BAg-8 Powder for Powder Metallurgy
Table of Contents
The world of Powder Metallurgy (PM) thrives on tiny, potent ingredients. Among these champions stands BAg-8 powder, a silver-copper alloy that injects remarkable properties into PM parts. Let’s delve into the fascinating world of BAg-8, exploring its composition, applications, and why it’s a PM powerhouse.
BAg-8 Powder: Composition and Characteristics
BAg-8 Powder, also known as ASTM B 961, is a workhorse material in PM. It’s a binary alloy, meaning it’s primarily composed of two elements:
- Silver (Ag): The star player, silver brings exceptional electrical and thermal conductivity to the party. Think of it as the party host, ensuring a smooth flow of electricity and heat.
- Copper (Cu): Copper, the ever-reliable sidekick, strengthens the alloy and enhances its mechanical properties. Imagine it as the bouncer, keeping things sturdy and functional.
The magic lies in the specific ratio: BAg-8 Powder boasts 8 weight percent (wt%) silver and 92 wt% copper. This carefully chosen blend unlocks a unique set of characteristics that make BAg-8 a PM superstar.
Here’s a table summarizing the key details of BAg-8:
Feature | Description |
---|---|
Composition | 8 wt% Silver (Ag), 92 wt% Copper (Cu) |
Classification | Silver-Copper Alloy |
Standard | ASTM B 961 |
Appearance | Silvery-pink, similar to copper in raw form |
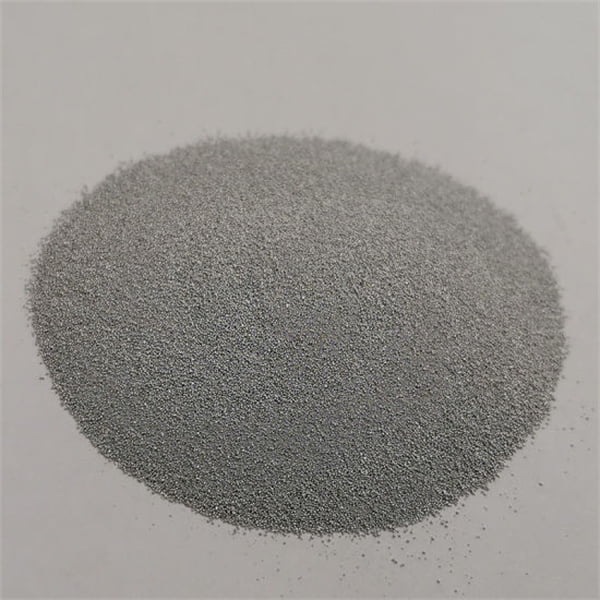
Properties and Characteristics of BAg-8 Powder
BAg-8’s true power lies in its exceptional properties, making it a PM material of choice for diverse applications. Let’s explore some of its key characteristics:
- High Electrical Conductivity: Remember the silver host? It shines here! BAg-8 boasts excellent electrical conductivity, rivaling pure copper in some cases. This makes it ideal for electrical contacts, connectors, and components requiring efficient current flow.
- Superior Thermal Conductivity: The heat transfer capabilities of BAg-8 are equally impressive. This allows PM parts to dissipate heat efficiently, a crucial feature in applications like heat sinks and electronic components.
- Enhanced Mechanical Strength: Copper, the bouncer, steps up here. Compared to pure silver, BAg-8 offers superior mechanical strength and wear resistance. This makes it suitable for parts that experience friction and stress.
- Excellent Weldability: BAg-8 readily bonds with other materials, making it perfect for creating multi-material components with unique properties.
- Good Corrosion Resistance: While not the most corrosion-resistant material, BAg-8 offers decent resistance in many environments, adding to its versatility.
Comparing BAg-8 Powder with Other Metal Powders
BAg-8 Powder isn’t the only player in the PM game. Here’s a comparison of BAg-8 with other popular metal powders to understand its strengths and limitations:
Feature | BAg-8 | Copper (Cu) | Iron (Fe) |
---|---|---|---|
Composition | 8 wt% Ag, 92 wt% Cu | 100% Cu | 100% Fe |
Electrical Conductivity | High | High | Low |
Thermal Conductivity | High | High | Moderate |
Mechanical Strength | Moderate | Moderate | High |
Weldability | Excellent | Good | Moderate |
Corrosion Resistance | Moderate | Moderate | Low |
Cost | More expensive | Less expensive | Least expensive |
As you can see, BAg-8 strikes a balance between excellent electrical and thermal conductivity, good mechanical strength, and weldability. However, it comes at a higher cost compared to pure copper or iron.
Applications of BAg-8 in PM
BAg-8’s unique blend of properties translates to a wide range of applications in PM. Here are some key areas where BAg-8 shines:
- Electrical Applications: Its high electrical conductivity makes BAg-8 ideal for electrical contacts, connectors, bus bars, and brush contacts in motors and generators.
- Thermal Management: The exceptional thermal conductivity of BAg-8 finds applications in heat sinks for electronic components, LED lighting, and power electronics. Imagine BAg-8 as a tiny bodyguard, whisking away heat and protecting sensitive components from overheating.
- Electronic Packaging: BAg-8’s ability to be formed into intricate shapes and its good weldability make it suitable for electronic packaging components like leadframes and lids for integrated circuits. Think of BAg-8 as the invisible scaffolding that holds electronic components together efficiently.
- Friction Components: While not the strongest metal, BAg-8 offers a good balance of strength and wear resistance. This makes it suitable for applications like sliding electrical contacts, brushes, and switchgear components that experience constant friction. Here, BAg-8 plays the role of a tireless worker, enduring wear and tear while maintaining functionality.
- Biocompatible Applications: In some cases, BAg-8 can be used in biocompatible applications due to its moderate corrosion resistance and ability to be sterilized. However, extensive testing and regulatory approvals are necessary for such uses.
Beyond the Obvious: Exploring Niche Applications of BAg-8
The versatility of BAg-8 Powder extends beyond common PM applications. Here are some interesting niche uses:
- Additive Manufacturing (AM): With advancements in AM techniques, BAg-8 powder can be used in 3D printing processes to create intricate components with unique electrical and thermal properties. Think of BAg-8 as a versatile artist’s palette, allowing for the creation of complex, functional parts.
- Electromagnetic Shielding: The excellent electrical conductivity of BAg-8 can be used to create electromagnetic shielding materials, protecting sensitive electronics from unwanted interference. Imagine BAg-8 as a suit of armor, guarding electronics from the chaos of electromagnetic waves.
Metal Powders for BAg-8 – Specification Variations
BAg-8 Powder itself comes in various forms, each with slightly different properties and applications. Here’s a table outlining some key specifications to consider:
Specification | Description |
---|---|
Particle Size Distribution | Affects packing density, flowability, and final part properties. Common grades include finer powders for intricate shapes and coarser powders for better strength. |
Surface Area | Influences sintering behavior, reactivity, and mechanical properties. Higher surface area powders may sinter faster but might require lower processing temperatures. |
Apparent Density | The bulk density of the powder, impacting material handling and powder bed formation during PM processes. |
Flowability | The ease with which the powder flows, affecting die filling and overall process efficiency. |
Purity | The presence of impurities can affect final part properties. Higher purity BAg-8 might be required for specific applications. |
Specific BAg-8 Metal Powders
Now, let’s delve into some specific BAg-8 Powder offerings from various manufacturers. Here’s a table showcasing 10 popular options, highlighting their key features and potential applications:
Manufacturer | Product Name | Description | Key Applications |
---|---|---|---|
Höganäs AB | AMPCOS 4800 | Spherical BAg-8 powder with excellent flowability and packing density. | Electrical contacts, connectors, heat sinks, electronic packaging |
Carpenter Additive | Carpenter Incus BAg-8 | Optimized BAg-8 powder for Additive Manufacturing applications, offering good printability and sinterability. | 3D printed electrical components, heat sinks, complex electronic packaging |
GKN Hoeganaes Corporation | Catamold 485 | Electrolytic BAg-8 powder with a high degree of purity. | Electrical contacts requiring high conductivity and reliability |
Sandvik Hyperion | Osprey BAg-8 | Gas-atomized BAg-8 powder with a clean spherical morphology and good flowability. | Electrical connectors, brush contacts, components requiring high thermal conductivity |
AMI Metals | AMI-BAg-8 | Electrolytic BAg-8 powder with a controlled particle size distribution for consistent performance. | Electrical contacts, connectors, bus bars, components requiring balanced conductivity and strength |
APEX Powder Company | ASC A100 BAg-8 | Water-atomized BAg-8 powder with a cost-effective option for non-critical applications. | Brush contacts, sliding electrical |
the Advantages and Disadvantages of BAg-8 power
BAg-8 Powder, like any material, boasts distinct advantages and disadvantages. Understanding them is crucial for making informed decisions in your PM projects.
Advantages of BAg-8: A Shining Star
BAg-8 offers a compelling package of benefits for PM applications:
- Superior Electrical and Thermal Conductivity: The star of the show, BAg-8’s exceptional conductivity makes it ideal for applications demanding efficient current and heat flow.
- Enhanced Mechanical Strength: Compared to pure silver, BAg-8 packs a punch with its improved mechanical strength and wear resistance, making it suitable for parts under stress.
- Excellent Weldability: BAg-8 readily bonds with other materials, allowing for the creation of multi-material components with unique properties, expanding design possibilities.
- Good Corrosion Resistance: While not the most corrosion-resistant material, BAg-8 offers decent protection in many environments, adding to its versatility.
- Wide Range of Applications: From electrical contacts to heat sinks and biocompatible components (with caution), BAg-8 finds applications across diverse PM fields.
- Availability in Various Forms: The ability to choose BAg-8 with different particle sizes, surface areas, and purities allows for tailoring the material to specific application needs.
Disadvantages of BAg-8: Considering the Other Side of the Coin
Despite its numerous advantages, BAg-8 Powder has some limitations to consider:
- Higher Cost: Compared to pure copper or iron, BAg-8 comes at a premium price. This might be a deciding factor for cost-sensitive applications.
- Oxidation Potential: Silver in BAg-8 can oxidize at high temperatures, potentially affecting electrical conductivity and requiring controlled processing environments.
- Limited Corrosion Resistance: While decent, BAg-8 might not be suitable for highly corrosive environments. Consider alternative materials for such applications.
- Health Considerations: Silver can have health implications upon inhalation or ingestion. Proper handling procedures and safety equipment are crucial when working with BAg-8 powder.
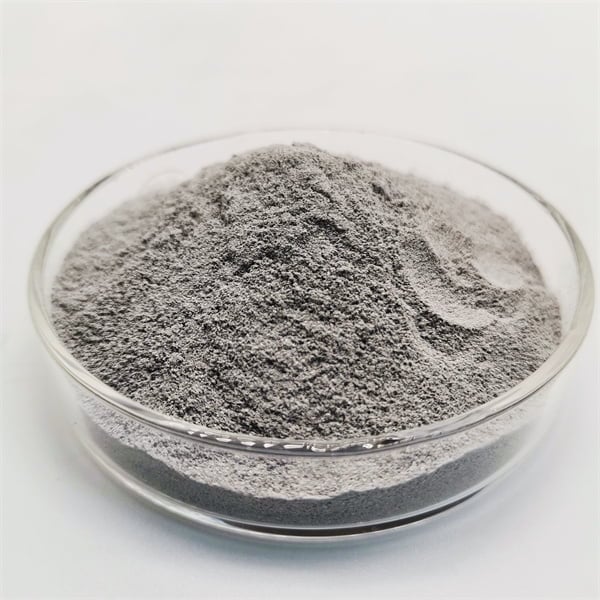
the Pros and Cons of BAg-8 power
The decision to use BAg-8 Powder hinges on your specific project requirements. If excellent electrical and thermal conductivity, good mechanical strength, and weldability are paramount, BAg-8 might be the perfect fit. However, for cost-sensitive applications or highly corrosive environments, alternative materials might be more suitable.
Finding the Right Balance: Optimizing BAg-8 for Your Needs
The beauty of BAg-8 Powder lies in its versatility. By understanding the impact of particle size distribution, surface area, and purity, you can optimize BAg-8 for your specific needs. For instance:
- Finer powders with a larger surface area might be ideal for intricate shapes but might require lower processing temperatures due to faster sintering.
- Coarser powders offer better strength but might be less suitable for complex geometries.
- Higher purity BAg-8 might be necessary for applications demanding top-notch conductivity and minimal electrical resistance.
Consulting with material suppliers and experienced PM professionals can help you select the optimal BAg-8 variant for your project.
FAQ
Here are some commonly asked questions regarding BAg-8 powder, answered in a clear and concise format:
Question | Answer |
---|---|
What is BAg-8 powder made of? | BAg-8 powder is a binary alloy composed of 8 wt% silver (Ag) and 92 wt% copper (Cu). |
What are the benefits of using BAg-8 powder in PM? | BAg-8 offers excellent electrical and thermal conductivity, good mechanical strength, weldability, and decent corrosion resistance. |
What are some applications of BAg-8 powder? | BAg-8 is used in electrical contacts, connectors, heat sinks, electronic packaging, friction components, and some biocompatible applications (with caution). |
Are there any disadvantages to using BAg-8 powder? | BAg-8 can be more expensive than other materials, susceptible to oxidation at high temperatures, and has limited corrosion resistance. It might also have health considerations with inhalation or ingestion. |
What are some things to consider when choosing BAg-8 powder? | Consider the application requirements, cost, particle size distribution, surface area, and purity of the BAg-8 powder. |
Share On
MET3DP Technology Co., LTD is a leading provider of additive manufacturing solutions headquartered in Qingdao, China. Our company specializes in 3D printing equipment and high-performance metal powders for industrial applications.
Inquiry to get best price and customized Solution for your business!
Related Articles
About Met3DP
Recent Update
Our Product
CONTACT US
Any questions? Send us message now! We’ll serve your request with a whole team after receiving your message.
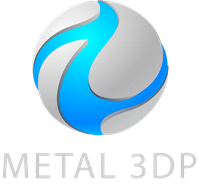
Metal Powders for 3D Printing and Additive Manufacturing