CVD Nickel Powder: A Comprehensive Guide
Table of Contents
CVD nickel powder, a revolutionary material engineered through Chemical Vapor Deposition (CVD), has captivated industries with its unique properties and diverse applications. Imagine microscopic particles of nickel, meticulously crafted through precise chemical reactions, offering exceptional qualities unlike any other nickel powder. This guide delves into the fascinating world of CVD nickel powder, exploring its creation, characteristics, applications, and the very factors that make it stand out.
Unveiling the Magic: CVD Nickel Powder Creation
CVD, a sophisticated technique, transforms gaseous precursors into solid materials on a heated substrate. In the case of CVD nickel powder, nickel chloride (NiCl₂) is heated, releasing nickel and chlorine atoms. These atoms then react with hydrogen gas (H₂), forming nickel (Ni) and hydrochloric acid (HCl). The nickel atoms deposit on a cool surface, forming the coveted ultra-fine nickel powder.
Here’s a captivating analogy: Picture yourself roasting marshmallows over a campfire. The heat breaks down the sugar molecules in the marshmallow, releasing smaller sugar fragments. These fragments then react with the oxygen in the air, forming a brown, crispy layer – the delicious char on your marshmallow. Similarly, the CVD process breaks down the nickel chloride molecule, releasing nickel atoms that react to form the coveted nickel powder.
A Closer Look: Composition, Properties, and Characteristics
CVD nickel powder boasts exceptional qualities that set it apart from conventionally produced powders. Let’s delve deeper into its composition, properties, and unique characteristics:
Composition | Properties | Characteristics |
---|---|---|
Primarily Nickel (Ni) | High purity (>99.5%) | Ultra-fine particle size (10-100 nm) |
Trace elements (varies) | High surface area (>10 m²/g) | Spherical morphology |
– | Good electrical conductivity | Excellent packing density |
– | High thermal conductivity | High chemical purity |
– | Magnetic properties (tailorable) | Superior sinterability |
Imagine holding a single grain of CVD nickel powder in your hand, smaller than a single bacterium. Despite its diminutive size, this tiny particle packs a powerful punch. Its high surface area, akin to having a mountain range crammed onto a tiny island, allows for exceptional reactivity and unique interactions with other materials. The spherical shape, analogous to tiny marbles, facilitates smooth flow and efficient packing within various applications.
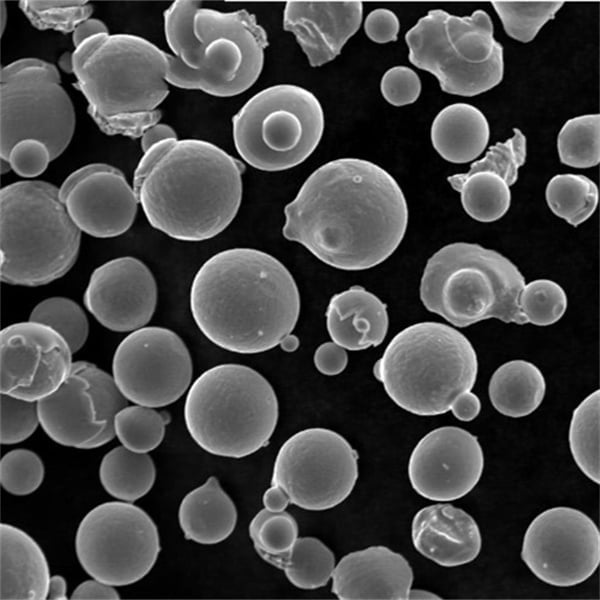
A Spectrum of Applications: Unleashing the Potential
CVD nickel powder‘s unique properties translate into a diverse array of applications across various industries. Let’s explore some of the most prominent uses:
Application | Reasoning | Benefits |
---|---|---|
Lithium-ion batteries | High surface area, improved conductivity | Enhanced energy density, faster charging rates |
Fuel cells | Tailorable magnetic properties | Efficient conversion of chemical energy into electrical energy |
Electromagnetic shielding | Excellent conductivity, high purity | Effective attenuation of electromagnetic interference (EMI) |
Additive manufacturing (3D printing) | Spherical morphology, high packing density | Smooth printing process, creation of complex structures |
Magnetic recording media | Tailorable magnetic properties | High-density data storage, improved recording performance |
Catalyst supports | High surface area, superior sinterability | Enhanced catalytic activity, efficient utilization of catalysts |
Imagine the possibilities: From powering our next generation of electric vehicles to shielding sensitive electronics, CVD nickel powder is paving the way for advancements across various sectors. Its versatility and unique properties make it a valuable material for pushing the boundaries of innovation.
Specifications, Sizes, Grades, and Standards
CVD nickel powder comes in various specifications, sizes, grades, and adheres to specific industry standards:
Specification | Description | Example |
---|---|---|
Purity | Percentage of nickel content | >99.5% |
Particle size | Average diameter of particles | 20 nm |
Surface area | Total surface area per unit mass | 20 m²/g |
Bulk density | Mass per unit volume of the powder | 1.5 g/cm³ |
Grade | Defines specific properties for various applications | Battery grade, catalyst grade |
Standards | Industry-recognized specifications | ASTM B880, MPIF Standard 06 |
Choosing the right CVD nickel powder requires careful consideration of its specifications and desired application. For instance, battery applications demand high purity and specific particle size distributions, while catalyst supports might prioritize high surface area and tailorable morphologies.
Comparing CVD Nickel Powder with Other Options
While CVD nickel powder shines brightly, it’s crucial to understand its strengths and limitations compared to other nickel powder options:
Comparison Point | CVD Nickel Powder | Other Nickel Powder Options | Advantages (CVD) | Disadvantages (CVD) |
---|---|---|---|---|
Production method | Chemical Vapor Deposition | Electroplating, reduction, atomization | High purity, controlled morphology | Higher cost, complex production process |
Particle size | Ultra-fine (10-100 nm) | Varies (micrometers) | Higher surface area, improved reactivity | Limited particle size range |
Sphericity | High | Varies | Improved packing density, smoother flow | May require additional shaping steps |
Purity | Very high (>99.5%) | Varies (95-99%) | Reduced contamination, consistent performance | May require additional purification steps |
Applications | Lithium-ion batteries, fuel cells, EMI shielding, 3D printing | Electrodes, catalysts, brazing alloys, pigments | Tailored properties for specific applications | Higher production cost limits wider adoption |
CVD nickel powder stands out for its exceptional purity, controlled size and morphology, and superior properties like high surface area and sphericity. However, its complex production process and higher cost compared to other options might limit its widespread use in certain applications.
The Challenge of CVD Production of Nickel Powder
Despite its remarkable qualities, CVD nickel powder production faces specific challenges:
- High capital and operational costs: Setting up and maintaining CVD equipment requires significant investment, making it less accessible to smaller-scale manufacturers.
- Scalability limitations: Scaling up CVD production to meet large-scale demands can be challenging, posing a hurdle for high-volume applications.
- Process control complexity: Maintaining precise control over various CVD parameters is crucial for consistent powder quality, requiring expertise and sophisticated monitoring systems.
These challenges are actively being addressed by researchers and manufacturers through innovative solutions and process optimizations. With continued advancements, CVD nickel powder production is poised to become more efficient and cost-effective, paving the way for wider adoption across various industries.
Advantages and Limitations
CVD nickel powder offers a multitude of advantages over conventional options, but it’s essential to acknowledge its limitations to make informed decisions:
Advantages:
- Exceptional purity: Minimizes contamination and ensures consistent performance in various applications.
- Tailorable properties: Allows fine-tuning of particle size, morphology, and surface area for specific needs.
- High surface area: Enhances reactivity, efficiency, and compatibility with other materials.
- Excellent packing density: Enables the creation of dense and high-performance components.
- Spherical morphology: Facilitates smooth flow and efficient processing in various applications.
Limitations:
- Higher production cost: Compared to other nickel powder options, CVD can be more expensive.
- Complex production process: Requires specialized equipment and expertise, limiting accessibility.
- Scalability limitations: Scaling up production for high-volume applications can be challenging.
Understanding these advantages and limitations is crucial for making informed decisions regarding the appropriate nickel powder for your specific needs. In some cases, the superior properties and performance of CVD nickel powder might outweigh the higher cost, while other applications might benefit from the cost-effectiveness and easier scalability of conventional options.
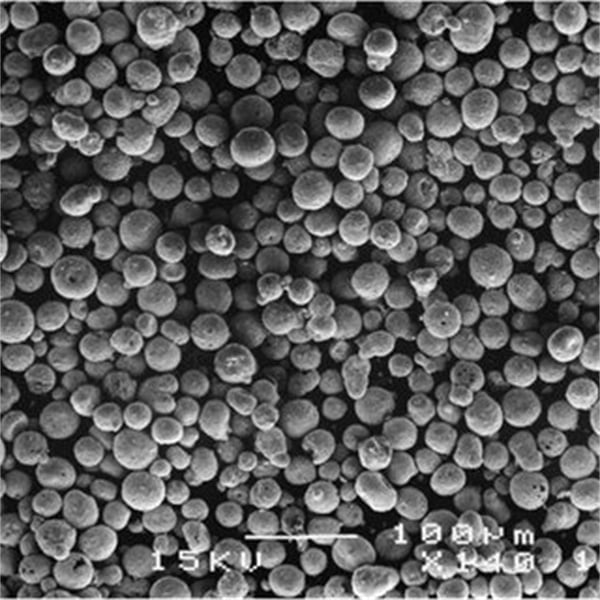
Emerging Applications of CVD Nickel Powder
CVD nickel powder, with its unique properties and potential for further development, is poised to play a significant role in several emerging applications:
1. Advanced battery technology: The high surface area and tailorable properties of CVD nickel powder make it a promising candidate for next-generation lithium-ion batteries. These powders can enhance battery performance by enabling faster charging rates, higher energy density, and improved cycle life. Additionally, research is ongoing to explore the use of CVD nickel powder in other battery chemistries, such as sodium-ion and lithium-sulfur batteries, potentially revolutionizing the energy storage landscape.
2. Hydrogen fuel cells: The development of efficient and cost-effective hydrogen fuel cells is crucial for the transition towards clean energy. CVD nickel powder, with its superior catalytic properties and ability to be tailored for specific reactions, can be used as catalyst supports in fuel cells. This can improve the efficiency of hydrogen conversion to electricity, paving the way for a more sustainable future.
3. 3D printing and additive manufacturing: The intricate structures and complex geometries achievable through 3D printing require advanced materials with specific properties. CVD nickel powder, with its spherical morphology and excellent flow characteristics, is well-suited for additive manufacturing processes. Additionally, its high purity and tunable properties allow for the creation of functional components with tailored mechanical and electrical characteristics, pushing the boundaries of 3D printing capabilities.
4. Sensor technology: The high surface area and excellent electrical conductivity of CVD nickel powder make it a valuable material for developing next-generation sensors. These powders can be used in various sensor types, including gas sensors, biosensors, and pressure sensors, offering enhanced sensitivity, faster response times, and improved detection capabilities.
5. Space exploration and aerospace applications: The demanding environment of space necessitates the use of lightweight and high-performance materials. CVD nickel powder, with its superior strength-to-weight ratio and tailorable properties, can be utilized in various aerospace applications, including spacecraft components, heat shields, and rocket engine parts.
These are just a few examples of the exciting possibilities that CVD nickel powder holds for the future. As research and development efforts continue, we can expect to see even more innovative and groundbreaking applications emerge, shaping various industries and contributing to advancements in technology and sustainability.
Conclusion
CVD nickel powder, with its exceptional properties and versatility, presents a compelling proposition for various industries. Its ability to be tailored to specific needs, coupled with its ongoing development and exploration of new applications, positions it as a material with immense potential to shape the future. Whether it’s revolutionizing energy storage, powering cleaner and more efficient vehicles, or enabling the creation of sophisticated sensors and advanced 3D-printed structures, CVD nickel powder is poised to play a significant role in the technological advancements and innovations of tomorrow.
FAQ
1. What are the environmental considerations of CVD nickel powder production?
CVD production can involve the use of hazardous chemicals and generate waste products. However, advancements are being made to minimize environmental impact, such as employing closed-loop systems and utilizing sustainable precursors.
2. How can I learn more about the safety precautions when handling CVD nickel powder?
As with any fine powder, CVD nickel powder can pose inhalation risks. Consulting the safety data sheet (SDS) provided by the manufacturer and adhering to recommended handling procedures, including the use of personal protective equipment (PPE), is crucial.
3. What are the future research directions for CVD nickel powder?
Research efforts are focused on improving production efficiency, reducing costs, and developing novel functionalities through material doping or composite structures. Additionally, exploring eco-friendly production methods and expanding applications in emerging fields like energy storage and electronics are ongoing areas of research.
4. Where can I find reliable suppliers of CVD nickel powder?
Several reputable companies specialize in the production and supply of CVD nickel powder. Consulting online directories and contacting material science distributors can help you find suitable suppliers based on your specific needs and desired specifications.
5. How does CVD nickel powder compare to other nanomaterials?
CVD nickel powder offers distinct advantages like high purity, controlled morphology, and tunable properties, making it a valuable option for various applications. However, other nanomaterials might offer unique functionalities or cost advantages, depending on the specific needs.
Share On
MET3DP Technology Co., LTD is a leading provider of additive manufacturing solutions headquartered in Qingdao, China. Our company specializes in 3D printing equipment and high-performance metal powders for industrial applications.
Inquiry to get best price and customized Solution for your business!
Related Articles
About Met3DP
Recent Update
Our Product
CONTACT US
Any questions? Send us message now! We’ll serve your request with a whole team after receiving your message.
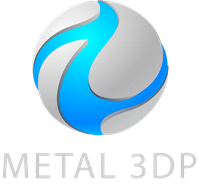
Metal Powders for 3D Printing and Additive Manufacturing