Žáruvzdorné práškové materiály
Obsah
Žáruvzdorný prášek Materiály představují specializovanou třídu anorganických nekovových materiálů s extrémně vysokou tepelnou odolností používaných v náročných průmyslových odvětvích. Tato komplexní příručka slouží technickým profesionálům a kupujícím, kteří porozumí všem klíčovým charakteristikám žáruvzdorných prášků – zahrnující typické složení, údaje o kritických vlastnostech, výrobní procesy, aplikace, specifikace a dodavatele.
Přehled žáruvzdorných práškových materiálů
Žáruvzdorné prášky obsahují jemně rozptýlené inertní nekovové materiály, které vykazují mimořádnou tepelnou stabilitu, pevnost a tvar při vysokých teplotách přesahujících 1000 °C. Klíčové podtřídy zahrnují oxidy, karbidy, nitridy a keramiku.
Kritické atributy:
- Tepelná odolnost přes 1000°C
- Odolávejte teplotním šokům
- Odolávají korozi
- Vysoký bod tání
- Udržujte strukturální integritu
Jejich výjimečné schopnosti zvyšují výkon v pecích, kotlích, pecích, reaktorech a dalších extrémních tepelných prostředích, kde tradiční materiály rychle selhávají.
Typické složení
Materiál | Role | Řada Wt% |
---|---|---|
Hliník | Tepelné vlastnosti | 40-100% |
Silica | Svažte matrici | 0-60% |
Magnesia | Odolávat zhoršení | 0-20% |
Grafit | Zvyšte odolnost proti tepelným šokům | 0-15% |
Vyvážení klíčových složek umožňuje optimalizaci charakteristik, jako je tepelná kapacita, izolace, odolnost proti erozi, bod tání a náklady.
Hlavní typy žáruvzdorných prášků
Typ | Popis |
---|---|
Sloučený | Extrémní čistota, vydrží přes 1800°C |
Spékané | Lisování/vypalování prášku, nižší cena |
Karbid křemíku | Keramika s vysokou tepelnou vodivostí |
Chromit | Odolá strusce, průniku kovu |
Zirkonie | Odolnost proti tepelným šokům |
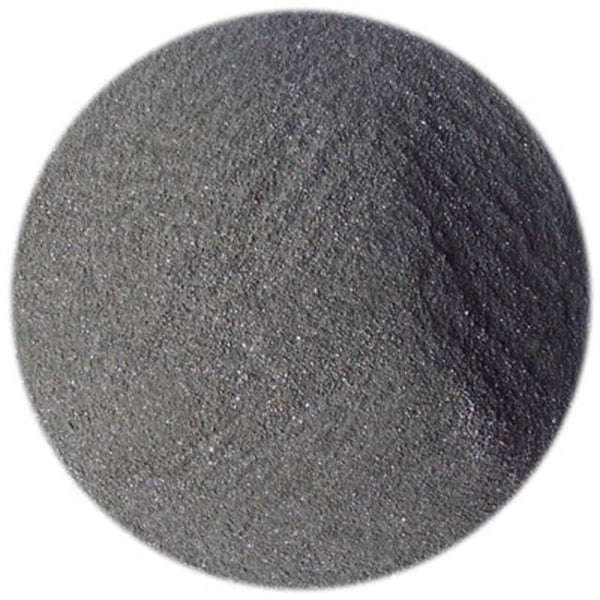
Žáruvzdorný prášek Procesy výroby materiálů
Benefit | Popis | Dopad |
---|---|---|
Díly s vysokou hustotou a tvarem blízkým síti | EBM vytváří díly s hustotou přesahující 99,5% teoretické hustoty použitého kovového prášku. Tím se eliminuje porozita (drobné vzduchové kapsy), která je běžná u jiných aditivních výrobních metod, a výsledkem jsou díly s výjimečnou pevností, únavovou odolností a rozměrovou přesností. | To umožňuje vytvářet funkční kovové součásti pro náročné aplikace v leteckém (lopatky turbín, kryty motorů), lékařském (zubní implantáty, protetika) a automobilovém průmyslu (lehké, vysoce výkonné díly). |
Vynikající mechanické vlastnosti | Vysoce vakuové prostředí a přesný proces tavení v EBM minimalizují oxidaci a kontaminaci a zachovávají přirozené vlastnosti kovového prášku. Výsledkem jsou díly s vynikající pevností v tahu, odolností proti tečení (schopnost odolávat deformaci při namáhání za vysokých teplot) a lomovou houževnatostí. | Součásti vyrobené technologií EBM snesou značné zatížení, účinně pracují při zvýšených teplotách a odolávají šíření trhlin, takže jsou ideální pro aplikace vyžadující odolnost a strukturální integritu v náročných podmínkách. |
Zpracování žáruvzdorných a reaktivních kovů | Na rozdíl od tradičních výrobních metod omezených vysokými body tání a reaktivitou vyniká EBM při zpracování náročných materiálů, jako jsou slitiny titanu, tantalu a Inconelu. Vakuové prostředí zabraňuje oxidaci a umožňuje přesnou kontrolu procesu tavení, což zajišťuje úspěšnou výrobu. | To rozšiřuje možnosti konstrukce pro průmyslová odvětví, jako je letectví a biomedicína, kde se u komponentů vyžaduje výjimečný poměr pevnosti a hmotnosti, biokompatibilita (kompatibilita s živými tkáněmi) a výkon při vysokých teplotách. |
Volnost návrhu pro složité geometrie | Přístup EBM k vytváření vrstev po vrstvách umožňuje vytvářet složité vnitřní prvky, kanály a mřížkové struktury, které jsou běžnými technikami nemožné. Tato konstrukční flexibilita optimalizuje rozložení hmotnosti, zlepšuje přenos tepla a umožňuje vytvářet komponenty s vynikající funkčností. | Tato výhoda přináší revoluci v konstrukci výrobků v průmyslových odvětvích, jako je letectví a kosmonautika, kde jsou lehké a vysoce pevné součásti se složitými chladicími kanály klíčové pro účinnost motoru. Umožňuje také vytvářet lékařské implantáty na míru, které dokonale odpovídají anatomii pacienta. |
Minimální podpůrné struktury | Vzhledem k vysoké inherentní pevnosti dílů vyráběných metodou EBM je během procesu výroby potřeba minimálních podpůrných konstrukcí. Tím se snižuje doba následného zpracování a plýtvání materiálem, jakož i riziko poškození podpůrné konstrukce konečné součásti. | To se projevuje v kratších výrobních časech, nižších celkových nákladech a schopnosti vytvářet složité geometrie, které by bylo obtížné nebo nemožné vytvořit tradičními metodami. |
Snížení množství materiálového odpadu | EBM je aditivní výrobní proces, což znamená, že se materiál přidává vrstvu po vrstvě, aby se vytvořil požadovaný tvar. Tím se minimalizuje plýtvání materiálem ve srovnání se subtraktivními technikami, jako je obrábění, kdy se pro dosažení konečného tvaru odebírá značná část surového materiálu. | Tato výhoda podporuje udržitelnost a snižuje výrobní náklady díky maximálnímu využití materiálu. Kromě toho lze nepoužitý prášek z konstrukční komory často znovu použít pro další konstrukce, což dále minimalizuje množství odpadu. |
Vlastnosti žáruvzdorných práškových materiálů
Vlastnictví | Typická hodnota |
---|---|
Bod tání | Přes 1600°C |
Hustota | 2 – 6 g/cm3 |
Pevnost v tlaku | 20 – 100 MPa |
Pevnost v ohybu | 10 – 60 MPa |
Lomová houževnatost | 2 – 10 MPa-m^1/2 |
Tepelná vodivost | 20 – 100 W/mK |
Elektrický odpor | 10^8 – 10^13 Ohm-cm |
Maximální provozní teplota | 1200 °C – 2000 °C |
Výběr určují požadavky na vyvážení, jako je bod tání, tepelná kapacita, odolnost proti tepelným šokům, hodnota izolace, chemická setrvačnost a cena.
Aplikace žáruvzdorných práškových materiálů
Průmysl | aplikace | Materiál | Využívané vlastnosti |
---|---|---|---|
Aerospace | * Lopatky turbíny * Raketové trysky * Tepelné štíty | * Wolfram * Tantal * Rhenium | * Vysoké body tání (>3000°C) * Vynikající mechanická pevnost při vysokých teplotách * Vynikající odolnost proti oxidaci |
Automobilový průmysl | * Elektrody zapalovacích svíček * Výfukové ventily * Součásti turbodmychadla | * Wolfram * Molybden * Slitiny niklu | * Vysoká elektrická vodivost * Odolnost proti opotřebení * Odolnost proti tepelným šokům |
Elektronika | * Vysokoteplotní rezistory * Kondenzátory * Elektrické kontakty | * Wolfram * Molybden * Stříbro | * Vysoké body tání * Nízký odpor * Odolnost proti erozi oblouku |
Energie | * Vyzdívky pro pece v elektrárnách * Reaktory s roztavenou solí | * Karbid křemíku * Alumina *Zirkonie | * Vynikající tepelná vodivost * Vysoká chemická stabilita * Odolnost vůči roztaveným solím |
Lékařský | * Náhrady kyčlí a kolen * Zubní implantáty * Radiační stínění | * Titanové slitiny * Tantal * Wolfram | * Biokompatibilita * Vysoký poměr pevnosti a hmotnosti * Opacity rentgenového záření |
Chemické zpracování | * Reaktory pro drsná chemická prostředí * Vysokoteplotní potrubí * Výměníky tepla | * Tantal *Zirkonium * Slitiny niklu | * Odolnost proti korozi * Vysoká pevnost při zvýšených teplotách * Výborná tvarovatelnost |
Nástroje | * Řezné nástroje pro vysoce pevné materiály * Zápustky pro tváření kovů * Formy na sklo a keramiku | * Karbid wolframu * Nitrid boru * Diamantové prášky | * Výjimečná tvrdost * Vysoká odolnost proti opotřebení * Nízká tepelná roztažnost |
Aditivní výroba | * 3D tisk složitých kovových součástí * Opravy opotřebovaných nebo poškozených dílů | * Prášky Inconel * Slitiny kobaltu a chromu * Titanové prášky | * Vysoká tekutost prášku pro přesný tisk * Vynikající slinovací vlastnosti * Mikrostruktury na míru pro specifické aplikace |
Specifikace a třídy
Vlastnictví | Popis | Klíčová hlediska pro výběr |
---|---|---|
Chemické složení | Primární stavební bloky prášku, typicky oxidy kovů, karbidy, nitridy nebo keramika. | * Dominantní oxid: Alumina (Al2O3) nabízí vynikající pevnost při vysokých teplotách, ale nižší odolnost proti tepelným šokům. Oxid křemičitý (SiO2) poskytuje dobrou chemickou odolnost, ale nižší žáruvzdornost. Magnesia (MgO) vyniká odolností proti napadení struskou, ale snadno hydratuje. * Sekundární aditiva: Vápník (CaO) zvyšuje odolnost proti strusce, zatímco chromát (Cr2O3) zlepšuje odolnost proti opotřebení. * Čistota: Vyšší čistota obecně znamená lepší výkon, ale může přinést zvýšení nákladů. |
Distribuce velikosti částic | Rozsah a rozložení jednotlivých velikostí částic v prášku. | * Průměrná velikost částic: Jemnější prášky nabízejí vynikající hustotu a povrchovou plochu pro spojení, ale mohou být náchylnější k aglomeraci (shlukování) a bránit průtokovým charakteristikám. * Distribuce velikosti částic: Úzká distribuce zajišťuje konzistentní balení a minimalizuje segregaci během zpracování. Širší distribuce mohou být prospěšné pro vyplnění dutin a zlepšení účinnosti balení. * Specifické aplikace: Procesy jako 3D tisk často vyžadují přísnější kontrolu velikosti pro optimální tok a tiskatelnost. |
Morfologie částic | Tvar a forma jednotlivých částic. | * Tvar: Sférické částice se obvykle balí efektivněji, zatímco hranaté částice mohou vytvářet mechanický do sebe zapadající efekt pro lepší pevnost. * Plocha povrchu: Prášky s větším povrchem nabízejí lepší vazebný potenciál, ale mohou také zvýšit reaktivitu. * Kontrola morfologie: Některé aplikace mohou upřednostňovat specifické tvary, jako jsou destičky pro zvýšenou tepelnou vodivost. |
Zdánlivá hustota | Hmotnost prášku na jednotku objemu v jeho sypkém, nezhutněném stavu. | * Účinnost balení: Vyšší zdánlivá hustota znamená lepší účinnost balení a může snížit spotřebu materiálu. * Tekutost: Prášky s nižší zdánlivou hustotou typicky vykazují lepší tokové vlastnosti pro snadnější manipulaci a zpracování. * Zelená síla: Zdánlivá hustota může ovlivnit pevnost v surovém stavu (předem vypálená) tvarovaných součástí. |
Sypná hustota | Hmotnost prášku na jednotku objemu po absolvování standardizovaného postupu poklepávání nebo vibrací. | * Účinnost hutnění: Sypná hustota odráží, jak dobře lze prášek zhutnit, což ovlivňuje hustotu a vlastnosti konečného produktu. * Pórovitost: Nižší objemová hmotnost indikuje vyšší pórovitost, která může ovlivnit tepelně izolační vlastnosti, ale může snížit mechanickou pevnost. * Manipulace s materiálem: Sypná hustota ovlivňuje, kolik prášku lze efektivně skladovat nebo přepravovat v daném objemu. |
Specifická gravitace | Poměr hustoty materiálu k hustotě vody. | * Žáruvzdorný výběr: Materiály s vysokou měrnou hmotností obecně nabízejí vynikající tepelnou odolnost, ale mohou být spojeny se zvýšenou hmotností. * Efektivita nákladů: Lehčí materiály s nižší měrnou hmotností mohou být nákladově efektivnější při přepravě a manipulaci. |
Žáruvzdornost | Maximální teplota, kterou materiál vydrží, aniž by se roztavil nebo ztratil strukturální integritu. | * Požadavky na přihlášku: Žáruvzdorný prášek musí v konečné aplikaci překročit očekávanou provozní teplotu. * Chemické prostředí: Některé atmosféry mohou ovlivnit žáruvzdornost. Například redukční prostředí může degradovat některé oxidy. |
Tepelná vodivost | Schopnost materiálu vést teplo. | * Řízení přenosu tepla: Vysoká tepelná vodivost může být výhodná pro aplikace vyžadující účinný přenos tepla, jako jsou výměníky tepla. * Tepelná izolace: Nízká tepelná vodivost je žádoucí pro aplikace vyžadující udržení tepla, jako jsou vyzdívky pecí. |
Tepelná roztažnost | Množství, které materiál expanduje při zahřívání. | * Odolnost proti tepelnému šoku: Materiály s nižší tepelnou roztažností jsou obecně odolnější vůči praskání a odlupování v důsledku rychlých teplotních změn. * Rozměrová stabilita: Přizpůsobení koeficientu tepelné roztažnosti žáruvzdorného prášku materiálu substrátu minimalizuje vývoj napětí během tepelného cyklování. |
Chemická odolnost | Schopnost materiálu odolávat působení korozivních chemikálií a roztavených kovů/strusek. | * Konkrétní agresivní agenti: Výběr by měl vzít v úvahu typy chemikálií, se kterými se žáruvzdorný materiál v aplikaci setká. * Kyselost/zásaditost: Kyselé nebo zásadité prostředí může degradovat specifické žáruvzdorné materiály. |
Další výkonnostní charakteristiky | Další vlastnosti v závislosti na konkrétní aplikaci, jako je odolnost proti erozi, elektrická vodivost nebo odolnost proti opotřebení. | * Zaměření na potřeby: Identifikujte kritické faktory výkonu pro zamýšlený případ použití a vyberte prášek, který v těchto oblastech vyniká. * Kompromisy: Často dochází ke kompromisům mezi různými vlastnostmi. Výběr optimálního materiálu zahrnuje upřednostnění nejdůležitějších vlastností. |
Žáruvzdorný prášek Dodavatelé materiálů
Společnost | Umístění |
---|---|
Saint-Gobain | Globální |
RHI Magnesita | Brazílie, Rakousko, Čína |
Krosaki Harima | Japonsko |
Vesuv | Evropa, Spojené státy americké |
Morgan Advanced Materials | Spojené království, Spojené státy americké |
Odhady cen
Třída | Cena za kg |
---|---|
Tabulární oxid hlinitý | $10-30 |
Karbid křemíku | $50-150 |
Zirkonie | $100-500 |
Ostatní | $20-100 |
Úspory z rozsahu ovlivňují náklady – přizpůsobené složení a přísné požadavky na kvalitu vyžadují prémie.
Výhody vs. nevýhody
Klady | Nevýhody |
---|---|
Bezkonkurenční tepelná odolnost: Žáruvzdorné prášky se mohou pochlubit výjimečnou tepelnou stabilitou, vydrží teploty přesahující 1500 °C (2732 °F) bez tavení nebo degradace. Díky tomu jsou ideální pro vyzdívky pecí, pecí, reaktorů a dalších aplikací s vysokou teplotou, kde by tradiční materiály rychle podlehly. | Křehkost a odlupování: Vzhledem ke své tuhé struktuře mohou být žáruvzdorné prášky náchylné k praskání a odštěpování, zejména při rychlých teplotních výkyvech (tepelný šok). Toto odlupování může narušit integritu obložení, což vyžaduje opravy nebo výměnu. |
Výkon na míru: Pečlivým výběrem a smícháním různých typů žáruvzdorných prášků (např. oxid hlinitý, oxid zirkoničitý, hořčík) mohou inženýři vytvářet přizpůsobené materiálové složení se specifickými vlastnostmi. To umožňuje optimalizaci faktorů, jako je tepelná odolnost, chemická kompatibilita a odolnost proti opotřebení, aby přesně odpovídaly požadavkům aplikace. | Komplexní instalace: Na rozdíl od předem tvarovaných cihel nebo tvarovek vyžadují žáruvzdorné prášky náročnější instalační proces. To často zahrnuje techniky, jako je lití, stříkání nebo vibrační lití, které vyžadují specializované vybavení a kvalifikovanou práci k dosažení husté, jednotné výstelky. |
Všestrannost ve formě a funkci: Žáruvzdorné prášky nabízejí vynikající konstrukční flexibilitu ve srovnání s prefabrikovanými součástmi. Jejich schopnost tvarování do složitých tvarů umožňuje vytváření složitých vyzdívek pecí, kelímků a dalších žáruvzdorných prvků na zakázku. | Úvahy o ceně: Suroviny a zpracovatelské techniky používané při výrobě vysoce výkonných žáruvzdorných prášků se mohou promítnout do vyšších počátečních nákladů ve srovnání s některými konvenčními žáruvzdornými materiály. |
Lehká výhoda: Žáruvzdorné prášky přispívají k výraznému snížení hmotnosti ve srovnání s tradičními cihlovými obklady. To je výhodné zejména v aplikacích, kde se nižší hmotnost promítá do zlepšené energetické účinnosti, sníženého zatížení konstrukce a snadnější manipulace během instalace. | Potenciální zdravotní rizika: Některé žáruvzdorné práškové kompozice, zejména ty obsahující oxid křemičitý nebo chromit, mohou při vdechování představovat zdravotní rizika. Při manipulaci a instalaci je zásadní zavést správné bezpečnostní protokoly a používat vhodné osobní ochranné prostředky (OOP). |
Vylepšené žáruvzdorné vlastnosti: Začleněním specifických přísad nebo využitím pokročilých výrobních technik mohou být žáruvzdorné prášky navrženy tak, aby vykazovaly vynikající vlastnosti nad rámec základní tepelné odolnosti. To může zahrnovat zlepšenou odolnost proti tepelným šokům, zvýšenou chemickou odolnost vůči roztaveným kovům nebo struskám a dokonce i samoopravné schopnosti pro prodlouženou životnost. | Zásah do životního prostředí: V závislosti na specifickém složení a výrobních metodách mohou mít některé žáruvzdorné prášky environmentální problémy spojené s jejich těžbou, zpracováním nebo likvidací. Výběr ekologických surovin a odpovědné postupy recyklace jsou důležitými faktory, které je třeba zvážit. |
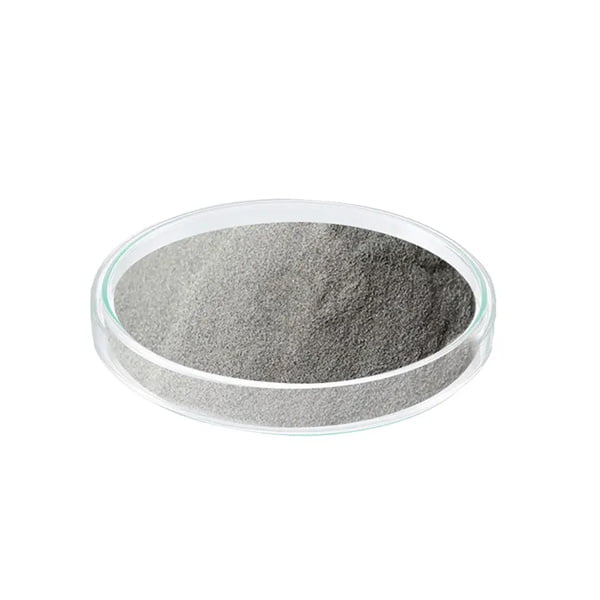
Nejčastější dotazy
Otázka: Jaký je rozdíl mezi žáruvzdornými prášky a žáruvzdornými cihlami?
Odpověď: Cihly jsou předem tvarované konsolidované konstrukce, zatímco prášky představují výchozí suroviny umožňující výrobu speciálních žáruvzdorných komponent lisováním/vypalováním nebo pokročilými metodami výroby aditiv.
Otázka: Lze všechny žáruvzdorné prášky vytisknout 3D technologií AM?
Odpověď: Ano – tryskání pojiva a tisk s přímou depozicí energie se ukázaly být kompatibilní s většinou tepelně odolných druhů oxidu hlinitého, zirkonu a karbidu křemíku pro dříve nemožné žáruvzdorné geometrie.
Otázka: Který žáruvzdorný prášek nabízí nejvyšší provozní teplotu?
Odpověď: Tavený mullit a oxid zirkoničitý s ultra vysokou čistotou spolehlivě odolávají teplotám přes 2000 °C pro nejnáročnější pece, letectví a jaderné aplikace, kde se alternativy taví nebo rozkládají.
Otázka: Jaký je rozdíl mezi syntetickými a přírodními žáruvzdornými materiály?
Odpověď: Přírodní suroviny, jako je bauxit, magnezit a jíl, musí být rozsáhle zpracovány na přesně kontrolované prášky, aby se dosáhlo zvýšené stejnoměrnosti a extrémní tepelné odolnosti, jaké jsou možné u syntetických receptur.
Závěr
Cílem této příručky bylo poskytnout holistický odkaz na žáruvzdorné prášky – speciální materiály, které překonávají omezení běžných kovů a slitin v nejžhavějších a nejagresivnějších průmyslových prostředích díky výjimečné tepelné odolnosti. Spojte se prosím s odborníkem v oboru a prodiskutujte přizpůsobení pokročilých žáruvzdorných jakostí vašim konkrétním extrémním potřebám zpracování. Možnosti sahají daleko.
Sdílet na
MET3DP Technology Co., LTD je předním poskytovatelem řešení aditivní výroby se sídlem v Qingdao v Číně. Naše společnost se specializuje na zařízení pro 3D tisk a vysoce výkonné kovové prášky pro průmyslové aplikace.
Dotaz k získání nejlepší ceny a přizpůsobeného řešení pro vaše podnikání!
Související články
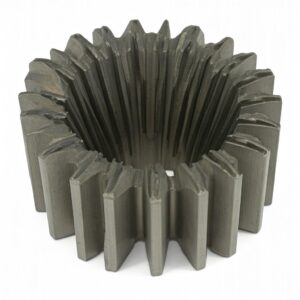
Vysoce výkonné segmenty lopatek trysek: Revoluce v účinnosti turbín díky 3D tisku z kovu
Přečtěte si více "O Met3DP
Nedávná aktualizace
Náš produkt
KONTAKTUJTE NÁS
Nějaké otázky? Pošlete nám zprávu hned teď! Po obdržení vaší zprávy obsloužíme vaši žádost s celým týmem.
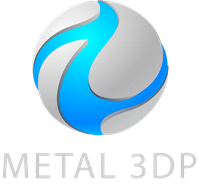
Kovové prášky pro 3D tisk a aditivní výrobu