The advantages of EBM process
Table of Contents
Electron Beam Melting (EBM) has emerged as a revolutionary force in the world of additive manufacturing (AM), also known as 3D printing. This captivating technology utilizes a focused electron beam to meticulously melt and fuse metal powders layer by layer, building intricate and high-performance components. But what truly sets EBM apart? Buckle up, because we’re about to embark on a journey exploring the compelling advantages of this cutting- edge process.
High Precision of the EBM Process
Imagine crafting metal parts with near-flawless accuracy, exceeding the capabilities of traditional methods. That’s the magic of EBM! The concentrated electron beam melts metal powder with exceptional precision, resulting in dimensional tolerances that rival those achieved through techniques like machining. This translates to parts with superior surface finishes, tighter geometric details, and minimal need for post-processing. Think of it like drawing a picture with a pencil versus a paintbrush – the EBM process offers an unparalleled level of control, allowing engineers to bring their most intricate designs to life.
A Closer Look at Precision in EBM
- Layer thickness: EBM boasts the ability to create layers as thin as 30 microns (roughly the width of a human hair!), enabling the fabrication of highly intricate features.
- Minimal shrinkage: Unlike traditional casting methods, EBM experiences minimal shrinkage during the build process, leading to parts with exceptional dimensional accuracy.
- Surface roughness: EBM-produced parts generally exhibit a smooth surface finish, reducing the need for extensive post-processing steps such as grinding or polishing.
This exceptional precision makes EBM ideal for applications demanding tight tolerances, intricate geometries, and superior surface finishes. From complex medical implants to intricate aerospace components, EBM delivers unparalleled precision.
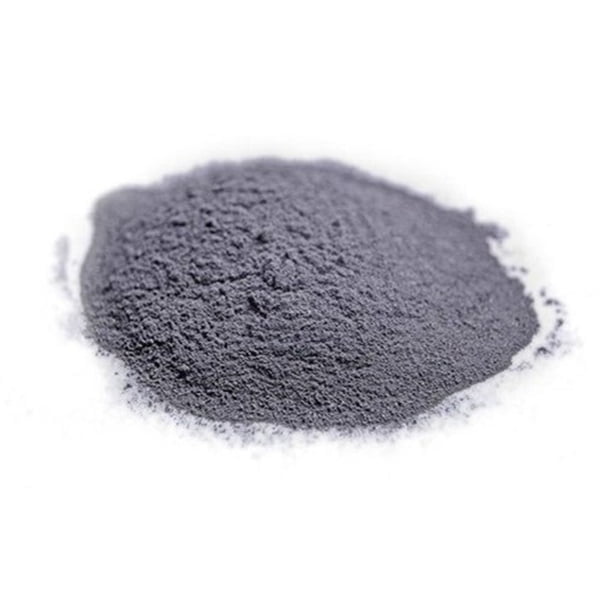
High Density of EBM Process
Ever dreamt of building metal parts with near-solid density? Look no further than EBM! Unlike other additive manufacturing methods that can trap air pockets within the printed object, EBM operates in a vacuum environment. This eliminates the risk of oxidation and ensures the complete melting of metal powder, resulting in parts with densities exceeding 99.5%.
The Power of Density: Why it Matters
- Enhanced mechanical properties: High density translates to superior strength, stiffness, and fatigue resistance, making EBM-produced parts suitable for demanding applications.
- Improved performance: Denser parts exhibit better thermal and electrical conductivity, crucial for applications like heat sinks and electrical components.
- Closer to traditional manufacturing: The high density of EBM parts makes them comparable in strength and performance to those produced through conventional methods like casting or machining.
This exceptional density makes EBM a perfect choice for applications where strength, durability, and performance are paramount. Imagine building lightweight yet incredibly strong components for aerospace, medical implants that can withstand decades of wear and tear, or heat sinks that efficiently dissipate heat – EBM makes it all possible.
High Melting Point Materials for the EBM Process
EBM truly shines when it comes to handling a diverse range of metal powders, including those with exceptionally high melting points. The powerful electron beam effortlessly melts materials that would pose a challenge for other AM techniques. This opens doors to a whole new world of possibilities!
Metal Powders for EBM: Unleashing a Material Marvel
Here’s a glimpse into some of the fascinating metal powders that can be utilized in the EBM process:
Metal Powder | Description | Properties | Applications |
---|---|---|---|
Titanium Ti-6Al-4V (Grade 23) | The workhorse of EBM, known for its excellent strength-to-weight ratio, biocompatibility, and corrosion resistance. | High strength, low weight, good biocompatibility | Aerospace components, medical implants, sporting goods |
Titanium CP (Commercially Pure) | A pure form of titanium offering superior biocompatibility and ductility. | Excellent biocompatibility, good ductility | Medical implants, dental applications |
Stainless Steel 17-4PH | A precipitation-hardening stainless steel known for its high strength and corrosion resistance. | High strength, good corrosion resistance, good hardenability | Aerospace components, marine applications, oil and gas equipment |
Inconel 625 (Nickel Superalloy) | A high-performance superalloy known for its exceptional strength at elevated temperatures. | High strength, excellent heat resistance, good corrosion resistance | Gas turbine components, heat exchangers, rocket engines |
Cobalt Chrome (CoCr) | A biocompatible alloy widely used in medical applications due to its wear resistance and strength. | High strength, wear resistance, good biocompatibility | Medical implants, joint replacements, dental applications |
Tungsten (W) | A heavy metal known for its exceptional density, high melting point, and good thermal conductivity. | High density, high melting point, good thermal conductivity | Military applications, radiation shielding, electrodes |
Tantalum (Ta) | A biocompatible and corrosion-resistant metal with a high melting point. | High melting point, good biocompatibility, excellent corrosion resistance | Medical implants, chemical processing equipment, capacitors |
Molybdenum (Mo) | A high-melting point metal with good strength and heat resistance. | High melting point, good strength, good heat resistance | Aerospace components, high-temperature furnace parts, electronic components |
Copper (Cu) | A highly conductive metal used for electrical applications. | Excellent electrical conductivity, good thermal conductivity | Electrical components, heat sinks, electrodes |
This is just a sampling of the vast array of metal powders that can be utilized in the EBM process. With its ability to handle high-melting point materials, EBM opens doors to applications that were previously limited by conventional manufacturing techniques.
EBM Process Does Not Require Supporting Structures
Imagine creating complex geometries without the need for temporary supports! That’s another captivating advantage of EBM. Since the electron beam melts the metal powder layer by layer in a vacuum environment, the parts are self-supporting during the build process. This eliminates the need for intricate support structures often required in other AM techniques.
The Freedom of Supportless Builds
- Design complexity made simple: EBM allows for the fabrication of parts with internal channels, overhangs, and intricate features that would be challenging or impossible to produce with traditional methods requiring support structures.
- Reduced post-processing: The elimination of support structures translates to less time and effort spent on post-processing steps such as removal and cleaning.
- Minimal material waste: Without the need for support structures, EBM offers a more sustainable and cost-effective approach to additive manufacturing.
This design freedom empowers engineers to unleash their creativity and create parts with unparalleled complexity. Imagine intricate medical implants that perfectly mimic natural bone structures, lightweight aerospace components with internal channels for improved heat dissipation, or complex microfluidic devices – EBM makes it all possible.
The EBM Process Also Has Other Advantages
While the aforementioned benefits are truly remarkable, EBM boasts a range of additional advantages that solidify its position as a powerful AM technology:
- Vacuum environment: The vacuum environment in EBM minimizes oxidation and contamination, leading to parts with superior material properties.
- Minimal heat distortion: Compared to other AM techniques that utilize lasers, EBM generates less heat, minimizing the risk of warping and distortion in the final parts.
- Scalability: EBM systems can accommodate a wide range of build sizes, making them suitable for producing parts ranging from small medical implants to large aerospace components.
EBM vs. Other AM Techniques: A Comparative Glance
While EBM offers a plethora of advantages, it’s essential to acknowledge that other AM techniques have their own strengths. Here’s a quick comparison to help you understand where EBM shines:
Feature | EBM | Selective Laser Melting (SLM) | Stereolithography (SLA) | Fused Deposition Modeling (FDM) |
---|---|---|---|---|
Material compatibility | High melting point materials | Metals | Mainly plastics | Mainly thermoplastics |
Part density | High density (>99.5%) | High density (>99%) | Moderate density | Moderate density |
Surface finish | Smooth surface finish | Smooth surface finish | High-resolution details | Layered surface finish |
Support structures | Not required | May be required for complex geometries | Not required | Required for most geometries |
The Bottom Line: EBM excels in producing high-density, high-precision metal parts from a wide range of materials, particularly those with high melting points. While other AM techniques offer advantages in terms of cost or material selection, EBM stands out for its exceptional precision, density, and design freedom.
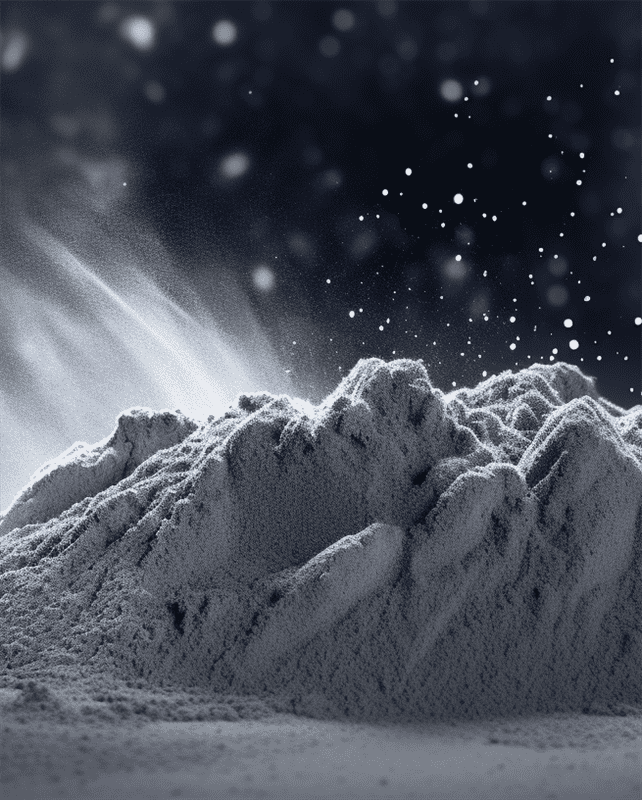
FAQ
Question | Answer |
---|---|
What are the limitations of the EBM process? | EBM can be a slower and more expensive process compared to some other AM techniques. The high cost of metal powders and the limited availability of machine sizes are also considerations. |
What industries commonly use EBM? | EBM is used in various industries, including aerospace, medical, automotive, and electronics. |
Is EBM environmentally friendly? | Compared to traditional manufacturing techniques, EBM can offer some environmental benefits. The process is more material-efficient due to minimal waste from support structures. Additionally, the vacuum environment minimizes emissions and contaminants. However, the environmental impact also depends on the energy consumption of the EBM system and the source of the electricity used. |
What are some future advancements expected in EBM? | Researchers are continuously exploring ways to improve the EBM process. Areas of focus include: * Increasing build speeds to make EBM more competitive with other AM techniques. * Reducing the cost of metal powders to make EBM more accessible. * Developing new EBM systems that can accommodate even larger build sizes. * Expanding the range of compatible metal powders to include new and innovative materials. |
Where can I learn more about the EBM process? | There are several resources available to learn more about EBM, including: * Industry associations: Organizations like the American Society for Testing and Materials (ASTM) and the Additive Manufacturing Users Group (AMUG) provide information and resources related to EBM and other AM technologies. * Machine manufacturers: Leading manufacturers of EBM systems, such as Arcam and EOS, offer comprehensive information about their machines and the EBM process on their websites. * Technical publications: Several technical publications and websites cover additive manufacturing technologies, including EBM. These resources can provide in-depth information about the process, materials, and applications. |
Conclusion
EBM has established itself as a transformative force in the world of additive manufacturing. Its ability to produce high-density, high-precision metal parts from a vast array of materials, particularly those with high melting points, opens doors to a universe of possibilities. From intricate medical implants that mimic natural bone structures to lightweight aerospace components with internal channels for improved heat dissipation, EBM empowers engineers to bring their most ambitious designs to life.
As the technology continues to evolve with advancements in build speeds, material compatibility, and cost-effectiveness, EBM is poised to revolutionize various industries. So, the next time you encounter a marvel of modern engineering, there’s a good chance EBM played a role in its creation.
Share On
MET3DP Technology Co., LTD is a leading provider of additive manufacturing solutions headquartered in Qingdao, China. Our company specializes in 3D printing equipment and high-performance metal powders for industrial applications.
Inquiry to get best price and customized Solution for your business!
Related Articles
About Met3DP
Recent Update
Our Product
CONTACT US
Any questions? Send us message now! We’ll serve your request with a whole team after receiving your message.
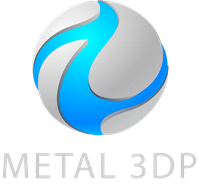
Metal Powders for 3D Printing and Additive Manufacturing