Which metal powder is suitable for Binder Jetting
Table of Contents
Binder jetting, the revolutionary 3D printing technique, has opened a new chapter in metal additive manufacturing. But just like a perfectly brewed cup of coffee relies on the right beans, successful binder jetting hinges on the ideal metal powder. So, which metallic magic dust takes the cake? Buckle up, because we’re diving deep into the world of metal powders for binder jetting, exploring their characteristics, applications, and the key players in this fascinating arena.
The Characteristics of These Metal Powders
Imagine tiny, spherical metal particles – that’s the basic building block of binder jetting powders. But these aren’t your average glitter. Here’s what makes them special:
- Particle size and distribution: Think of it like building with Legos. Finer, more uniform particles (typically between 10 and 50 microns) create smoother surfaces and tighter packing, leading to superior final part quality.
- Morphology: The shape of these particles matters. Spherical shapes flow better, enabling even deposition during printing.
- Chemical composition: This determines the final properties of the printed part. Common choices include stainless steel, nickel alloys, and tool steels, each offering unique benefits.
- Sinterability: Imagine these metal particles holding hands after the binder burns off. Powders with good sinterability readily bond during the sintering stage, achieving high final density.
- Flowability: Just like pouring sand, these powders need to flow freely for consistent layer formation during printing.
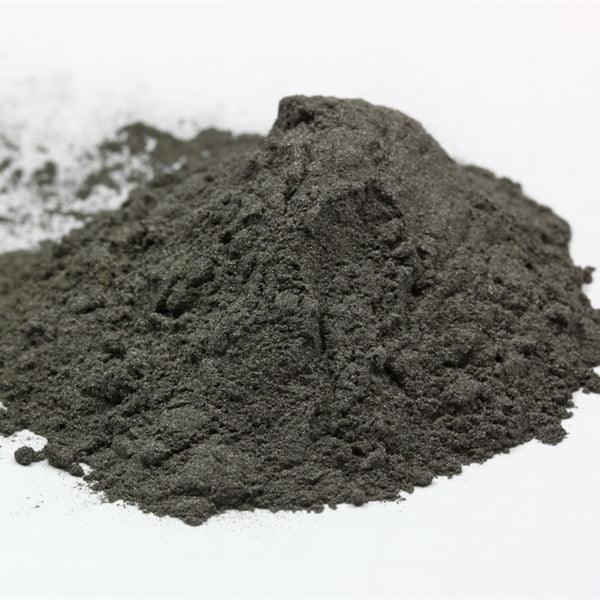
Here’s a handy table summarizing these key characteristics:
Characteristic | Description | Importance in Binder Jetting |
---|---|---|
Particle size and distribution | Fineness and uniformity of the metal particles | Impacts surface finish, density, and mechanical properties of the final part |
Morphology | Shape of the metal particles | Spherical shapes improve flowability and packing density |
Chemical composition | Elements present in the metal powder | Determines final properties like strength, corrosion resistance, and thermal behavior |
Sinterability | Ability of the powder particles to bond during sintering | Crucial for achieving high density and mechanical strength in the final part |
Flowability | Ease with which the powder flows | Essential for consistent layer formation during printing |
Commonly Used Metal Powders for Binder Jetting
Now, let’s meet some of the most popular metal powders used in binder jetting, each with its own strengths and applications:
1. 316L Stainless Steel:
A champion of versatility, 316L stainless steel powder reigns supreme in binder jetting. Renowned for its excellent corrosion resistance, strength, and biocompatibility, it’s ideal for applications ranging from medical implants to aerospace components.
2. 17-4PH Stainless Steel:
This high-strength stainless steel powder boasts exceptional mechanical properties. Think demanding applications like gears, shafts, and other components requiring superior strength and wear resistance. Compared to 316L, it offers a bit less corrosion resistance, but its superior strength makes it a compelling choice for specific needs.
3. Inconel 625:
Calling all high-temperature heroes! Inconel 625 powder shines in environments where the heat is on. This nickel-chromium superalloy withstands extreme temperatures and exhibits excellent resistance to oxidation and corrosion. Imagine jet engine components or parts exposed to harsh chemicals – that’s where Inconel 625 thrives.
4. Maraging Steel:
When it comes to toughness, maraging steel powder packs a punch. Offering a unique combination of high strength and good ductility (the ability to bend without breaking), it’s a valuable player for applications like tooling and structural components.
5. Copper:
Looking for a conductive champion? Copper powder steps into the ring. Its exceptional thermal and electrical conductivity make it ideal for heat sinks, electrical components, and applications demanding efficient heat dissipation. Compared to other options, copper powder might require specific binder formulations due to its unique properties.
6. Titanium:
Lightweight yet surprisingly strong, titanium powder is a favorite for aerospace and biomedical applications. Offering a good balance of strength, weight savings, and biocompatibility, it’s well-suited for components where both weight and performance matter.
7. Nickel Alloys:
A diverse family, nickel alloys offer a range of properties depending on their specific composition. From the high-temperature prowess of Inconel to the corrosion resistance of Hastelloy, these powders cater to specialized needs in demanding environments.
8. Tool Steels:
Need a powder that can take a beating? Tool steel powders are formulated for exceptional wear resistance and hardness.
the Applications of These Metal Powders
Now that we’ve met the stars of the show, let’s see how these metal powders translate into real-world applications:
Metal Powder | Common Applications | Key Considerations |
---|---|---|
316L Stainless Steel | Medical implants, aerospace components, jewelry, fluid handling components | Excellent corrosion resistance, biocompatibility, good strength |
17-4PH Stainless Steel | Gears, shafts, bearings, structural components | High strength, wear resistance |
Inconel 625 | Jet engine components, chemical processing equipment, heat exchangers | High-temperature resistance, oxidation resistance, corrosion resistance |
Maraging Steel | Tooling, structural components | High strength, good ductility |
Copper | Heat sinks, electrical components, waveguides | Excellent thermal and electrical conductivity |
Titanium | Aerospace components, biomedical implants, sporting goods | Lightweight, good strength, biocompatibility |
Nickel Alloys | Chemical processing equipment, marine components, heat exchangers | Tailored properties based on specific alloy composition |
Tool Steels | Cutting tools, dies, molds | Exceptional wear resistance, hardness |
Beyond the A-List: Exploring Additional Metal Powders
The world of metal powders for binder jetting is ever-expanding. Here are some additional options gaining traction:
- Aluminum alloys: Offering a lightweight alternative with good strength and corrosion resistance, aluminum alloys are being explored for applications in automotive and aerospace industries.
- Refractory metals: For those venturing into truly extreme environments, refractory metals like tungsten and molybdenum can withstand incredibly high temperatures, making them ideal for applications like furnace components and rocket nozzles. However, these powders can be more challenging to process due to their high melting points.
- Metal composites: Innovation is brewing with the exploration of metal composite powders. These combine metal particles with other materials like ceramics or polymers, offering unique combinations of properties like improved wear resistance or self-lubricating characteristics.
Choosing the right metal powder for binder jetting
Choosing the ideal metal powder for your binder jetting project involves careful consideration of several factors. Here’s a breakdown of key specifications to keep in mind:
Specification | Description | Importance |
---|---|---|
Particle size and distribution | As discussed earlier, finer and more uniform particles lead to better surface finish and density. | |
Chemical composition | The specific elements present in the powder determine the final properties of the printed part. | |
Flowability | The powder needs to flow freely for consistent layer formation during printing. | |
Apparent density | This refers to the density of the powder in its loose form. | Affects powder handling and storage requirements. |
Tap density | This is the density of the powder after tapping to remove air pockets. | |
Minimum order quantity (MOQ) | The minimum amount of powder you can purchase from a supplier. |
The Price Tag: Exploring Costs and Suppliers
The cost of metal powder for binder jetting can vary significantly depending on the specific material, particle size, and supplier. Here’s a ballpark range for some popular options:
Metal Powder | Price Range (per kg) |
---|---|
316L Stainless Steel | $50 – $100 |
17-4PH Stainless Steel | $70 – $120 |
Inconel 625 | $150 – $250 |
Maraging Steel | $100 – $150 |
Copper | $30 – $50 |
Titanium | $200 – $300 |
Pros and Cons of Binder Jetting
Just like any material, metal powders for binder jetting come with their own set of advantages and limitations. Here’s a balanced perspective to help you make an informed decision:
Pros:
- Design freedom: Binder jetting allows for the creation of complex geometries that might be difficult or impossible with traditional manufacturing techniques.
- Material diversity: A wide range of metal powders are available, catering to various application needs.
- Lightweight parts: Metal powders like aluminum and titanium enable the creation of lightweight components, crucial for industries like aerospace.
- Mass customization: Binder jetting is well-suited for producing small batches or even one-off custom parts.
Cons:
- Material cost: Metal powders can be expensive compared to some conventional materials.
- Surface finish: Binder jetting parts might require post-processing for a smooth surface finish.
- Part density: While sintering improves density, it might not reach the same level as some other metalworking techniques like forging.
- Limited production speed: Binder jetting can be slower than some traditional manufacturing methods for high-volume production.
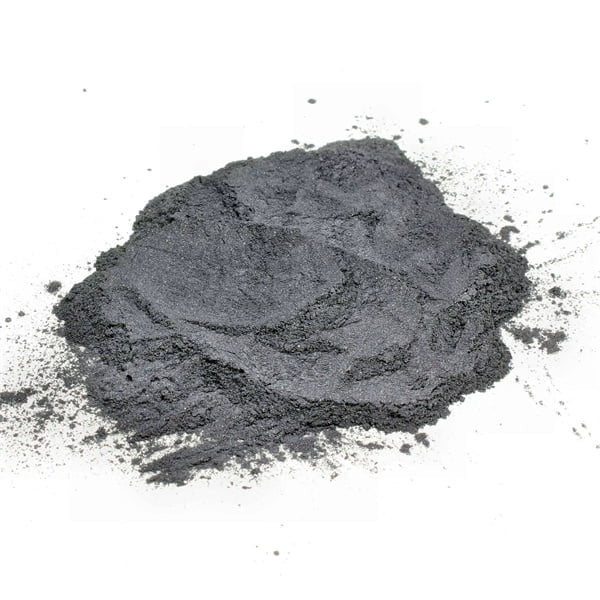
Choosing the Right Powder
So, how do you select the ideal metal powder for your binder jetting project? Here’s a roadmap to guide you:
- Identify your application requirements: Consider factors like the part’s function, mechanical properties needed (strength, wear resistance, etc.), and environmental conditions it will encounter.
- Research compatible materials: Explore the available metal powders and their properties based on your application needs. Refer to the information and tables provided earlier to narrow down your options.
- Consult with a material supplier: Material suppliers can offer valuable insights and recommendations based on your specific project requirements. They can also advise on factors like powder flowability and compatibility with your binder jetting system.
- Consider prototyping: If you’re unsure about the best powder choice, consider creating prototypes with different options to evaluate printability, final part properties, and overall suitability for your application.
FAQ
Q: What are some factors that affect the flowability of metal powder?
A: Particle size, shape, and surface characteristics all influence flowability. Finer powders and irregular shapes can lead to flowability issues. Suppliers often offer powders with enhanced flow properties for binder jetting applications.
Q: Can I use recycled metal powder in binder jetting?
A: The feasibility of using recycled metal powder depends on the specific application and the recycling process. Recycled powders might require additional processing to ensure consistent quality and printability. It’s advisable to consult with a material supplier to determine the suitability of recycled powders for your project.
Q: How are metal powders stored?
A: Metal powders are typically hygroscopic, meaning they absorb moisture from the air. Therefore, they need to be stored in moisture-controlled environments to prevent oxidation and ensure consistent performance during printing.
Share On
MET3DP Technology Co., LTD is a leading provider of additive manufacturing solutions headquartered in Qingdao, China. Our company specializes in 3D printing equipment and high-performance metal powders for industrial applications.
Inquiry to get best price and customized Solution for your business!
Related Articles
About Met3DP
Recent Update
Our Product
CONTACT US
Any questions? Send us message now! We’ll serve your request with a whole team after receiving your message.
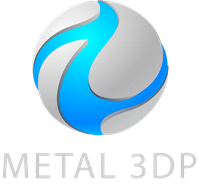
Metal Powders for 3D Printing and Additive Manufacturing