Detailed introduction to CVD
Table of Contents
Imagine building intricate structures atom by atom, meticulously crafting layers of material so thin they are invisible to the naked eye. This is the realm of chemical vapor deposition (CVD), a powerful technology that has revolutionized countless industries by enabling the creation of high-performance, precisely engineered materials.
Specific Introduction to Chemical Vapor Deposition
CVD, in essence, is a thin-film deposition technique where a gaseous precursor undergoes a chemical reaction within a chamber, depositing a solid film on a substrate. Think of it like painting with invisible vapor instead of traditional paintbrushes and liquids. This seemingly simple process, however, unlocks a world of possibilities, allowing for the creation of materials with specific properties like superior conductivity, enhanced wear resistance, and tailored optical characteristics.
The Three Main Steps of CVD Process
While the specifics of CVD can vary depending on the desired material and application, the core process generally follows three key steps:
- Precursor Delivery: Gaseous precursors, containing the elements that will form the deposited film, are introduced into the chamber. These precursors can be single elements like silicon or complex molecules containing various elements.
- Reaction and Deposition: The precursors are subjected to various activation methods, such as heat, plasma, or light, which trigger a chemical reaction. This reaction breaks down the precursors and allows the desired elements to combine and form the solid film on the substrate.
- Purge and Exhaust: After the deposition is complete, any unreacted precursor gases and byproducts are removed from the chamber using a vacuum system.
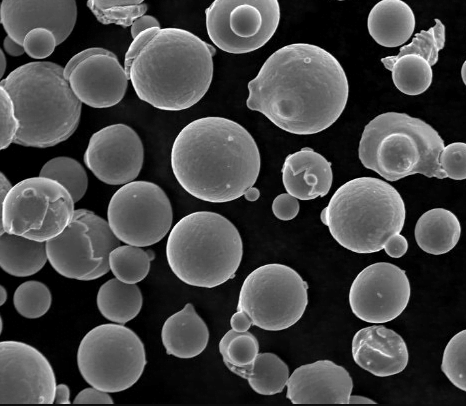
Many Advantages of CVD Process
CVD offers several distinct advantages over other thin-film deposition techniques, making it a preferred choice in various applications:
- High Conformality: CVD allows for the deposition of uniform and conformal films, even on complex three-dimensional surfaces. This is because the gaseous precursors can reach all nooks and crannies of the substrate, unlike techniques like physical vapor deposition (PVD) that might struggle with intricate geometries.
- Precise Control: The process parameters in CVD, such as temperature, pressure, and precursor flow rates, can be precisely controlled, allowing for the tailoring of film properties like thickness, composition, and crystallinity. This level of control enables the creation of highly customized and engineered materials.
- Purity and Reproducibility: CVD processes typically take place in a controlled environment, minimizing contamination and ensuring high purity of the deposited films. Additionally, the precise control of process parameters allows for excellent reproducibility, ensuring consistent film properties across multiple batches.
- Wide Material Range: CVD can be used to deposit a vast array of materials, including metals, semiconductors, dielectrics, and even polymers. This versatility makes it a valuable tool for various industries, from microelectronics to solar energy.
Some Disadvantages of CVD Process
Despite its numerous advantages, CVD also has some limitations:
- High Cost: Setting up and maintaining a CVD system can be expensive due to the specialized equipment and precise control systems required.
- Slower Deposition Rates: Compared to some other deposition techniques, CVD can have slower deposition rates, which can be a drawback for high-volume production applications.
- Limited Substrate Compatibility: Not all materials are suitable for CVD due to the high temperatures or reactive environments involved in the process.
Specific Metal Powders Used in CVD
CVD can be used to deposit a wide variety of metal films, each with unique properties and applications. Here are ten specific metal powder models commonly used in CVD processes:
Metal Powder Model | Description and Properties | Applications |
---|---|---|
Tungsten (W) | Known for its high melting point, excellent thermal stability, and good electrical conductivity. | Used in semiconductor devices, high-temperature filaments, and wear-resistant coatings. |
Molybdenum (Mo) | Offers high melting point, good corrosion resistance, and reasonable electrical conductivity. | Used in electronics packaging, heat sinks, and refractory applications. |
Tantalum (Ta) | High melting point, excellent corrosion resistance, and good compatibility with other materials. | Used in capacitors, microelectromechanical systems (MEMS), and biomedical implants. |
Chromium (Cr) | Offers good wear resistance, corrosion resistance, and hardness. | Used in decorative and protective coatings, cutting tools, and wear parts. |
Titanium (Ti) | Biocompatible, lightweight, and offers good strength and corrosion resistance. | Used in biomedical implants, aerospace components, and sporting goods. |
Aluminum (Al) | Highly reflective, lightweight, and good conductor of electricity. | Used in metallization for integrated circuits, mirrors, and heat sinks. |
Copper (Cu) | Excellent electrical conductivity and thermal conductivity. | Used in electrical wiring, interconnects in microelectronics, and heat exchangers. |
Nickel (Ni) | Good electrical conductivity, magnetic properties, and corrosion resistance. | Used in electroplating, magnetic recording media, and corrosion-resistant coatings. |
Gold (Au) | Excellent electrical conductivity, corrosion resistance, and biocompatibility. | Used in electrical connectors, integrated circuits, and medical devices. |
Platinum (Pt) | High melting point, excellent catalytic properties, and corrosion resistance. | Used in catalytic converters, fuel cells, and temperature sensors. |
Applications of CVD: Shaping Industries
CVD’s versatility extends to various industries, playing a crucial role in numerous applications:
- Semiconductors: CVD is essential for creating the intricate layers of transistors, capacitors, and other building blocks of integrated circuits (ICs). The precise control and high purity offered by CVD are critical for ensuring the reliable and efficient operation of modern electronics.
- Microelectromechanical Systems (MEMS): MEMS devices integrate mechanical elements with electronics on a microscopic scale. CVD enables the deposition of thin films for various MEMS components, such as movable beams, diaphragms, and electrodes.
- Solar Cells: CVD is used to deposit thin films of materials like silicon, silicon nitride, and various transparent conductive oxides, which are essential components for capturing and converting sunlight into electricity.
- Optical Coatings: Anti-reflective coatings, mirrors, and filters used in various optical devices can be created using CVD. The precise control over film thickness and composition allows for the tailoring of optical properties for specific applications.
- Cutting Tools and Wear-Resistant Coatings: CVD coatings can significantly enhance the wear resistance and hardness of cutting tools, extending their lifespan and improving cutting performance. Additionally, CVD is used to create wear-resistant coatings for various components in machinery and equipment.
- Biomedical Implants: CVD plays a crucial role in the development of biocompatible implants, such as artificial joints and stents. The ability to deposit thin films with specific properties like biocompatibility and corrosion resistance is crucial for successful implantation and long-term functionality.
These are just a few examples, and as technology continues to evolve, we can expect CVD to play an even greater role in shaping various industries and developing innovative materials for the future.
Beyond the Basics: Advanced CVD Techniques
The world of CVD extends beyond the core three-step process. To achieve even greater control and access a wider range of materials, various advanced CVD techniques have been developed:
- Plasma-Enhanced CVD (PECVD): This technique introduces plasma into the reaction chamber, which can increase the reaction rate, improve film uniformity, and enable the deposition of materials that are difficult to deposit using thermal CVD alone.
- Atomic Layer Deposition (ALD): ALD is a highly precise technique where the precursor is introduced in a self-limiting manner, allowing for the deposition of atomically thin films with exceptional uniformity and control over thickness.
- Metal Organic CVD (MOCVD): This technique utilizes metal-organic precursors, offering advantages like lower deposition temperatures and the ability to deposit complex materials with specific compositions.
By exploring these advanced techniques, researchers and engineers can push the boundaries of what’s possible with CVD, paving the way for the development of even more sophisticated and functional materials.
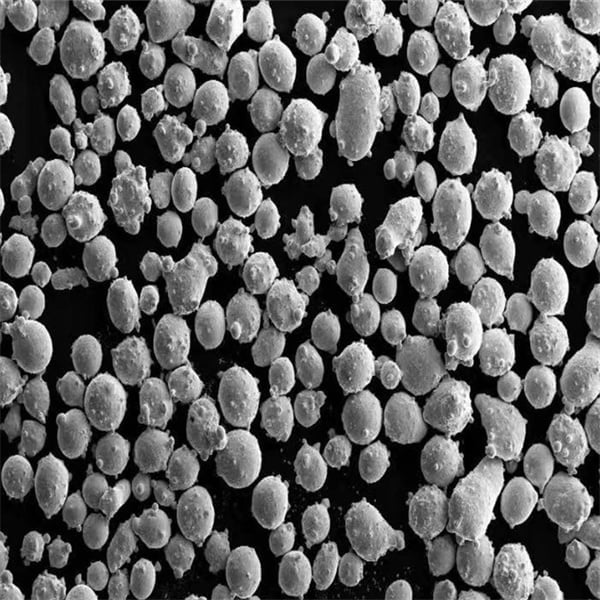
FAQs
Here are some frequently asked questions about CVD, answered in a table format for easy reference:
Question | Answer |
---|---|
What are some alternatives to CVD? | Other thin-film deposition techniques include physical vapor deposition (PVD), electroplating, and spin coating. Each technique has its own advantages and limitations, and the best choice for a specific application depends on various factors like desired material properties, cost, and production requirements. |
What safety precautions are important during CVD? | CVD processes often involve hazardous materials and high temperatures. It’s crucial to follow proper safety protocols, including wearing appropriate personal protective equipment (PPE), working in a well-ventilated environment, and adhering to established safety procedures for handling chemicals and operating equipment. |
What is the future of CVD? | As research and development continue, we can expect advancements in CVD technology leading to: * Development of new precursor materials enabling deposition of even wider range of materials. * Further improvements in process control and uniformity, allowing for even more precise creation of thin films. * Integration of CVD with other manufacturing processes for the development of complex and multifunctional devices. |
Conclusion
Chemical vapor deposition (CVD) stands as a testament to human ingenuity. It allows us to build structures atom by atom, creating materials with properties tailored to specific needs. From the intricate circuits that power our devices to the life-saving implants that mend our bodies, CVD plays a crucial role in shaping our world in countless ways.
As we delve deeper into the world of materials science and explore new technological frontiers, CVD will undoubtedly continue to evolve and play an even greater role in shaping the future. With advancements in precursor materials, process control, and integration with other technologies, the possibilities for CVD are vast and hold immense potential for innovation and progress.
So, the next time you hold a smartphone in your hand or marvel at the sleek design of a modern aircraft, remember the invisible layers of meticulously crafted materials, each a testament to the power of chemical vapor deposition, a microscopic marvel with a macro impact on our world.
Share On
MET3DP Technology Co., LTD is a leading provider of additive manufacturing solutions headquartered in Qingdao, China. Our company specializes in 3D printing equipment and high-performance metal powders for industrial applications.
Inquiry to get best price and customized Solution for your business!
Related Articles
About Met3DP
Recent Update
Our Product
CONTACT US
Any questions? Send us message now! We’ll serve your request with a whole team after receiving your message.
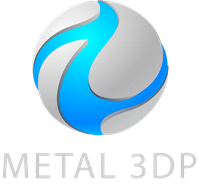
Metal Powders for 3D Printing and Additive Manufacturing
COMPANY
PRODUCT
cONTACT INFO
- Qingdao City, Shandong, China
- [email protected]
- [email protected]
- +86 19116340731