causing it to fragment into tiny droplets.
The choice of atomization technique depends on the desired particle size, material properties, and the final application.
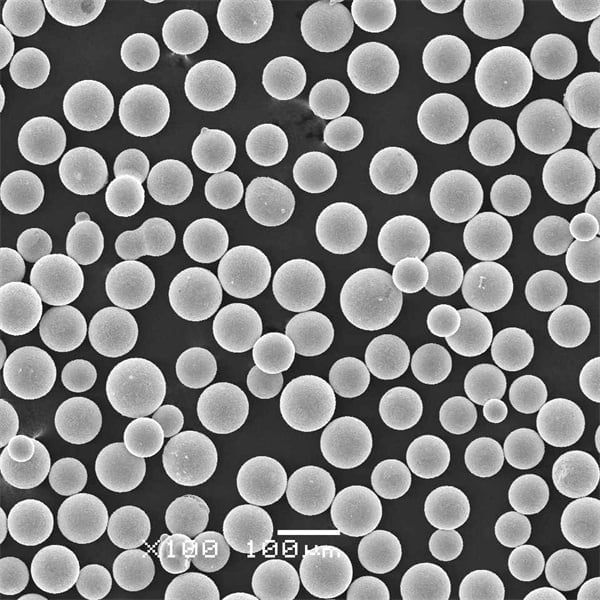
Process Characteristics of Atomization
The magic of atomization lies in the unique characteristics it imparts to materials. Here’s a closer look at some key benefits:
- Increased surface area: When a material is broken down into tiny particles, its surface area dramatically increases. Imagine a crumpled piece of paper versus a flat sheet. The crumpled paper has more surface area exposed, right? The same principle applies to atomization. This increased surface area makes the material more reactive and efficient in various applications.
- Improved control: Imagine trying to paint a detailed picture with a giant paintbrush versus a fine-tipped one. Atomization allows for much finer control over the application of materials. For example, in 3D printing, metal powders are precisely deposited layer by layer using atomization techniques.
- Enhanced properties: Atomization can sometimes alter the properties of materials. For instance, some atomized metal powders exhibit improved strength and ductility compared to their bulk counterparts.
However, atomization also comes with some limitations to consider:
- Energy consumption: The process of breaking down materials can be energy-intensive, depending on the chosen technique.
- Particle size control: Achieving a uniform and consistent particle size can be challenging, especially for some materials.
- Material limitations: Not all materials are easily atomized. Some materials may be too viscous or prone to clumping during the process.
Metal Powders: The Building Blocks of Tomorrow
One of the most exciting applications of atomization lies in the creation of metal powders. These tiny metallic particles, ranging in size from a few micrometers to hundreds of micrometers, are revolutionizing various industries, particularly additive manufacturing (3D printing). Here’s a closer look at some of the most popular metal powders used in 3D printing:
Type | Composition | Properties | Applications |
---|---|---|---|
Stainless Steel 316L | Fe (Iron), Cr (Chromium), Ni (Nickel), Mo (Molybdenum) | Excellent corrosion resistance, high strength, biocompatible | Medical implants, aerospace components, chemical processing equipment |
Titanium 6Al-4V (Grade 23) | Ti (Titanium), Al (Aluminum), V (Vanadium) | High strength-to-weight ratio, good biocompatibility, excellent corrosion resistance | Aerospace components, biomedical implants, sporting goods |
Inconel 625 | Ni (Nickel), Cr (Chromium), Mo (Molybdenum), Fe (Iron) | Exceptional high-temperature performance, outstanding oxidation resistance | Turbine blades, heat exchangers, chemical processing equipment |
Aluminum AlSi10Mg | Al (Aluminum), Si (Silicon), Mg (Magnesium) | Good weldability, high strength-to-weight ratio, excellent corrosion resistance | Automotive parts, aerospace components, consumer electronics |
Copper | Cu (Copper) | High thermal and electrical conductivity | Heat exchangers, electrical components, electrodes |
Nickel | Ni (Nickel) | Excellent corrosion resistance, good ductility | Chemical processing equipment, electronics, battery components |
Maraging Steel | Fe (Iron), Ni (Nickel), Mo (Molybdenum), Ti (Titanium), Al (Aluminum) | High strength, excellent toughness, good dimensional stability | Aerospace components, tooling, molds and dies |
Tool Steel | Fe (Iron), C (Carbon), Cr (Chromium), V (Vanadium), Mo (Molybdenum) | Excellent wear resistance, high hardness | Tools and dies, punches, cutting blades |
Inconel 718 | Ni (Nickel), Cr (Chromium), Fe (Iron), Nb (Niobium), Mo (Molybdenum) | High strength at elevated temperatures, good creep resistance | Turbine blades, rocket engine components, heat exchangers |
Nickel Aluminum Bronze (NAB) | Cu (Copper), Ni (Nickel), Al (Aluminum), Fe (Iron) | High strength, excellent corrosion resistance, good wear resistance | Marine components, gears, bearings |
Tungsten | W (Tungsten) | Very high melting point, excellent wear resistance | Electrodes, filaments for additive manufacturing, heating elements |
Choosing the Right Metal Powder
Selecting the ideal metal powder for your 3D printing project depends on several crucial factors:
- Desired properties: Consider the mechanical properties (strength, ductility, wear resistance), corrosion resistance, thermal conductivity, and biocompatibility (if applicable) needed for the final part.
- Application: The intended use of the 3D printed part will heavily influence the choice of metal powder. For instance, aerospace components require high strength-to-weight ratio materials like titanium, while heat exchangers might benefit from the high thermal conductivity of copper.
- Printer compatibility: Different 3D printers have varying capabilities regarding the types of metal powders they can handle. Ensure the chosen powder is compatible with your specific printer’s laser or electron beam melting technology.
- Cost: Metal powders can vary significantly in price. Factors like material rarity, processing complexity, and demand all play a role.
Beyond 3D Printing: A Universe of Applications
While 3D printing is a major driver for metal powder development, these versatile materials have applications far beyond additive manufacturing. Here are a few examples:
- Metal Injection Molding (MIM): This process utilizes metal powders mixed with a binder to create complex shapes through injection molding. The binder is then removed through a thermal debinding process, leaving behind a near-net-shape metal part. MIM is ideal for producing high-volume, intricate metal components.
- Thermal Spraying: Metal powders are used in thermal spraying techniques to coat surfaces with specific properties. For instance, thermal spraying can be used to apply a wear-resistant layer of tungsten carbide on cutting tools or a corrosion-resistant layer of nickel on a steel pipe.
- Cladding: Metal powders can be used in cladding processes to create a composite material with a core and a bonded outer layer of a different metal. This technique allows for combining the strengths of different materials in a single component.
The Future of Metal Powders: Brighter Than Ever
The field of metal powder development is constantly evolving, with researchers pushing the boundaries of particle size, shape, and composition. Here are some exciting trends shaping the future of metal powders:
- Nanoparticles: Metal nanoparticles offer unique properties like enhanced strength and improved reactivity. Researchers are exploring the use of metal nanoparticles in various applications, including catalysts and composite materials.
- Custom Alloys: The ability to tailor metal powder compositions to achieve specific properties is becoming increasingly feasible. This opens doors for the development of novel alloys with properties optimized for specific applications.
- Recycled Powders: Sustainability is a growing concern, and the development of efficient methods for recycling metal powders from scrap materials is gaining traction. This will not only reduce environmental impact but also make metal powders more cost-effective.
Metal powders are revolutionizing the way we design and manufacture products. With their versatility, unique properties, and ever-expanding application range, metal powders are poised to play a pivotal role in shaping the future of manufacturing.
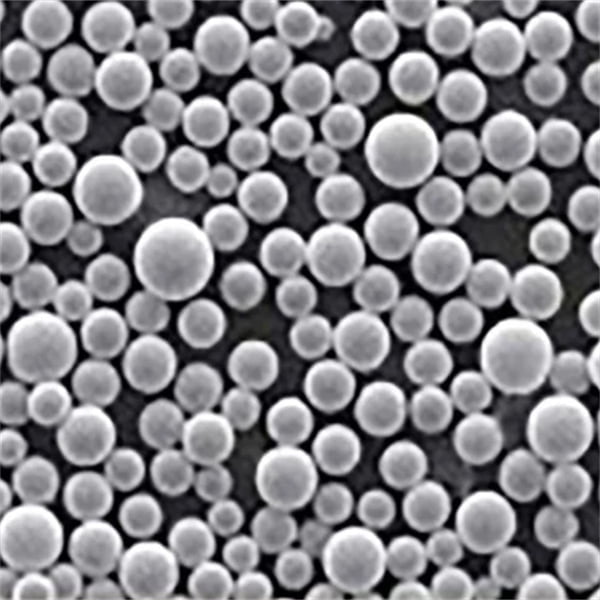
FAQ
Question | Answer |
---|---|
What is metal atomization? | Metal atomization is the process of breaking down bulk metal into fine particles (powders) using various techniques like pressure atomization, two-fluid atomization, and rotary atomization. |
What are the advantages of using metal powders? | Metal powders offer several advantages, including increased surface area, improved control over material application, enhanced properties, and the ability to create complex shapes through additive manufacturing and other techniques. |
What are some of the limitations of metal powders? | Metal powders also come with some limitations, such as high energy consumption during the atomization process, challenges in achieving perfectly uniform particle size, and limitations in the types of materials that can be easily atomized. |
What are the different types of metal powders used in 3D printing? | There’s a wide variety of metal powders used in 3D printing, each with distinct properties. Some popular options include stainless steel 316L (known for its corrosion resistance and biocompatibility), titanium 6Al-4V (offering a good balance of strength, weight, and biocompatibility), and Inconel 625 (ideal for high-temperature applications due to its exceptional oxidation resistance). |
How do I choose the right metal powder for my 3D printing project? | Selecting the ideal metal powder hinges on several factors. Consider the desired properties for the final part (strength, weight, corrosion resistance, etc.), the application of the 3D printed component, compatibility with your specific 3D printer’s technology, and of course, the cost of the metal powder. |
What are some applications of metal powders beyond 3D printing? | Metal powders have a vast range of applications beyond additive manufacturing. They are used in Metal Injection Molding (MIM) to create intricate metal parts, thermal spraying to coat surfaces with specific properties (like wear resistance), and cladding to create composite materials with a core and a bonded outer layer of a different metal. |
What’s the future outlook for metal powders? | The future of metal powders is incredibly promising. Researchers are exploring exciting areas like the use of metal nanoparticles for enhanced properties, development of custom alloys with tailored properties, and even the utilization of recycled metal powders for a more sustainable approach. |
Where can I learn more about metal atomization and metal powders? | Numerous resources are available online and in libraries that delve deeper into metal atomization and metal powders. Reputable websites of metal powder manufacturers, industry associations, and research institutions can provide valuable insights. Additionally, academic journals and publications focused on materials science and engineering often explore advancements in metal powder technology. |
Share On
MET3DP Technology Co., LTD is a leading provider of additive manufacturing solutions headquartered in Qingdao, China. Our company specializes in 3D printing equipment and high-performance metal powders for industrial applications.
Inquiry to get best price and customized Solution for your business!
Related Articles
About Met3DP
Recent Update
Our Product
CONTACT US
Any questions? Send us message now! We’ll serve your request with a whole team after receiving your message.
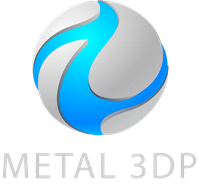
Metal Powders for 3D Printing and Additive Manufacturing