BNi-5 Powder: A Powerful Ally for PM
Table of Contents
Imagine building intricate metal parts layer by layer, with exceptional strength and heat resistance. That’s the magic of Powder Metallurgy (PM), and BNi-5 powder is a superstar in this game. But what exactly is BNi-5, and why should PM professionals take notice? Let’s dive deep and explore this remarkable material.
A Nickel-Based Marvel
BNi-5 powder is a nickel-based superalloy specifically designed for PM applications. Think of it as a concentrated blend of superpowers. Nickel forms the base, providing excellent high-temperature strength and corrosion resistance. But BNi-5 doesn’t stop there. It’s meticulously formulated with other elements like chromium, aluminum, and titanium. Each addition plays a specific role, like adding fire resistance (chromium) or lightness (aluminum). This synergistic blend unlocks a unique set of properties that make BNi-5 a game-changer in PM.
Here’s a table summarizing the key details of BNi-5 powder:
Feature | Description |
---|---|
Material Type | Nickel-based superalloy |
Primary Application | Powder Metallurgy (PM) |
Key Elements | Nickel (Ni), Chromium (Cr), Aluminum (Al), Titanium (Ti) |
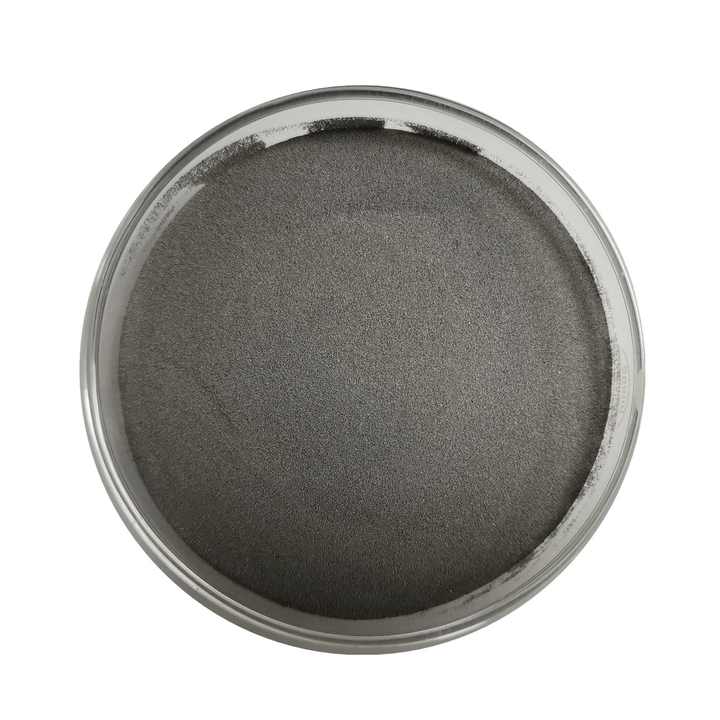
Properties of BNi-5 Powder
BNi-5 powder boasts a remarkable combination of properties, making it a highly sought-after material for demanding PM applications. Let’s dissect its superpowers:
High-Temperature Strength: Imagine a jet engine soaring through the sky. The intense heat generated could melt lesser materials. But BNi-5 shines here. It retains exceptional strength at elevated temperatures, making it ideal for aerospace components like turbine blades and discs.
Excellent Corrosion Resistance: Saltwater, harsh chemicals – these elements can wreak havoc on metals. BNi-5, however, stands strong. Its robust resistance to corrosion makes it perfect for marine and chemical processing applications.
Oxidation Resistance: High temperatures often lead to oxidation, a process that weakens metals. BNi-5, with its carefully chosen alloying elements, forms a protective oxide layer that shields it from degradation at elevated temperatures. This makes it perfect for applications like heat exchangers and combustors.
Good Weldability: Creating complex shapes in PM often involves joining different parts. BNi-5 exhibits good weldability, allowing PM professionals to fabricate intricate components without compromising strength.
Tailorable Microstructure: The beauty of PM lies in its ability to control the microstructure of the final product. BNi-5 powder allows for fine-tuning the grain size and distribution, further enhancing its mechanical properties for specific applications.
Here’s a table showcasing the key properties of BNi-5 powder:
Property | Description |
---|---|
High-Temperature Strength | Retains strength at elevated temperatures |
Excellent Corrosion Resistance | Resists degradation from harsh environments |
Oxidation Resistance | Forms a protective layer resisting high-temperature |
degradation | |
Good Weldability | Allows for joining PM parts without compromising |
strength | |
Tailorable Microstructure | Fine-tuning microstructure for specific applications |
Applications of BNi-5 Powder
BNi-5 powder isn’t just another pretty face in the PM world. It finds application in a wide range of demanding industries:
Aerospace: As mentioned earlier, BNi-5’s high-temperature strength and oxidation resistance make it perfect for jet engine components like turbine blades and discs. It can also be used in rocket engine parts and other aerospace applications where extreme temperatures and harsh environments are the norm.
Energy Production: Power plants, both fossil fuel and nuclear, rely on BNi-5 for critical components like turbine blades and heat exchangers. Its resistance to high temperatures and corrosion ensures reliable performance in these demanding environments.
Chemical Processing: Chemical processing plants often deal with aggressive chemicals. BNi-5’s stellar corrosion resistance makes it a valuable material for pumps, valves, and other equipment exposed to harsh chemicals.
Marine Applications: Saltwater is a nightmare for many metals. But BNi-5 thrives in this environment. It’s used in propellers, rudders, and other marine components that need to withstand the corrosive effects of seawater.
Metal Powder Options for PM beyond BNi-5
While BNi-5 shines as a superstar, the PM world offers a diverse selection of metal powders, each with its own strengths and applications. Let’s explore ten other noteworthy options:
- 316L Stainless Steel: This popular stainless steel powder offers a winning combination of corrosion resistance, affordability, and good mechanical properties. It’s widely used in automotive parts, medical devices, and general-purpose components.
- 17-4 PH Stainless Steel: This precipitation-hardening stainless steel powder boasts high strength and good corrosion resistance. After fabrication, it can be further strengthened through a simple heat treatment process. Applications include aerospace components, fasteners, and gears.
- Inconel 625: Another nickel-based superalloy like BNi-5, Inconel 625 offers exceptional high-temperature strength, oxidation resistance, and resistance to a wide range of chemicals. It’s a go-to material for demanding applications in the aerospace, chemical processing, and power generation industries.
- Titanium Grade 2: Lightweight and boasting excellent corrosion resistance, titanium grade 2 powder is a popular choice for applications demanding strength-to-weight ratio. It’s used in aerospace components, medical implants, and sporting goods.
- Copper: A highly conductive metal, copper powder finds application in electrical components like heat sinks and connectors. Additionally, its antimicrobial properties make it suitable for touch surfaces in healthcare settings.
- Aluminum Alloy 6061: This versatile aluminum alloy powder offers a good balance of strength, weight, and machinability. It’s widely used in automotive parts, electronics enclosures, and general-purpose components.
- Tool Steel: Various tool steel powders exist, each tailored for specific cutting tool applications. They offer exceptional hardness, wear resistance, and hot hardness, making them ideal for drills, dies, and punches.
- Kovar: This iron-nickel-cobalt alloy powder boasts excellent thermal expansion properties that closely match glass. It’s used for making glass-to-metal seals in electronic components and scientific instruments.
- MIM (Metal Injection Molding) Grade Powders: These specially formulated powders are designed for the MIM process, which allows for creating complex shapes with high precision. Applications include small gears, medical components, and electronic connectors.
- Biocompatible Metal Powders: The medical field is increasingly utilizing PM for creating biocompatible implants. Powders like titanium and tantalum offer excellent biocompatibility, integrating well with human tissue.
Here’s a table for easy comparison of these metal powders:
Metal Powder | Description | Key Applications |
---|---|---|
316L Stainless Steel | Affordable, corrosion-resistant, good mechanical properties | Automotive parts, medical devices, general-purpose components |
17-4 PH Stainless Steel | High strength, good corrosion resistance, precipitation-hardening capabilities | Aerospace components, fasteners, gears |
Inconel 625 | Exceptional high-temperature strength, oxidation resistance, and broad chemical resistance | Aerospace, chemical processing, power generation |
Titanium Grade 2 | Lightweight, excellent corrosion resistance, high strength-to-weight ratio | Aerospace components, medical implants, sporting goods |
Copper | Highly conductive, suitable for electrical components and antimicrobial applications | Heat sinks, connectors, touch surfaces in healthcare settings |
Aluminum Alloy 6061 | Good balance of strength, weight, and machinability | Automotive parts, electronics enclosures, general-purpose components |
Tool Steel | Exceptional hardness, wear resistance, and hot hardness for cutting tools | Drills, dies, punches |
Kovar | Excellent thermal expansion properties for glass-to-metal seals | Electronic components, scientific instruments |
MIM Grade Powders | Designed for Metal Injection Molding (MIM) process, enabling complex shapes with high precision | Small gears, medical components, electronic connectors |
Biocompatible Metal Powders | Excellent biocompatibility for medical implants | Medical implants |
Choosing the Right Metal Powder
Selecting the ideal metal powder for your PM application involves considering several factors. Here are some key questions to ask:
- Required Properties: What are the essential mechanical, physical, and chemical properties needed for your component? High-temperature strength? Corrosion resistance? Conductivity?
- Application Environment: Where will the component operate? Will it be exposed to extreme temperatures, harsh chemicals, or saltwater?
- Part Geometry: How complex is the shape of the component? Some metal powders are better suited for intricate geometries than others.
- Cost Considerations: Metal powders vary in price. Balancing cost with desired properties is crucial for budget-conscious projects.
Understanding the Pros and Cons
Each metal powder has its own set of advantages and limitations. Here’s a table highlighting some key pros and cons of the listed options:
Metal Powder | Pros | Cons |
---|---|---|
316L Stainless Steel | Affordable, readily available, good corrosion resistance | Lower strength compared to some other options |
17-4 PH Stainless Steel | High strength, good corrosion resistance, tailorable properties through heat treatment | More complex processing compared to 316L |
Inconel 625 | Exceptional high-temperature performance, broad chemical resistance | Higher cost compared to many other options |
Titanium Grade 2 | Lightweight, excellent corrosion resistance, biocompatible | Higher cost compared to steel options |
Copper | Highly conductive, good for electrical applications, antimicrobial properties | Lower strength compared to most other options, prone to oxidation at high temperatures |
Aluminum Alloy 6061 | Good balance of properties, widely available, good machinability | Lower strength compared to steel options |
Tool Steel | Exceptional hardness, wear resistance, diverse options for specific cutting tool needs | Limited applications outside of cutting tools, often requires post-processing for best performance |
Kovar | Excellent thermal expansion match for glass, enables strong glass-to-metal seals | Limited applications outside of glass-to-metal seals |
MIM Grade Powders | Enables high precision and complex geometries, good for small parts | May require specialized equipment and expertise for MIM processing |
Biocompatible Metal Powders | Excellent biocompatibility for medical implants | May require regulatory approvals for medical device applications |
Additional Considerations:
- Powder Size and Distribution: The size and distribution of the metal powder particles significantly impact the final properties of the PM component. Finer powders generally result in denser parts with better mechanical properties. However, they can also be more challenging to process.
- Surface Finish: The surface finish of the PM component may require additional post-processing steps depending on the application. Techniques like machining, grinding, or polishing can be employed to achieve the desired surface finish.
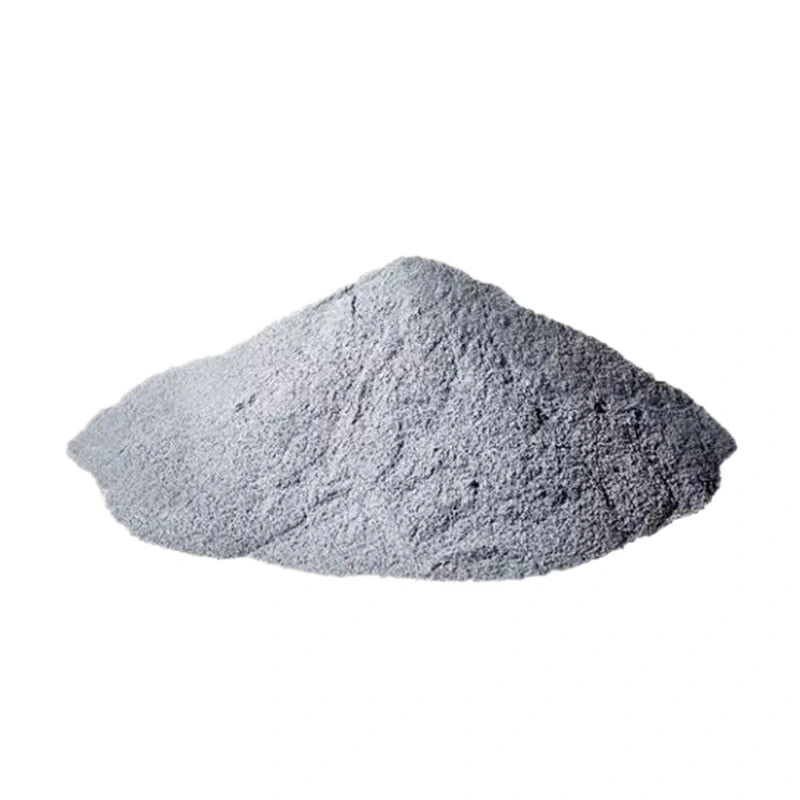
The Future of Metal Powders
The realm of metal powders for PM is constantly evolving. Researchers are developing new alloys with even more impressive properties, pushing the boundaries of what’s possible. Additionally, advancements in 3D printing technologies are opening up exciting new avenues for PM applications.
In Conclusion:
BNi-5 powder stands as a testament to the power and versatility of metal powders in PM. But it’s just one player in a vast and ever-expanding field. By understanding the properties, applications, and limitations of various metal powders, PM professionals can unlock the full potential of this innovative manufacturing technique.
Share On
MET3DP Technology Co., LTD is a leading provider of additive manufacturing solutions headquartered in Qingdao, China. Our company specializes in 3D printing equipment and high-performance metal powders for industrial applications.
Inquiry to get best price and customized Solution for your business!
Related Articles
About Met3DP
Recent Update
Our Product
CONTACT US
Any questions? Send us message now! We’ll serve your request with a whole team after receiving your message.
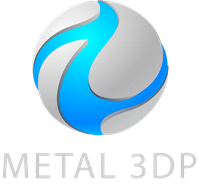
Metal Powders for 3D Printing and Additive Manufacturing