Carbonyl Nickel Powder
Table of Contents
Carbonyl nickel powder is a fine, uniform powder made by decomposing nickel carbonyl gas. With its high purity, spherical particle shape, and good flowability, carbonyl nickel powder has become an important feedstock material across electronics, metal 3D printing, magnetics, brazing, and more.
Overview of Carbonyl Nickel Powder
Carbonyl nickel powder, often abbreviated as CNP, is composed almost entirely of elemental nickel metal. Key properties and characteristics include:
Table 1: Overview of Carbonyl Nickel Powder
Properties | Details |
---|---|
Composition | 99%+ nickel |
Particle shape | Highly spherical |
Particle size | 0.5 – 12 microns |
Apparent density | 2-4 g/cm3 |
Tap density | 3-6 g/cm3 |
Purity | 99.8%+ nickel |
Flow characteristics | Free flowing |
The gas-based production process allows very precise control over particle size distribution, ensuring the powder flows smoothly for industrial handling. The lack of internal voids gives carbonyl nickel higher densities compared to other nickel metal powders.
The combination of high purity, spherical morphology, good flowability and stability make carbonyl nickel versatile for use across manufacturing, including:
Table 2: Major Applications of Carbonyl Nickel Powder
Industry | Applications |
---|---|
Electronics | Conductive pastes, coatings, solders, circuits |
Metal 3D printing | Binder jet printing, laser powder bed fusion |
Magnetic materials | Cores, shielding |
Brazing and welding | Filler material |
Thermal spray | Wires, coatings, corrosion protection |
Batteries | Electrode material, foams |
Next, we’ll explore the production process behind carbonyl nickel powder and how it achieves unique material qualities.
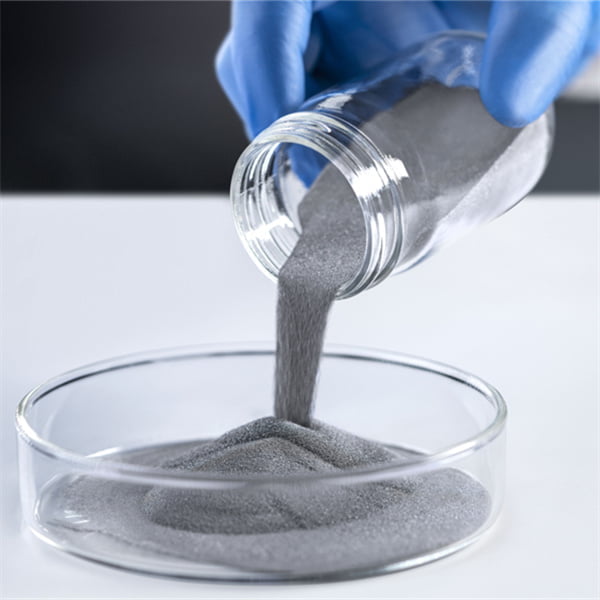
How is Carbonyl Nickel Powder Made?
Carbonyl nickel is manufactured via the chemical decomposition of nickel carbonyl gas. The specialized production process allows precise control over powder characteristics.
There are five key steps:
Table 3: Main Steps in Carbonyl Nickel Powder Production
Step | Description |
---|---|
1. Generation | Nickel carbonyl gas is generated by exposing nickel to carbon monoxide gas at 50-100°C under pressure |
2. Decomposition | The unstable nickel carbonyl gas is thermally decomposed at 180-220°C into pure nickel powder and carbon monoxide |
3. Collection | The ultra-fine nickel powder is collected and separated from gases |
4. Milling | Optional size-reduction via jet milling or ball milling |
5. Classification | Powder is air classified by particle size for different applications |
Controlling the process kinetics and gas velocities allows very uniform, spherical nickel powder particles to be generated consistently.
The next section covers the unique composition and morphological properties possible with the carbonyl process.
Composition and Properties of Carbonyl Nickel
The carbonyl process for making nickel powder achieves both high purity and excellent particle characteristics simultaneously.
Table 4: Composition and Material Properties
Parameter | Details |
---|---|
Nickel content | Up to 99.9% |
Key impurities | Carbon, oxygen, nitrogen |
Particle shape | Highly spherical |
Particle size distribution | Controllable, varying grades |
Apparent density | 2 – 4 g/cm3 |
Tap density | 3 – 6 g/cm3 |
Specific surface area | 0.3 – 10 m2/g |
Oxide content | Very low, <0.5% |
Hydrogen absorption | Minimal |
The lack of internal voids gives carbonyl nickel powder higher density compared to other nickel metal powders. This improves packing efficiency in applications like 3D printing.
By avoiding hydrogen gas exposure during production, carbonyl nickel resists hydrogen embrittlement and storage compared to electrolytic nickel. This enhances stability in battery applications.
Overall, the controlled gas-phase synthesis method creates a very pure, spheroidal nickel powder amenable for advanced applications.
Next we’ll go over particle size options available.
Particle Size Grades for Carbonyl Nickel Powders
One advantage of the carbonyl process is the tunability of particle size distribution by controlling process parameters. Carbonyl nickel powder is commercially available in different size ranges:
Table 5: Particle Size Grades of Carbonyl Nickel
Grade | Particle Size (microns) |
---|---|
Type 287 | Submicron, 0.6-0.8 μm |
Type 123 | 0.5-3 μm distribution |
Type 255 | 3-7 μm distribution |
Type 287 | 7-12 μm distribution |
The smallest grade at 0.5 microns is suited for conductive inks and pastes. Larger grades over 5 microns work better for powder bed printing processes.
By air classifying the starter powder, manufacturers can provide custom particle distributions optimized for a given application.
Now we’ll compare carbonyl nickel powder to other nickel metal powders.
How Carbonyl Nickel Compares to Other Nickel Powders
Carbonyl nickel possesses distinct advantages over other forms of nickel powder when purity and particle morphology are critical.
Table 6: Carbonyl Nickel Powder vs. Alternatives
Parameter | Carbonyl Nickel | Electrolytic Nickel | Carbonyl Iron |
---|---|---|---|
Purity | 99.8%+ | 99.7% | 99% |
Particle shape | Highly spherical | Irregular, spiky | Spherical |
Particle size control | Excellent | Moderate | Excellent |
Hydrogen absorption | Very low | High | Low |
Cost | High | Low | Low |
Electrolytic nickel made from aqueous electroplating contains more impurities, while carbonyl iron lacks nickel’s functional properties.
Carbonyl nickel strikes an optimal balance, justifying its use for conductive pastes, 3D printing, brazing, and other niche applications where quality trumps cost.
Next we’ll go over standards and specifications guiding carbonyl nickel powder production.
Standards and Specifications
Multiple standards organizations have specifications for carbonyl nickel powder, ensuring quality:
Table 7: Key Standards for Carbonyl Nickel Powder
Standard | Description |
---|---|
ASTM B831 | Standard specification for high-purity nickel powder |
ISO 4491 | Metallic powders – Determination of oxygen content by reduction methods |
ISO 4490 | Metallic powders – Determination of hydrogen content |
ISO 4494 | Metallic powders – Determination of sulfur content |
These standards test powder composition, impurity levels, particle size distribution, density, and handling properties relevant to industrial applications.
Following standardized testing protocols allows buyers to compare quality across suppliers.
Next we’ll highlight some leading global suppliers.
Top Suppliers of Carbonyl Nickel Powder
There are over a dozen commercial producers manufacturing carbonyl nickel powder worldwide. Some top suppliers include:
Table 8: Leading Suppliers of Carbonyl Nickel Powder
Company | Location |
---|---|
Vale Canada Limited | Canada |
Jilin Jien Nickel Industry Co., Ltd. | China |
Beijing Xingrongyuan Technology Co., Ltd. | China |
Jien International Corporation | United States |
INCO Special Products | United Kingdom |
Vale Canada is a well-known producer. Jilin Jien and Jien International focus specifically on carbonyl nickel and copper powders out of China and the US.
Prices range widely from $5 per pound for bulk purchases to $50 per pound for ultra-high purity grades.
Plating technologies and battery companies often negotiate discounted supply contracts with powder manufacturers directly.
Now we’ll examine the pros and cons of using carbonyl nickel powder.
Advantages and Limitations of Carbonyl Nickel
Like any specialized material, carbonyl nickel brings unique benefits along with caveats across cost and processing.
Table 9: Pros and Cons of Carbonyl Nickel Powder
Advantages | Disadvantages |
---|---|
Extremely high purity | Relatively expensive |
Spherical morphology | Limited global production |
Excellent flow characteristics | Requires handling care |
More chemically stable | Challenging to alloy |
Custom particle distribution |
Cost is the primary downside, especially for smaller buyers without bulk purchasing power. However, carbonyl nickel enables performance not possible with cheaper alternatives.
For critical applications in aerospace components, medical implants, or battery electrodes where quality trumps price concerns, carbonyl nickel is often the top choice.
Interest in carbonyl nickel continues growing – the next section explores emerging trends across industries developing new uses for this ultra-pure powder.
Current Trends and Future Outlook
Several key trends are raising the profile of carbonyl nickel powders to enable new technologies:
Rising Adoption in 3D Printing
Binder jet and laser powder bed fusion rely on spherical powders to achieve high packing density and smooth flow. Carbonyl nickel’s excellent morphology makes it an ideal material as metal 3D printing expands.
Advancing 5G Infrastructure
5G smartphones and networks utilize more antennas and sensors using conductive nickel pastes and solders. This drives demand for ultra-fine carbonyl nickel powders.
Electric Vehicle Battery Innovations
Pure metallic nickel is being implemented in battery electrodes and current collectors to increase power density and charging rates. This leverages carbonyl nickel’s purity and hydrogen resistance.
Growth in Microelectronics
Shrinking semiconductor components call for smaller, purer metal powders for printed circuits and conductive adhesive films. Submicron carbonyl nickel usage grows.
Expanding Use in Multi-Layer Ceramic Capacitors
MLCCs in electronics require nickel metal layers, which are fabricated by screen printing carbonyl nickel pastes and firing.
Let’s explore the industry trends and future outlook for carbonyl nickel in each application area.
Carbonyl Nickel Powder for 3D Printing
3D printing via binder jetting can print carbonyl nickel without melting, retaining its purity and properties. This allows printing low-cost nickel 201 stainless steel parts.
Laser powder bed fusion also utilizes carbonyl nickel powder with a high absorption rate during sintering/melting. This unlocks printing of custom nickel superalloys.
Table 10: Carbonyl Nickel Powder for 3D Printing
Process | Benefits | Trends |
---|---|---|
Binder jetting | Low melting point, good binder compatibility | Adoption for stainless steel prototyping |
Laser powder bed fusion | Excellent absorption and densification | Materials development for aerospace |
With demand for metal 3D printing projected to reach $15 billion by 2030, carbonyl nickel powders will play an integral role across startups and industrial manufacturers.
Carbonyl Nickel Pastes for Advanced Electronics
Carbonyl nickel micron and sub-micron powders discern small, lightweight electronics requiring ultra-fine printed circuits and connections.
Table 11: Carbonyl Nickel for Printed Electronics
Application | Benefits | Trends |
---|---|---|
Conductive inks/pastes | High conductivity, stability | Growth in wearables, sensors |
EMI shielding | Excellent attenuation | Expansion with 5G, EVs, LEDs |
Printed antennas | High frequency response | Higher frequencies, miniaturization |
Development is very active creating novel functional inks with carbonyl nickel for flexible hybrid electronics.
Carbonyl Nickel in EV Battery Innovations
Nickel is critical for the cathode chemistry of most lithium-ion batteries. Carbonyl nickel enables higher energy densities as EVs demand increased range.
Table 12: Carbonyl Nickel for EV Batteries
Component | Benefits | Trends |
---|---|---|
Cathodes | Stable cycling | Transitioning to higher nickel cathodes like NCA, NMC |
Anodes | Nanostructuring boosts power | Exploring lithium metal anodes |
Current collectors | Corrosion resistant conductivity | Shift from copper to nickel |
Purer metallic nickel from carbonyl powder improves battery storage capacity, charging speed, and lifespans to push electric vehicle mainstream adoption.
As global EV sales rise exponentially this decade, demand is rocketing for advanced battery materials like carbonyl nickel.
Surging Use in MLCC Components
Multi-layer ceramic capacitors utilize printed nickel electrodes stacked in layers then co-fired into tiny, high-capacity components vital across electronics.
Table 13: Carbonyl Nickel for MLCCs
Function | Benefits | Trends |
---|---|---|
Electrode printing | High conductivity at micron scale | Miniaturization requiring finer prints |
Stacked layer co-firing | Excellent high temperature stability | Higher layer counts raising capacity |
Making terminations | Solderable high-purity nickel | Surface-mount需求上升 |
As one of the world’s most manufactured components, surging MLCC demand leads to increasing consumption of carbonyl nickel powder.
Summary of Carbonyl Nickel Powder
In summary, carbonyl nickel powder provides an ultra-pure, spherical nickel feedstock vital for advanced applications across industries:
Electronics: Conductive inks, EMI shielding, fine pitch PCBs, MLCCs Additive Manufacturing: Binder jet printing, laser powder bed fusion Automotive: Cables, connectors, batteries, sensors Aerospace: Superalloy components, thermal coatings
With excellent particle size control and powder characteristics, carbonyl nickel enables emerging technologies and higher-performance products across sectors.
While relatively expensive, its unparalleled purity justifies use in applications where quality outweighs cost.
With accelerating commercial adoption from EVs to 5G infrastructure, global demand for carbonyl nickel powder has robust growth prospects this decade across both legacy and novel uses.
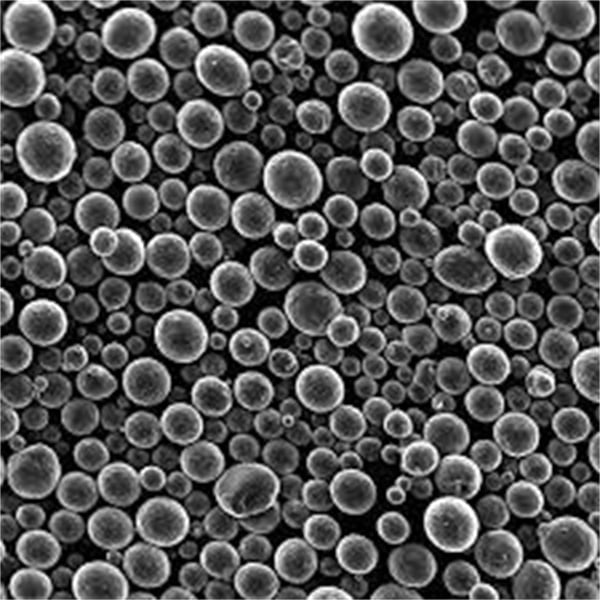
FAQs
Here are answers to some frequently asked questions about carbonyl nickel powder:
Q: What are the major advantages of carbonyl nickel powder?
A: Extremely high purity, highly spherical particle shape, customizable particle size distribution, good powder flow and packing density, low levels of hydrogen absorption.
Q: What industries use carbonyl nickel powder?
A: Primary users include electronics, 3D printing, batteries/energy storage, multilayer ceramic capacitors, brake pads, magnets, welding, thermal spray.
Q: What is the typical price per pound of carbonyl nickel powder?
A: Base pricing starts around $5 per pound for bulk purchases of industrial-grade powder. Specialty grades with finer particle size or higher purity range from $10 to $50+ per pound.
Q: Does carbonyl nickel powder require special handling or storage?
A: Inert gas blanketing is ideal to prevent oxidation. Due to potential dust explosivity, avoid ignition sources in storage areas and equipment. Follow safety protocols for respiratory, explosion, and powder handling hazards.
Q: What are common applications for ultra fine sub-micron carbonyl nickel powder?
A: Sub-micron grades under 1 micron are utilized in conductive inks and pastes for printed electronics, circuit boards, capacitors, EMI shielding and more. The fine uniform powder enables resolution of microscale features.
Q: Is it possible to alloy carbonyl nickel powder?
A: Alloying via standard powder metallurgy techniques can be challenging due to high oxygen affinity. Special reducing atmospheres and temperatures may be required. Elemental blends suitable for alloy formation during sintering can be produced.
Share On
MET3DP Technology Co., LTD is a leading provider of additive manufacturing solutions headquartered in Qingdao, China. Our company specializes in 3D printing equipment and high-performance metal powders for industrial applications.
Inquiry to get best price and customized Solution for your business!
Related Articles
About Met3DP
Recent Update
Our Product
CONTACT US
Any questions? Send us message now! We’ll serve your request with a whole team after receiving your message.
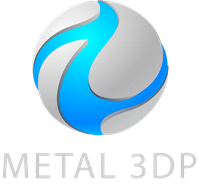
Metal Powders for 3D Printing and Additive Manufacturing