Atomized Metal powder – A Comprehensive Guide in 2025
Table of Contents
What is atomized metal powder?
Atomized metal powder refers to metal powders produced through atomization, a process where molten metal is converted into fine droplets which solidify into powder particles. Atomization allows the production of metal powders with precise particle sizes, shapes and chemical compositions.
Atomized metal powders find a wide range of applications in additive manufacturing, 3D printing, metal injection molding, brazing, welding, thermal spraying and more. This article provides a detailed guide on atomized metal equipment including types, characteristics, applications, specifications, suppliers, installation, operation, maintenance and more.
Atomized Metal Powder Composition
The composition of atomized metal powder is determined by the type of metal or alloy being atomized. Different metals and alloys are used depending on the desired properties of the final product. Here’s a breakdown of common metals used for atomization and their characteristics.
Metal/Alloy | Composition | Characteristics |
---|---|---|
Aluminum (Al) | 99% Aluminum or Aluminum Alloys | Lightweight, corrosion-resistant, high thermal conductivity. |
Steel (Fe-C Alloys) | Iron, Carbon, Chromium (various alloys) | Strong, durable, used in automotive and construction industries. |
Copper (Cu) | 99% Copper or Copper Alloys | Excellent electrical and thermal conductivity, used in electronics and wiring. |
Titanium (Ti) | Pure Titanium or Alloys (Ti-6Al-4V) | High strength-to-weight ratio, corrosion resistance, used in aerospace and medical. |
Nickel (Ni) | Nickel Alloys (Inconel, Monel) | High-temperature resistance, used in turbines and engine components. |
Cobalt (Co) | Cobalt Alloys (Stellite, Haynes) | Wear-resistant, used in cutting tools and dental/medical applications. |
Why Composition Matters
The composition of atomized metal powder dictates its final properties. For instance, aluminum is great for lightweight applications, while titanium is ideal when you need something strong yet light for aerospace components. Understanding the composition can help you choose the right powder for your specific application.
Atomized Metal Powder Properties
When selecting a metal powder for a particular application, it’s crucial to understand its properties. These properties will affect everything from how the powder behaves during processing to the performance of the final product.
Property | Description |
---|---|
Particle Size Distribution | The range of particle sizes, which affects flowability and packing density. |
Shape | Can be spherical, irregular, or flake-like; spherical particles are ideal for 3D printing. |
Purity | High-purity powders are essential for applications requiring precise performance. |
Density | The mass-to-volume ratio, which influences strength and material usage. |
Flowability | The ease with which the powder flows, important for processes like sintering. |
Hardness | A measure of a material’s resistance to deformation, relevant in wear applications. |
Oxidation Resistance | The ability of the powder to resist oxidation, crucial for storage and processing. |
Thermal Conductivity | How well the material conducts heat, critical for electronics and heat sinks. |
The Importance of Properties
Imagine you’re 3D printing a part that needs to be both strong and lightweight. If you choose a powder with the wrong particle size or flowability, you could run into issues with the print’s quality or the final part’s strength. This is why understanding the properties of atomized metal powder is so important.
Applications of Atomized Metal Powder
Atomized metal powders are used across various industries due to their versatility, precision, and unique properties. Here are some of the most common applications:
Industry | Application |
---|---|
Additive Manufacturing | Metal powders are used in 3D printing to create complex, high-strength parts. |
Powder Metallurgy | Powders are pressed and sintered to create parts like gears, bearings, and filters. |
Coatings | Used in thermal spraying to coat surfaces with a protective or functional layer. |
Automotive | Metal powders are used in producing lightweight, high-strength engine components. |
Aerospace | High-performance powders like titanium are used for turbine blades and structural parts. |
Medical | Powders are used to produce biocompatible implants and surgical tools. |
Electronics | Used in the production of electrical connectors and heat sinks. |
Why These Applications Matter
Think about the automotive industry. Cars today are lighter and more fuel-efficient than ever before, thanks in part to the use of lightweight metal powders in engine components. Similarly, in the medical field, atomized metal powders allow for the creation of customized implants that perfectly fit a patient’s anatomy.
Specifications and Standards for Atomized Metal Powder
When purchasing or working with atomized metal powder, it’s essential to know the specifications that define its performance and compatibility. These specs can vary by industry and application, but the following are some of the most common.
Specification | Description |
---|---|
Particle Size Range | Typically ranges from 10 microns to 150 microns, depending on the application. |
Powder Shape | Spherical or irregular, with spherical being preferred for additive manufacturing. |
Purity | High-purity grades are essential for critical applications like aerospace or medical. |
Density | Bulk and tapped density impact how the powder packs and sinters during processing. |
Flow Rate | Measured in seconds per 50g, indicating how easily the powder flows. |
Standards | ASTM, ISO, and AMS standards dictate the quality and testing methods for metal powders. |
Choosing the Right Specifications
Let’s say you’re involved in 3D printing aerospace components. You’ll likely need a powder with a very specific particle size range and purity to ensure the final product meets safety and performance standards. Knowing what to look for in terms of specifications is crucial for success.
Suppliers and Pricing for Atomized Metal Powder
The price of atomized metal powder varies widely depending on the type of metal, the quality, and the supplier. Here’s a look at some general price ranges and suppliers.
Supplier | Country | Material | Price Range (per kg) |
---|---|---|---|
Met3dp | China | Iron, Copper, Stainless Steel, Titanium, Inconel | $10 – $50 |
Valimet | USA | Aluminum, Titanium | $30 – $300 |
LPW Technology | UK | Nickel Alloys, Titanium | $100 – $500 |
Tekna | Canada | Spherical Titanium, Aluminum | $200 – $700 |
Sandvik | Global | Various Alloys | $150 – $600 |
Factors Affecting Pricing
Several factors influence the cost of atomized metal powders, including the type of atomization process (gas atomization is more expensive than water atomization), the metal or alloy used, and the required purity. For example, titanium powder is significantly more expensive than iron powder due to its higher melting point and more complex atomization process.
Handling, Storage, and Safety Information for Atomized Metal Powder
Proper handling and storage of atomized metal powder are essential to maintain quality and ensure safety. Metal powders can be hazardous if not handled correctly, with risks including inhalation, combustion, and contamination.
Consideration | Guidelines |
---|---|
Handling | Always use personal protective equipment (PPE) such as gloves and masks to avoid direct contact or inhalation. |
Storage | Store in a cool, dry place, away from any sources of ignition. Keep containers sealed to avoid contamination. |
Fire and Explosion Risk | Some metal powders (like aluminum and titanium) are highly flammable in powder form. Avoid creating dust clouds and ensure proper ventilation. |
Moisture Control | Metal powders, especially those prone to oxidation (like iron), should be stored in a low-humidity environment. |
Disposal | Dispose of unused powder according to local environmental regulations, as some powders can be hazardous to the environment. |
Why Safety Matters
Handling metal powder is like handling fireworks—safe and controlled in the right circumstances, but dangerous if mishandled. For instance, aluminum and titanium powders are prone to combustion when exposed to air in the wrong conditions. Hence, proper safety protocols are a must.
Inspection and Testing Methods for Atomized Metal Powder
Ensuring the quality and consistency of atomized metal powder is crucial for its performance in various applications. Inspection and testing methods are used to verify that the powder meets the required specifications.
Testing Method | Purpose |
---|---|
Particle Size Analysis (PSA) | Ensures that the powder has the correct particle size distribution. |
X-ray Diffraction (XRD) | Analyzes the crystalline structure of the powder for phase identification. |
Scanning Electron Microscopy (SEM) | Provides detailed images of the powder’s surface to examine shape and morphology. |
Chemical Composition Test | Verifies the elemental composition of the powder, ensuring purity. |
Flow Rate Test | Measures how quickly the powder flows, which is important for processes like 3D printing. |
Tap Density Test | Determines how tightly the powder packs, which affects sintering and final part density. |
The Importance of Testing
Think of testing like quality control for a gourmet chef. Just as a chef tastes and adjusts seasoning, manufacturers must test powders for particle size, composition, and flow to ensure the final product meets performance and safety standards.
Pros and Cons of Atomized Metal Powder
Like any material, atomized metal powder has its advantages and limitations. Let’s take a deeper look at some of the key pros and cons.
Pros | Cons |
---|---|
High Precision | Atomized powders allow for precise control over particle size and shape, making them ideal for additive manufacturing. |
Versatility | Can be used across a wide range of industries, from aerospace to electronics. |
High Purity | Atomization processes can produce very pure powders, essential for critical applications. |
Cost | High-quality metal powders, especially those made from materials like titanium, can be expensive. |
Safety Risks | Some powders, like aluminum and titanium, are highly flammable and require careful handling. |
Energy-Intensive Production | The atomization process, especially gas atomization, can be energy-intensive. |
Why the Pros Outweigh the Cons
While atomized metal powders can be expensive and require careful handling, their precision, versatility, and high-quality make them indispensable in industries where performance and reliability are non-negotiable. For example, in aerospace, the ability to create lightweight yet strong parts from titanium powder far outweighs the cost and safety concerns.
Frequently Asked Questions (FAQ) About Atomized Metal Powder
Question | Answer |
---|---|
What is atomized metal powder used for? | Atomized metal powder is used in industries like additive manufacturing, powder metallurgy, and coatings. |
How is metal powder atomized? | Metal is atomized by spraying molten metal through a nozzle, breaking it into fine particles. |
Is atomized metal powder hazardous? | Some powders, like aluminum and titanium, are flammable and require careful handling and storage. |
What is the difference between gas and water atomization? | Gas atomization produces smoother, more spherical powders, while water atomization produces irregular shapes. |
How do you store atomized metal powder? | Store in a cool, dry place with minimal exposure to air and moisture to prevent oxidation and degradation. |
Can I use atomized metal powder for 3D printing? | Yes, atomized metal powders are commonly used in additive manufacturing due to their consistent particle size and shape. |
Types of Atomized Metal Equipment
Equipment | Description |
---|---|
Gas atomizers | Use high velocity inert gas (N2, Ar) to break up molten metal stream into fine droplets |
Water atomizers | Use high pressure water jets to atomize molten metal into powder |
Rotating electrode atomizers | Use centrifugal force from rotating metal wire or disk to disintegrate molten metal into droplets |
Ultrasonic atomizers | Use ultrasonic vibrations to create capillary waves and disintegrate molten metal stream |
Centrifugal atomizers | Molten metal poured on spinning disk breaks into droplets flung outwards by centrifugal force |
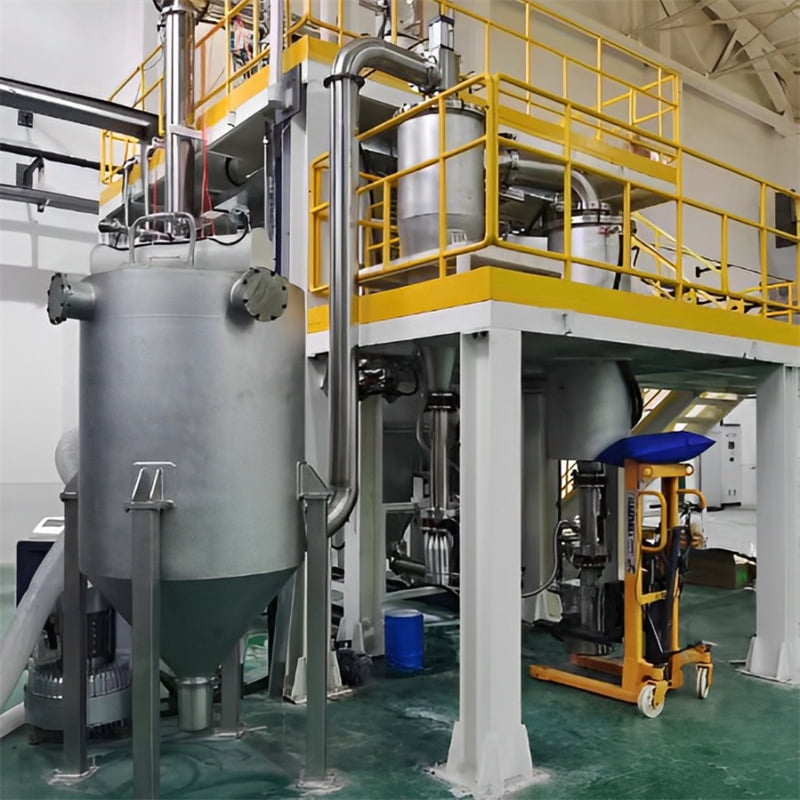
Characteristics of Atomized Metal Powder
Characteristic | Description |
---|---|
Particle size | Microns to millimeters; controlled by atomization process parameters |
Particle shape | Spherical, irregular or satellite shaped; depends on method and conditions |
Size distribution | Can be made very narrow using certain atomization techniques |
Purity | High purity possible by using refined molten metal feedstock |
Density | Can approach theoretical density of the metal |
Flowability | Affected by particle size, shape and distribution; important for handling |
Sintering activity | Fine powders with large surface area sinter rapidly during compaction into solid metal |
Applications of Atomized Metal Powder
Application | Details |
---|---|
Metal powder bed fusion | Atomized fine powders used in laser/electron beam powder bed 3D printing |
Binder jetting | Stainless steel, tool steel, aluminum powders for binder jet 3D printing |
Metal injection molding | Stainless steel, titanium, aluminum powders mixed with binder and molded |
Thermal spray coatings | Fe, Ni, Co, Cu and alloy powders sprayed onto surfaces for wear/corrosion protection |
Brazing pastes | Ag, Cu, Ni alloy powders in paste formulations for joining metals |
Friction materials | Cu, Fe powders improve friction and wear in brake linings and clutch facings |
Welding | Atomized Ti, Al powders added during arc welding to improve weld properties |
Powder metallurgy | Press and sinter atomized Fe, steel, Cu powders into net shape components |
Magnetics | Insulated Fe, ferrite powders pressed into magnets and inductors |
Metal catalysts | Wide range of alloy powder catalysts used in chemical industry |
Specifications of Atomized Metal powder Equipment
Parameter | Typical Range |
---|---|
Production capacity | 10-100 kg/hour |
Gas consumption | 10-100 Nm3/hr argon or nitrogen |
Cooling water usage | 100-1000 L/min |
Power consumption | 50-500 kW |
Floor space | 100-500 sqft |
Control systems | PLC, SCADA, data monitoring |
Safety systems | Gas detectors, fire suppression, safety PPE |
Molten metal handling | Launders, troughs, pouring systems |
Powder collection | Cyclones, bag filters, screw conveyors |
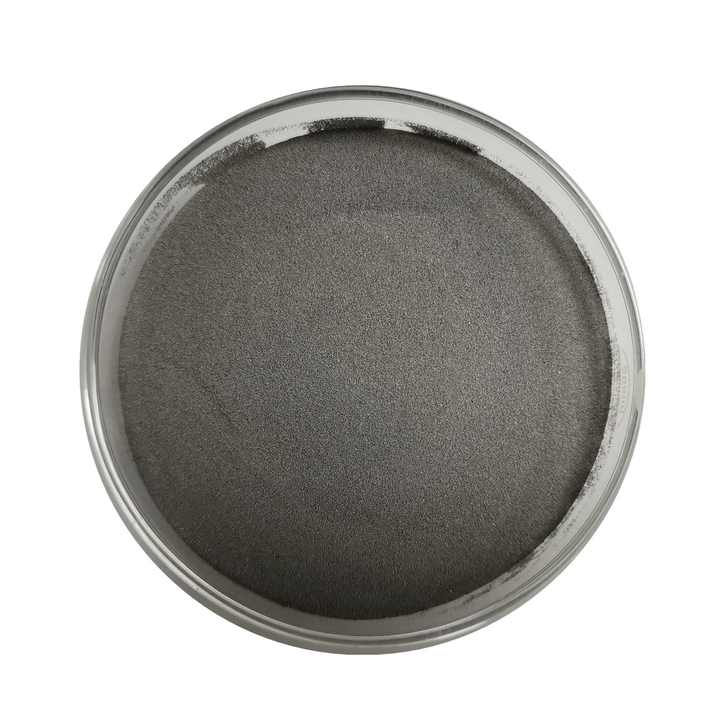
Suppliers and Pricing
Supplier | Equipment | Price Range |
---|---|---|
Gasbarre | Gas atomizers | $500,000 – $2 million |
Idra | Water atomizers | $1 – 5 million |
Kessenich | Rotating electrode | $250,000 – $1 million |
Sodick | Ultrasonic nozzle | $100,000 – $500,000 |
AcuPowder | Centrifugal wheel | $50,000 – $250,000 |
Atomized metal equipment prices vary widely depending on capacity, automation features, ancillary systems, brand reputation and other factors. Budget at least $250,000 to $1 million for an industrial scale production unit.
Installation and Facilities
- Atomized metal equipment should be installed in a well-ventilated, temperature and humidity controlled production space.
- Provide sufficient overhead cranes, hoists and rigging gear for equipment installation and maintenance.
- Ensure adequate power supply, utilities and compressed air connections are in place.
- Have qualified personnel for equipment assembly, alignment, testing and commissioning.
- Design proper foundations, anchor bolts, equipment platforms for secure installation.
- Include dust collection ducting, cyclones and baghouse for collecting atomized metal powder.
- Install safety features like gas monitoring sensors, fire suppression systems.
- Allow enough free space for material handling, workflows and maintenance access.
Operation and Maintenance
Activity | Details | Frequency |
---|---|---|
Equipment inspection | Check fluid levels, leaks, unusual noise/vibration, safety devices | Daily |
Parameter monitoring | Log process data like temps, pressures, flows, power | Continuous |
Consumable replenishment | Refill cooling water, inert gas cylinders, lubricants | As needed |
Housekeeping | Clean spills, empty dust collectors, general cleaning | Daily |
Component replacement | Replace worn out nozzles, bearings, seals, filters | Per schedule |
Calibration | Calibrate sensors, measurement devices, control systems | Quarterly |
Major maintenance | Inspect major parts; repair/replace if needed | Annually |
Proper operation and preventive maintenance as per manufacturer guidelines is key to maximizing equipment life and performance. Maintain detailed logs of all maintenance work.
Choosing an Atomized Metal powder Equipment Supplier
Consideration | Details |
---|---|
Technical expertise | Long experience in atomization technology and metal powder production |
Customization | Ability to customize equipment to meet specific production needs |
Reliability | Proven track record of robust, reliable equipment with low failure rates |
Automation | Advanced control systems, data monitoring for optimized powder characteristics |
Aftersales service | Installation support, operator training, service contracts for maintenance |
References | Positive feedback from existing customers on equipment quality and vendor reputation |
Value | Right balance of quality, performance and fair pricing |
Local presence | Physical proximity for face-to-face meetings and quick response |
Evaluate vendors thoroughly on the above parameters before investing in atomized metal equipment. Weigh factors like quality, reliability, service over lowest cost while making a selection.
Pros and Cons of Atomized Metal Processes
Gas Atomization
Pros
- Produces highly spherical, smooth powders ideal for AM, MIM etc.
- Narrow particle size distribution possible
- Operates continuously with good productivity
- Lower capital cost compared to water atomization
Cons
- Limited to smaller particle sizes, usually below 100 microns
- Requires large volumes of expensive inert gas
- Dust levels in work area may be high
Water Atomization
Pros
- Can produce a wide range of powder sizes including large diameters
- Lower gas consumption than gas atomization
- Denser powders compared to gas atomized
Cons
- Less spherical particles, more satelliting
- Water treatment needed for atomizing water
- Oxide inclusions possible from water contact
Centrifugal Atomization
Pros
- Simple mechanism with minimal utilities
- Compact design with lower capital costs
- Operates semi-continuously with good productivity
Cons
- Limited control over particle size distribution
- Irregular, non-spherical particle shapes
- Contamination risk from disk wear over time
Limitations of Atomized Metal Processes
- High production costs especially for very fine metal powders
- Particle shape and size range constraints based on technique
- Requirement ofSpecialized equipment with controlled conditions
- High purity feedstock metals needed for pure powders
- Batch operation in some methods lowers productivity
- Post-processing like sieving often needed to control particle sizes
- Highly skilled personnel needed to operate equipment
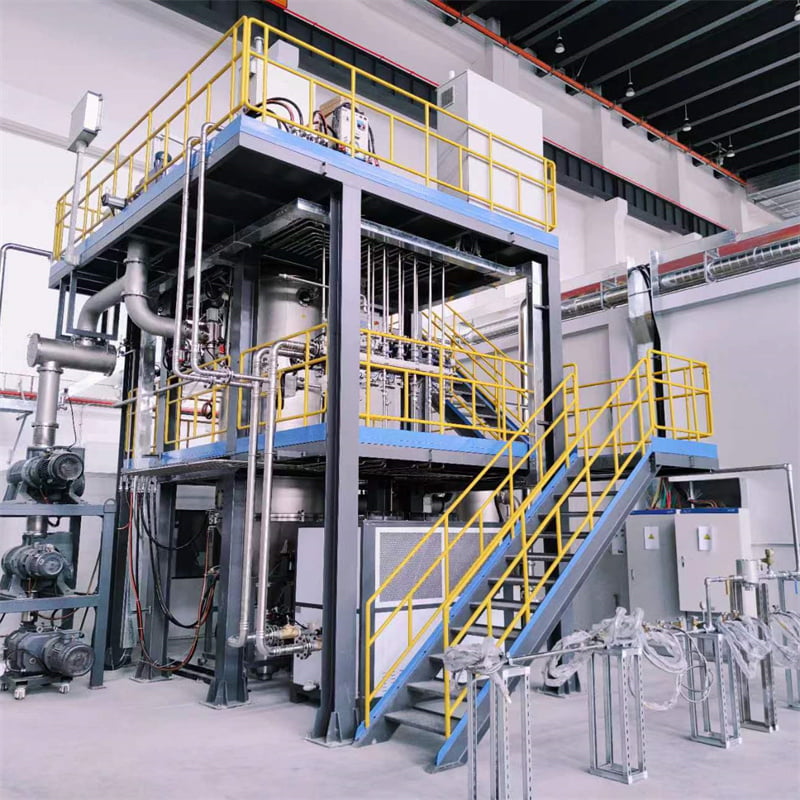
FAQ
What methods are used for classifying atomized metal powders by particle size?
Common methods for classifying atomized metal powders include:
- Sieving – Stack of sieves with decreasing mesh size separates powder into size fractions
- Air classification – Centrifugal or cyclone separators classify fines from coarser particles
- Elutriation – Counterflow air/water fluidization allows fines to overflow by gravity
- Sedimentation – Particles settle downward in liquid at rates dependent on size/density
What safety precautions are required when handling atomized metal powders?
Key safety precautions when handling atomized powders:
- Use PPE – gloves, eye protection, filter masks to prevent skin/eye contact and inhalation
- Inert gas purging to prevent powder oxidation and dust explosions
- Proper grounding of powder handling equipment to dissipate static charges
- Avoid all ignition sources in powder processing areas
- Install dust collection equipment to capture airborne powder
- Conduct air monitoring to check for combustible dust levels
How are atomized metal powders handled and transported?
Typical powder handling steps:
- Collected in drums below cyclone separators or bag house filters
- Transported in sealed containers to prevent oxygen contact
- Pneumatic conveying via nitrogen or argon through pipelines
- Vacuum suction transfer into powder storage vessels
- Manual scooping/shovelling for small batches
- Automated mechanical conveyors for large volumes
Powders are kept sealed until ready for use to prevent contamination.
What steps are taken to prevent contamination during atomized metal powder production?
- Use high purity raw materials and feedstock
- Maintain inert atmosphere using argon/nitrogen
- Keep oxygen and moisture out through sealing
- Avoid contact between powder and tramp metal
- Frequent cleaning of equipment contacting powder
- Remove oil and grease residues using solvents
- Sieving/classification to isolate irregular particles
- Analysis to identify and eliminate impurity sources
What are the most common applications for stainless steel powders produced via atomization?
Typical applications of atomized stainless steel powders:
- Additive manufacturing – Selective laser melting, binder jetting
- Metal injection molding of small, complex parts
- Brazing pastes and solder fillers for joining
- Powder metallurgy pressing into porous filters
- Self-lubricating bearings manufacturing
- Production of stainless steel fibers for textiles
- Electrochemical machining/discharge machining electrodes
- Manufacture of stainless steel powder paints and coatings
How to choose inert gas supply systems for gas atomization?
Considerations for inert gas supply:
- Argon preferred over nitrogen for reactive metals like titanium
- High capacity gas storage tanks with backup cylinders
- Purity levels of 99.99%+ to prevent contamination
- Pressure regulators and flow meters for gas control
- Use of gas recovery systems to minimize waste
- Heated gas lines to prevent freezing of moisture
- Automated changeover and monitoring of gas parameters
- Proper alarms and interlocks for gas safety
Optimizing Atomized Metal Powder Characteristics
The properties of atomized metal powders can be optimized by controlling process parameters and atomization conditions:
Particle Size Distribution
Method | Effect |
---|---|
Increase molten metal flow rate | Larger mean particle size |
Use higher atomizer spinning speeds | Finer powder fraction increased |
Lower molten metal pour temperature | Tighter particle size distribution |
Classify powder via sieving/air separation | Remove oversize and undersize fractions |
Particle Shape
Method | Effect |
---|---|
Use gas or water atomization | More spherical particles |
Lower metal pour rate | More spherical particles |
Increase melt superheat temperature | Reduces satellites and irregular shapes |
Anneal powders after atomization | Improves spherical morphology |
Powder Purity
Method | Effect |
---|---|
Use high purity metal feedstock | Reduces metallic impurities |
Add slag removal stage | Removes non-metallic inclusions |
Increase inert gas purity | Reduces gaseous impurities |
Use nickel-plated collection vessels | Lowers iron pickup |
Sieve powder to remove satellites | Increases powder purity |
Powder Density
Method | Effect |
---|---|
Optimize atomization parameters | Uniform dense powder |
Anneal powder after atomization | Removes internal voids and pores |
Compress powder after atomizing | Work hardens and consolidates powder |
Thermomechanical processing | Improves powder microstructure |
By optimizing the atomization process and powder handling steps, the characteristics of atomized metal powders can be tailored to meet application requirements.
Emerging Trends in Atomized Metal Powder Production
Some key emerging trends in atomized powder production technology include:
- Additive manufacturing is driving demand for spherical ultrafine powders below 30 microns. New nozzles and atomization methods are enabling such powders.
- Automation of powder production using Industry 4.0 concepts allowing remote monitoring, control and data-driven manufacturing.
- Hybrid atomization techniques combining aspects of gas, water and centrifugal atomization for better particle control.
- Microwave assisted heating of molten metal for faster, more uniform heating prior to atomization.
- Simulation and modelling of droplet formation dynamics leading to better understanding of atomization physics.
- Development of new alloys tailored specifically for additive manufacturing applications.
- Improved powder handling systems with integrated sieving, classification and storage.
- Continuous powder production processes instead of batch methods for higher throughput.
- Advanced control systems using AI and machine learning algorithms for automated optimization of atomization process.
- Specialized gas atomization nozzles optimized for reactive metals like titanium and aluminum alloys.
- Recycling and reusing scrap metal powders from AM processes using thermal treatments.
- In-process monitoring techniques such as infrared imaging for better powder quality control.
Conclusion
Atomized metal powders enable critical applications across automotive, aerospace, medical, 3D printing and other key industries. With increasing demand for high quality powders, metal atomization technology continues to evolve through new innovations in process intensification, automation, alloys development and advanced characterization techniques. By adopting the latest advances, powder producers can manufacture powders in an agile, cost-effective and sustainable manner.
Share On
MET3DP Technology Co., LTD is a leading provider of additive manufacturing solutions headquartered in Qingdao, China. Our company specializes in 3D printing equipment and high-performance metal powders for industrial applications.
Inquiry to get best price and customized Solution for your business!
Related Articles
About Met3DP
Recent Update
Our Product
CONTACT US
Any questions? Send us message now! We’ll serve your request with a whole team after receiving your message.
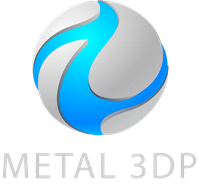
Metal Powders for 3D Printing and Additive Manufacturing