Understanding Diffusion Alloy Powder
Table of Contents
Overview
Diffusion alloy powder is a fascinating and versatile material widely used in various industries due to its unique properties and applications. This guide will delve into the intricacies of diffusion alloy powder, exploring its composition, characteristics, types, applications, and much more. By the end, you’ll have a comprehensive understanding of why this material is so valuable and how it can be utilized effectively.
What is Diffusion Alloy Powder?
Diffusion alloy powder is a type of metallic powder where alloying elements are diffused into the surface of a base metal powder particle. This process enhances the surface properties of the base metal, leading to improved performance in various applications. The diffusion process involves heating the base metal powder and the alloying elements together at high temperatures, allowing the atoms of the alloying elements to migrate and integrate into the base metal’s surface.
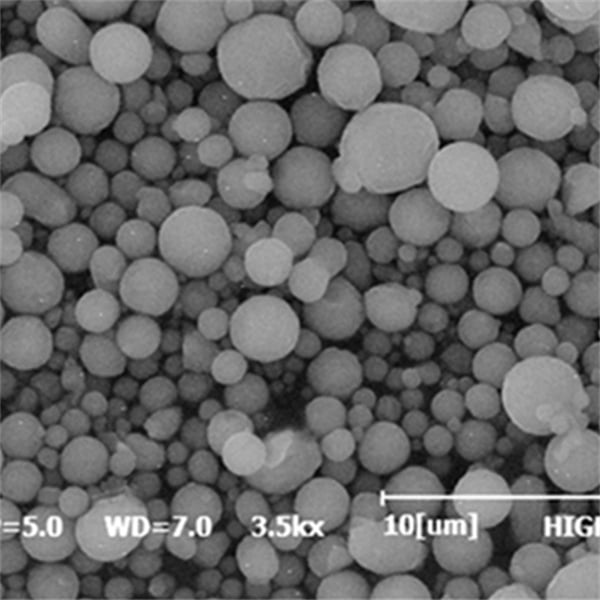
Key Components and Composition
To understand diffusion alloy powder better, let’s break down the composition and characteristics of some specific metal powder models:
Metal Powder Model | Composition | Properties | Applications |
---|---|---|---|
Iron-Copper Powder | Fe, Cu | Enhanced strength, corrosion resistance | Automotive parts, machinery components |
Nickel-Cobalt Powder | Ni, Co | High-temperature stability, wear resistance | Aerospace, gas turbines |
Tungsten Carbide Powder | W, C | Extreme hardness, high melting point | Cutting tools, mining equipment |
Stainless Steel Powder | Fe, Cr, Ni | Corrosion resistance, strength | Medical instruments, food processing |
Bronze Powder | Cu, Sn | Good conductivity, low friction | Bearings, electrical connectors |
Aluminum-Silicon Powder | Al, Si | Lightweight, high strength-to-weight ratio | Automotive, aerospace |
Titanium Alloy Powder | Ti, Al, V | High strength, biocompatibility | Medical implants, aerospace |
Molybdenum Powder | Mo | High melting point, good thermal conductivity | Furnace components, electronics |
Zinc-Aluminum Powder | Zn, Al | Good corrosion resistance, lightweight | Galvanizing, die casting |
Chromium Powder | Cr | High hardness, corrosion resistance | Hard-facing, wear-resistant coatings |
Properties and Characteristics
The properties of diffusion alloy powder vary based on the composition and the specific alloying elements used. Here are some common properties:
- Enhanced Mechanical Strength: The diffusion process often increases the hardness and tensile strength of the base metal.
- Corrosion Resistance: Many diffusion alloy powders are designed to resist oxidation and corrosion, making them suitable for harsh environments.
- Thermal Stability: Certain alloy powders, such as those containing nickel or tungsten, can withstand high temperatures without degrading.
- Wear Resistance: Powders like tungsten carbide are known for their exceptional wear resistance, ideal for cutting and grinding tools.
Applications of Diffusion Alloy Powder
Diffusion alloy powders find applications across various industries. Here are some common uses:
Application Area | Description |
---|---|
Automotive Industry | Used in the manufacturing of gears, bearings, and other components that require durability. |
Aerospace Industry | Essential for high-temperature applications like turbine blades and engine components. |
Medical Field | Utilized in surgical instruments and implants due to biocompatibility and strength. |
Machinery Manufacturing | Key material for making parts that endure high wear and stress. |
Electronics | Applied in components that need good thermal conductivity and resistance. |
Construction | Used in tools and materials that require high strength and wear resistance. |
Specifications, Sizes, Grades, and Standards
Diffusion alloy powders come in various specifications tailored to different applications. Here’s a closer look:
Metal Powder Model | Particle Size Range (µm) | Grade | Industry Standard |
---|---|---|---|
Iron-Copper Powder | 10-45 | FC-0208 | MPIF Standard 35 |
Nickel-Cobalt Powder | 5-20 | IN718 | ASTM B637 |
Tungsten Carbide Powder | 0.5-20 | WC-Co 12% | ISO 4499 |
Stainless Steel Powder | 15-53 | 316L | ASTM F1580 |
Bronze Powder | 20-60 | C90700 | ASTM B306 |
Aluminum-Silicon Powder | 15-45 | AlSi10Mg | ISO 23510 |
Titanium Alloy Powder | 20-63 | Ti6Al4V | ASTM F1580 |
Molybdenum Powder | 10-45 | Mo-MP-101 | ASTM B386 |
Zinc-Aluminum Powder | 10-50 | ZA-27 | ASTM B669 |
Chromium Powder | 5-30 | Cr99 | ISO 5755 |
Suppliers and Pricing Details
Finding the right supplier is crucial for obtaining high-quality diffusion alloy powders. Here’s a list of some reputable suppliers and their pricing details:
Supplier Name | Location | Metal Powder Models Offered | Price Range (per kg) |
---|---|---|---|
Höganäs AB | Sweden | Iron-Copper, Stainless Steel | $20 – $50 |
Sandvik AB | Sweden | Nickel-Cobalt, Titanium Alloy | $30 – $70 |
Carpenter Technology | USA | Stainless Steel, Molybdenum | $25 – $60 |
Oerlikon Metco | Switzerland | Tungsten Carbide, Chromium | $40 – $100 |
ATI Metals | USA | Titanium Alloy, Nickel-Cobalt | $35 – $75 |
Sumitomo Electric | Japan | Tungsten Carbide, Molybdenum | $50 – $120 |
GKN Hoeganaes | USA | Iron-Copper, Bronze | $15 – $45 |
Rio Tinto Metal Powders | Canada | Aluminum-Silicon, Zinc-Aluminum | $20 – $55 |
Erasteel | France | Stainless Steel, Nickel-Cobalt | $30 – $65 |
VDM Metals | Germany | Molybdenum, Titanium Alloy | $35 – $80 |
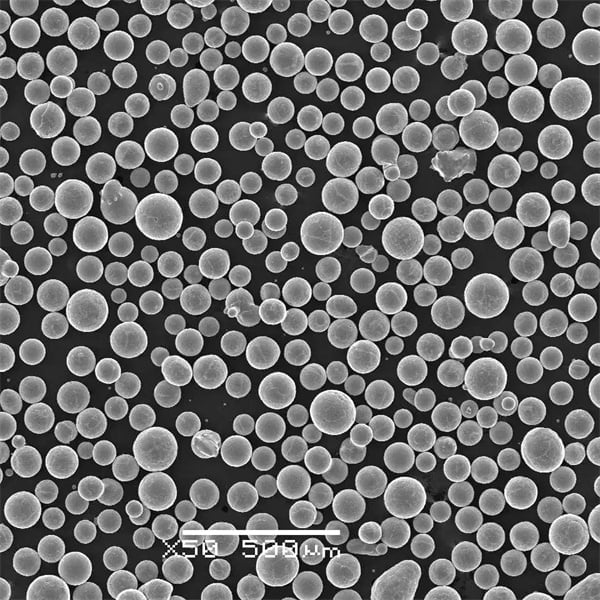
Comparing Pros and Cons of Diffusion Alloy Powder
When choosing a diffusion alloy powder, it’s essential to weigh the advantages and limitations of each type:
Metal Powder Model | Advantages | Limitations |
---|---|---|
Iron-Copper Powder | Affordable, good mechanical properties | Limited high-temperature stability |
Nickel-Cobalt Powder | Excellent high-temperature performance, wear resistance | Expensive, can be difficult to process |
Tungsten Carbide Powder | Extreme hardness, wear resistance | Very high cost, brittle in some applications |
Stainless Steel Powder | Corrosion resistance, versatile | Heavier compared to other alloy powders |
Bronze Powder | Good conductivity, low friction | Lower strength compared to other alloy powders |
Aluminum-Silicon Powder | Lightweight, high strength-to-weight ratio | Can be reactive in certain environments |
Titanium Alloy Powder | High strength, biocompatibility | Expensive, requires special processing techniques |
Molybdenum Powder | High melting point, good thermal conductivity | Can be challenging to fabricate |
Zinc-Aluminum Powder | Good corrosion resistance, lightweight | Lower strength compared to other metallic powders |
Chromium Powder | High hardness, excellent corrosion resistance | Can be expensive, limited availability |
In-Depth Analysis of Specific Metal Powders
Iron-Copper Powder
Composition: Iron (Fe) and Copper (Cu)
Iron-Copper powder is a cost-effective material widely used in the automotive industry for producing gears, bearings, and other components. It combines the strength of iron with the corrosion resistance of copper, making it suitable for parts exposed to varying environmental conditions. However, its high-temperature performance is somewhat limited, which can be a drawback in certain applications.
Nickel-Cobalt Powder
Composition: Nickel (Ni) and Cobalt (Co)
Nickel-Cobalt powder is renowned for its excellent high-temperature stability and wear resistance, making it ideal for aerospace applications and gas turbines. Despite its impressive properties, it is relatively expensive and can be challenging to process, which may limit its use in cost-sensitive projects.
Tungsten Carbide Powder
Composition: Tungsten (W) and Carbon (C)
Tungsten Carbide powder stands out for its extreme hardness and high melting point, making it perfect for cutting tools and mining equipment. However, its high cost and brittleness in some applications can pose significant challenges, requiring careful consideration during material selection
.
Stainless Steel Powder
Composition: Iron (Fe), Chromium (Cr), and Nickel (Ni)
Stainless Steel powder offers excellent corrosion resistance and versatility, making it a go-to material for medical instruments and food processing equipment. While it provides robust performance, its heavier weight compared to other alloy powders can be a disadvantage in applications where weight savings are critical.
Bronze Powder
Composition: Copper (Cu) and Tin (Sn)
Bronze powder is known for its good electrical conductivity and low friction, making it suitable for bearings and electrical connectors. However, its lower strength compared to other alloy powders can limit its use in high-stress applications.
Aluminum-Silicon Powder
Composition: Aluminum (Al) and Silicon (Si)
Aluminum-Silicon powder is prized for its lightweight and high strength-to-weight ratio, commonly used in the automotive and aerospace industries. Despite its benefits, it can be reactive in certain environments, requiring protective coatings or treatments.
Titanium Alloy Powder
Composition: Titanium (Ti), Aluminum (Al), and Vanadium (V)
Titanium Alloy powder boasts high strength and biocompatibility, making it an excellent choice for medical implants and aerospace components. However, its high cost and need for specialized processing techniques can be barriers to widespread adoption.
Molybdenum Powder
Composition: Molybdenum (Mo)
Molybdenum powder is valued for its high melting point and good thermal conductivity, ideal for furnace components and electronics. Its challenging fabrication process can be a limiting factor, necessitating advanced manufacturing methods.
Zinc-Aluminum Powder
Composition: Zinc (Zn) and Aluminum (Al)
Zinc-Aluminum powder provides good corrosion resistance and is lightweight, commonly used in galvanizing and die casting. Its lower strength compared to other metallic powders can restrict its use in high-stress applications.
Chromium Powder
Composition: Chromium (Cr)
Chromium powder is known for its high hardness and excellent corrosion resistance, suitable for hard-facing and wear-resistant coatings. However, its cost and limited availability can pose challenges for widespread use.
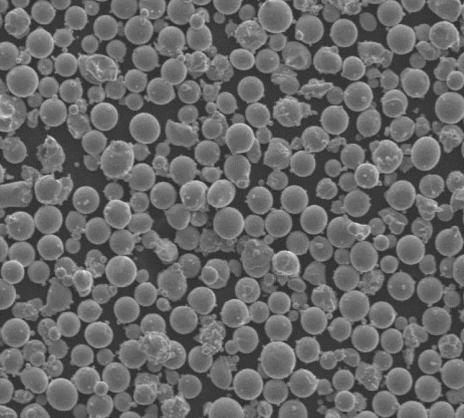
FAQs
Question | Answer |
---|---|
What is diffusion alloy powder used for? | Diffusion alloy powder is used in various industries, including automotive, aerospace, medical, and electronics, for applications requiring enhanced material properties. |
How is diffusion alloy powder made? | It is made by heating a base metal powder and alloying elements together at high temperatures, allowing the atoms of the alloying elements to diffuse into the base metal. |
What are the benefits of using diffusion alloy powder? | Benefits include enhanced mechanical strength, corrosion resistance, thermal stability, and wear resistance. |
Can diffusion alloy powder be customized? | Yes, diffusion alloy powder can be tailored to specific applications by altering the composition and processing conditions. |
What industries use diffusion alloy powder the most? | Major industries include automotive, aerospace, medical, electronics, and construction. |
Is diffusion alloy powder expensive? | The cost varies depending on the composition and properties of the powder. Some powders, like Tungsten Carbide, can be quite expensive. |
How does diffusion alloy powder compare to pure metals? | Diffusion alloy powders generally offer superior properties compared to pure metals, such as increased strength and resistance to wear and corrosion. |
What are the challenges of using diffusion alloy powder? | Challenges include high cost, potential brittleness, and the need for specialized processing techniques. |
Can diffusion alloy powder be recycled? | Yes, many diffusion alloy powders can be recycled, though the process may vary depending on the specific material and application. |
Where can I buy diffusion alloy powder? | Reputable suppliers include Höganäs AB, Sandvik AB, Carpenter Technology, Oerlikon Metco, and ATI Metals, among others. |
Conclusion
Diffusion alloy powder represents a significant advancement in material science, offering a blend of properties that can be tailored to meet the demands of various industries. From the automotive sector to aerospace and medical fields, the versatility and enhanced performance of these powders make them invaluable. Understanding the specifics of each metal powder model, along with their advantages and limitations, allows for informed decision-making in selecting the right material for your application.
Whether you’re looking to improve the durability of automotive parts, enhance the performance of aerospace components, or ensure the reliability of medical implants, diffusion alloy powder provides a solution that meets these diverse needs. So, the next time you’re in the market for a high-performance material, consider the remarkable benefits of diffusion alloy powder.
Share On
MET3DP Technology Co., LTD is a leading provider of additive manufacturing solutions headquartered in Qingdao, China. Our company specializes in 3D printing equipment and high-performance metal powders for industrial applications.
Inquiry to get best price and customized Solution for your business!
Related Articles
About Met3DP
Recent Update
Our Product
CONTACT US
Any questions? Send us message now! We’ll serve your request with a whole team after receiving your message.
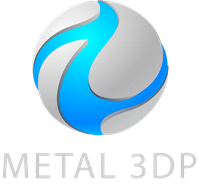
Metal Powders for 3D Printing and Additive Manufacturing