The application of DMLS technology in the medical field
Table of Contents
Imagine a world where surgeons can operate with custom-made instruments perfectly suited for a patient’s unique anatomy. Picture a future where damaged bones can be repaired with intricate implants that mimic the natural structure, promoting faster healing and improved functionality. This is the reality DMLS technology is bringing to the medical field, and it’s nothing short of revolutionary.
DMLS (Direct Metal Laser Sintering), also known as Selective Laser Melting (SLM), is a 3D printing technique that uses a high-powered laser to selectively melt metal powder layer-by-layer, building complex 3D objects from digital designs. This technology offers incredible advantages over traditional manufacturing methods, particularly in the medical industry.
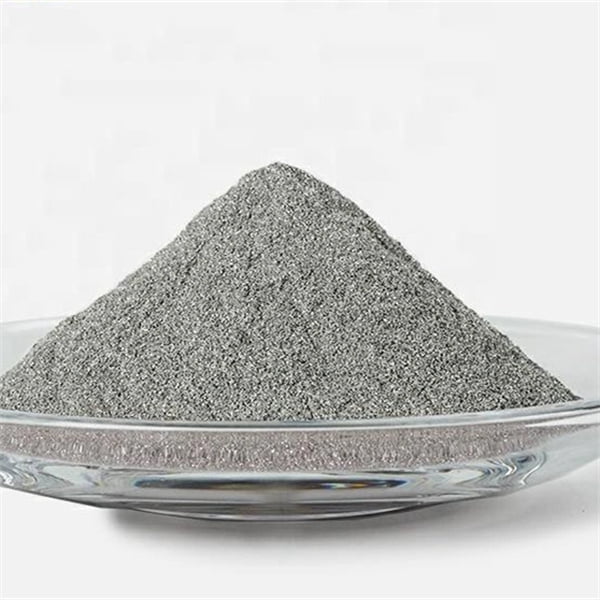
A Universe of Metal Powders: Building Blocks for Medical Marvels
DMLS utilizes a diverse range of metal powders, each possessing unique properties that make them ideal for specific medical applications. Let’s delve into some of the most common metal powders used in DMLS for medical devices:
Metal Powder | Composition | Properties | Applications |
---|---|---|---|
Titanium Alloy (Ti-6Al-4V) | 90% Titanium, 6% Aluminum, 4% Vanadium | Excellent strength-to-weight ratio, biocompatible, corrosion-resistant | Orthopedic implants (hip replacements, knee replacements, trauma repair plates), dental implants |
Cobalt-Chrome (CoCr) | 60% Cobalt, 20% Chromium, balance Molybdenum, Nickel, and Carbon | High strength, wear-resistant, good biocompatibility | Orthopedic implants (joint replacements), dental implants |
Stainless Steel (316L) | ~66% Iron, 16-18% Chromium, 10-14% Nickel, 2% Molybdenum | Affordable, biocompatible, good corrosion resistance | Surgical instruments, dental bridges, bone screws |
Tantalum | 100% Tantalum | Biocompatible, radiolucent (doesn’t show up on X-rays), good for osseointegration (bone growth into the implant) | Cranial implants, facial reconstruction plates, dental implants |
Nickel-Titanium (NiTi) | 55% Nickel, 45% Titanium | Shape memory alloy (returns to its original shape after deformation), good fatigue strength | Orthodontic braces, stents, guidewires for minimally invasive surgery |
Inconel 625 | Nickel-chromium alloy with Molybdenum, Iron, and other elements | High-temperature resistant, excellent corrosion resistance | Prosthetic heart valves, surgical instruments exposed to high heat |
Molybdenum | 100% Molybdenum | Biocompatible, good radiopacity (shows up clearly on X-rays), used for shielding radiation | Radiation therapy shielding, dental implants |
Gold | 100% Gold | Biocompatible, malleable, corrosion-resistant | Dental crowns, bridges, inlays, for patients with allergies to other metals |
Platinum | 100% Platinum | Biocompatible, highly corrosion-resistant | Electrodes for pacemakers and other implantable devices |
This table provides a glimpse into the diverse metal powder landscape used in DMLS for medical applications. Each powder offers a unique set of properties, allowing for the creation of highly specialized implants and instruments tailored to specific medical needs. For instance, titanium alloys strike a perfect balance between strength and weight, making them ideal for weight-bearing orthopedic implants like hip replacements. Conversely, tantalum’s radiolucency makes it perfect for cranial implants, ensuring clear X-ray images for monitoring post-surgery.
Beyond the Table: A Deeper Dive into Key Metal Powders
Here, we delve deeper into some of the most widely used metal powders in DMLS for medical applications:
- Titanium Alloy (Ti-6Al-4V): This workhorse material dominates the orthopedic implant market due to its exceptional strength-to-weight ratio. It’s biocompatible, meaning the body readily accepts it, and its corrosion resistance ensures long-lasting performance within the body. Think of it as the titanium skeleton for a variety of crucial implants.
- Cobalt-Chrome (CoCr): Another champion in the orthopedic arena, cobalt-chrome offers superior strength and wear resistance compared to titanium. This makes it particularly suitable for high-stress applications like joint replacements. However, some concerns exist regarding potential trace metal allergies associated with cobalt-chrome.
- Stainless Steel (316L): This cost-effective option provides a balance of affordability, biocompatibility, and corrosion resistance. It’s commonly used for surgical instruments, dental bridges, and bone screws. Imagine it as the economical workhorse for various medical tools and non-load-bearing implants.
DMLS Technology: Transforming Medical Care Across Specialties
DMLS technology’s impact transcends specific metal powders. It revolutionizes medical care across various specialties by enabling:
- Personalized Implants: DMLS allows for the creation of custom-made implants perfectly tailored to a patient’s unique anatomy. Imagine a surgeon operating with a hip replacement implant that precisely matches the patient’s bone structure, ensuring a perfect fit and potentially faster recovery. This level of customization can significantly improve surgical outcomes and patient satisfaction.
- Complex Geometries: DMLS excels at producing intricate geometries that traditional manufacturing methods struggle with. This opens doors for the creation of highly porous implants that encourage bone ingrowth, mimicking the natural structure of bone and promoting faster healing. Additionally, DMLS can fabricate lattice structures within implants, reducing weight while maintaining strength – a crucial factor for weight-bearing applications.
- Minimally Invasive Surgery: DMLS-made surgical instruments can be incredibly precise and delicate, facilitating minimally invasive procedures. This translates to smaller incisions, reduced blood loss, faster healing times, and less pain for patients. Imagine surgeons wielding specialized DMLS-printed instruments for delicate spinal surgery or intricate cranial procedures, minimizing patient discomfort and recovery time.
- Reduced Risk of Rejection: DMLS allows for the creation of implants using biocompatible materials, significantly reducing the risk of rejection by the body. This is particularly important for patients with allergies to traditional implant materials.
- Faster Innovation: DMLS facilitates rapid prototyping, allowing medical professionals to design, test, and iterate on implant designs quickly. This accelerates innovation in the medical device field, leading to the development of more effective and patient-centric solutions.
DMLS: A Boon for Patients and Medical Professionals
The advantages of DMLS technology extend beyond the creation of cutting-edge implants and instruments. It empowers both patients and medical professionals in several ways:
- Improved Patient Outcomes: Personalized implants, minimally invasive surgery, and reduced risk of rejection all contribute to improved patient outcomes. Faster healing times, reduced pain, and improved functionality can significantly enhance a patient’s quality of life after surgery.
- Enhanced Surgical Precision: DMLS-made instruments offer surgeons unparalleled precision and control during procedures. This translates to a higher degree of accuracy, leading to potentially fewer complications and improved surgical outcomes.
- Reduced Healthcare Costs: While the initial cost of DMLS-made implants might be higher, the potential for reduced surgery time, shorter hospital stays, and lower infection rates can lead to long-term cost savings for healthcare systems.
DMLS: Not Without Its Challenges
While DMLS offers a treasure trove of benefits, it’s important to acknowledge the challenges associated with this technology:
- Cost: DMLS machines and metal powders can be expensive, impacting the initial cost of implants. However, as the technology matures and adoption increases, costs are expected to decrease.
- Regulation: Regulatory frameworks for DMLS-made medical devices are still evolving. Ensuring the safety and efficacy of these devices requires ongoing collaboration between medical device manufacturers, regulatory bodies, and healthcare professionals.
- Surface Finish: DMLS-printed parts can have a rough surface finish compared to traditionally manufactured implants. However, advancements in post-processing techniques are addressing this issue.
The Future of DMLS in Medicine
DMLS technology stands at the forefront of a medical revolution, promising a future filled with:
- Bioprinting of Organs and Tissues: The ability to 3D-print organs and tissues using biocompatible materials and living cells holds immense potential for regenerative medicine. Imagine a future where damaged organs can be repaired or even replaced with bioprinted alternatives, offering hope to countless patients suffering from organ failure. While this technology is still in its early stages, DMLS paves the way for significant advancements in this field.
- Advanced Drug Delivery Systems: DMLS-printed implants with controlled porosity can be designed to deliver medications directly to the target site within the body. This targeted approach can improve treatment efficacy and minimize side effects.
- Remote Surgery and Robotics: The precision offered by DMLS-made surgical instruments can be further amplified when coupled with robotic surgery and remote surgical technologies. Imagine surgeons performing complex procedures on patients located miles away, with the help of DMLS-crafted instruments and advanced robotics.
- Personalized Medicine: DMLS technology aligns perfectly with the growing trend of personalized medicine. By creating custom implants and instruments tailored to individual patients, DMLS empowers healthcare professionals to deliver truly individualized care.
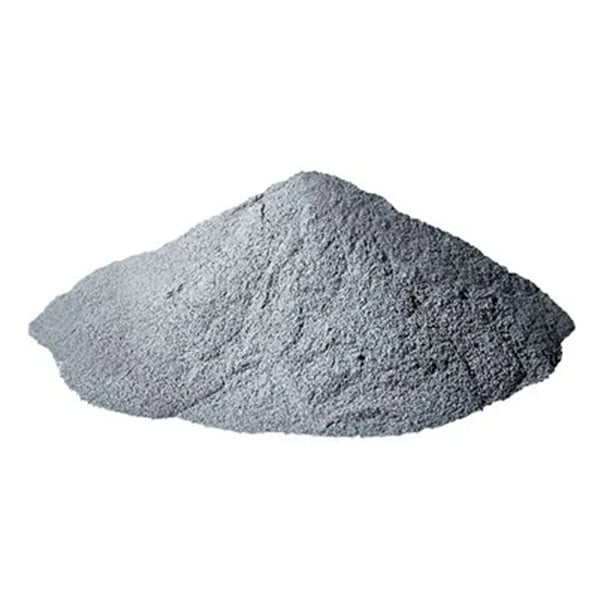
FAQs
Here, we address some of the most frequently asked questions regarding DMLS technology in the medical field:
Question | Answer |
---|---|
Is DMLS safe for medical implants? | DMLS technology can be used to create safe and biocompatible implants when proper materials and manufacturing practices are followed. Regulatory bodies ensure the safety and efficacy of DMLS-made medical devices. |
How strong are DMLS-printed implants? | DMLS implants can be incredibly strong, depending on the chosen metal powder and the design of the implant. They can be engineered to meet the specific strength requirements of various applications. |
Will DMLS-printed implants last a lifetime? | With proper care and depending on the material used, DMLS-printed implants have the potential to last a lifetime. Advancements in material science and design are continuously improving the longevity of these implants. |
How much do DMLS-printed implants cost? | The cost of DMLS-printed implants can be higher upfront compared to traditionally manufactured implants. However, potential cost savings in surgery time, hospital stays, and reduced infection rates can balance this out in the long run. As the technology matures, costs are expected to decrease. |
Is DMLS right for everyone? | DMLS technology offers numerous advantages, but it’s not a one-size-fits-all solution. Consult with your doctor to determine if DMLS-made implants are the best option for your specific condition. |
In Conclusion
DMLS technology represents a significant leap forward in medical care. Its ability to create intricate, biocompatible implants and instruments paves the way for a future of personalized medicine, improved surgical outcomes, and potentially life-saving advancements. While challenges remain, the potential of DMLS is undeniable. As this technology continues to develop and gain wider adoption, we can look forward to a brighter future in medicine, where patients benefit from more effective, personalized, and minimally invasive treatments.
Share On
MET3DP Technology Co., LTD is a leading provider of additive manufacturing solutions headquartered in Qingdao, China. Our company specializes in 3D printing equipment and high-performance metal powders for industrial applications.
Inquiry to get best price and customized Solution for your business!
Related Articles
About Met3DP
Recent Update
Our Product
CONTACT US
Any questions? Send us message now! We’ll serve your request with a whole team after receiving your message.
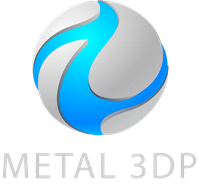
Metal Powders for 3D Printing and Additive Manufacturing